COMMENT CONTRÔLER LE RECHARGEMENT LASER 3D?
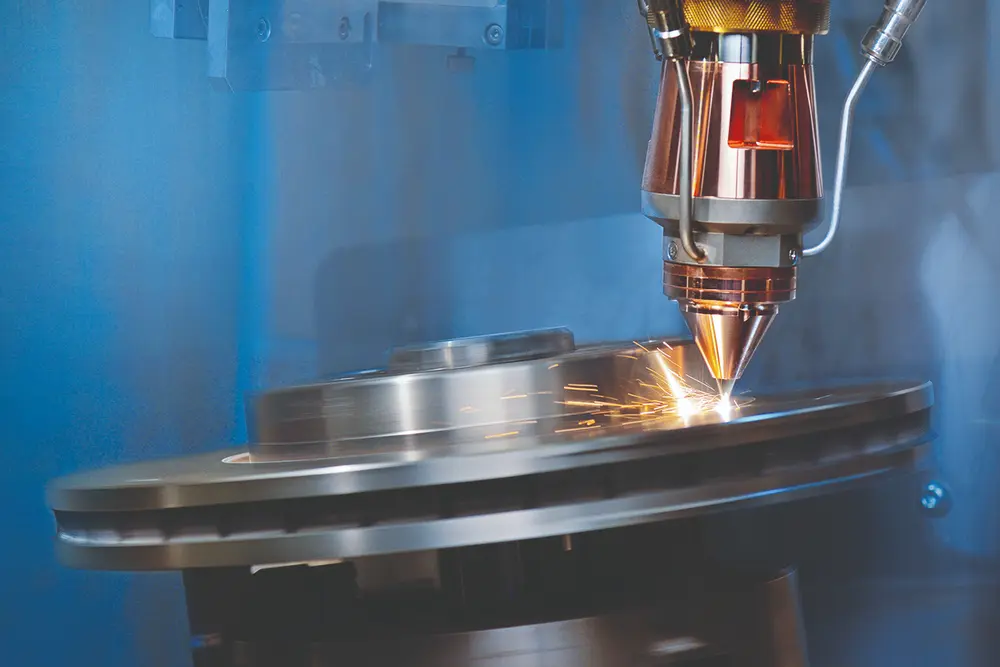
Cela fait longtemps que les chercheurs scientifiques et les entreprises du monde entier sont à la recherche du Saint Graal pour garantir la qualité des processus de rechargement laser. Comment contrôlez-vous et gérez-vous ce processus, qui est en fait un processus de soudage? C'est particulièrement important si vous comptez utiliser le rechargement laser pour l'impression 3D métal. La Smart Industry constitue une partie de la solution; les innovations dans les composants matériels en sont une autre. Ensemble, ils ouvrent de nouvelles possibilités.
Lisez la première partie sur les possibilités du rechargement laser ici
La qualité du rechargement laser, au sens de l'application d'un revêtement supplémentaire sur un produit, n'est plus remise en question aujourd'hui. Pour ces applications, le processus peut être adéquatement surveillé, contrôlé et donc validé. Il en va autrement lorsqu'on s'oriente vers le rechargement de formes 3D, officiellement appelé Directed Energy Deposition. L'un des défis à relever est la prévention de la porosité des matériaux composés.
Nouveau type de caméra
Divers facteurs influent sur ce point: de la précision du contrôle du flux de poudre - tant en termes de direction que de quantité exacte de combinaison poudre-gaz et de qualité des poudres métalliques - au contrôle du bain. Longtemps, les systèmes sont restés principalement basés sur des inspections visuelles de la géométrie et de la température du bain avec des caméras IR à haute vitesse. Mais cette méthode présente une limite: ces caméras n'enregistrent que peu ou pas de chaleur en dessous de 900°C, ce qui les rend 'aveugles' au processus de refroidissement du rechargement.
Les capteurs MWIR PbSe gèrent mieux la distribution de la température et fournissent ainsi une image plus complète
En outre, ces caméras CMOS sont très sensibles aux réflexions dans le champ infrarouge visible. Un nouveau développement est l'utilisation de la technologie des capteurs MWIR PbSe. Il s'agit d'un nouveau type de caméra qui détecte les longueurs d'onde courtes et moyennes de l'infrarouge et les capture à une fréquence de 1.000 images par seconde. La plage dynamique de ce nouvel appareil est beaucoup plus importante. Le principal avantage est que ces capteurs MWIR PbSe sont mieux à même de gérer la distribution de la température pendant la fonte du matériau. Ils fournissent ainsi une image plus complète.
En outre, la variation de la valeur mesurée est plus faible qu'avec les capteurs CMOS. Cela donne une image de la distribution de la température dans le bain qui contient beaucoup moins de bruit qu'avec d'autres technologies de mesure. Avec ce nouveau type de capteur, on obtient donc des résultats plus précis. Cela rend le système plus adapté à une utilisation dans un système en boucle fermée, qui ajuste les paramètres du processus en fonction des données en temps réel.
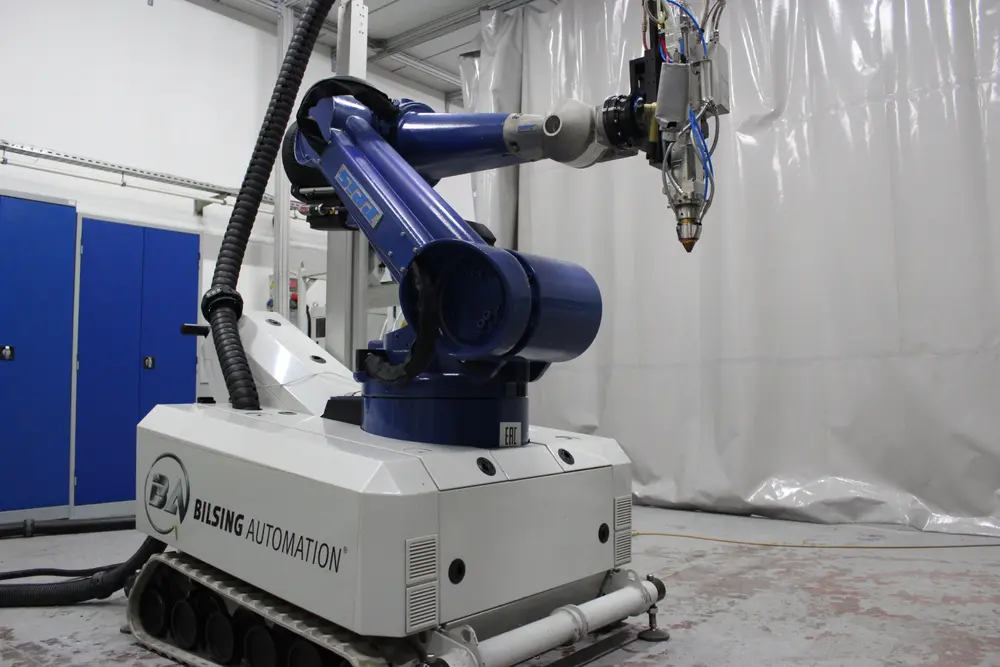
Distribution de poudre
Un autre facteur qui influence la qualité est la répartition des poudres métalliques dans la surface que l'on applique. Il s'avère que c'est un facteur crucial pour la qualité de la pièce. Une évolution assez récente en Allemagne consiste à mesurer cette distribution de poudre à l'aide d'une caméra qui mesure la réflexion à travers la buse. Il est ainsi possible de visualiser la répartition des particules métalliques en 3D, après quoi des modèles mathématiques calculent un certain nombre de chiffres clés sur base de la répartition mesurée. Plus les algorithmes sont alimentés en images, plus les résultats sont précis. Les résultats sont optimaux à partir d'environ 10.000 images. Ce système peut ensuite être utilisé pour contrôler le débit massique de la poudre avec plus de précision, rendant le processus plus prévisible et plus fiable.
Jusqu'à présent, c'était l'un des chaînons manquants dans le contrôle du processus de rechargement laser. Le dosage de la poudre était surtout contrôlé mécaniquement. En mesurant avec précision le flux de gaz de poudre et la distribution 3D et en documentant le processus, les données d'un processus précédent peuvent être récupérées pour la prochaine impression de cette pièce. Selon les chercheurs, cela fait du revêtement laser un processus reproductible.
Les scientifiques chinois utilisent cette approche pour réduire les contraintes dans la pièce en ajustant la façon dont la géométrie est construite à l'aide de modèles mathématiques. Selon ces chercheurs, une meilleure répartition de la poudre assure une structure de couche plus stable, ce qui devient de plus en plus important à mesure que les pièces rechargées sont grandes, par exemple les pièces structurelles des avions.
Température et position du point chaud
La température dans le bain et les couches environnantes reste cependant un facteur important. Une température non homogène peut entraîner des déviations géométriques de la pièce. C'est pourquoi les chercheurs continuent à améliorer l'imagerie thermographique du processus. Avec une caméra thermique, des images sont prises en 2D et en 3D pendant le processus de rechargement, ce qui est comparable à ce qui se passe en tomographie par ordinateur (CT). Ces images montrent les points faibles de la pièce et révèlent les défauts éventuels.
Les systèmes de surveillance utilisant des caméras à haute vitesse et des spectromètres ont souvent un prix élevé
Dans une étude récente de la Ruhr-Universität de Bochum (Allemagne), les chercheurs ont travaillé sur l'enregistrement simultané de la température dans le bain de soudure et du hot spot (point le plus chaud) dans la surface de mesure. Ils l'ont fait avec une seule caméra thermo-optique sur une installation de rechargement laser à 3 axes. Les données de température et la position du hot spot dans l'image enregistrée sont traitées en temps réel. Grâce à la position de la caméra infrarouge, à un angle de 45 degrés et sans déplacement par rapport à la buse, on peut calculer à partir des données la hauteur réelle de la paroi en cours d'impression. Comme le logiciel compare cette hauteur avec celle indiquée dans le modèle CAO, il est possible de compenser l'écart en temps réel.
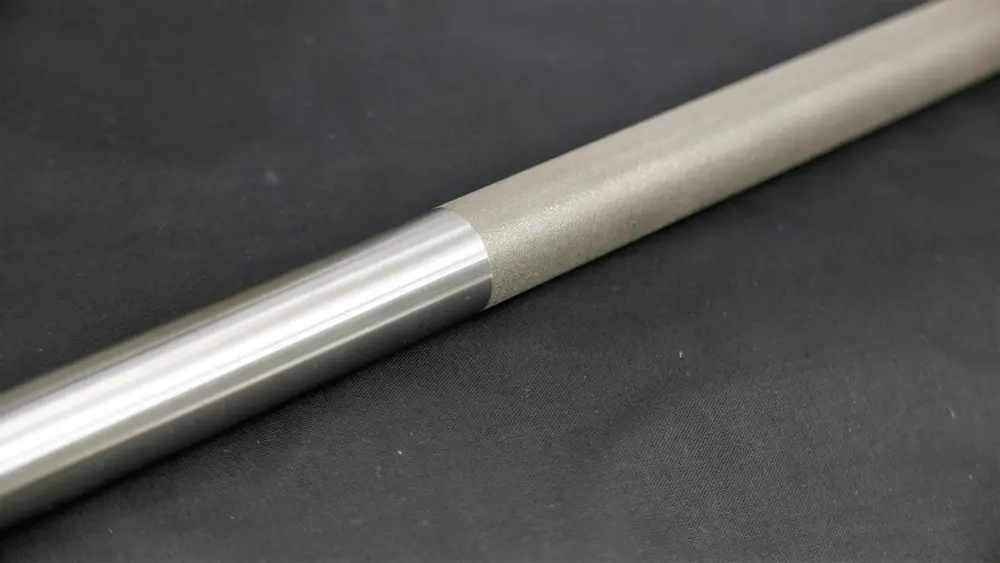
Une solution moins coûteuse
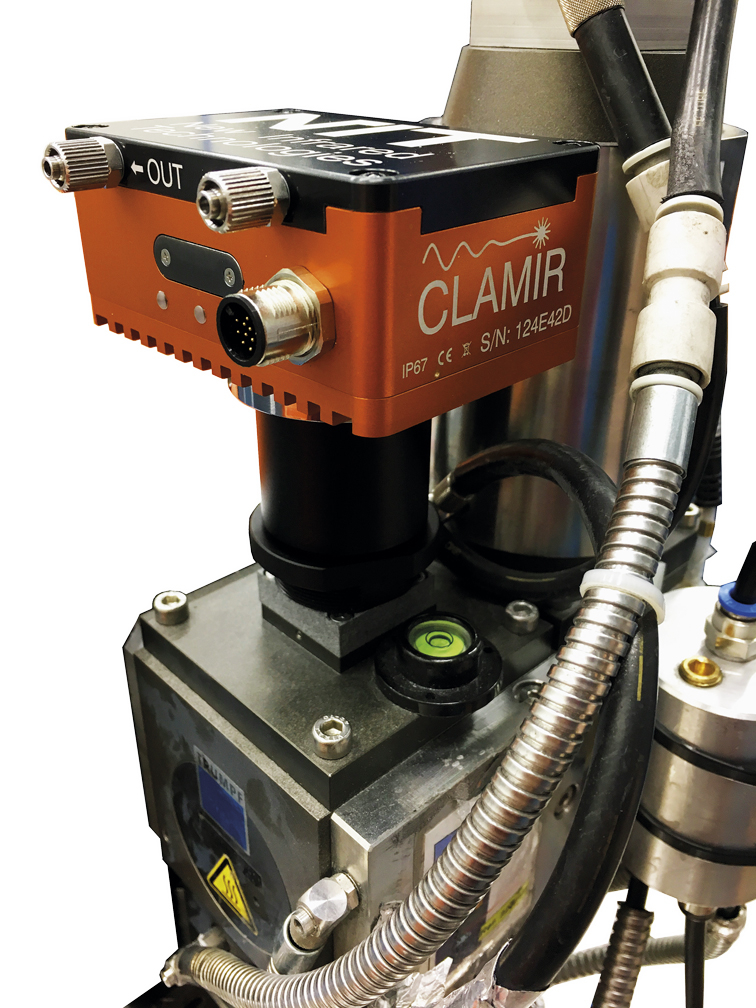
Clamir de NIT Europe est un système de surveillance du processus LMD
Les systèmes de surveillance utilisant des caméras à haute vitesse et les spectromètres ont souvent un prix élevé. Les composants ne sont pas bon marché. En Chine, des chercheurs de l'Université du Sud-Est à Nanjing ont donc étudié la possibilité d'enregistrer les émissions optiques pendant le rechargement laser, dans ce cas avec du 316L. Ils ont utilisé deux photodiodes relativement bon marché pour détecter les situations anormales pendant le processus de rechargement. En analysant à la fois la durée du signal et sa fréquence, les chercheurs ont pu se prononcer sur la cause sous-jacente de l'anomalie. Des facteurs tels que la vitesse de balayage, la puissance du laser et l'alimentation en poudre ont été pris en compte.
NIT Europe a développé un système de surveillance pour le processus LMD: Clamir. Il utilise la caméra MWIR, qui prend 1000 images par seconde et, contrairement à une caméra CMOS, montre également la température pendant le refroidissement (en dessous de 900°C).
Pour que le rechargement laser 3D continue à se développer en tant que procédé alternatif d'impression 3D métal, il est important de pouvoir le contrôler avec précision et de rendre le procédé reproductible. C'est pourquoi le contrôle des processus est si important.
La VUB fait un premier pas vers un système en boucle fermée pour LMD
Des chercheurs de la Vrije Universiteit Brussel ont présenté leur plateforme MiCLAD lors d'une conférence du CRIP sur les Photonic Technologies début septembre.
MiCLAD est une machine hybride développée par la VUB qui combine revêtement laser et fraisage CNC. La machine expérimentale a une portée de 450 par 300 par 300 mm, utilise un laser à fibre de 2 kW et une buse à poudre du Fraunhofer ILT. Le contrôleur 5 axes MTX de Bosch Rexroth est utilisé comme système de contrôle. Une caméra hyperspectrale est utilisée pour prendre des images du changement de matériau, qui sont analysées par le logiciel pour le profil de température et le point de consigne du laser. En outre, une caméra à haute vitesse avec un filtre IR absorbant la chaleur a été ajoutée. Cette caméra est principalement utilisée pour l'inspection visuelle du bain. Les données ainsi collectées sont inscrites dans le jumeau numérique du produit à chaque milliseconde.
L'intelligence artificielle est utilisée pour trouver les paramètres optimaux dans ces jumeaux numériques. Selon les chercheurs, la complexité du processus LMD, où de nombreux paramètres influencent le résultat final, se prête parfaitement au travail avec des algorithmes auto-apprenants. Il s'avère que le délai de 1 ms avec lequel fonctionne le système de contrôle en boucle fermée est facilement gérable dans la pratique.