Drempels voor 3D-metaalprinten worden lager
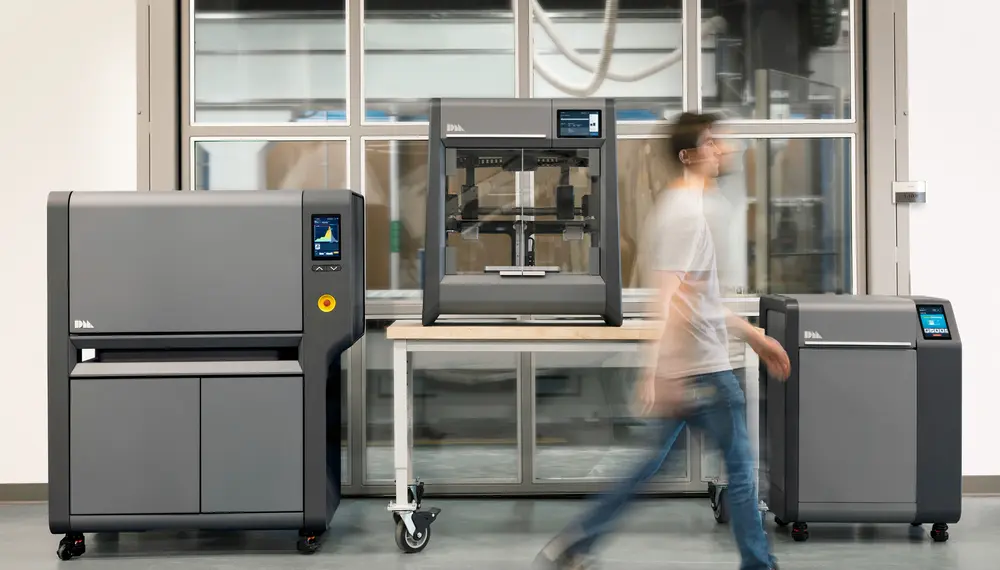
De drempel om in metal additive manufacturing te stappen is voor veel bedrijven te hoog. Stilaan komt daar verandering in door lowcostmetaalprinters en AM-systemen die aanzienlijk goedkopere materialen verwerken. Is dit het moment om te beginnen met 3D-metaalprinten?
Hoe groot is de markt?
De metaalprintmarkt is afgelopen jaar weer gegroeid, nadat de sector in 2020 onder druk kwam te staan door de rem op investeringen in met name de luchtvaart- en automobielindustrie. De dubbelcijferige groei in 2021 gaat zeker tien jaar aanhouden, verwachten sommige analisten. AMPower, een Duits consultancybureau, voorspelt dat komende jaren de markt voor metaalprinten met zo’n 26% zal groeien. IDTechEx, een Britse marktonderzoeker, rekent tot 2032 op een jaarlijkse groei van bijna 19%.
Dubbelcijferige groei klinkt indrukwekkend, zeker afgezet tegen groeicijfers van bijvoorbeeld de verkopen van werktuigmachines. Maar: het zijn cijfers van een zeer kleine markt, waarvan zelfs de exacte omvang niet bekend is. De Duitse machinebouwvereniging VDW zegt bijvoorbeeld geen cijfers te kunnen geven omdat er wereldwijd nog geen eenduidige afspraken gelden over de registratie van AM-machines.
De consultants van AMPower schatten dat er vorig jaar voor ongeveer 1 miljard euro aan metaalprinters is verkocht. Ter vergelijking: volgens de VDW werd in 2020 wereldwijd voor 4,3 miljard euro aan slijpmachines verkocht. Een nichemarkt, in een zwak jaar voor investeringen in werktuigmachines, maar die dus wel meer dan vier keer zo groot is als de markt voor metal additive manufacturing een jaar later.
De aandacht is er wel
Moet je de technologie dan links laten liggen? Nee, klinkt het bij de fabrikanten van AM-systemen. De omstandigheden in de wereldwijde toeleverketens zijn zodanig verstoord dat er een ideaal klimaat is ontstaan voor verdere groei van additive manufacturing. "Verstoringen worden het nieuwe normaal, iedereen lijdt hieronder", zegt Tali Rosman, die bij Xerox de 3D-metaalprintactiviteiten leidt.
Volgens een onderzoek van het Amerikaanse Gardner investeert 90 procent van de bedrijven momenteel in meer flexibiliteit om zich minder afhankelijk te maken van de grillen van lange supply chains. Deze ondernemingen zien additive manufacturing als een van de oplossingen, niet alleen om lokaal te produceren, maar ook om met additive manufacturing het aantal losse onderdelen terug te brengen en om voorraden te verkleinen door on-demand te gaan produceren.
Er moeten nog de nodige hindernissen worden weggenomen voordat additive manufacturing echt doorbreekt
Er moeten nog de nodige hindernissen worden weggenomen voordat additive manufacturing echt doorbreekt, geven ingewijden uit de industrie toe. Zo zijn er bijvoorbeeld betere en goedkopere materialen nodig. En moeten de AM-systemen eenvoudiger kunnen worden opgenomen in de digitale workflows waarmee de hele productie wordt aangestuurd.
Het vergroten van designkennis voor additive manufacturing is misschien wel de grootste uitdaging. Maar dat het beeld van metal additive manufacturing aan het kantelen is, staat voor de meesten vast. SmarTech schat dat de waarde van alle metalen geprinte onderdelen tegen 2030 zo’n $ 30 miljard aan waarde vertegenwoordigt.
En dan is metaal AM vertrokken. Hoewel tegen die tijd technieken als binder jetting, extrusie en Directed Eenergy Deposition (DED) ook hun plek hebben gevonden, verwacht analist Scott Dunhamm dat de laser powderbed fusion (PLBF)-technologie dominant blijft.
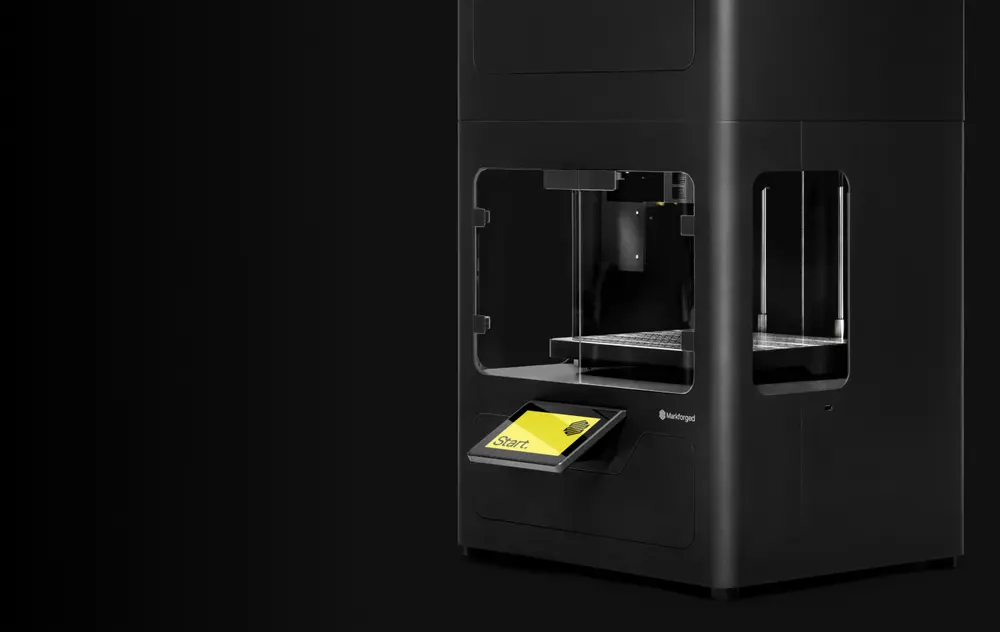
Markforged heeft vorig jaar de tweede generatie van de MetalX gepresenteerd, de metaalprinter die werkt met filament dat grotendeels gevuld is met metaalpoeder
Low cost AM-oplossingen
Tot nog toe laten kmo’s en ook grotere bedrijven de technologie links liggen, onder andere vanwege de hoge investeringen. Dikwijls lopen die in de vele honderdduizenden euro’s en komen er nog extra investeringen bij voor bijvoorbeeld poederopslag, gas, handling etc. Een aantal partijen heeft daarom oplossingen ontwikkeld die aanzienlijk goedkoper zijn. Voor ongeveer 100.000 euro zijn er tegenwoordig al poederbedmetaalprinters.
Daarnaast zijn er zowel materiaal- als printerfabrikanten die beloven dat ze met filamentmetalen onderdelen kunnen printen. Hoe bruikbaar zijn die lowcost-AM-systemen? Heel bruikbaar, zeggen de analisten, die verwachten dat de lagere instapdrempel de markt een impuls kan geven. Fabrikanten zoals Xact Metal en Kurtz Ersa gebruiken goedkopere laserbronnen in hun machines met een grotere focusdiameter; soms plaatsen ze zelfs het optiek op een cartesisch assenstelsel dat in X- en Y-richting beweegt.
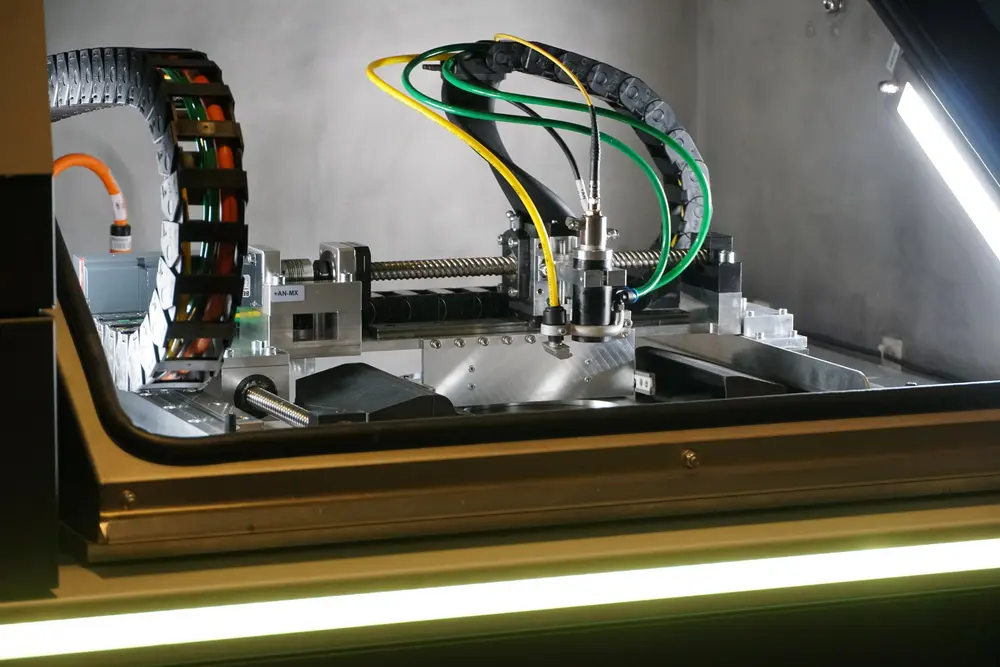
Een lagere straalkwaliteit en grotere focusdiameter hebben wel effect op de oppervlaktenauwkeurigheid van een metaalprinter, maar dat is geen onoverkomelijk bezwaar. Het grote voordeel is dat de fabrikanten hierdoor de kostprijs kunnen drukken. Naast het ontwikkelen van goedkopere AM-systemen proberen deze nieuwkomers ook het hele proces te vergemakkelijken.
One Click Metal, oorspronkelijk gestart door enkele Trumpf-medewerkers en inmiddels voor het grootste deel in handen van Index Werke, gebruikt bijvoorbeeld cartridges waarin het poeder zit. Hiermee vereenvoudigt het de hele poederhandling en neemt daarmee een drempel weg. Ook via de software, die in de cloud draait, vereenvoudigt men het printproces, alles om de instapdrempel lager te maken.
Met vaste materialen printen
Poeder is een onderwerp van voortdurende discussie. Metaalpoeders zijn duur, enerzijds vanwege een kostbaar productieproces, anderzijds omdat het aanbod nog klein is. Poeders vergen bovendien extra investeringen in een veilige opslag. Sommigen fabrikanten kiezen daarom voor een andere insteek qua materiaal. Markeforged en Desktop Metal doen dat bijvoorbeeld. De eerste gebruikt filament, de tweede cassettes waarin staafjes zitten. In beide materialen is een hoog aandeel metaalpoeder verpakt in een polymeer bindmiddel.
Deze aanpak vergt vaak een debinding stap, soms geïntegreerd in de sinteroven, en sinteren om een hoge dichtheid te bereiken. Tijdens het sinteren treedt er krimp op; gemiddeld krimpt het werkstuk in alle richtingen zo’n 20 procent, omdat de metaaldeeltjes vrijwel volledig met elkaar versmelten en de ruimten waar eerst polymeer bindmiddel zat opvult. Uiteindelijk kan men, aldus de fabrikanten, een dichtheid in het werkstuk halen die op 99% of hoger ligt.
Door gebruik te maken van het complete systeem – 3D printer en sinteroven - is de krimp goed voorspelbaar en wordt het sinterproces volledig gestuurd vanuit de software, waarin men slechts een klein aantal parameters hoeft in te geven. Het voordeel van het sinteren is dat alle restspanningen uit het werkstuk zijn. Bij poederbedsystemen moet men, als restspanningen een probleem zijn, vaak nog een thermische nabehandeling doen. Omdat het sinteren gecontroleerd gebeurt, vervormen de onderdelen nauwelijks, wat bij de poederbed systemen wel eens wil gebeuren.
Het Spaanse Meltio is een van de nieuwkomers als het om DED-technologie gaat. Er wordt geprint met lasdraad. Op deze video is (versneld) te zien hoe met een robot en een draaizwenkas producten worden geprint zonder dat supportstructuur nodig is.
Er zijn ook aanbieders die metaalgevuld filament op de markt brengen dat met min of meer gewone FFF-printers verwerkt kan worden. Een industriële sinteroven is dan nog noodzakelijk, soms zullen bedrijven deze hebben. In dat geval liggen de investeringen fors lager, omdat de sinteroven doorgaans een van de kostbaarste onderdelen van het systeem is. Bedrijven zullen dan zelf hun instellingen moeten ontwikkelen om de krimp van de onderdelen te beheersen. Hier speelt dus de keuze snelheid en gemak versus méér tijd voor applicatie ontwikkeling en het investeren van meer kennis.
Onderzoekers van de universiteit Arts et Metiers in het Franse Lille hebben begin dit jaar hun concept voor Hardware X in een wetenschappelijk artikel beschreven. Ze beschrijven hierin een concept voor een lowcost-3D-metaalprinter die gebruikmaakt van pellets waarin het metaalpoeders zit opgesloten. De productie van de met metaalpoeder gevulde pellets is eenvoudiger en dus goedkoper dan van metaalgevuld filament.
De wetenschappers hebben de HardwareX zelf gebouwd en getest met 316L. De eerste resultaten zijn. Gecombineerd met CNC-frezen (eventueel in dezelfde machine) komen er bruikbare onderdelen van de machine. Hun systeem kan metaal additive manufacturing dichterbij de industriële productiestandaarden brengen.
Bij alle hiervoor beschreven technieken, zowel de goedkope poederbedsystemen als de filamentsystemen, is support nodig tijdens het 3D-printen. Desktop Metal en Markforged printen beide een tussenlaag tussen support en werkstuk, zodat de supportstructuur eenvoudig verwijderd kan worden. Dat scheelt tijd en dus kosten in de nabewerking.
Bedenk wel: deze oplossingen hebben pas zin als het ontwerp van het onderdeel wordt aangepast om maximaal profijt te halen uit het 3D-metaalprinten.
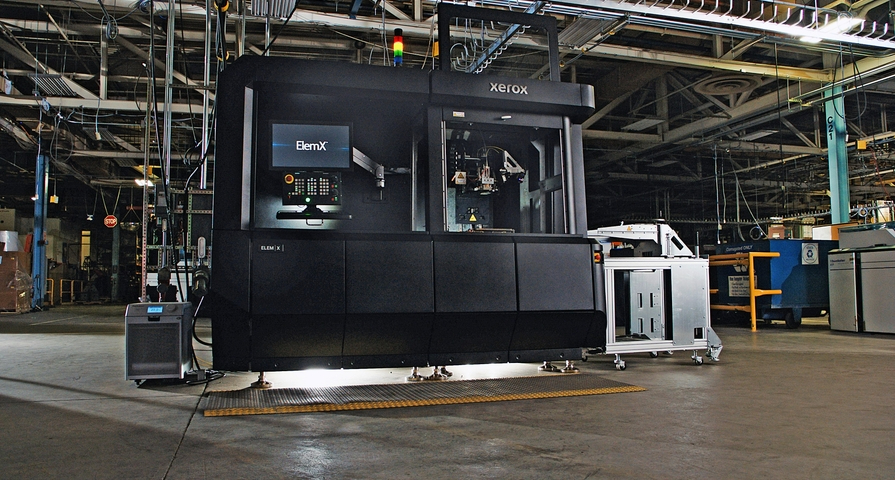
De Liquid Metal Printing-technologie van Xerox gebruikt goedkoop materiaal (aluminium lasdraad) en is snel. Daar staat tegenover dat de dichtheid met 98,5% lager is dan bij poederbedsystemen en de tolerantie van 0,6 mm in XY-richting lager is dan bij de klassieke systemen
Goedkopere materialen
Een derde piste om de kosten per 3D-geprint onderdeel te verlagen, is het 3D-printen met standaard lasdraad, die gesmolten wordt door een laserstraal. Deze DED-systemen (Directed Energy Deposition) bestaan al langer. Nieuwe spelers in de markt slagen er echter in om de eigenschappen van de onderdelen die men print op een niveau te brengen van gietwerk, soms zelfs iets beter.
Er zijn fabrikanten die een materiaaldichtheid van meer dan 99,9% beloven met een fijne microstructuur. Dat zijn eigenschappen die boven die van smeed- en gietstukken liggen. De DED-systemen, beschikbaar als complete machine of als printunit voor inbouw in een CNC-machine, of te combineren met een robot, kosten weliswaar nog steeds meer dan € 100.000, maar vooral de lage materiaalprijzen drukken het kostenplaatje per geprint onderdeel. De technologie is bovendien veel eenvoudiger dan de LPBF-systemen.
Daarnaast kan men in sommige van deze systemen meerdere soorten draad combineren, zodat onderdelen geprint kunnen worden die uit meerdere legeringen zijn opgebouwd. Deze systemen kennen zeker hun beperkingen vergeleken met een laserpoederbedsysteem, zo kan men met deze laatste complexere inwendige structuren printen. Maar er zijn in de metaalindustrie legio toepassingen waarvoor DED-technologie een goede oplossing is.
Door near net shape te printen voorkomt men dat er veel materiaal verspaand moet worden
Bovendien kan men in combinatie met een 4e en 5e as waarop het product zit, zonder supportstructuur printen. Deze systemen spelen in op nog een onderwerp dat komende jaren aan belang zal winnen: terugdringen van materiaalverspilling. Door near net shape te printen voorkomt men dat er veel materiaal verspaand moet worden. Sommige aanbieders, zoals het Spaanse Meltio, bieden naast volledig geïntegreerde machines ook losse koppen aan om zelf te integreren in een CNC-machine of met een robot. Andere, zoals Gefertec (tegenwoordig gedeeltelijk in handen van EMAG) bieden een complete machine aan.
Ook het Amerikaanse Xerox gebruikt aluminium lasdraad, een goedkoop materiaal dus. De technologie van Xerox is echter anders: het gesmolten aluminium wordt in de vorm van hele kleine druppels (Liquid Metal Printing) op het werkstuk ‘gejet’ waardoor het werkstuk zich snel opbouwt. Ook voor deze technologie geldt dat de investering weliswaar fors is, maar dat de materiaalkosten zeer laag zijn en de opbouwsnelheid hoog: men 3D print 220 gram aluminium per uur. De nauwkeurigheid beperkt zich in X-Y-vlak tot 0,6 mm.
In België werkt Valcun aan een technologie, Molten metal Deposition, waarmee 3D-metaalprinten goedkoper zou worden. De startup uit Gent gebruikt extrusietechnologie (FDM) om metalen onderdelen te printen. Hiervoor gebruikt het willekeurige feedstock, zelfs gerecycled metaal als het moet. Doordat het een continu extrusie inzet, verloopt het proces snel. Valcun wil het beeld dat 3D-metaalprinten duur is, doorbreken. Toepassingen ziet het onder andere in near-net-shapeproducten en in warmtewisselaars.
3D-metaalprinten hoeft dus niet 'duur' meer te zijn. Er zijn oplossingen die binnen handbereik liggen van een kmo die gewend is € 100.000 of meer aan een CNC-bewerkingscentrum uit te geven.
Het is misschien niet eens de lagere kostprijs maar vooral het gebruiksgemak van de nieuwe systemen die de drempel om in 3D-metaalprinten te stappen, weghalen.