HOE Controle HOUDEN over 3D-lasercladden?
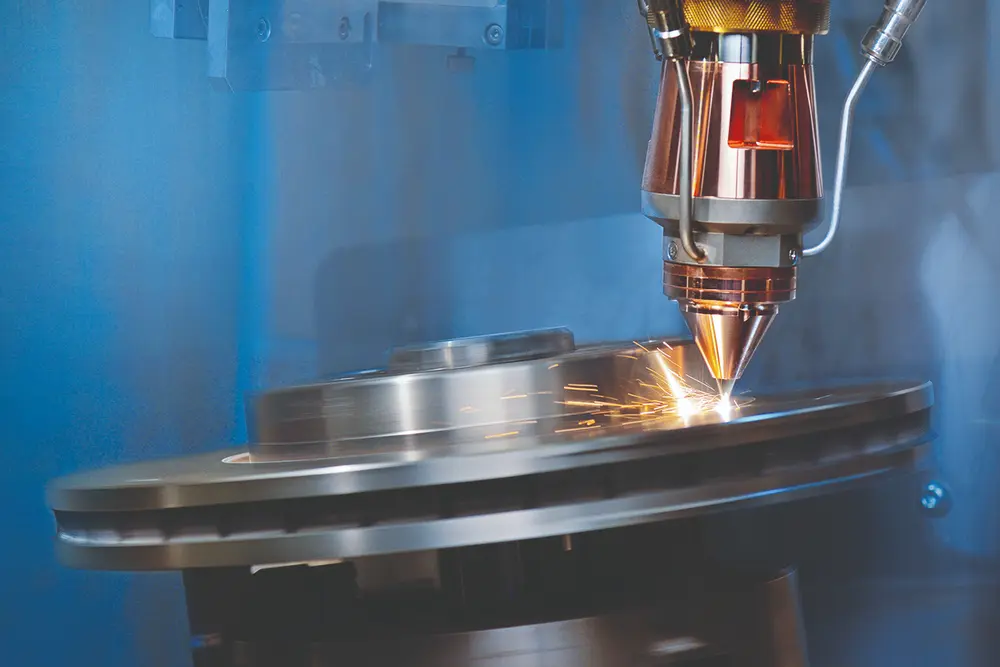
Vooral wetenschappelijke onderzoekers en ook wel bedrijven zijn wereldwijd al lange tijd op zoek naar de heilige graal voor kwaliteitsborging van lasercladdingprocessen. Hoe controleer en beheers je dat proces, dat in feite een lasproces is? Dat is vooral belangrijk als men lasercladden gaat inzetten voor 3D-metaalprinten. Smart industry is één deel van de oplossing; innovaties in de hardwarecomponenten het andere deel. Samen openen ze nieuwe mogelijkheden.
Lees hier het eerste deel over de mogelijkheden van lasercladden
De kwaliteit van lasercladden, in de zin van het aanbrengen van een extra deklaag op een product, staat vandaag niet meer ter discussie. Voor die toepassingen kan het proces afdoende worden bewaakt, bestuurd en dus gevalideerd. Anders is het als men richting het cladden van 3D-vormen gaat, officieel Directed Energy Deposition. Het voorkomen van porositeit in de opgebouwde materialen is dan een van de uitdagingen.
Nieuw type camera
Verschillende factoren zijn hierop van invloed: van de nauwkeurigheid van het sturen van de poederstroom – zowel qua richting als de exacte hoeveelheid poeder-gascombinatie en de kwaliteit van de metaalpoeders – tot en met het monitoren van het smeltbad. De systemen zijn lange tijd vooral geënt op visuele inspecties van de geometrie en temperatuur van het smeltbad met high speed IR-camera’s. De beperking hiervan is dat ze weinig tot geen warmte registreren onder de 900 °C, waardoor ze dus ‘blind’ zijn voor het afkoelproces bij cladden.
MWIR PbSe-sensoren gaan beter om met temperatuurdistributie en geven zo een completer beeld
Daarnaast zijn deze CMOS-camera’s in het zichtbare infraroodgebied erg gevoelig voor weerkaatsingen. Een nieuwe ontwikkeling is het gebruik van MWIR PbSe-sensortechnologie. Dat is een nieuw cameratype dat korte- en middengolflengte van infrarood detecteert en met een frequentie van 1000 beelden per seconde vastlegt. Het dynamisch bereik van dit nieuwe apparaat is veel groter. Het grootste voordeel hiervan is dat deze MWIR PbSe-sensoren beter weten om te gaan met de temperatuurdistributie tijdens het smelten van het materiaal. Ze geven zo een completer beeld.
Daarnaast is de variatie in de gemeten waarde kleiner dan bij de CMOS-sensoren. Er ontstaat hierdoor een beeld van de temperatuurdistributie in het smeltbad dat veel minder ruis bevat dan bij de andere meettechnologie. Met dit nieuw type sensor krijgt men dus nauwkeurigere resultaten. Hierdoor is het systeem meer geschikt om in te zetten in een closed loop-systeem, dat de procesparameters bijstelt aan de hand van realtime data.
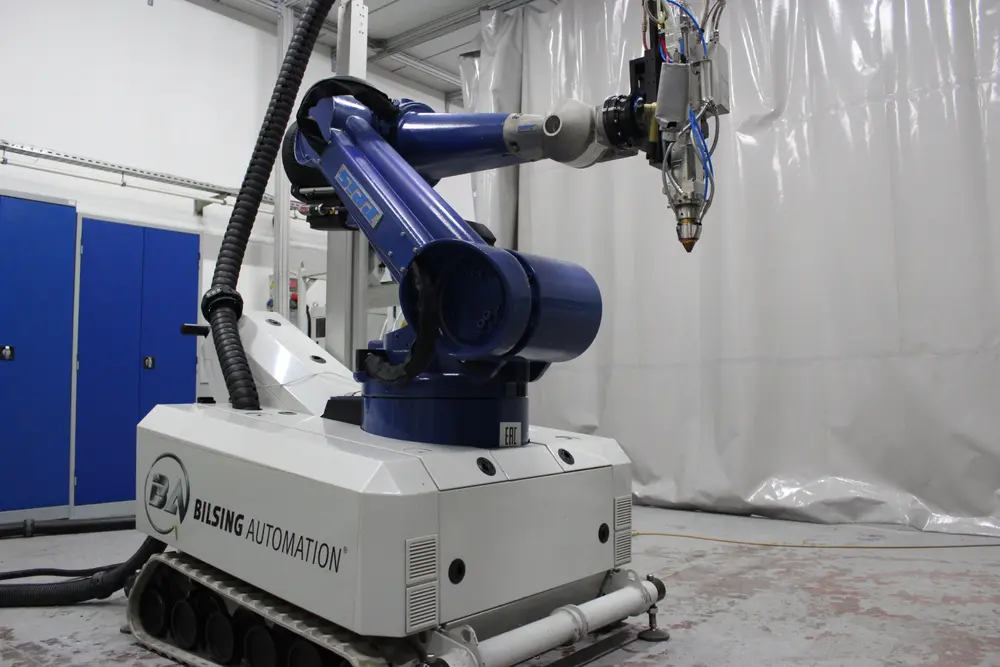
Poederdistributie
Een andere factor die invloed heeft op de kwaliteit is de verdeling van de metaalpoeders in het vlak dat wordt opgebracht. Dat blijkt een wezenlijke factor te zijn voor de kwaliteit van het onderdeel. Een vrij recente ontwikkeling in Duitsland is dat men deze poederdistributie meet met een camera die de reflectie door de nozzle meet. Hiermee kan men de distributie van de metaaldeeltjes in 3D weergeven, waarna rekenmodellen op basis van de gemeten verdeling een aantal kengetallen berekenen. Met hoe meer beelden de algoritmen worden gevoed, des te nauwkeuriger de resultaten zijn. Vanaf zo’n 10.000 beelden zijn de resultaten op hun best. Met dit systeem kan men vervolgens de poedermassastroom nauwkeuriger regelen om daarmee het proces voorspelbaarder en betrouwbaarder te maken.
Dat was tot nog toe een van de ontbrekende schakels in de procescontrole van lasercladden. De poederdosering werd vooral mechanisch gestuurd. Doordat men nu de poedergasstroom en de 3D-distributie nauwkeurig meet en men het proces documenteert, kunnen bij een volgende print van dit werkstuk de data van een eerder proces worden opgeroepen. De onderzoekers zeggen dat lasercladden hiermee een reproduceerbaar proces wordt.
Chinese wetenschappers gebruiken deze aanpak om de spanningen in het onderdeel te verlagen, door de manier waarop de geometrie wordt opgebouwd aan te passen aan de hand van rekenkundige modellen. Een betere poederdistributie zorgt volgens deze onderzoekers voor een stabieler laagopbouw, iets dat belangrijker wordt naarmate de onderdelen die men cladt groter worden, bijvoorbeeld structuurdelen voor vliegtuigen.
Temperatuur en positie hotspot
De temperatuur in het smeltbad en de omliggende lagen blijft evenwel een belangrijke factor. Een niet-homogene temperatuur kan tot geometrische afwijkingen in het werkstuk leiden. Daarom blijven onderzoekers doorgaan met het verbeteren van de thermografische beeldvorming van het proces. Met een thermische camera maakt men zowel in 2D als in 3D beelden tijdens het cladden, eigenlijk vergelijkbaar met wat er bij computer thomografie (CT) gebeurt. Deze beelden tonen de zwakke punten in het werkstuk en brengen mogelijke fouten aan het licht.
Aan de monitoringsystemen die gebruikmaken van high-speedcamera’s en spectrometers hangt vaak een fors prijskaartje
In een recent onderzoek door de Ruhr-Universität in Bochum (Duitsland) hebben de onderzoekers gewerkt met het gelijktijdig registeren van de temperatuur in het smeltbad en de hotspot (warmste punt) in het meetvlak. Dat doen ze met één thermisch-optische camera op een 3-assige lasercladdinginstallatie. De temperatuurdata en de positie van het heetste punt in het opgenomen beeld worden realtime verwerkt. Door de positie van de infraroodcamera, onder een hoek van 45 graden en zonder dat hij relatief beweegt ten opzichte van de nozzle, kan men uit de data de echte hoogte berekenen van de wand die in dit geval wordt geprint. Doordat de software die vergelijkt met de hoogte die in het CAD-model staat aangegeven, kan men in real time compenseren voor de afwijking.
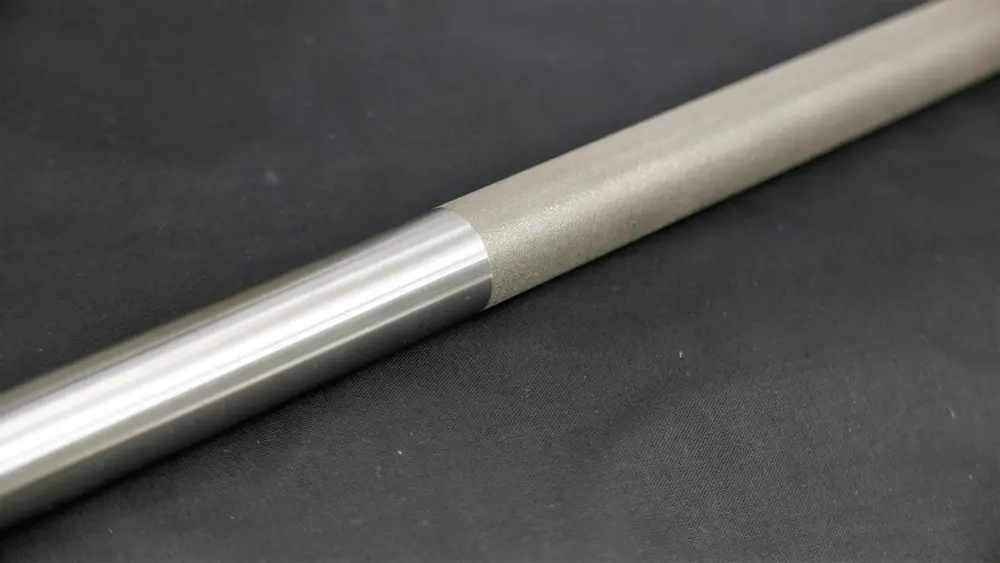
Goedkopere oplossing
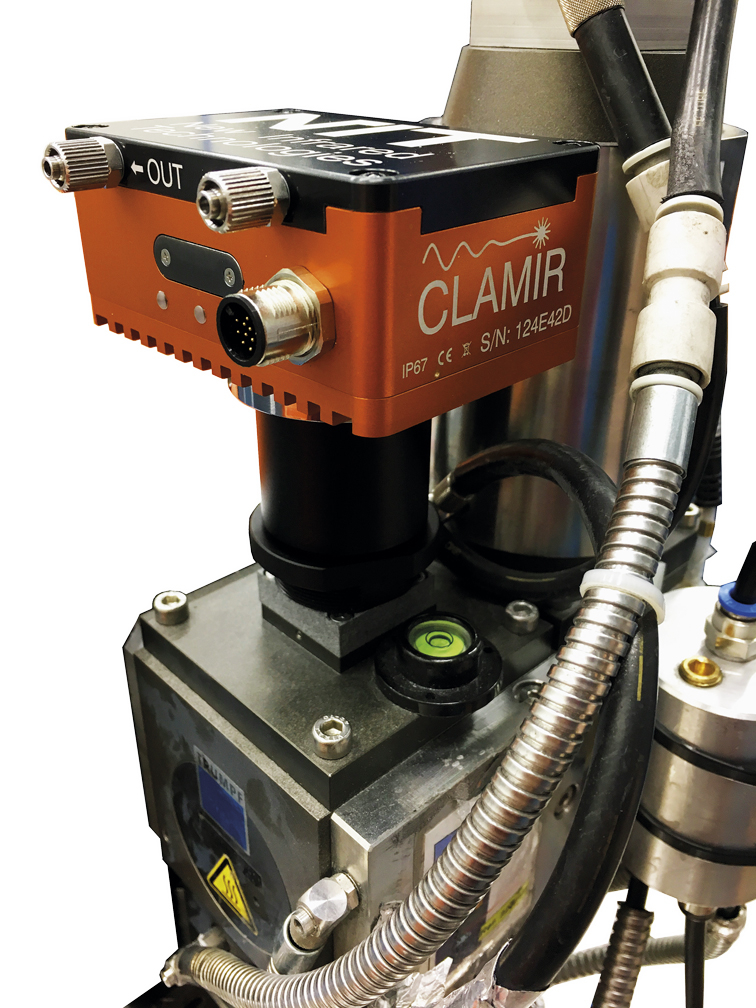
Aan de monitoringsystemen die gebruikmaken van high-speedcamera’s en spectrometers hangt vaak een fors prijskaartje. De componenten zijn namelijk niet goedkoop. In China hebben onderzoekers van de Southeast University in Nanjing daarom onderzoek gedaan naar de potenties van het registreren van optische emissies tijdens het lasercladden, in dit geval met 316L. Ze gebruikten hiervoor twee relatief goedkope fotodiodes waarmee ze abnormale situaties tijdens het cladden detecteerden. Door zowel de tijdsduur van het signaal als de frequentie te analyseren, slaagden de onderzoekers erin om een uitspraak te doen over de achterliggende oorzaak van de afwijking. Hierbij hielden ze rekening met factoren zoals de scansnelheid, het laservermogen en de poedertoevoer.
NIT Europe heeft voor het LMD-proces een monitoringsysteem ontwikkeld: Clamir. Dat maakt gebruik van de MWIR-cemara, die per seconde 1000 beelden maakt en in tegenstelling tot een CMOS-camera ook de temperatuur tijdens het afkoelen (onder 900 °C) toont.
Voor de verdere groei van 3D-lasercladden als een alternatief 3D-metaalprintproces is het belangrijk dat men het lasercladden nauwkeurig kan sturen en het proces reproduceerbaar wordt. Daarom is procescontrole zo belangrijk.
VUB zet eerste stap naar closedloopsysteem voor LMD
Onderzoekers van de Vrije Universiteit Brussel hebben begin september op een CRIP-conferentie over Photonic Technologies een presentatie gegeven over hun MiCLAD-platform.
MiCLAD is een hybridemachine die de VUB zelf ontwikkeld heeft: lasercladding en CNC-frezen ineen. De experimentele machine heeft een bereik van 450 bij 300 bij 300 mm, gebruikt een 2 kW-fiberlaser en een poedernozzle van het Fraunhofer ILT. Qua besturing grijpt men terug op de Bosch rexroth MTX 5-assige besturing. Met een hyperspectrocamera worden de beelden gemaakt van de materiaalverandering die door de software worden geanalyseerd voor temperatuurprofiel en lasersetpoint. Daarnaast heeft men een highspeedcamera toegevoegd met een warmteabsorberend IR-filter. Deze camera gebruikt men vooral voor de visuele inspectie van het smeltbad. De data die zo verzameld worden, schrijft de besturing elke milliseconde weg in de digitale tweeling van het product.
Met kunstmatige intelligentie zoekt men in deze digitale tweeling naar de optimale instellingen. De onderzoekers zeggen dat de complexiteit van het LMD-proces, waarbij veel parameters van invloed zijn op het eindresultaat, zich bij uitstek leent om met zelflerende algoritmen te werken. De vertraging van 1 ms waarmee het closedloopregelsysteem werkt, is in de praktijk goed hanteerbaar, zo blijkt.