Derde Factory of the Future Award voor Continental Mechelen
Continental uit Mechelen hoort bij het kruim der bedrijven dat zich voor de derde keer tot een Factory of the Future mocht kronen. Diensthoofd Industrial Engineering Marc Moris stond ons te woord over de uitbouw van de productiefaciliteit tot een voorbeeldfabriek binnen de Continental-groep.
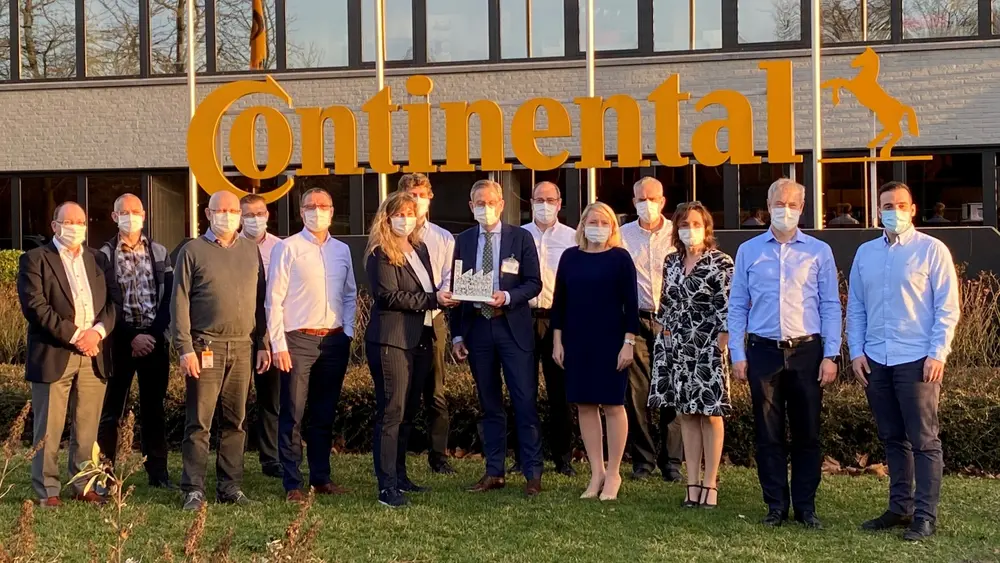
‘Tier 1’ leverancier
Continental is een belangrijke ‘Tier 1 supplier’ voor de automotive en bekleedt volgens het gespecialiseerde onderzoeksbureau Berylls de 2e plaats in de Europese ranking op dat gebied. De Belgische pijler in Mechelen maakt drie grote productgroepen: actieve wielsensoren, hydraulische ventielen en complete remsystemen.
De productie gebeurt op volautomatische productielijnen met gebruik van diverse technologieën zoals spuitgietmachines, weerstandslassen, robots, laserlassen, servo-persen, camerasystemen, 100% functionele testsystemen en een testinstallatie met meer dan 200 bar luchtdruk. Ook de logistiek kent een hoge automatiseringsgraad met een automatisch magazijn, e-kanban en toevoeren en ophalen van de producten met AGV’s. We kunnen dus met recht en reden spreken van een Factory of the Future.
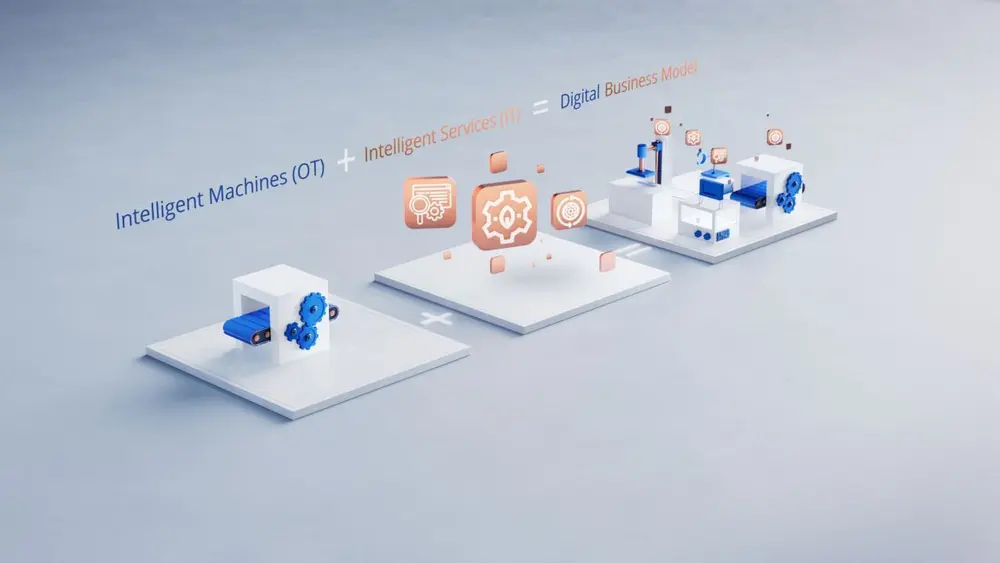
evoluties en impact
De automotive sector is vandaag het voorwerp van meerdere zeer boeiende evoluties. Er is bijvoorbeeld de shift naar elektrisch rijden, er waren de gevolgen van het dieselschandaal en Chinese constructeurs betreden stilaan de Europese markt. Tot slot had ook Covid-19 een belangrijke impact.
Motion Control: Wij vroegen ons af hoe Continental omgaat met die situaties ...
Marc Moris “Het mag duidelijk zijn dat Covid-19 een belangrijk effect had op onze marksituatie, iets wat we nog nooit hebben meegemaakt sinds we elektronische remsystemen maken. Van de komst van Chinese autobouwers zal de Continental-groep bijvoorbeeld weinig invloed ondervinden, want de andere Continental-fabrieken die remsystemen maken, zitten al in die plaatselijke toeleveringsketens.”
“De shift naar elektrisch rijden heeft op zich weinig invloed op de productie van de huidige remsystemen. In een hydraulisch remsysteem zijn zowel een verbrandingsmotor als een elektromotor aanwezig, dat zal voorlopig ook zo blijven omwille van de veiligheid. Ik stip ook nog de belangrijke trend aan van het autonoom rijden, waar nog meer ventielen in een remsysteem voor nodig zijn. Er zijn wel volop ontwikkelingen gestart om tegen 2030 'droge' remsystemen te kunnen aanbieden”
Factory of the future
“Sinds 2010 worden we volop geconfronteerd met de I4.0 hype en dan is het leerrijk om de assessment ook als evaluatietool in te zetten”
Waarom is Continental Mechelen in 2014 meegestapt in het Factory of the Future verhaal?
Marc Moris: “Onze toenmalige Plant Manager Stefaan Van Thielen was lid van de raad van bestuur van Agoria. Daar werden samen met Sirris de kiemen gelegd om de Vlaamse maakindustrie vooruit te helpen, met de bedoeling om productievolumes terug naar Vlaanderen te halen en hier te verankeren. Die visie heeft geleid tot het ontstaan van het Factory of the Future assessment. Het is dan ook ergens logisch dat we voor onze eigen 360°-feedback meestapten in dit verhaal. In de eerste plaats was het een goede oefening om op een gestructureerde manier een reflectie te hebben van wat we de afgelopen jaren gerealiseerd hadden, plus de bevestiging dat we wel met de juiste dingen bezig waren. Sinds 2010 worden we volop geconfronteerd met de I4.0 hype en dan is het leerrijk om de assessment ook als evaluatietool in te zetten.”
“Via Agoria kregen we bij onze eerste deelname een lijstje met opportuniteiten om onze reeds ingeslagen weg 'Cyber Physical Production System' verder te bewandelen in een echte 4.0 omgeving. Daarin kwamen enkele accenten naar voor:
•Fysische elementen draadloos integreren in het informatienetwerk;
•Productiesystemen omvormen naar maximaal flexibele, zelflerende en adaptieve Smart Production Systems;
•Conditioned based maintenance;
en tot slot de fabriek sterker inzetten als marketingtool.”
“We hebben toen sterk rekening gehouden met de aanbevelingen. Voor conditioned based maintenance zijn er bijvoorbeeld nieuwe ideeën ontstaan en omgezet naar mooie applicaties. Ook op de transformatie ECO Factory hebben we sterk ingezet, waarbij we ondertussen ook de nodige erkenningen behaalden. Zo waren we het eerste bedrijf binnen de Continental groep met 100% groene energie. We verbinden ons ook om bepaalde doelstellingen te halen, zoals het MVO charter van VOKA. Dat leidde er toe dat we de Continental Green Label award konden binnenhalen.”
“We beschikken over een interne energiemanager die ons ECOS-team leidt. Dat staat voor Energy COst Saving, dat team is al sinds de jaren 90 actief. Onze initiatieven daar zijn zeer divers: centrale koeling, warmterecuperatie van de luchtcompressoren, automatisch afschakelen van de lijnen en hydraulische aggregaten, energiezuinige verlichting … Ook bij onze nieuwe industriële wasmachines bekeken we hoe we water en energie kunnen recupereren en besparen.”
Traceerbaarheid tot op onderdeelniveau
“Autoconstructeurs willen ten allen prijze vermijden dat ze dure terugroepacties moeten uitvoeren. Daarom is traceerbaarheid zo belangrijk in onze sector. Dankzij het reeds vroegtijdig inzetten van digitale technieken in de productie is dat een van de sterke punten ons bedrijf. In Mechelen is er een volledige gesloten traceability, van component tot eindproduct. Het is met andere woorden niet alleen mogelijk om op eindproductniveau te traceren, maar tot op onderdeelniveau. We volgen daarin meerdere factoren op: lotnummers van de leverancier, wanneer de onderdelen uit het magazijn genomen worden, wanneer deze geconditioneerd worden, op welke machines bewerkingen uitgevoerd worden, wanneer ze in de subassemblies ingebouwd worden en tot slot in welke eindassemblies ze gemonteerd worden. Dat alles compleet met alle bijhorende locaties en tijdstippen. Dat laat ons toe om bij eventuele klachten zeer gericht te reageren en de kosten te beperken.“
Inspiratiebron en imago
Waren er bepaalde ideeën die opgepikt werden in de collega-Factory of the Future- bedrijven?
Marc Moris: “Ja, de lean approach van onze material flow met inzet van AGV’s is toch opgepikt door enkele bedrijven. Ook voor onze Human Centered Organisation was er veel aandacht, dat heeft eveneens geleid tot uitwisseling met andere ondernemingen. Agoria heeft toen een evenement bij ons georganiseerd rond dat thema. Continental Mechelen heeft een matrixorganisatie en op zeker niveau zijn er in sommige afdelingen teams die zelfsturend werken.”
"Een extra bevestiging en certificatie van onze benchmarkpositie binnen de groep, via externe expertise”
Wat betekende de award voor de positie van Continental Mechelen in de wereldwijde groep?
Marc Moris: “Dankzij de Factory of the Future Award hebben we binnen de groep aan image building kunnen doen, zeker naar het Duitse management toe. Het betekende nog eens een extra bevestiging en certificatie van onze benchmarkpositie binnen de groep, deze keer via externe expertise.”
In 2018 volgde de hercertificatie als Factory of the Future. Vergde dat meer of net minder inspanning?
Moris: “Een Factory of the Future Award binnenrijven is nooit een kwestie van laaghangend fruit, maar van continu verbeteren en opportuniteiten te zien. Dat geldt ook voor het inzetten van nieuwe technologie. In de assessments wordt de lat ook elk jaar hoger gelegd, dus je moet blijvend inspanningen doen om bij - en voorop - te blijven.”
PRojecten
Zijn er bepaalde projecten die eruit springen voor u?
Smart Toolshop
Marc Moris: “De Smart Toolshop uit de vorige assessment was een prachtig project. Daar ontwikkelden we een webbased platform voor de productie van de tools die we zelf maken, wat het geval is voor ongeveer de helft van onze wisselstukken en gereedschappen. Vroeger betekende dat voortdurend over-en-weer telefoneren en e-mailen tussen de werkvoorbereider en de verantwoordelijken van de toolshop over de status van een order. Om dat tijdverlies te vermijden ontwikkelden we een platform waarin de werkvoorbereiders continu de status van hun stukken kunnen opvolgen. Omdat de werkstukken in bakken geplaatst worden die voorzien zijn van een tag, die via WiFi de geolocatie aangeeft, weet men direct waar de stukken zich bevinden. De werkvoorbereiders krijgen verder ook een sms als het stuk afgewerkt is. Die werkwijze kende veel bijval en spaart veel tijd uit. De nieuwe manier van werken liet bovendien toe om over te schakelen naar een zelfsturend team in de Smart Toolshop, daar waar vroeger 2 teamleiders vereist waren.”
Wielsensoren van start
“Een andere belangrijke mijlpaal in onze recente geschiedenis is de start van de productie van de Next-Gen wielsensoren in Mechelen. Daarbij werd de productie uit lageloonlanden terug naar ons land gebracht. Sensoren zijn een typisch lagekostenproduct, een van de vele componenten die van Europa richting de lageloonlanden verhuisden in de jaren ’90. Dankzij onze verregaande automatisering slagen we erin om nu goedkoper en kwalitatiever te produceren dan de lageloonlanden. Het resultaat is dat we sinds één jaar de Next-Gen wielsensoren hier produceren en dat er nog expansie op het programma staat. Ik denk dat er wel meer bedrijven die oefening eens zouden moeten maken. Met een goede automatiseringsgraad, voldoende output en een optimale kwaliteit is er veel mogelijk.”
Re-engineering productielijn
“Een derde project dat ik wil aanhalen is de re-engineering van een oude lijn. Op die lijn werden sinds 2001 de MK70-remsystemen geassembleerd, maar dat product was uitgefaseerd. We hebben die lijn omgebouwd om de EBS-remsystemen voor motorrijwielen te kunnen maken. Delen van de lijn werden teruggestuurd naar een machinebouwer om te laten aanpassen, er werden nieuwe machines ingepast en we bouwden zelf een aantal machines om, zoals de palletisseerders. Het volledige project nam ongeveer een jaar in beslag. Dankzij de lage investeringskosten zijn we erin geslaagd om ook die productie naar Mechelen te halen.”
Roadmap is geen exacte wetenschap
Zijn er technologiën die de afgelopen jaren geprobeerd werden, maar later terug afgevoerd?
Marc Moris: De technologische roadmap stippelen we niet alleen uit, maar samen met onze wereldwijde collega’s. Enerzijds verloopt dit via ‘simultaneous engineering’ werkgroepen, anderzijds binnen het wereldwijd expertisenetwerk van de Continental-groep. Maar een roadmap bepalen is geen exacte wetenschap. Een idee dat gesteund wordt, kan uitmonden in een prototype of een kleine try-out maar er zijn ook dingen die al eens mislukken, of die achteraf niet het verwachte succes hebben. Dat was bij ons het geval met Vuzix of Google Glass, een systeem dat wel succesvol was bij een ander bedrijf uit de Factory of the Future groep. We dachten dat het systeem een meerwaarde kon betekenen, we hadden ook een toepassing voor ogen waarin het systeem de werknemers zou toelaten om minder scanbewegingen manueel te verrichten. Maar in ons werkveld stootten we op technische tekortkomingen en de gebruikers accepteerden het niet omdat de ergonomie niet goed zat voor hen. Ook een vervolgsysteem met een Smartwatch voerden we af. Daarop konden medewerkers foutmeldingen krijgen, maar door de grootte van de toestellen en de nood om voortdurend de batterij voldoende op te laden, was het systeem minder goed geschikt.”
Goede stukken en digitalisatie
Welke projecten werden recent afgerond?
Marc Moris: “Het ultieme doel is om geen enkel slecht stuk meer te maken. Een van de paden die we bewandelen, is de implementatie van de Space software. Daarmee kunnen we de trends in ons proces zo diepgaand analyseren en bewaken dat we kunnen ingrijpen lang voor er effectief een slecht stuk geproduceerd wordt. Verder zetten we nog sterker in op onze digitale transformatie. Er is in 2020 een I4.0 coördinator aangesteld om deze transformatie over het hele bedrijf nog sterker te ondersteunen. De moeilijke situatie in 2020 heeft ook geholpen om bepaalde zaken in een versnelling te brengen. Dus ook op het vlak van Human Centered Organisation kan je nieuwe initiatieven verwachten. Met de nieuwe Plant Manager Alexandra Bornemann, die een bewezen ervaring in change management kan voorleggen, hoeven we niet te twijfelen dat een volgende award in 2024 ongetwijfeld op onze agenda staat.”