Les tendances à surveiller en matière de fabrication additive
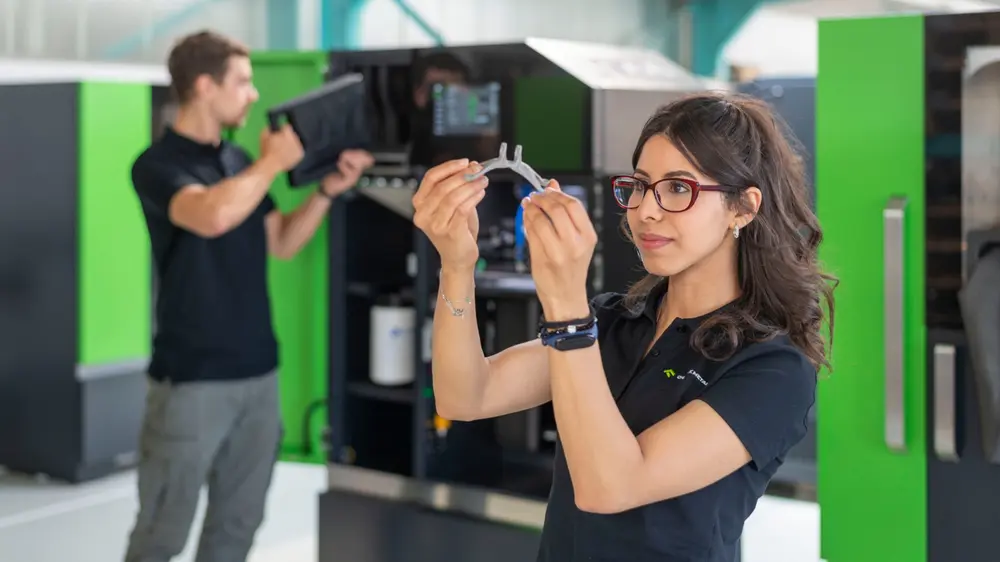
L'industrie de la fabrication additive a toujours été optimiste quant à sa croissance. Néanmoins, 2020 a été une moins bonne année pour le secteur, mais cela a été rattrapé en 2021. Où en est l'industrie de l'AM aujourd'hui? Quelles sont les tendances pour l'impression 3D métal? La technologie va-t-elle percer en 2022 grâce à de nouvelles techniques moins coûteuses?
Situation du marché
Le marché de l'impression 3D métal a continué à se redresser en 2021 après le creux causé par la pandémie de corona: pour la première fois depuis de nombreuses années, les ventes d'imprimantes 3D métal ont légèrement diminué en 2020.
Cela s'explique en partie par le fait que les constructeurs d'avions et les principaux fournisseurs ont freiné des quatre fers au début de la crise. Au second semestre, cette perte a été largement compensée par l'industrie aérospatiale américaine et de nombreuses startups qui ont investi massivement dans la fabrication additive. Le bureau de recherche allemand Ampower conclut dans une étude récente que les Etats-Unis sont actuellement - et de loin - le plus grand marché pour la fabrication additive, avec les taux de croissance les plus élevés. La Chine est le deuxième marché le plus important, grâce au développement de sa propre industrie aéronautique, suivie par l'Allemagne.
Selon les chercheurs, l'industrie automobile est un autre secteur qui a réduit ses investissements dans l'AM. Toutefois, cette branche industrielle connaît une reprise rapide.
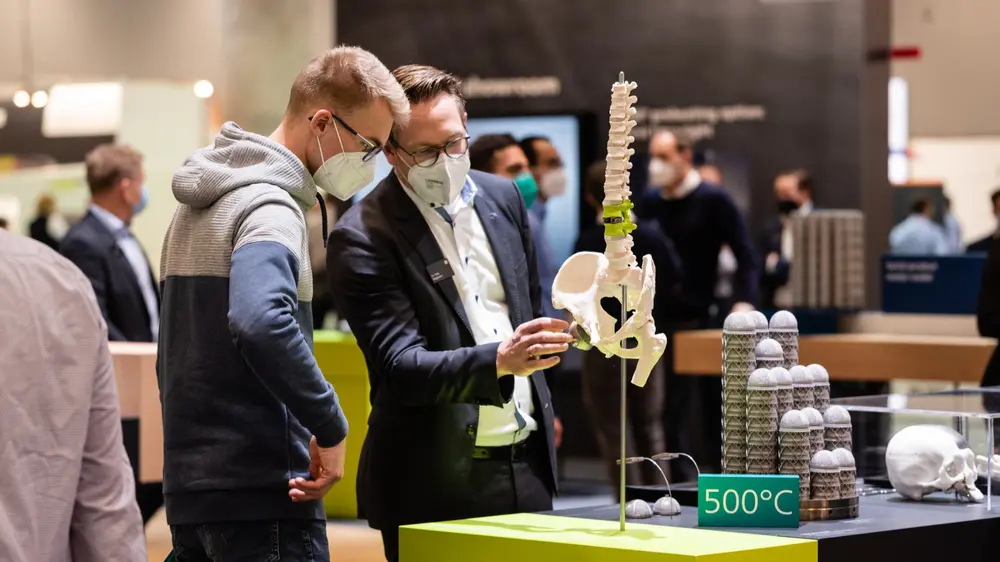
Plus de lasers
Le coût par pièce issue d'une machine d'AM doit baisser afin d'augmenter substantiellement le nombre d'applications. L'augmentation de la productivité est une solution à ce problème.
La baisse des coûts mènera à un nombre d'applications élevé
Les fabricants y ont déjà remédié en partie en équipant leurs machines de davantage de lasers. Les systèmes laser doubles et quadruples sont courants depuis plusieurs années. Pendant longtemps, on s'est limité à quatre lasers mais la première imprimante 3D métal dotée de 12 lasers de 1 kW a été présentée récemment. Combiné à un grand volume de construction, cela permet d'obtenir une production nettement plus élevée dans le même temps (au moins 5 fois plus rapide). La productivité, quant à elle, peut être multipliée par 10 à 20.
Cependant, tout le monde ne pense pas que la multiplication des lasers soit la solution pour réduire le coût des pièces. Elle entraîne plus de chaleur dans la chambre de fabrication, ce qui rend le processus plus difficile à contrôler. Les machines de fabrication additive laser sur lit de poudre nécessitent déjà un bon contrôle du processus pour éviter les déformations dues à la chaleur et le développement de microfissures.
Optimisation des processus
D'autres fabricants estiment qu'il est encore possible de réaliser des bénéfices suffisants en optimisant l'ensemble du processus. Une solution courante consiste pour les fabricants à augmenter l'Overall Equipment Effectiveness de leurs systèmes. Certaines sociétés d'AM ont un objectif initial de 75% de temps de fonctionnement effectif des machines. Cela nécessite tout d'abord un processus stable. Les logiciels de surveillance et les systèmes de contrôle du bain de soudure doivent y contribuer. Des recherches récentes ont également montré que l'influence du flux de gaz peut être plus importante qu'on ne le pensait. L'ajout d'hélium à l'argon semble conduire à un processus plus stable et donc à une productivité plus élevée.
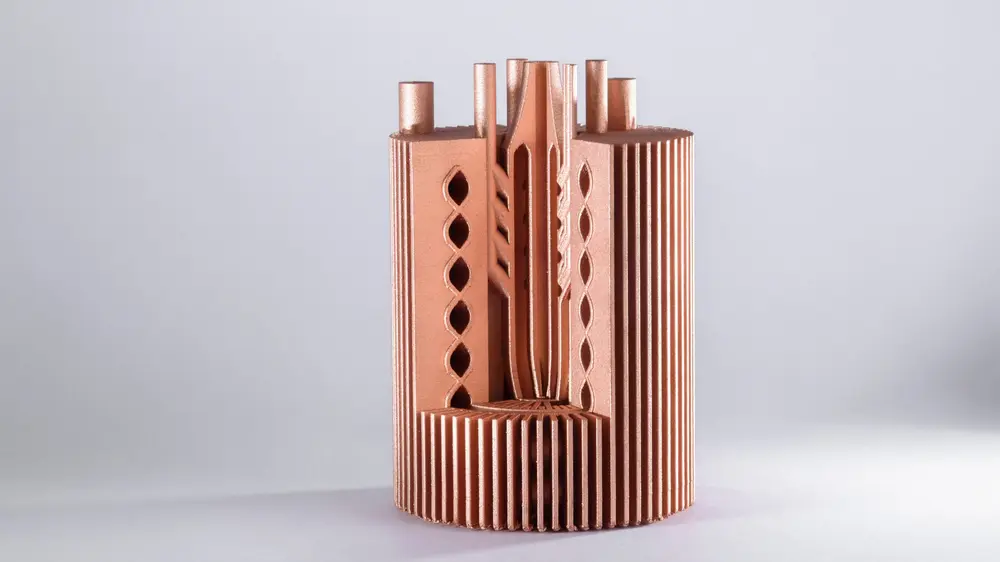
Réduire les structures de support
La possibilité de réduire le nombre de structures de support est une autre possibilité pour augmenter la productivité. Ce support n'est pas seulement imprimé lorsqu'il y a un surplomb dans la pièce, mais aussi pour dévier la chaleur de la pièce vers la plaque de construction. Les coûts des structures de support sont relativement élevés. En effet, elles nécessitent des matériaux coûteux pendant le processus d'impression et doivent être retirées par la suite, ce qui coûte du temps et donc de l'argent.
Utiliser moins de structures de support peut augmenter la productivité
La quantité de support peut être réduite en positionnant la pièce différemment sur la plaque de construction. Des logiciels de simulation de plus en plus performants sont disponibles à cet effet. Cela peut également être fait en ajustant les paramètres du processus. Il existe aujourd'hui sur le marché plusieurs imprimantes 3D métal qui nécessitent beaucoup moins de structures de support et permettent également d'empiler des produits dans la chambre de fabrication, ce qui est possible depuis un certain temps avec l'impression 3D par fusion de faisceau d'électrons, par exemple. Cela permet également de réduire le coût par pièce imprimée. Une meilleure intégration avec le post processing peut également contribuer à réduire le coût par pièce imprimée en 3D. Et la quatrième piste consiste à simplifier le flux de travail.
L'intégration arrive
Toutefois, ce flux de travail est une pierre d'achoppement lorsqu'il s'agit de produire réellement en série avec la fabrication additive. Les différentes étapes de la préparation d'une impression 3D et de la finition mécanique doivent se dérouler dans des programmes différents. Toutefois, la situation évolue progressivement.
Plusieurs développeurs de FAO se sont lancés dans la fabrication additive et intègrent la préparation du travail pour l'imprimante 3D dans l'environnement logiciel où est effectuée la préparation du travail pour la finition mécanique. Certains ajoutent également un logiciel de simulation du processus d'impression, afin de réduire le risque de déformations dues à l'apport de chaleur. Cela permet d'automatiser en partie la préparation du travail de construction et de saisir les connaissances et de les combiner avec les réglages spécifiques d'une machine AM. L'un des obstacles que les fabricants de logiciels ont dû surmonter était la combinaison de données maillées et de données CAO dans le même environnement logiciel. Cette percée a été accélérée par le développement par Siemens du noyau de modélisation Parasolid, qui est maintenant utilisé par plus de 200 développeurs de logiciels.
Le fraisage adaptatif ressort également. Comme pour les pièces moulées, les pièces fabriquées de manière additive ne sont jamais exactement identiques en termes de dimensions. En mesurant la pièce dans la machine-outil à l'aide d'un palpeur, puis en corrigeant le programme CN pour les écarts par rapport au modèle CAO, le post-traitement peut être davantage automatisé.
Besoin de machines accessibles
Il y a une autre lacune dans le flux de travail. Jusqu'à récemment, certains grands fabricants de systèmes d'impression 3D métal n'étaient pas disposés à permettre à des logiciels tiers d'accéder aux données des machines. Progressivement, cela commence à changer, car ils reconnaissent que les logiciels, les algorithmes d'apprentissage automatique et l'intelligence artificielle seront des éléments importants du futur processus d'AM. C'est pourquoi on voit apparaître aujourd'hui des systèmes plus ouverts.
Au printemps 2021, la Commission européenne a publié un rapport sur l'importance de la législation et des règlements pour réglementer précisément ce type de questions. Les auteurs du rapport espèrent que la réglementation contribuera à accroître l'interopérabilité des systèmes d'AM. Cela devrait donner aux acheteurs une plus grande confiance dans la technologie.
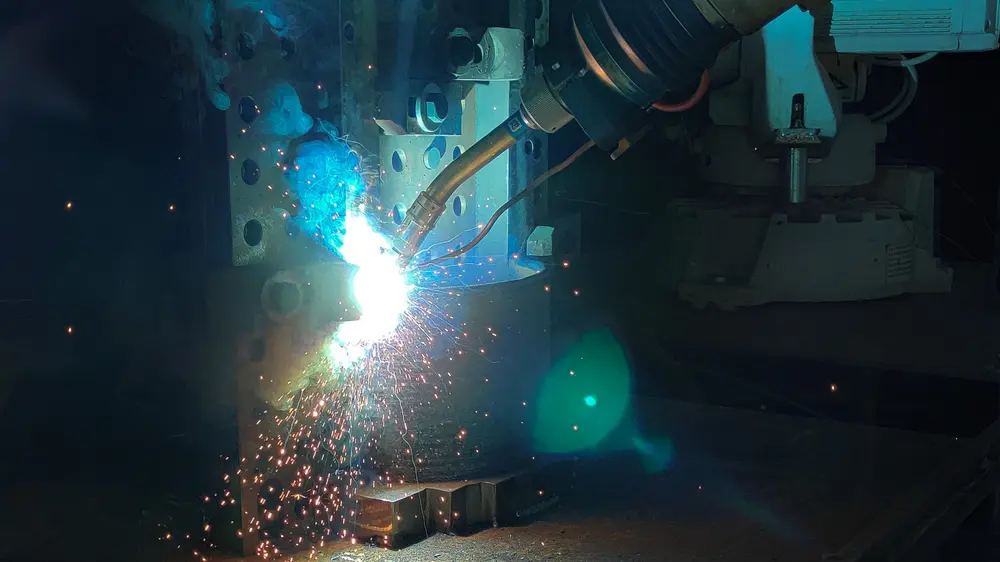
De nouvelles techniques sur le point de percer
Pendant des années, la fusion laser sur lit de poudre a été la technologie d'impression métal par excellence. C'est toujours le cas, mais les marchés commencent à changer. Ampower prévoit que d'ici 2025, les techniques alternatives gagneront des parts de marché au détriment de la technique classique. Les deux technologies AM à surveiller sont le Binder Jetting et le Directed Energy Deposition. Deux acteurs dans le domaine du Binder Jetting sont Desktop Metal et HP; les fabricants proposant la technologie DED sont plus nombreux. Il s'agit de systèmes qui utilisent un fil ou une poudre pour la soudure. Pensez aux systèmes tels que ceux utilisés par Mazak et DMG Mori dans leurs machines hybrides, ou la machine AM de Chiron.
Les deux technologies AM à surveiller sont le Binder Jetting et le Directed Energy Deposition
Directed Energy Deposition
Récemment, de nombreux signes positifs d'applications de la technologie DED ont été observés. L'industrie pétrolière et gazière est l'un des secteurs où cette technologie est très utilisée. Elle veut utiliser la fabrication additive pour réduire le stock de pièces de rechange pour les installations coûteuses. Ces stocks sont désormais maintenus car l'immobilisation d'une plateforme pétrolière ou d'une usine pétrochimique est très coûteuse, jusqu'à 1 million d'euros par jour. La fabrication additive raccourcit les délais de production et est adaptée aux séries de taille 1. Elle permet de réduire les stocks et de produire localement.
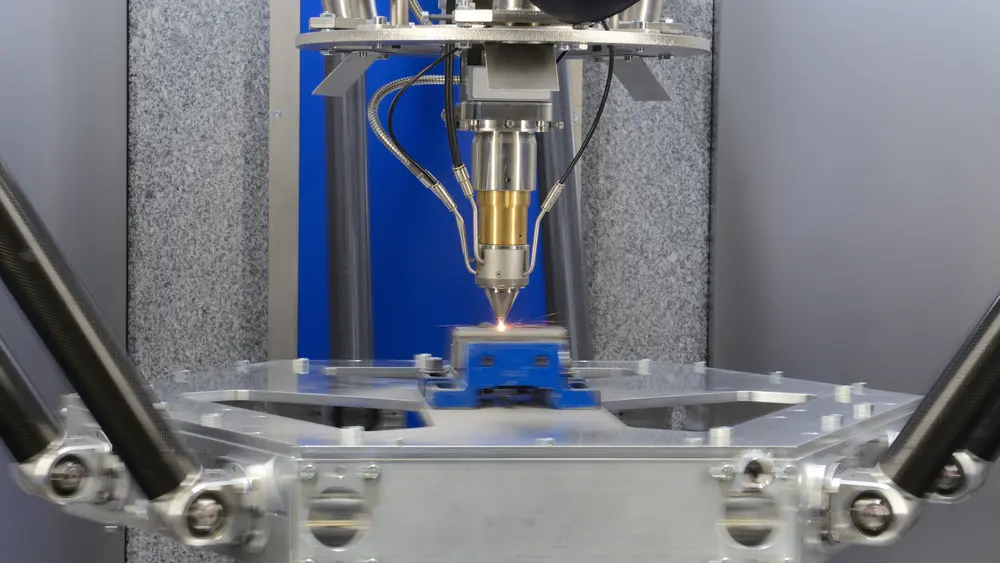
Les principaux avantages de la technologie DED sont que l'on peut produire des pièces de grande taille et que l'accumulation de matériau est beaucoup plus rapide qu'avec les machines à lit de poudre. Cette technologie permet également de combiner plus facilement plusieurs alliages dans une seule pièce, car il est possible de combiner des poudres ou des fils de soudure. Pensons par exemple à un outil dans lequel on utilise du cuivre pour une dissipation rapide de la chaleur et une couche supérieure en Inconel pour la résistance à l'usure. La durabilité est également un problème. Avec la technologie DED, l'impression 3D peut se poursuivre sur les matériaux existants. Il est ainsi possible de réparer des outils usés et coûteux. La qualité de ces pièces AM a été démontrée dans plusieurs projets de recherche. Cette technologie se prête également à des pièces moins critiques, par exemple dans la construction mécanique. Depuis l'apparition de la pandémie de corona, de nombreux équipementiers ont pris conscience de ce phénomène, car ils y voient une solution possible pour devenir moins dépendants des lignes d'approvisionnement vulnérables en provenance de Chine, par exemple.
Binder jetting
Le Binder Jetting est l'autre technologie d'impression sur métal dont on attend beaucoup. L'un des avantages est qu'il n'y a pas de chaleur dans les pièces. En outre, les structures de support sont inutiles. Comme les matériaux sont souvent basés sur ceux utilisés dans le moulage par injection de métal (MIM), on utilise souvent la même norme. Selon la plupart des fabricants, les pièces répondent aux normes internationales de la technologie MIM ou sont même meilleures. Ils soulignent toujours la différence entre les poudres MIM, qui contiennent jusqu'à 93% de poids de particules métalliques, et les poudres d'impression 3D, qui en contiennent jusqu'à 99%. Il y a donc moins de liant à retirer dans ces produits. Les fabricants affirment que la projection de liant permet d'obtenir une meilleure structure de grain isotrope du matériau que la fusion au laser. Comme ce procédé dégage peu de chaleur, les pièces peuvent être imbriquées, ce qui réduit le coût par pièce.
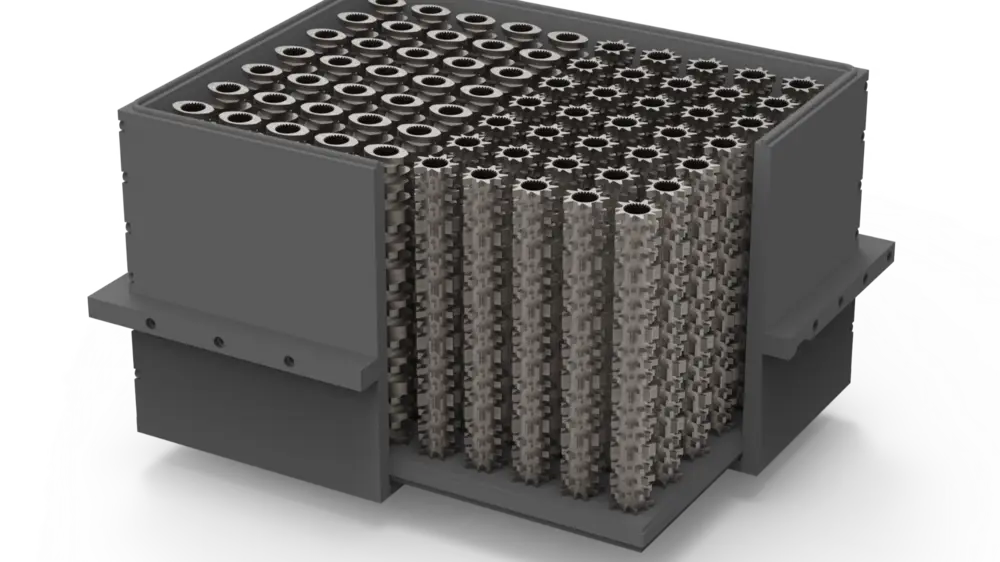
Les inconvénients sont que la technique est principalement adaptée aux petites pièces et que l'étape de frittage nécessite une grande expertise ou une solution intégrée; système AM avec four de frittage contrôlé par un système central. La grande percée se fait encore attendue.
Impression métal à faible coût
Les investissements nécessaires pour lancer l'impression 3D métal sont élevés. Que l'on investisse dans la fusion sur lit de poudre laser ou dans un système de jet de liant, le coût d'un système d'AM orienté vers la production peut facilement aller de quelques centaines de milliers d'euros à plus d'un million d'euros. Certains acteurs plus modestes pensent que ce seuil est trop élevé, notamment pour les PME, et proposent donc des solutions peu coûteuses.
Des solutions à peu coûteuses peuvent abaisser le seuil d'investissement
Le remplacement d'un laser à fibre de haute qualité par un laser à diode de qualité inférieure, par exemple, contribue à réduire les coûts d'un système de fusion sur lit de poudre. Dans ce cas, le système complexe de miroirs (système galvo) peut également être supprimé. Il sera remplacé par un système mécanique moins coûteux. Le laser à diode est placé sur un système de coordonnées cartésiennes. Cela entraîne une perte de vitesse et de précision, mais pour les petites pièces et les pièces qui sont de toute façon post-traitées mécaniquement, cela ne doit pas être un problème insurmontable. Ces fabricants accordent également beaucoup d'attention à la simplification du fonctionnement de l'imprimante 3D métal.
On assiste également à l'émergence de nouvelles techniques d'AM qui promettent de rendre le processus beaucoup plus simple, de réduire le coût des matériaux et de produire des pièces d'une qualité proche de celle des pièces moulées. Liqiuid Metal est un exemple d'une telle technologie, qui fonctionne avec un fil de soudure standard qui est fondu. Grâce à une technique spéciale, d'innombrables petites gouttes du matériau liquide sont déposées par jet sur la pièce à construire. Dans la dernière étape, les pièces subissent un traitement thermique pour éliminer les contraintes du matériau. Les procédés d'impression lithographique sur métal constituent un autre développement, basé sur la technologie d'impression de céramique technique. Dans ce cas, la poudre métallique est dispersée dans une pâte qui est exposée avec un projecteur numérique.
Inspirés par les imprimantes Markforged et Desktop Metal, les fabricants de filaments et les développeurs d'imprimantes de bureau FFF ont commencé à expérimenter l'impression 3D avec des filaments largement remplis de poudre métallique. Avec une imprimante FFF industrielle, les gens impriment en 3D des pièces qui doivent ensuite, en fonction du filament, passer par une ou deux étapes supplémentaires pour obtenir une pièce en métal. La première étape est le déliantage: il s'agit de retirer le composant polymère. Cela peut se faire par voie thermique ou catalytique. La deuxième étape est le frittage. Certains combinent les deux étapes. Après frittage, la densité de ces pièces est comparable à celle d'un moulage fin. La surface est rugueuse, mais peut être bien post-traitée. Le plus grand avantage de cette approche est que les investissements sont extrêmement faibles. En outre, il s'agit d'une technologie assez simple. Les inconvénients sont les multiples étapes du processus et le fait que le frittage nécessite souvent des fours de frittage spéciaux et coûteux, ainsi que des connaissances spécifiques.
Impression 3D indirecte
Outre les coûts d'investissement élevés, les projets d'impression 3D sur métal échouent souvent à cause des certifications des matériaux. L'impression 3D indirecte évite ce dernier cas. L'impression en 3D de moules devient particulièrement intéressante pour les entreprises de traitement des composites. De nouveaux matériaux dotés de meilleures propriétés, qui améliorent la durée de vie des moules, et la disponibilité d'imprimantes 3D grand format ouvrent de toutes nouvelles possibilités. Les temps de passage sont beaucoup plus courts que lors du fraisage des moules. En particulier maintenant que la réduction du poids est à l'ordre du jour dans de nombreuses applications, il est utile de ne plus avoir à fabriquer des outils coûteux pour des pièces uniques ou des petites séries. Des recherches sont même en cours pour savoir si un moule imprimé en plastique suffira pour les prototypes de pièces en tôle.
Nous parlons donc d'une application indirecte de l'impression 3D. L'industrie automobile s'y intéresse aussi beaucoup, mais pour des outils métalliques produits de manière additive. L'avantage est que le processus de production existant peut être maintenu, et que l'on peut continuer à travailler avec les matériaux validés et parfois certifiés. L'investissement dans un outil coûteux n'est pas nécessaire. Cela réduit le risque et permet de commercialiser plus rapidement un nouveau produit. En effet, la production d'un outil prend vite plusieurs semaines, voire plusieurs mois. L'expérience des constructeurs automobiles allemands montre qu'avec ces inserts fabriqués de manière additive dans le traitement des tôles, il est possible d'atteindre des durées de vie de plusieurs centaines de milliers de cycles de presse. Grâce à un meilleur refroidissement, les temps de cycle sont réduits et la qualité du pliage est améliorée.
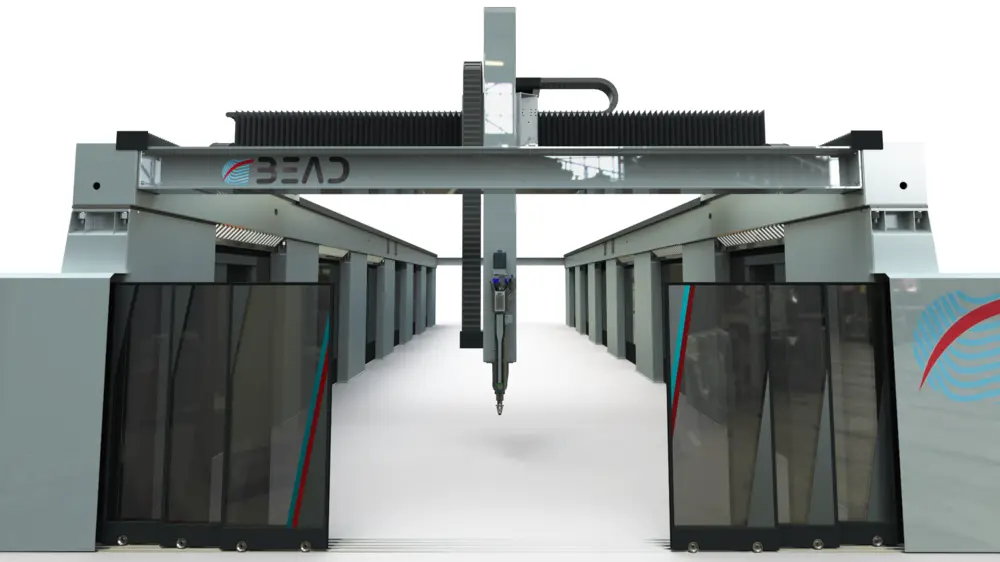
L'intérêt pour l'impression 3D des noyaux et des moules augmente également dans l'industrie de la fonderie, bien que cette technologie soit disponible depuis une vingtaine d'années. Des délais d'exécution courts, le maintien de la production d'outils en interne et la réduction des coûts tout en continuant à couler avec les matériaux approuvés commencent à peser de plus en plus lourd dans la décision d'investir dans une imprimante à sable pour la fabrication de moules et de noyaux. L'une des dernières annonces dans ce domaine concerne la construction de la plus grande imprimante 3D au monde pour un parc éolien offshore. Dans une quinzaine de jours, ces moules doivent être prêts à couler de grandes pièces métalliques d'un diamètre de 9,5 mètres et d'un poids de plus de 60 tonnes. Le délai de réalisation de l'outillage est actuellement d'environ 10 semaines. En outre, les initiateurs comptent sur une meilleure qualité de surface et une meilleure précision dimensionnelle.
