De plus en plus de choix en ce qui concerne l'impression 3D métal
La fabrication additive arrive à maturité
De nos jours, il n'est plus question de 'one size fits all' pour l'impression 3D métal. Alors qu'il y a cinq ans, la fusion laser sur lit de poudre (LPBF) était la technologie de prédilection pour l'impression des métaux, il existe aujourd'hui plusieurs alternatives. Néanmoins, les experts s'attendent à ce que l'impression laser sur lit de poudre reste la technologie d'impression métallique dominante dans les années à venir. Mais s'agit-il de la technologie idéale pour les PME? Serait-il temps pour elles aussi d'envisager sérieusement l'implémentation de la fabrication additive (AM) en tant que technologie de fabrication?
Situation actuelle (difficile)
Lorsque même un pionnier de la fabrication additive et partisan de cette technologie(Siemens) reconnaît que le marché ne croît pas aussi vite que prévu, c'est qu'il y a quelque chose qui cloche. C'est également le cas d'un point de vue financier et économique. Cette année, le marché de l'impression 3D est en difficulté. Les fabricants d'imprimantes métal en particulier, qui ont connu une croissance rapide au cours de la dernière décennie, ont rencontré des problèmes en raison d'une diminution de la demande et d'une augmentation des coûts, basés sur des prévisions de croissance surestimées. Soit ils ont été rachetés (comme Desktop Metal par Nano-Dimension et SLM Solutions par Nikon), soit ils cherchent ardemment un partenaire (comme Velo3D), soit ils jettent l'éponge (comme Xerox qui a arrêté et vendu la technologie à ADDiTEC).
Les fabricants chinois se développent
En outre, ils sont de plus en plus 'gênés' par les fabricants chinois. Ceux-ci se sont déjà emparés du marché des imprimantes 3D de bureau (notamment Bambu Lab et Creality) et maintenant, plusieurs fabricants chinois d'imprimantes 3D métal haut de gamme sont en train de se démener sur le marché européen. Ils y ouvrent des bureaux de vente et de service (comme Farsoon Technologies et Eplus3D), faisant taire les critiques qui remettaient en question leur modèle de service.
Si les fabricants chinois peuvent se développer, c'est parce qu'ils disposent d'un vaste marché intérieur. Au niveau mondial, une machine LPBF-AM sur trois est vendue en Chine! Alors qu'en Europe, nous recherchons encore des applications de niche pour l'impression métal, en Chine, il s'agit désormais de production de masse. La charnière de millions de téléphones pliables - plus populaires en Asie qu'ici - est imprimée en 3D, car son design ne peut pas être fabriqué autrement.
Les chiffres de vente les plus récents sur le marché mondial de l'impression 3D montrent que dans le segment supérieur du marché, les ventes mondiales de cette année accusent un retard de 25% par rapport à l'an dernier. Cela fait déjà quatre trimestres consécutifs que les ventes sont en baisse. Les imprimantes 3D métal sont les moins mal loties sur ce marché en perte de vitesse, avec une baisse de seulement 7% du nombre de machines livrées. Ces chiffres interviennent alors que le marché stagne depuis plusieurs années, avec environ 2.100 machines vendues dans le monde chaque année (dont environ 75% sont des LPBF).
Au niveau mondial, une imprimante 3D métal sur trois est vendue en Chine
Laser Powderbed Fusion (LPBF)
La plupart des spécialistes du marché s'attendent à ce que cette tendance se poursuive dans les années à venir. Si la technologie classique d'impression métal perd des parts de marché au profit d'autres techniques, elle reste de loin la plus utilisée en chiffres absolus. En principe, cette technologie est mature et largement applicable. L'inconvénient reste la rapidité: le produit est construit couche par couche. Il n'est pas rare que les travaux d'impression prennent plusieurs jours, voire plus d'une semaine. Mais cela ne doit pas être un obstacle si l'on exploite la valeur ajoutée de cette technologie et si l'on contrôle la qualité.
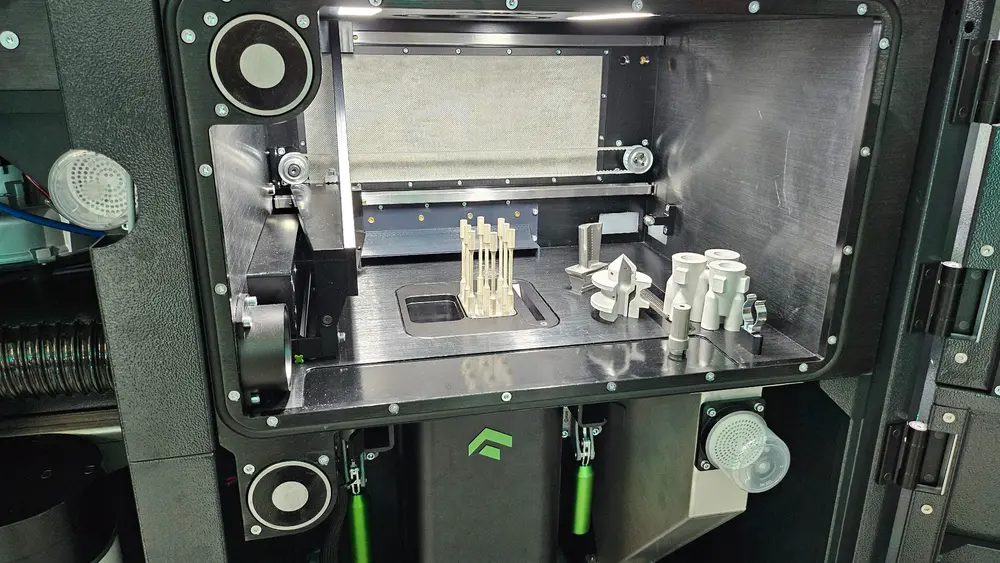
1. Systèmes multi-laser
L'intégration d'un plus grand nombre de lasers dans une même machine est l'un des moyens utilisés par les fabricants pour augmenter la vitesse et la rapidité d'exécution des travaux. Les systèmes multi-laser avec trois ou quatre lasers (de 0,5; 0,7 ou 1 kW) sont plus ou moins standard. En Chine, un fabricant a construit une machine avec 64 lasers.
Certains fabricants européens soulignent deux inconvénients liés à la multiplication des lasers: d'une part, les coûts d'investissement augmentent fortement et, d'autre part, la pièce est soumise à une forte chaleur, avec tous les risques que cela comporte. Les fabricants critiques à cet égard cherchent d'autres solutions, par exemple en commençant le recouvrement (= application d'une nouvelle couche de poudre) immédiatement après que les lasers aient éclairé une partie des chambres de construction.
2. Beam shaping
L'ILT Fraunhofer à Aix-la-Chapelle s'est intéressé très récemment à l'application du beam shaping dans les imprimantes LPBF. Cette technique a été récemment mise au point pour les machines de découpe laser. La forme du faisceau laser est ajustée pendant la découpe, ce qui permet de mieux contrôler la distribution de l'énergie.
Dans les machines LPBF-AM, cela permettrait d'utiliser des sources laser plus puissantes (> 1 kW). Actuellement, ce n'est pas encore le cas, car le faisceau laser classique accumule alors trop de puissance au centre du faisceau, ce qui peut entraîner des éclaboussures (qui perturbent le processus) et des inclusions (qui affectent l'intégrité des pièces à usiner).
Les chercheurs espèrent qu'en modifiant la forme du faisceau laser, ils pourront augmenter considérablement la productivité sans avoir à recourir à de nombreux lasers supplémentaires.
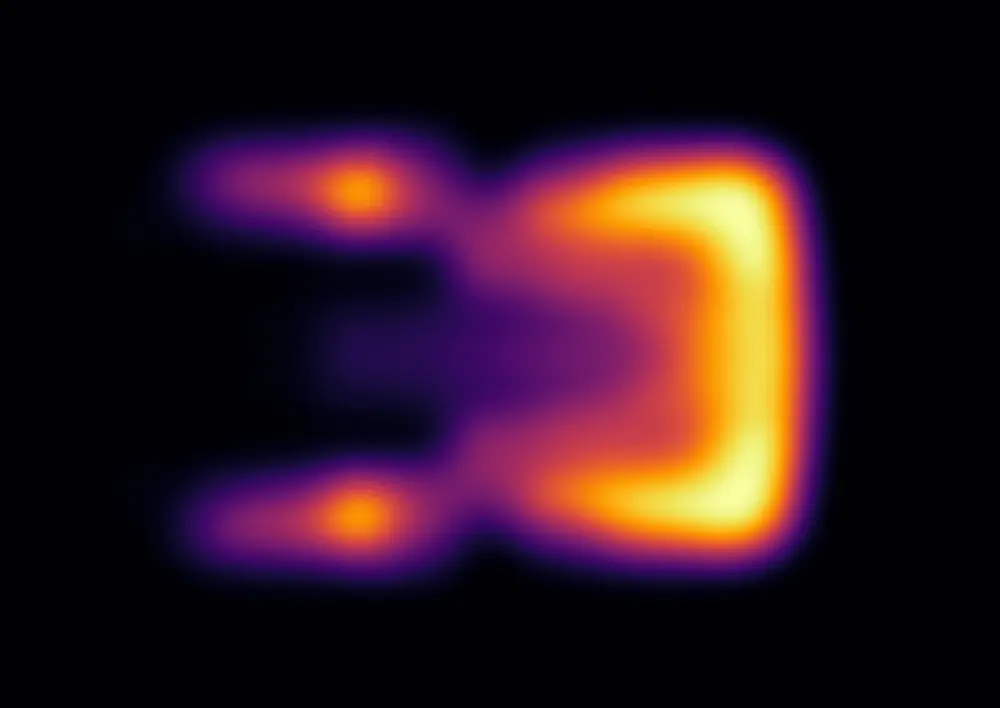
3. Volume de construction
Les imprimantes LPBF-3D connaissent également une augmentation du volume de construction. Alors qu'il y a quelques années, les machines d'une portée de 400 x 400 mm étaient courantes dans l'industrie, aujourd'hui, plusieurs fabricants proposent déjà des machines avec des volumes de construction de plus d'un mètre.
4. Laser bleu
Une quatrième évolution des systèmes LPBF (ainsi que des systèmes Direct Energy Deposition (DED), voir ci-dessous) est l'utilisation de la lumière laser bleue. C'est notamment le cas pour l'impression du cuivre. Ce laser bleu a une longueur d'onde de 400 nm, consomme moins d'énergie et a un taux de dépôt de matériau plus élevé car le cuivre absorbe mieux la lumière du laser bleu. Le taux d'absorption est de 44% avec le cuivre, contre 2% avec un laser proche infrarouge classique. Comme la quantité de lumière absorbée est plus importante, il est possible d'imprimer en 3D avec des puissances plus élevées. L'obstacle est actuellement le coût plus élevé du laser bleu.
5. Faisceau d'électrons
Une variante du LPBF est la technique qui utilise un faisceau d'électrons comme source d'énergie. L'expiration des brevets a donné naissance à plusieurs nouveaux acteurs dans ce segment. Comme le faisceau d'électrons fait fondre la poudre de métal dans une chambre à vide, des matériaux tels que le titane acquièrent de meilleures propriétés mécaniques. Par ailleurs, les produits sont plus faciles à empiler. En raison de la surface plus brute de ces impressions, cette technologie est surtout demandée dans le secteur médical.
Direct Energy Deposition (DED)
Une alternative à la technologie LPBF est le dépôt direct d'énergie (DED), qui est en fait un nom collectif pour plusieurs techniques par lesquelles le matériau est soudé.
- Cela se fait avec de la poudre, par exemple, et un faisceau laser comme source d'énergie (= l'ancien rechargement laser tel qu'il est appliqué par DMG MORI dans les machines hybrides ou par TRUMPF dans les systèmes LMD ).
- Une autre solution consiste à fondre le fil avec un faisceau d'électrons dans une chambre à vide (la technologie de Sciaky);
- Ou bien le fil est fondu au plasma dans un environnement inerte avec de l'argon (Norsk Titanium), ce qui permet d'obtenir des résistances plus élevées.
- Une variante plus récente consiste à faire fondre le fil de soudage par un processus d'arc léger (= Wire Arc Additive Manufacturing (WAAM), appliqué par GEFERTEC, CHIRON et Fronius, par exemple).
- Le fil de soudage peut également être fondu à l'aide d'un faisceau laser (le système de Meltio).
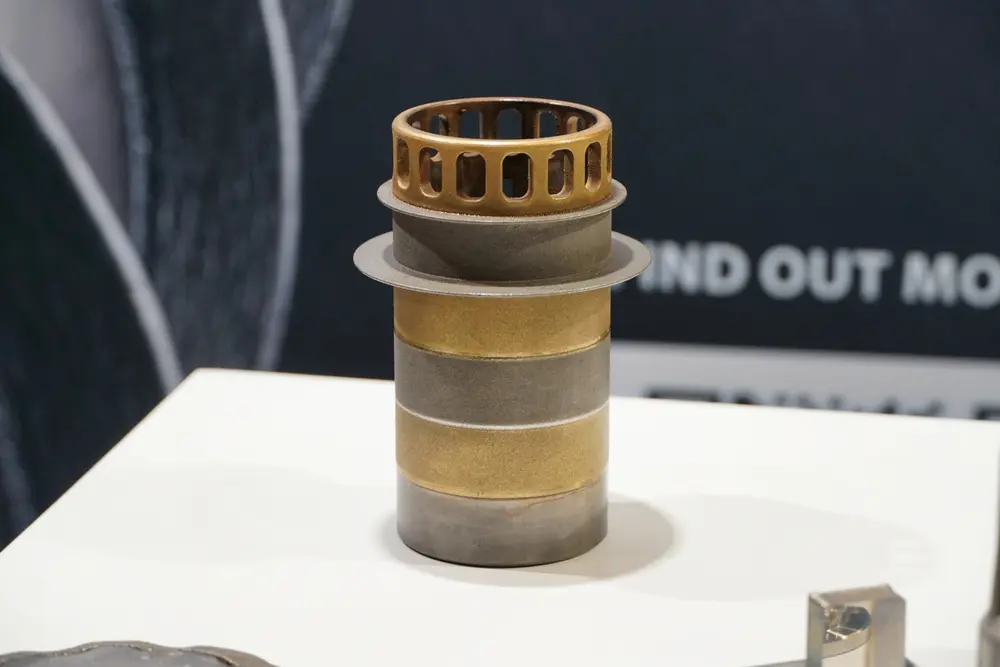
Molten Metal Deposition (MMD)
L'entreprise belge ValCUN fait figure de pionnier dans le domaine de l'impression 3D métal à l'aide de fils. La start-up gantoise, qui commercialisera ses machines Minerva à partir de 2025, extrude un fil de soudage en aluminium d'une épaisseur de 1,2 mm, le met sous pression dans une phase liquide et construit ensuite la pièce goutte à goutte (Molten Metal Deposition). Il est possible d'imprimer de cette manière un surplomb allant jusqu'à 75 degrés, sans support.
Le processus est similaire à l'impression par filament, le plastique devenant visqueux en raison de la pression élevée dans l'extrudeuse. La technologie belge est quelque peu similaire à celle de Vader Systems, qui a été rachetée par Xerox, lequel l'a finalement laissée à ADDiTEC.
Jusqu'à présent, ValCUN imprimait en 3D avec de l'aluminium, un matériau utilisé par de nombreuses PME et pour lequel il existe peu de solutions de fabrication additive.
Wire Arc Additive Manufacturing (WAAM)
Pour les PME, les systèmes à base de fil représentent une opportunité. En tant que matière première, le fil est beaucoup moins cher que la poudre et est disponible dans beaucoup plus d'alliages. Il s'agit souvent de matériaux déjà certifiés. La technologie WAAM (ainsi que la fusion du fil avec le laser) peut aussi être facilement intégrée à un robot.
Il est donc relativement peu coûteux de construire un système d'impression 3D de grandes pièces métalliques. En Belgique, l'entreprise Guaranteed l'a fait à Zelzate, où elle répare de grands outils lourds de l'industrie sidérurgique et d'autres secteurs grâce à l'impression 3D métal.
Deux autres avantages de l'impression 3D à l'aide de fils sont les coûts d'investissement réduits et la facilité d'utilisation. Cela s'applique surtout à la technologie WAAM, mais aussi aux technologies de Meltio (fusion de fil de soudage par faisceau laser) et de ValCUN (Molten Metal Deposition), entre autres. La technologie WAAM est facile à utiliser car il s'agit en fait d'un procédé de soudage.
Fronius, par exemple, lance actuellement son propre système de fabrication additive basé sur la technologie de soudage Cold Metal Transfer. Cela fait longtemps que le groupe autrichien fournit des sources de soudage pour la fabrication additive à d'autres parties, notamment à la société néerlandaise MX3D. La technologie de soudage étant très répandue dans l'industrie métallurgique, les paramètres les plus importants sont bien connus. Le point crucial réside davantage dans le positionnement correct de la torche de soudage, pour lequel Fronius a développé une solution compatible avec les systèmes robotiques courants.
Ces systèmes WAAM sont plus simples à utiliser car il s'agit essentiellement d'une machine CNC à 3 ou 5 axes (les systèmes sans robot). En outre, le nombre de paramètres qui influencent la qualité finale est beaucoup plus faible qu'avec la LPBF. Dans ce dernier cas, l'opérateur peut jouer avec plus de 150 paramètres. Souvent, les fabricants de ce type de machines utilisent une commande SINUMERIK, similaire à celle des machines CNC.
En outre, il existe déjà des programmes de FAO qui ont ajouté la technologie WAAM à leur logiciel de FAO pour les fraiseuses CNC. Aux Pays-Bas, la Hogeschool Windesheim a mis en service un centre d'usinage Haas à trois axes avec tête d'impression Meltio intégrée dans son usine NEXT, où les PME peuvent explorer la technologie en collaboration avec l'école supérieure. L'inconvénient est que, contrairement à ce que nous avons décrit plus haut pour la technologie LPBF, il faut une programmation séparée.
Le post-traitement est un point intéressant de la technologie WAAM. Il s'agit d'une technologie assez grossière; les pièces devront donc toujours être partiellement fraisées ou tournées, si l'on a besoin, par exemple, de surfaces de raccordement précises. La KU Leuven et Thomas More, en collaboration avec des partenaires dans le cadre d'un projet européen, travaillent sur un ensemble de paramètres qui permettront d'harmoniser l'impression métal et le post-traitement de manière à ce que les deux étapes du processus puissent se succéder de manière fluide.
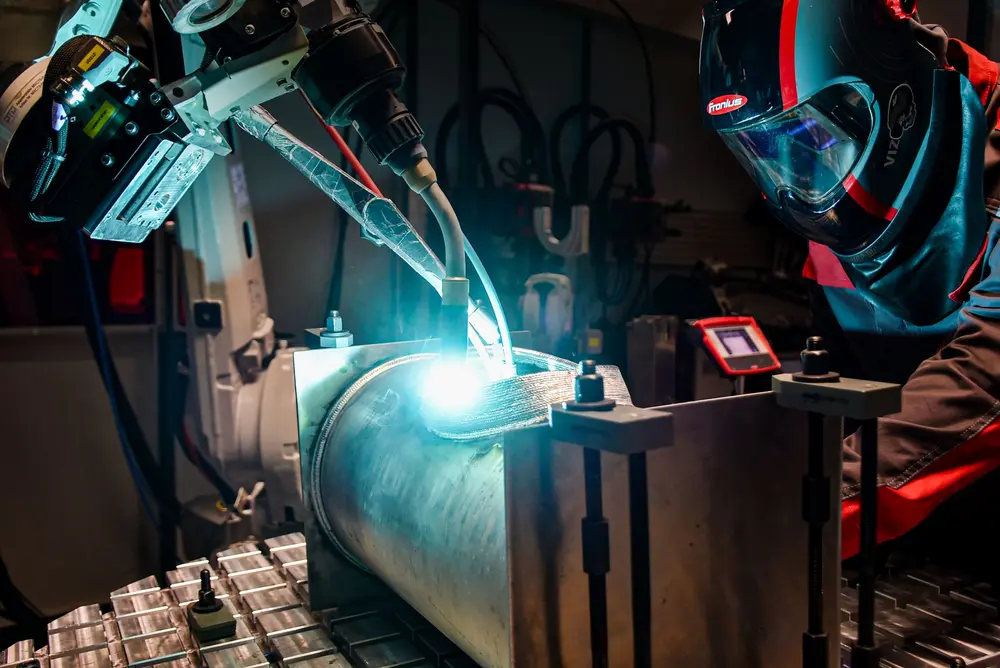
Coldspray
Une autre variante de la technologie DED est la technologie coldspray. Ici, de la poudre métallique est déposée dans un flux de gaz (à une vitesse supérieure à celle du son) sur le projet à fabriquer. L'énergie cinétique libérée fait fondre la poudre.
Deux fabricants australiens sont à la pointe de cette technique (Titomic et SPEE3D). Ils ont récemment remporté des succès dans l'industrie de la défense, entre autres, car il s'agit d'une technologie de fabrication additive très robuste qui est même actuellement utilisée sur le terrain. Cette technologie peut être facilement intégrée à un robot, ce qui offre une grande liberté de mouvement.
Cette technologie de projection à froid est étudiée dans plusieurs secteurs, dont celui du pétrole et du gaz, comme alternative à la production de pièces semi-finies forgées. Les délais de production sont longs (souvent plusieurs mois), surtout lorsqu'il s'agit de pièces en titane. Cette coldspray permet de transformer jusqu'à 27 kg de titane en quelques heures. Par rapport au fraisage à partir d'une tôle de titane forgée, l'économie de matière est de 70%.

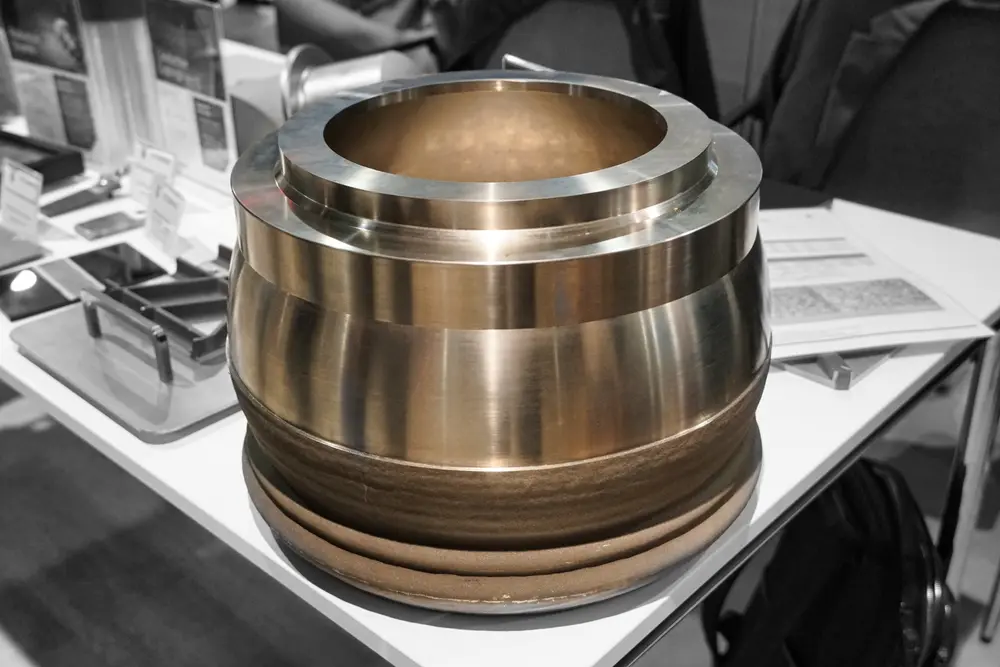
Binder Jetting
Outre les technologies LPBF et DED, la troisième technologie intéressante d'impression métal est le Binder Jetting (la technologie de Desktop Metal, HP mais aussi du nouveau venu français ADDIMETAL, entre autres). Contrairement au LPBF, le Binder Jetting n'introduit pas de chaleur dans la poudre métallique. Une fois la poudre étalée, de minuscules gouttes de liant sont pulvérisées dessus par des dizaines de milliers de buses jusqu'à obtenir la forme 2D du produit final. Sous l'effet d'une chaleur relativement faible, le liant réagit en durcissant. Comme il ne durcit qu'aux endroits où le métal doit entrer dans le produit, le reste de la poudre n'est pas affecté et peut être réutilisé.
La pièce est construite couche par couche. Dans une deuxième étape (lavage), la majeure partie de ce liant est éliminée. Vient ensuite l'étape du frittage: dans un four de frittage classique - comme avec la technologie de Metal Injection Molding (MIM) - la poudre est frittée et la pièce reçoit sa taille et sa densité finales. Cette dernière est généralement supérieure à 99%. Pendant le frittage, les pièces se contractent. Les fabricants peuvent prévoir correctement ce rétrécissement et en tenir compte lors de l'impression.
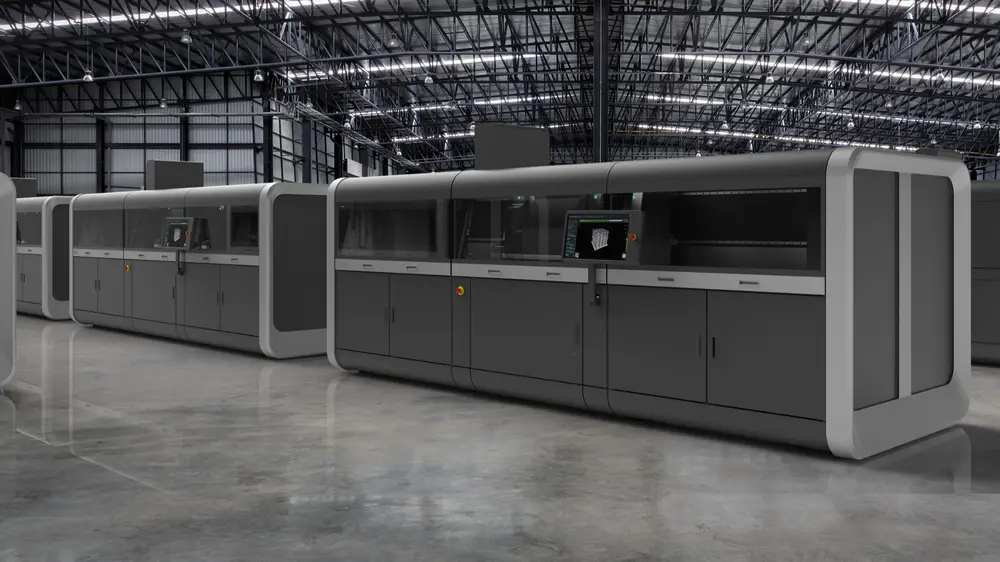
L'un des avantages de cette technologie est qu'aucune structure de soutien n'est nécessaire, que ce soit pour soutenir un surplomb ou pour dissiper la chaleur, comme c'est le cas avec la technologie LPBF. Toutefois, le frittage peut nécessiter un support pour certaines géométries.
L'absence d'apport direct de chaleur présente un autre avantage: il est possible de positionner plusieurs produits à proximité les uns des autres dans la build box. Cela permet de réduire le prix de revient par pièce.
Enfin, un avantage certain est qu'aucune contrainte n'apparaît dans le matériau, comme c'est le cas avec la technique LPBF.
Deux inconvénients par rapport aux autres techniques de fabrication additive: les dimensions sont limitées et il y a toujours deux étapes de processus après l'impression 3D. Les limites au niveau des dimensions sont liées au fait que c'est un produit vert qui sort de l'imprimante 3D. Tant qu'il n'est pas fritté, il est fragile. Le lavage et surtout le frittage sont deux étapes qui prennent du temps, au moins deux jours au total.
Fused Deposition Modeling (FDM)
Il existe d'autres techniques d'impression 3D qui peuvent être utilisées pour produire des composants métalliques. Par exemple, la technique de Fused Deposition Model (FDM), les fameuses imprimantes 3D qui utilisent du filament (comme chez Ultimaker, entre autres, mais aussi dans l'entreprise belge FuseLab). Dans ce cas, le filament est constitué d'un mélange de poudres métalliques (similaires à celles utilisées avec la technologie de Binder Jetting) et d'un polymère qui est enlevé thermiquement ou chimiquement.
L'étape finale consiste à fritter ces pièces. C'est là le talon d'Achille de cette solution: les fours de frittage industriels sont coûteux et le processus de frittage requiert de l'expérience et des connaissances. Ce qui est présenté comme un moyen peu coûteux d'imprimer des sujets métalliques s'avère en fin de compte coûteux. Ou chronophage si le frittage est effectué en externe.
En outre, la densité (98,7%) est inférieure à celle des autres techniques, de même que la dureté après une étape de durcissement supplémentaire. Par ailleurs, la rugosité de la surface est moins bonne qu'avec les techniques LPBF et Binder Jetting. C'est cette dernière qui produit les meilleurs résultats (valeur Ra de 5,2 µm contre Ra 7,5 pour le LPBF et 11,9 pour le FDM).
Le Fused Deposition Modeling est une technologie que l'on peut utiliser pour acquérir de l'expérience dans le domaine de la fabrication additive, mais il n'est pas certain qu'elle ait un sens si l'on n'imprime que des pièces uniques ou de très petites séries.
Pourquoi devrais-je me lancer dans l'impression 3D?
Pourquoi les PME qui pratiquent actuellement le fraisage CNC envisageraient-elles un système de fabrication additive WAAM ou laser? La complexité des produits que l'on peut fabriquer avec cette technologie n'est pas l'argument principal. L'aspect de la durabilité et de l'économie des ressources semble beaucoup plus important.
ASML a récemment rappelé, lors d'une réunion au Mikrocentrum, les raisons pour lesquelles il souhaite imprimer davantage de pièces en 3D (ses dernières machines intègrent déjà quelque 300 pièces imprimées). Outre la réduction des délais et l'augmentation du rendement, l'une des raisons est la diminution des pertes de matériaux. Désormais, les cadres des machines d'ASML sont souvent fraisés à partir de titane forgé. Cela signifie que jusqu'à 90% du matériau finit dans le bac à copeaux. Avec l'impression 3D métal par technologie DED, ce pourcentage est nettement inférieur. Les pertes de matériaux sont limitées à environ 10%, en fonction du produit et de la technologie. Cette raison deviendra de plus en plus importante pour l'utilisation de la fabrication additive dans les années à venir. Certains fournisseurs Tier 1 du constructeur néerlandais de machines de haute technologie ont déjà effectué des tests avec les technologies de Meltio et de Sciaky.
En outre, les avantages habituels tels que l'intégration de plusieurs pièces en une seule (nécessitant moins d'assemblage dans le produit final) et la réduction des stocks (production à la demande) restent des raisons importantes pour lesquelles les entreprises envisagent de recourir à la fabrication additive.
La plupart des chercheurs s'attendent donc à ce que le marché de la fabrication additive retrouve le chemin de la croissance dans les années à venir, après une période difficile. Selon l'un des bureaux de consultance les plus prudents, on peut envisager une croissance annuelle du marché total de l'impression 3D métal 20%. L'aérospatiale et la défense, ainsi que l'industrie médicale, sont les leaders. L'entreprise de consultance allemande AMPower s'attend à ce que le marché total de l'impression 3D métal dépasse les 10 milliards d'euros d'ici 2028. Les entreprises qui produiront des pièces à l'aide d'imprimantes représenteront la majeure partie de ce marché.