Steeds meer keuze als het om 3D-metaalprinten gaat
Additive manufacturing wordt volwassen
'One size fits all' geldt inmiddels niet meer voor 3D-metaalprinten. Waar vijf jaar geleden laser poederbedprinten (LPBF) dé technologie was voor metaalprinten, kan men tegenwoordig kiezen uit meerdere alternatieven. Toch verwachten experts dat LPBF de komende jaren de dominante metaalprinttechnologie blijft. Maar is dat nu ook de techniek voor kmo’s? En wordt het tijd dat ook zij zich serieus gaan beraden over de implementatie van Additive Manufacturing (AM) als productietechnologie?
(Moeilijke) huidige stand van zaken
Als zelfs een AM-pionier en voorvechter van de technologie (Siemens) erkent dat de markt minder snel groeit dan verwacht, moet er toch iets aan de hand zijn. Financieel-economisch is dat ook zo. Dit jaar heeft de 3D-printmarkt het moeilijk. Vooral fabrikanten van metaalprinters, die de afgelopen tien jaar snel zijn gegroeid, zijn in problemen gekomen door de achterblijvende vraag en de hoge kosten, gebaseerd op te hoge groeiprognoses. Ze zijn opgekocht door anderen (zoals Desktop Metal door Nano-Dimension en SLM Solutions door Nikon); of ze zijn hard op zoek naar een partner (zoals Velo3D) of ze gooien de handdoek in de ring (zoals Xerox dat stopte en de technologie verkocht aan ADDiTEC).
Chinese fabrikanten groeien wel
Daarnaast hebben ze in toenemende mate 'last' van Chinese fabrikanten. Die hebben de markt voor desktop-3D-printers al gekaapt (met name Bambu Lab en Creality) en inmiddels roert ook een aantal Chinese fabrikanten van hoogwaardige 3D-metaalprinters zich nadrukkelijk op de Europese markt. Ze openen hier verkoop- en servicekantoren (zoals Farsoon Technologies en Eplus3D) en halen daarmee criticasters de wind uit de zeilen, die eerder nochtans kanttekeningen maakten bij hun servicemodel.
De Chinese fabrikanten kunnen expanderen doordat ze een grote thuismarkt hebben. Wereldwijd wordt één op de drie LPBF-AM-machines verkocht in China! Waar we in Europa nog altijd nichetoepassingen zoeken voor metaalprinten, gaat het in China inmiddels om massaproductie. Het scharnier van miljoenen klaptelefoons – in Azië populairder dan hier – wordt 3D-geprint, omdat het design anders niet maakbaar is.
De meest recente verkoopcijfers over de wereldwijde 3D-printmarkt laten zien dat in het hoogste marktsegment de verkopen dit jaar wereldwijd met 25% achterblijven bij vorig jaar. Vier kwartalen op rij al dalen de verkopen. De 3D-metaalprinters doen het in deze krimpende markt nog het minst slecht met een daling van slechts 7% van het aantal uitgeleverde machines. Deze cijfers komen nadat de markt al enkele jaren stagneert, met wereldwijd ongeveer 2.100 verkochte machines per jaar (waarvan zo’n 75% LPBF is).
Wereldwijd wordt één op de drie 3D-metaalprinters verkocht in China
Laser Powderbed Fusion (LPBF)
De meeste marktonderzoekers verwachten dat die tendens de komende jaren zo blijft. De klassieke metaalprinttechnologie verliest weliswaar marktaandeel aan andere technieken, in absolute aantallen blijft dit veruit de meest gebruikte technologie. Deze technologie is in principe volwassen en breed inzetbaar. Het nadeel blijft de snelheid: laag voor laag wordt het product opgebouwd. Printjobs die dagen tot meer dan een week duren, zijn geen uitzondering. Toch hoeft dit geen belemmering te zijn als men de meerwaarde van de technologie benut én de kwaliteit bewaakt.
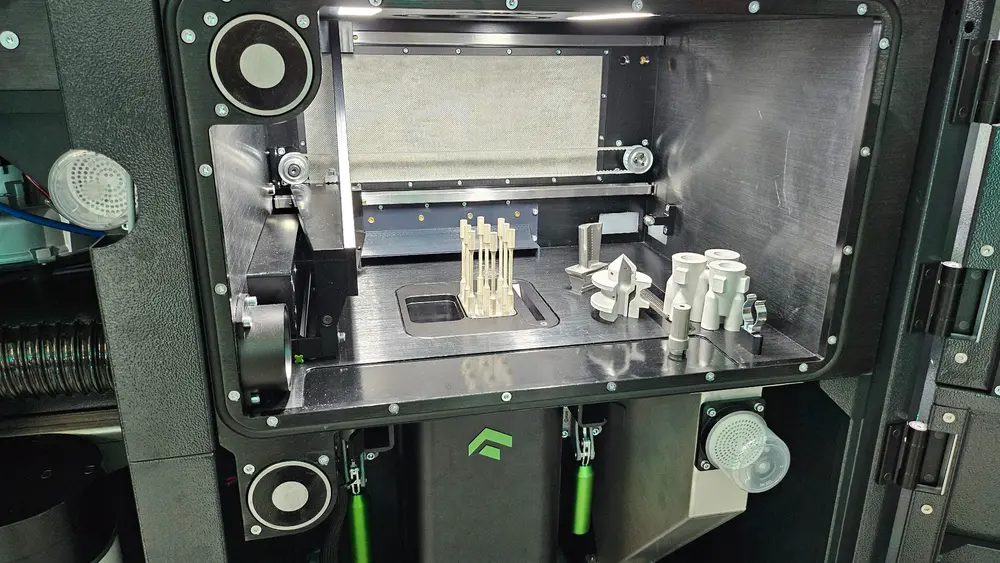
1. Multilasersystemen
Een van de manieren waarop fabrikanten de snelheid en het werkbereid proberen te verhogen, is de integratie van meer lasers in één machine. Multilasersystemen met drie of vier lasers (van 0,5; 0,7 of 1 kW) zijn min of meer standaard. In China heeft één van de fabrikanten inmiddels een machine gebouwd met 64 lasers.
Sommige Europese fabrikanten wijzen op twee nadelen van méér lasers: de investeringskosten nemen hierdoor sterk toe én men brengt heel veel warmte in het werkstuk met alle risico’s van dien. Fabrikanten die kritisch hierop zijn, zoeken naar andere oplossingen, bijvoorbeeld door het recoaten (= aanbrengen van de verse laag poeder) meteen te starten nadat de lasers een deel van de bouwkamers hebben belicht.
2. Beam shaping
Een heel recente ontwikkeling die het Fraunhofer ILT in Aken heeft opgepakt, is de toepassing van beam shaping in de LPBF-printers. Deze techniek is recent ontwikkeld voor lasersnijmachines. Tijdens het snijden wordt de vorm van de laserstraal aangepast, waardoor men de verdeling van energie beter kan sturen.
Bij LPBF-AM-machines zou men hierdoor sterkere laserbronnen (> 1 kW) kunnen gebruiken. Nu gebeurt dit nog niet, omdat de klassieke laserstraal dan te veel vermogen in het centrum van de lichtbundel bijeenbrengt, wat tot spetters (die het proces verstoren) en insluitingen (die de integriteit van de werkstukken aantasten) kan leiden.
De onderzoekers hebben goede hoop dat ze, door de vorm van de laserbundel te veranderen, de productiviteit fors omhoog kunnen brengen zonder dat er veel extra lasers nodig zijn.
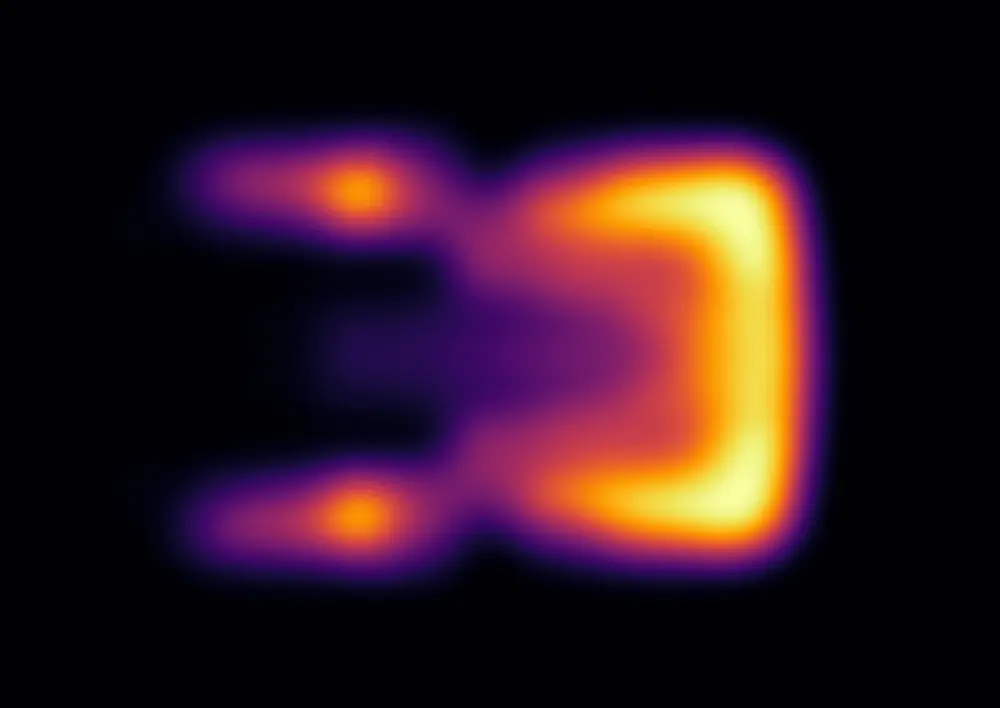
3. Bouwvolume
Bij de LPBF-3D-printers ziet men ook een toename van het bouwvolume. Waren enkele jaren terug machines met een bereik van 400 bij 400 mm gangbaar voor de industrie; tegenwoordig zijn er al meerdere fabrikanten die machines aanbieden met bouwvolumes van meer dan een meter.
4. Blauwe laser
Een vierde ontwikkeling bij LPBF-systemen (en ook Direct Energy Deposition (DED)-systemen, zie verderop) is het gebruik van blauw laserlicht. Met name gebeurt dit bij het printen met koper. Deze blauwe laser heeft een golflengte van 400 nm, verbruikt minder energie en heeft een hogere materiaaldepositie doordat het koper het blauwe laserlicht beter absorbeert. De absorptiegraad bedraagt bij koper 44% vergeleken met 2% bij een klassieke near infrarood. Omdat er meer licht wordt geabsorbeerd, zou men met hogere vermogens kunnen 3D-printen. De belemmering is momenteel de hogere kostprijs van de blauwe laser.
5. Elektronenstraal
Een variant van LPBF is de techniek die een elektronenstraal als energiebron gebruikt. Het aflopen van patenten heeft voor een aantal nieuwe spelers in dit segment gezorgd. Omdat de elektronenbundel het metaalpoeder smelt in een vacuümkamer, krijgt men bij materialen zoals titanium betere mechanische eigenschappen. Ook kan men makkelijker producten stapelen. Vanwege het ruwere oppervlak van deze prints, is deze technologie vooral in de medische sector gevraagd.
Direct Energy Deposition (DED)
Een alternatief voor LPBF is Direct Energy Deposition (DED), eigenlijk een verzamelnaam voor een aantal technieken waarmee materiaal wordt opgelast.
- Dat gebeurt bijvoorbeeld met poeder, en een laserstraal als energiebron (= het vroegere lasercladden zoals DMG MORI dit in hybridemachines of TRUMPF in LMD-systemen toepast).
- Een alternatief is met een elektronenstraal draad smelten in een vacuümkamer (de technologie van Sciaky);
- Of de draad wordt gesmolten met plasma in een inert omgeving met argon (Norsk Titanium), wat hogere sterktes oplevert.
- Een recentere variant is dat lasdraad gesmolten wordt met een lichtboogproces (= Wire Arc Additive Manufacturing (WAAM), toegepast door bijvoorbeeld GEFERTEC, CHIRON en Fronius).
- De lasdraad kan ook gesmolten worden met een laserstraal (het systeem van Meltio).
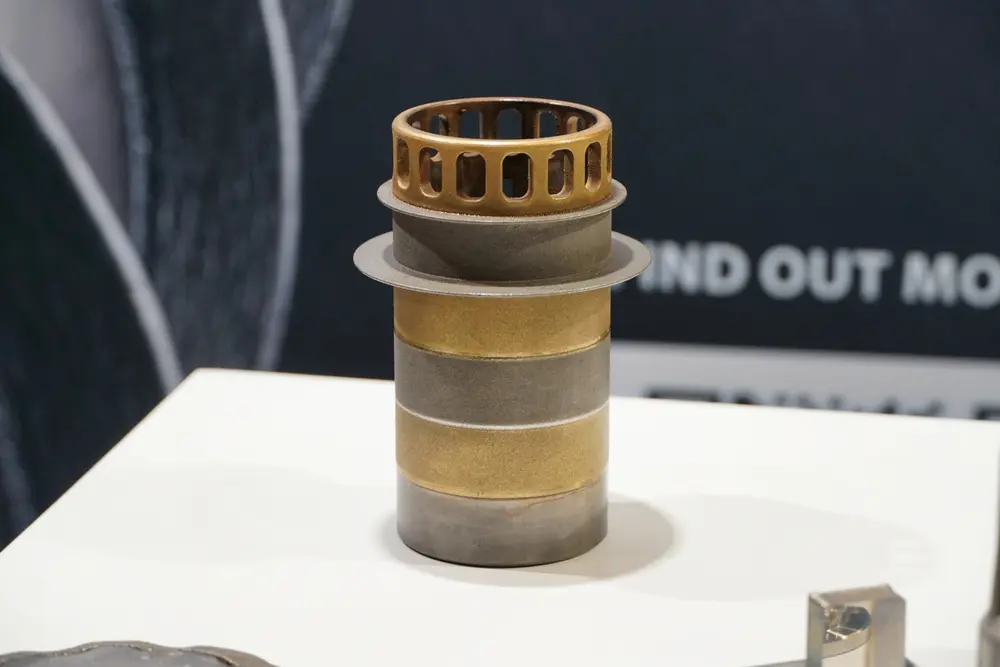
Molten Metal Deposition (MMD)
Eerder een buitenbeetje als het om 3D-metaalprinten met draad gaat, is het Belgische ValCUN. De start-up uit Gent, die in 2025 de verkoop van de Minerva-machines start, extrudeert 1,2 mm dunne aluminium lasdraad en brengt deze onder druk in een vloeibare fase en bouwt dan druppel voor druppel het werkstuk op (Molten Metal Deposition). Er kan op die manier een overhang tot 75 graden worden geprint, zonder support.
Het proces lijkt op filament printen, waarbij het plastic door de hoge druk in de extruder visceus wordt. De Belgische technologie is enigszins vergelijkbaar met die van Vader Systems, dat door Xerox werd gekocht en de technologie uiteindelijk heeft overgelaten aan ADDiTEC.
ValCUN 3D-print tot nog toe met aluminium, omdat dit een materiaal is dat veel kmo's gebruiken en er weinig AM-oplossingen voor zijn.
Wire Arc Additive Manufacturing (WAAM)
Voor kmo's zijn in het bijzonder de systemen die met draad werken een opportuniteit. Draad is als feedstock vele malen goedkoper dan poeder en is in veel meer legeringen verkrijgbaar. Vaak zijn dit al gecertificeerde materialen. WAAM (en ook draadsmelten met de laser) laat zich daarnaast goed integreren op een robot.
Zo kan men relatief goedkoop een systeem bouwen voor het 3D-printen van grote metalen componenten. In België heeft onder andere Guaranteed dit in Zelzate gedaan, waar het grote, zware gereedschappen uit de staalindustrie en andere sectoren met 3D-metaalprinten herstelt.
Twee andere voordelen van het 3D-printen met draad zijn de lagere investeringskosten en de eenvoudige bediening. Dit geldt dan met name voor WAAM, maar ook de technologie van onder andere Meltio (lasdraad smelten met laserstraal); en die van ValCUN (Molten Metal Deposition). WAAM is gemakkelijk te bedienen omdat het in feite een lasproces is.
Fronius lanceert momenteel bijvoorbeeld een eigen AM-systeem, gebaseerd op de Cold Metal Transfer lastechnologie. Het Oostenrijkse concern levert al langere tijd lasbronnen voor AM aan andere partijen, waaronder het Nederlandse MX3D. Omdat lastechnologie wijd verspreid is in de metaalindustrie, zijn de meest cruciale parameters wel bekend. De crux zit meer in de juiste positionering van de lastoorts, waar Fronius een oplossing voor ontwikkeld heeft die compatibel is met de gangbare robotsystemen.
Deze WAAM-systemen zijn eenvoudiger te bedienen, omdat men in feite met een 3- of 5-assige CNC-machine te maken heeft (de systemen zonder robot). En het aantal parameters dat invloed heeft op de eindkwaliteit, is veel geringer dan bij LPBF. Bij dit laatste zijn er meer dan 150 parameters waar een operator mee kan spelen. Vaak gebruiken fabrikanten van dit soort machines een SINUMERIK-besturing, vergelijkbaar met die in CNC-machines.
Daarnaast zijn er al CAM-programma’s die WAAM hebben toegevoegd aan hun CAM-software voor CNC-freesmachines. In Nederland heeft Hogeschool Windesheim in hun factory NEXT, waar kmo's samen met de hogeschool technologie kunnen verkennen, een 3-assig bewerkingscentrum van Haas met geïntegreerde printkop van Meltio in gebruik genomen. Nadeel is dat deze, in tegenstelling tot wat we hierboven beschreven bij LPBF, apart geprogrammeerd moeten worden.
Een aandachtspunt bij WAAM is de nabewerking. Het is een vrij grove technologie; de stukken zullen daarom altijd gedeeltelijk gefreesd of gedraaid moeten worden, als het bijvoorbeeld nauwkeurige aansluitvlakken nodig heeft. De KU Leuven en Thomas More werken samen met partners in een Europees project aan een set parameters waarmee men het metaalprinten en de nabewerking zodanig op elkaar kan afstemmen, dat de twee processtappen vrijwel naadloos in elkaar kunnen overlopen.
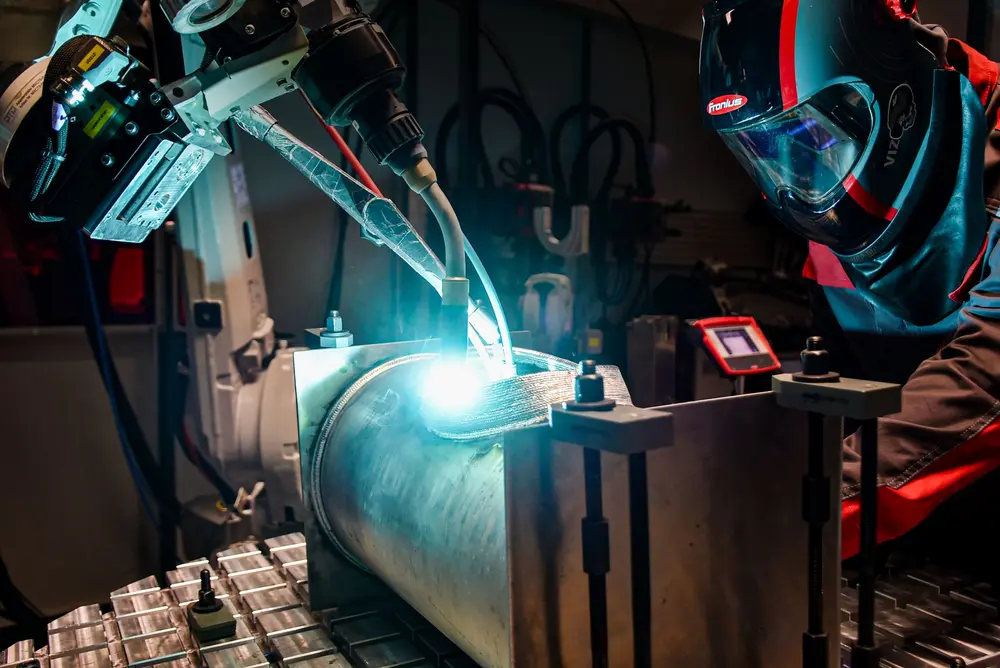
Coldspray
Een andere variant in de DED-technologie is coldspray. Hierbij wordt metaalpoeder in een gasstroom (met een snelheid hoger dan die van geluid) op het op te bouwen project gedeponeerd. Door de kinetische energie die vrijkomt, smelt het poeder.
Twee Australische fabrikanten lopen hiermee voorop (Titomic en SPEE3D). Ze hebben recent onder andere in de defensie-industrie succes geboekt, omdat het een heel robuuste AM-techniek is die momenteel zelfs in het veld wordt ingezet. De technologie kan eenvoudig geïntegreerd worden met een robot, zodat men veel bewegingsvrijheden krijgt.
Coldspray wordt in verschillende sectoren, waaronder die van olie en gas, onderzocht als een alternatief voor de productie van gesmede halffabricaten. Met name als het om titaniumonderdelen gaat, zijn de doorlooptijden lang (vaak vele maanden). Met deze coldspray-technologie kan men in enkele uren tijd tot 27 kilo titanium opbrengen. Vergeleken met frezen uit een gesmeed blik titanium is er een materiaalbesparing van 70%.

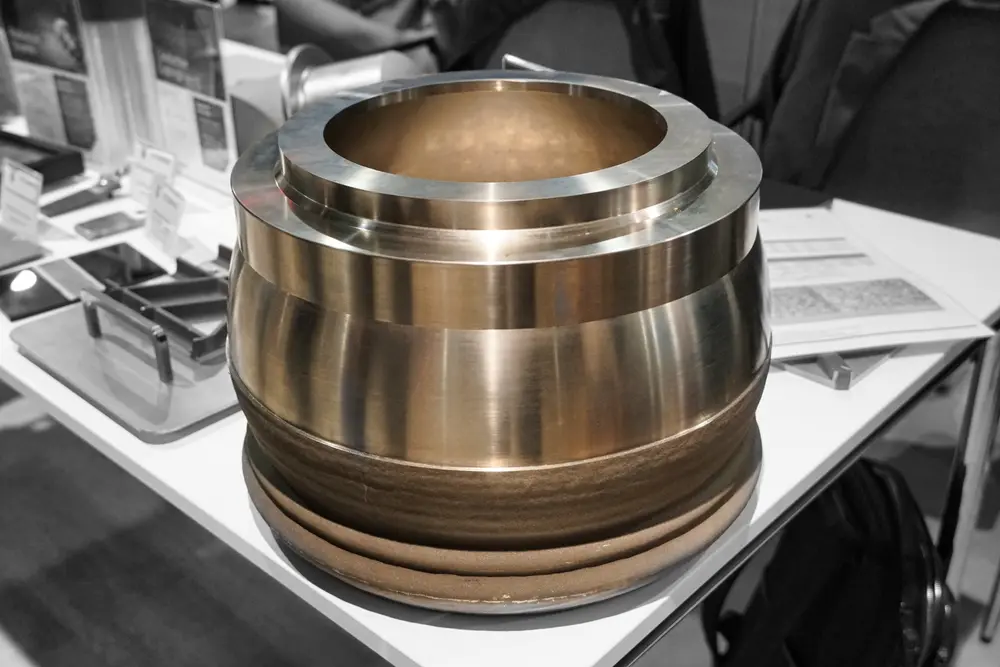
Binder Jetting
De derde interessante metaalprinttechnologie, naast LPBF en DED, is Binder Jetting (de technologie bij onder andere Desktop Metal, HP maar ook als nieuwkomer het Franse ADDIMETAL). In tegenstelling tot bij LPBF, wordt bij Binder Jetting geen warmte in het metaalpoeder gebracht. Als het poeder is uitgestreken, worden via tienduizenden nozzles minuscule druppels bindmiddel op het metaalpoeder gesproeid in de 2D-vorm van het eindproduct. Met relatieve geringe warmte reageert het bindmiddel door uit te harden. Omdat het alleen uithardt waar metaal in het product moet komen, blijft de rest van het poeder onaangetast en kan hergebruikt worden.
Laag voor laag wordt het onderdeel opgebouwd. In een tweede stap (wassen) wordt het grootste deel van dit bindmiddel verwijderd. Daarna volgt de sinterstap: in een klassieke sinteroven – vergelijkbaar met Metal Injection Molding (MIM) – wordt het poeder gesinterd en krijgt het werkstuk de definitieve maat en materiaaldichtheid. Deze laatste ligt doorgaans boven de 99%. Bij het sinteren krimpen de onderdelen. De fabrikanten kunnen deze krimp goed voorspellen en houden daar bij het printen rekening mee.
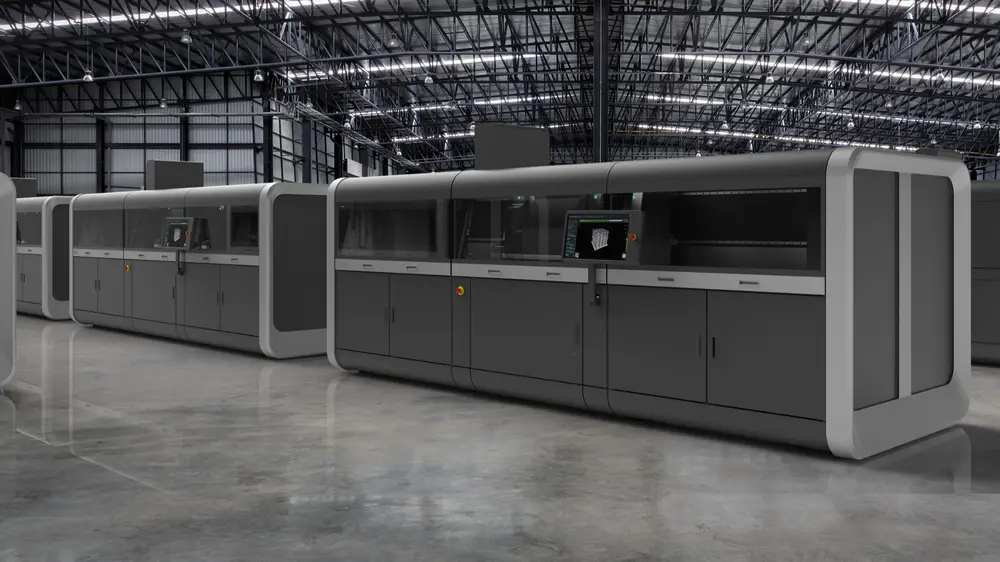
Eén van de voordelen van deze technologie is dat er geen support-structuur nodig is, noch ter ondersteuning van een overhang noch om warmte af te voeren, zoals wel nodig is bij LPBF. Wel kan voor het sinteren bij bepaalde geometrieën een support nodig zijn.
Een tweede voordeel van het ontbreken van een directe warmte-inbreng is dat je in de buildbox meerdere producten dichtbij elkaar kunt positioneren. Dit verlaagt de kostprijs per onderdeel.
Tot slot geldt zeker als voordeel dat er geen spanningen in het materiaal ontstaan, zoals wel het geval is bij LPBF.
Twee nadelen vergeleken met de andere AM-technieken: de afmetingen zijn beperkt en er volgen altijd nog twee processtappen na het 3D-printen. De begrenzingen aan de afmetingen hebben alles te maken met het feit dat er een groen product uit de 3D-printer komt. Zolang het niet gesinterd is, is het breekbaar. Het wassen en vooral het sinteren zijn twee processtappen die tijd vergen, reken in totaliteit zeker op twee dagen.
Fused Deposition Modeling (FDM)
Er zijn nog meer 3D-printtechnieken waarmee men metalen componenten kan produceren. Bijvoorbeeld Fused Deposition Modeling (FDM), de bekende 3D-printers die filament gebruiken (zoals bij onder andere Ultimaker, maar ook het Belgische FuseLab). In dit geval bestaat het filament uit een mix van metaalpoeders (vergelijkbaar met die van Binder Jetting) en een polymeer dat thermisch of chemisch verwijderd wordt.
Als laatste stap moeten deze onderdelen ook gesinterd worden. Dit is de achilleshiel van de oplossing: industriële sinterovens zijn kostbaar, het sinterproces vergt ervaring en kennis. Wat als een laagdrempelige en goedkope manier om metalen onderwerpen te printen gepresenteerd wordt, blijkt uiteindelijk toch kostbaar te zijn. Of tijdrovend als men extern gaat sinteren.
Bovendien blijft de dichtheid (98,7%) achter bij de andere technieken, evenals de hardheid na een extra hardingsstap. De oppervlakteruwheid is daarnaast slechter dan bij LPBF en Binder Jetting. Deze laatste levert de beste resultaten (Ra-waarde van 5,2 µm tegen Ra 7,5 voor LPBF en 11,9 bij FDM.
Fused Deposition Modeling is wel een technologie waarmee men ervaring met additive manufacturing kan opdoen; of die zinvol is als men alleen enkelstuks of hele kleine series print.
Waarom zou ik gaan 3D-printen?
Waarom zouden kmo's die zich nu bezighouden met CNC-frezen zo’n WAAM- of laser-AM-systeem overwegen? De complexiteit van de producten die men met deze technologie kan maken is niet het belangrijkste argument. Veel belangrijker lijkt het aspect duurzaamheid en grondstoffenbesparing te worden.
ASML heeft onlangs op een bijeenkomst bij het Mikrocentrum nog eens uit de doeken gedaan waarom het meer onderdelen wil laten 3D-printen (in de nieuwste machines zijn al zo’n 300 geprinte onderdelen verwerkt). Naast doorlooptijdverkorting en een hogere yield, is vooral het minder verspillen van materiaal in toenemende mate een reden. Frames voor de machines van ASML worden nu dikwijls uit gesmeed titanium gefreesd. Dat betekent dat tot 90% van het materiaal als spaan in de spanenbak belandt. Bij 3D-metaalprinten met DED is dat aanzienlijk minder. De materiaalverspilling blijft hier beperkt tot zo’n 10% afhankelijk van het product en de technologie. Dit zal komende jaren een steeds belangrijkere reden worden om additive manufacturing in te zetten. Sommige Tier 1-leveranciers van de Nederlandse hightech machinebouwer hebben al testen gedaan, zowel met de technologie van Meltio als die van Sciaky.
Daarnaast blijven de typische voordelen zoals het integreren van meerdere onderdelen in één (waardoor minder assemblage in het eindproduct nodig is) en het vermijden van voorraden (on-demand productie) belangrijke redenen waarom bedrijven additive manufacturing overwegen.
De meeste onderzoekers verwachten dan ook dat na de moeilijke jaren de AM-markt de komende jaren weer terug op het groeipad komt. Een jaarlijkse groei van de totale markt voor 3D-metaalprinten met dik 20% per jaar is denkbaar, aldus een van de conservatieve consultancybureaus. Lucht- en ruimtevaart en ook defensie, net als de medische industrie, zijn de kartrekkers. Tegen 2028 verwacht het Duitse AMPower een totale markt voor 3D-metaalprinten van ruim € 10 miljard. De bedrijven die met printers onderdelen produceren, zullen daarvan het grootste deel voor hun rekening nemen.