Flexibiliteit koppelen aan veiligheid, hoe doe je dat?
Machines moeten voldoen aan de Machinerichtlijn. Die richtlijn is jaren terug opgesteld met de vaste, rigide structuur die machines toen hadden in het achterhoofd. Vandaag staat die benadering door de toegenomen vraag naar flexibiliteit onder druk, met de collaboratieve robot als voornaamste voorbeeld. Welke gevolgen heeft dat op de regels?
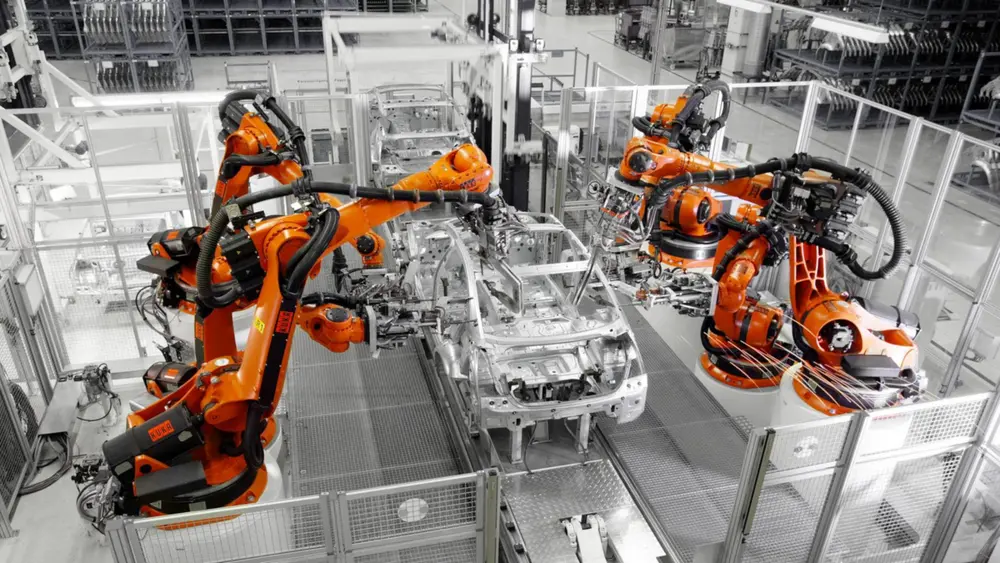
Machinerichtlijn over samenstel
Machineveiligheid wordt omschreven als ‘het vermogen van een machine om haar beoogde functie(s) gedurende haar levensduur uit te voeren, waarbij het risico voldoende is gereduceerd’. In de EN ISO 12100 wordt beschreven hoe dat in de praktijk aangepakt kan worden. Speerpunt in die benadering is de risico-beoordeling, waarbij alle mogelijke gevaren (thermisch, mechanisch, elektrisch, lawaai, chemisch ...) beschreven worden. Omdat het een systeem is waarin een terugkoppeling met evaluatie voorzien is, moet de werkwijze voortdurend worden herhaald tot de evaluatie positief is.
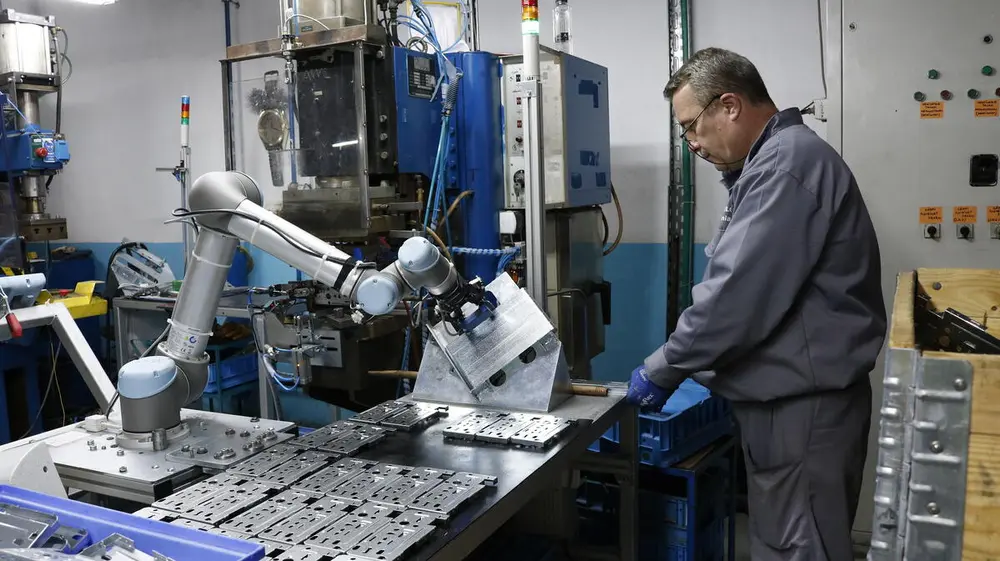
De mens/cobot-samenwerking en de inherente flexibiliteit zorgen voor een voortdurend wijzigende veiligheidssituatie
In dit verhaal is sprake van meerdere betrokken partijen: er is de fabrikant van de machine, er is een eindgebruiker en vaak is er ook een systeemintegrator. Die laatste heeft een belangrijke rol, want bij veel machines is er vandaag sprake van een samenstel, een systeem waarbij meerdere machines opgesteld en bediend worden zodanig dat ze als een geheel functioneren. Stel dat we in een vroegere situatie een losstaande machine hadden die manueel beladen werd, maar de eindklant wil dit automatiseren via een robot. De risicobeoordelingen voor de oorspronkelijke machine en die van de transportband kunnen dan niet simpelweg worden ‘samengeteld’ omdat er sprake kan zijn van bijkomende risico’s die veroorzaakt worden door het samenbouwen. Het meest duidelijke voorbeeld is hier uiteraard knelgevaar dat kan ontstaan bij de overgang tussen de beide machines. Bij elke machine apart was dit risico er nog niet, enkel door ze samen te bouwen ontstond het nieuwe gevaar. Maar wat is nu exact een samenstel? In dit voorbeeld is het overduidelijk dat deze installatie een nieuwe entiteit vormt, met potentieel nieuwe risico’s. Helaas is die scheidslijn niet altijd zo duidelijk te maken en bovendien zorgt de evolutie in technologie voor extra pigment in deze discussie.
De verwachtingen rond cobots liggen soms te hoog, het is geen toestel dat zomaar verplaatst kan worden
Vraag naar meer flexibiliteit
Geautomatiseerde productielijnen werden ooit gebouwd voor de lange termijn. Denk aan de automotive: robots en andere machines werden geprogrammeerd om soms miljoenen repetitieve bewegingen te maken, soms jaren aan een stuk. Vanuit veiligheidsoogpunt is dat de ideale situatie, want eens de risicobeoordeling op punt staat is de basis er om werknemers een veilige werkomgeving te garanderen. Vandaag zien we dat die benadering compleet overhoop gehaald wordt door enkele even markante als diverse evoluties. Zo zijn robots een pak goedkoper geworden, wat ze voor een breder pakket aan bedrijven beschikbaar maakt. Ook voor kleinere kmo's is robotica niet langer een verre droom. Daar staat wel tegenover dat dit type bedrijven meestal niet over de technische kennis beschikt om dit intern klaar te spelen. Hier komt de integrator dus vaker op de proppen.
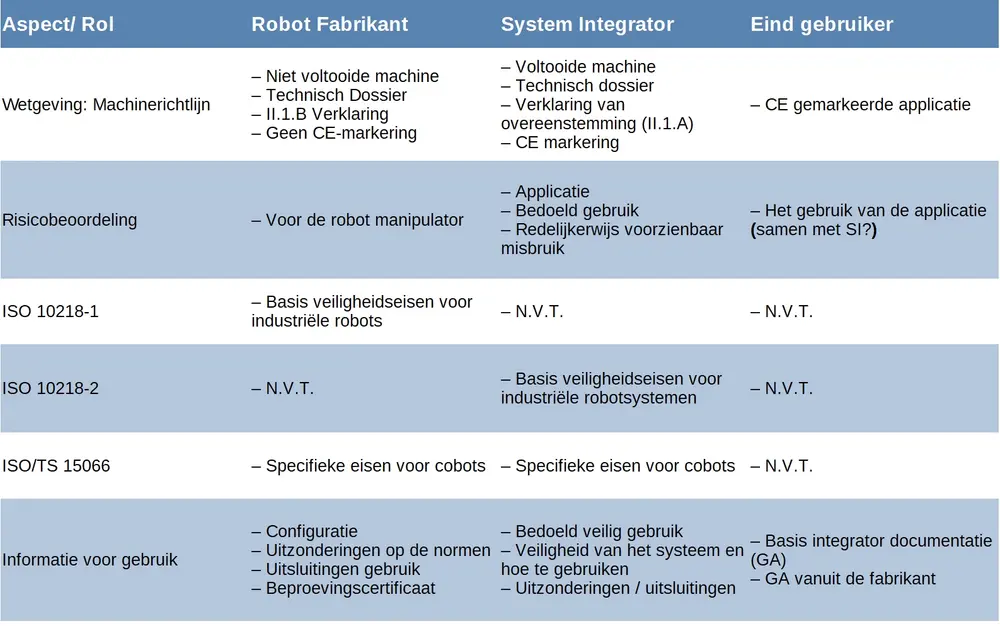
De verschillende rollen en hun verantwoordelijkheid bij het werken met een cobot
Een tweede belangrijke evolutie is het verdwijnen van massaproductie, ten voordele van kleinere maar meer gespecialiseerde reeksen. Dat vereist een aangepast machinepark, met de nodige flexibiliteit om snel om te stellen. Maar dat omstellen moet wel door de gebruiker worden gedaan, liefst op een toegankelijke wijze want technisch geschoold personeel ontbreekt.
Samengevat ...
We krijgen dus meer machines, die vaker door de eindgebruiker zelf ingesteld worden. Aan de hand van het voorbeeld van een cobot want deze lijkt wel geknipt als antwoord op dat soort evoluties: toegankelijk, makkelijk in te stellen, flexibel en ... veilig?
Veiligheidsvereisten
Helaas blijken de verwachtingen rond cobots soms wat te hoog te liggen. Het is geen toestel dat je zomaar kan opnemen, verplaatsen en weer inpluggen zoals weleens voorgespiegeld werd. Een cobot is maar zo veilig als de applicatie dat toelaat. Kort door de bocht: monteer een mes op je cobot in plaats van een grijper en je krijgt evengoed een gevaarlijke machine. Voor een cobot geldt evenzeer wat voor andere machines geldt: bij elke wijziging moet worden nagegaan in hoeverre de situatie nog veilig genoeg is. Maar wat meer is: in sommige gevallen zal de wijziging ook een verandering van rol betekenen voor de eindklant, die plots ook integrator wordt. Aan die gewijzigde rol zijn dan weer andere verantwoordelijkheden gebonden. Leest u vooral even mee.
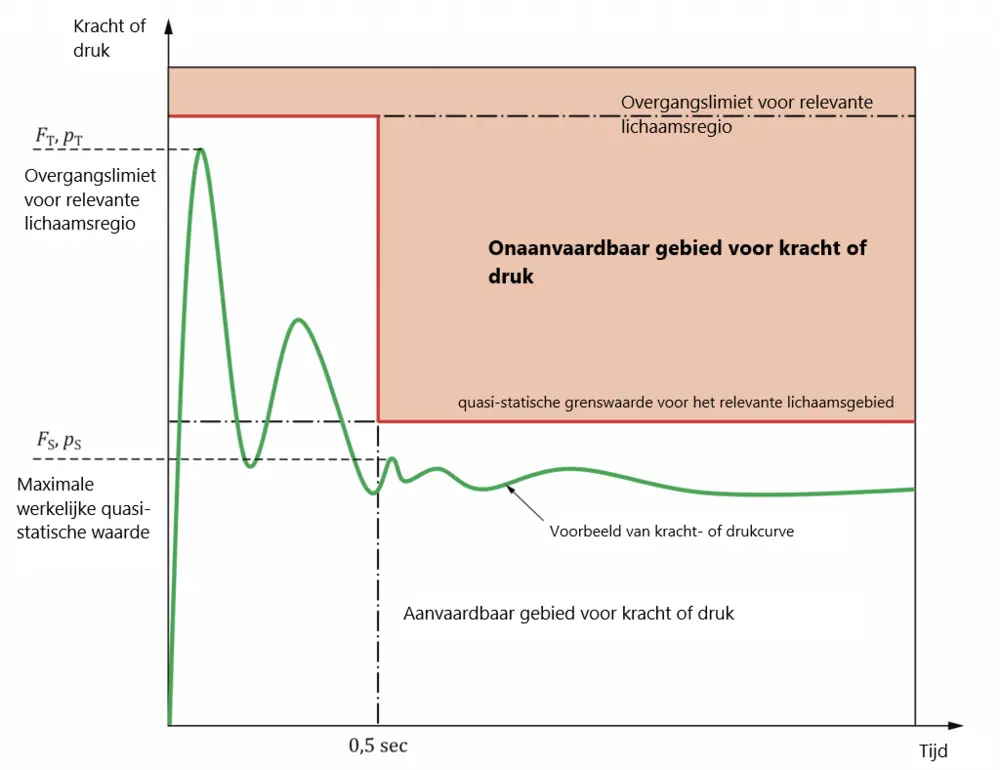
De ISO 15066 geeft aan hoe er omgegaan moet worden met de krachten en drukken op het menselijk lichaam en welke de acceptabele grenzen zijn
Rolverdeling: fabrikant, integrator, eindgebruiker
Om een veilige cobotomgeving te garanderen, moeten we eerst even alle rollen analyseren. In de meeste gevallen zullen dat er drie zijn: de fabrikant, integrator en eindgebruiker. De rol van fabrikant is de meest duidelijke: hij is degene die de cobot ontwikkelt en bouwt. De rol van eindgebruiker lijkt op het eerste zicht ook duidelijk: degene die de cobot gebruikt om zaken te produceren. De integrator is dan degene die de machine aanpast zodat de eindgebruiker ze kan gebruiken in zijn proces. Schijn bedriegt evenwel, want in de realiteit is de scheidslijn tussen eindgebruiker en integrator zeer dun. Vaak vallen ze zelfs helemaal samen, bijvoorbeeld bij grote bedrijven die zelf hun installaties bouwen. Maar de geschetste evoluties zorgen ervoor dat dit nu ook bij kleinere bedrijven steeds meer het geval is.
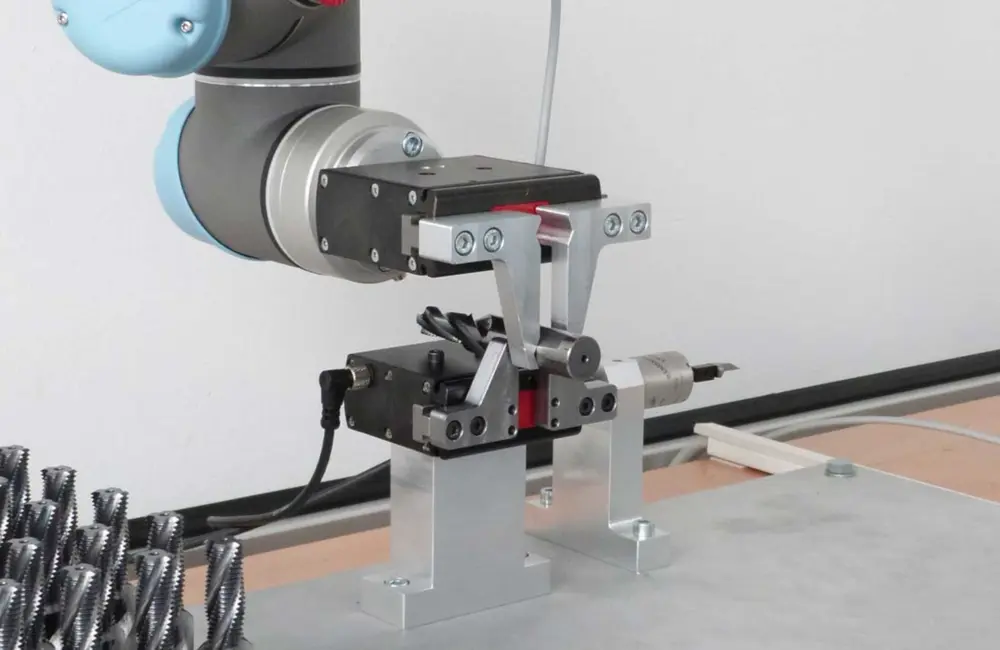
Voor een cobot geldt evenzeer wat voor andere machines geldt: bij elke wijziging moet worden nagegaan in hoeverre de situatie nog veilig genoeg is
Om bij het voorbeeld van de cobot te blijven: wie een cobot verplaatst van toepassing X naar toepassing Y, neemt de rol aan van integrator - met de bijhorende verantwoordelijkheden. Dit is een overduidelijk voorbeeld. Maar wat als we nu enkel de gripper van de cobot veranderen? Bij een één-op-één vervanging door slijtage lijkt het duidelijk dat de risico’s niet veranderen, maar stel dat we een driepuntsgrijper vervangen door een flexibele grijper, dan is dat al veel minder duidelijk. In de meeste gevallen zullen de risico’s hier wijzigen, en dat manifesteert zich op meerdere vlakken:
- de snelheid van de grijpbeweging kan wijzigen
- de omvang van de gripper kan anders zijn
- de grijpkracht kan anders zijn
- de reactiesnelheid kan wijzigen
Een eerste stap is en blijft de risicobeoordeling
Bovendien ontstaat er in feite een nieuw samenstel, met de bijhorende verplichtingen zoals een hernieuwing van de CE-markering met de bijhorende procedure. Let dus altijd op als u als eindgebruiker zaken verandert aan uw cobot of eender welke andere machine.
Gewijzigde rol
U wil uw cobot aanpassen en u bent zich bewust van de andere risico’s en de bijkomende rol die dit met zich meebrengt. Welke acties moet u dan ondernemen om uw werknemers veilig te houden te beantwoorden aan de wettelijke vereisten?
Een eerste stap is en blijft de risicobeoordeling, in de volksmond vaak onterecht verengd tot de risicoanalyse. In de risicobeoordeling volgens de EN-ISO 12100- norm worden een aantal stappen doorlopen:
- Aangeven van de grenzen van de applicatie: wat gebeurt er, wat is het werkgebied, waar is er menselijke interactie, welke machines zijn er actief ...
- de identificatie van gevaren en nagaan of aan de eisen van de norm wordt voldaan
- de risico-inschatting
- de risico-evaluatie, waarbij op basis van de eisen uit de norm 12100 risicoreducerende maatregelen getroffen worden, waarna de beoordeling opnieuw moet worden doorlopen
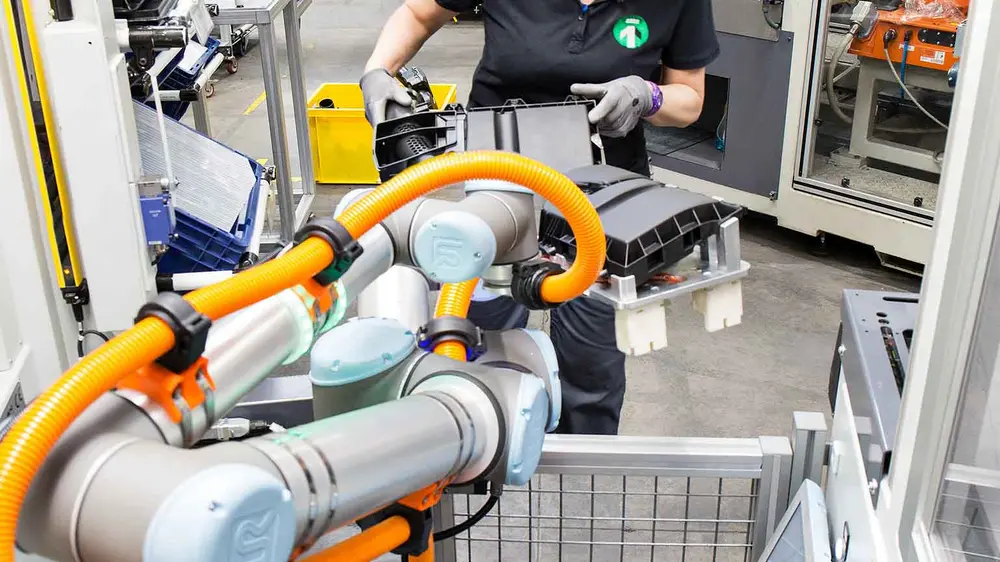
Wie een cobot verplaatst van toepassing X naar toepassing Y, neemt de rol aan van integrator, met de bijhorende verantwoordelijkheden
Als we het voorbeeld van de cobot hanteren, dan moeten we ons meerdere vragen stellen over de risico’s: waar kan er exact contact optreden tussen mens en cobot? Is er knelgevaar tussen cobot en werknemer? Is er knelgevaar tussen grijper en werknemer? Zijn er specifieke gevaren verbonden aan de grijper (scherpe punten bijvoorbeeld)? Wat zijn de gevolgen als een ledemaat van de werknemer gegrepen wordt? Is er gevaar op botsing tussen cobot en andere machines? Door deze lijst minutieus op te stellen en de bijhorende risicobeperkende maatregelen op te sommen, kan een uitgebreide lijst worden gecreëerd van te nemen maatregelen. Dit is uiteraard geen nattevingerwerk: de specifieke cobotnorm ISO 15066 is hierbij bijvoorbeeld een handige leidraad. Deze specifieert de veiligheidsvoorwaarden voor collaboratieve industriële robotsystemen en hun omgeving, en vormt daarbij een aanvulling op de voorwaarden en richtlijnen uit de robotnorm ISO 10218. De ISO 15066 - eigenlijk een technical specification - geeft aan hoe er omgegaan moet worden met de krachten en drukken op het menselijk lichaam en welke de acceptabele grenzen zijn. Er worden in de norm drie grootheden aangehaald om dit risico aan te duiden:
- Maximale kracht [F, Newton]
- Maximale druk per oppervlak [P, Newton / cm2]
- Maximale snelheid [v, mm/s]
Deze drie parameters worden bepaald op basis van de gevarenzone en het mogelijke risico. Een vinger kan andere krachten en drukken aan dan een been. Per zone dient bepaald te worden wat de maximale waarden mogen zijn, deze zijn allemaal terug te vinden in de norm. Als basisregel wordt er in eerste instantie vanuit gegaan dat de maximale kracht op dat deel van het lichaam bepaald wordt in de instelling van de cobot. Wanneer hiermee gerekend wordt als uitgangspunt, kan er door middel van het oppervlak van het contactpunt (in cm2) worden berekend wat de maximale contactdruk is op dat punt.