gebrek aan geautomatiseerd nabewerken remt groei 3D-metaalprinten
Post-processing AM kostbare zaak
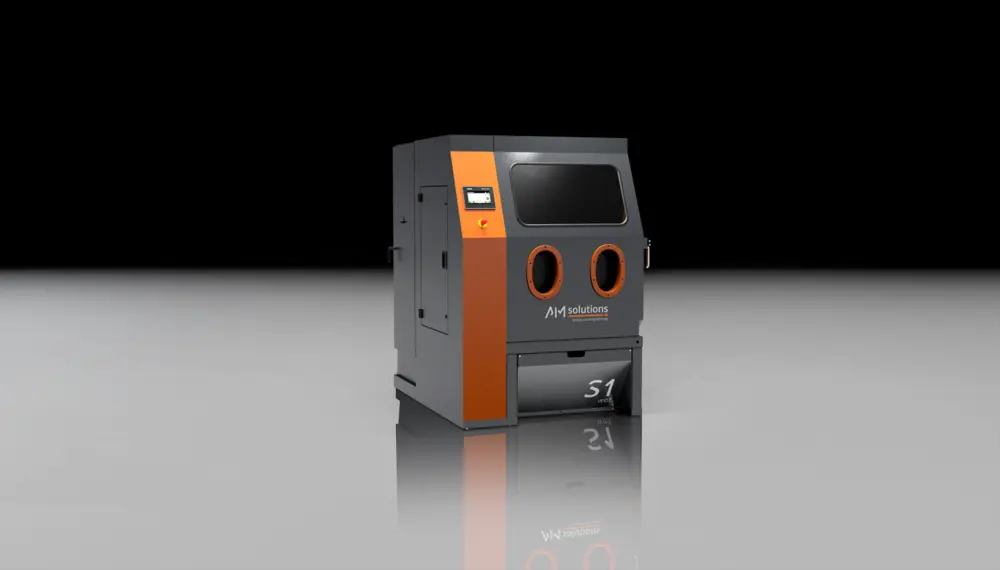
Post-processing van additief vervaardigde werkstukken is lange tijd een ondergeschoven kindje geweest in het hele AM-proces. Pas nu bedrijven serieus beginnen te denken over serieproductie met metaalprinten, komt er aandacht voor. Want het nabewerken kan een behoorlijke drempel opwerpen als men additive manufacturing wil gaan inzetten om grotere aantallen eindonderdelen te produceren.
De Amerikaanse AM-goeroe Terry Wohlers, die al meer dan een kwart eeuw jaarlijks in kaart brengt hoe de AM-markt zich wereldwijd ontwikkelt, kwam onlangs met een interessante studie naar buiten. Dit keer zowel bij 3D-printservicebedrijven alsook bij bedrijven die seriematig onderdelen voor eigen productie 3D-printen, onderzocht hij welke invloed post-processing op de kosten heeft. Gecombineerd voor zowel polymeren als metaal, komt Wohlers tot de slotsom dat 27% van de kosten om een onderdeel te 3D-printen wordt veroorzaakt door post-processing. Dat ligt op vrijwel hetzelfde niveau als in een ander recent onderzoek werd gevonden.
In het Additive Post-Printing Survey Trends Report 2021 constateren de onderzoekers dat 30% van de deelnemers aan dit onderzoek meer dan 26% van hun hele AM-budget besteedt aan het nabewerken. Een jaar eerder was dit nog 23%. De grootste pijnpunten zijn de lange doorlooptijd bij postprocessing, matige consistentie van de resultaten, beperkte productiviteit en het afval dat overblijft. Ook benoemt 26% de noodzaak om geschoolde medewerkers in te moeten zetten als een knelpunt.
Rem op opschalen
Deze twee onderzoeken staan niet op zichzelf als het om de ware impact van nabewerking op additive manufacturing gaat. Ook vanuit grote OEM’ers in de luchtvaartindustrie wordt post-processing als een achilleshiel aangeduid. Zowel bij Boeing als bij Airbus zegt men dat de momenteel beschikbare technologie voor het nabewerken van metalen AM-onderdelen een serieuze rem zet op de inzet van AM voor de productie van grotere volumes. Het opschalen zou betekenen dat ook alle vervolgprocessen opgeschaald moeten worden. Dat vergt bijkomende investeringen en vooral veel extra handjes. Dat remt de groei, klinkt het bij Boeing. Een van de AM-experts van Airbus merkte recent in een conferentie op dat 79% van de totale AM-kosten in iets anders zit dan het feitelijke 3D-printen. Post-processing heeft hier een flink aandeel in.
Post-processing van additief vervaardigde werkstukken is lange tijd een ondergeschoven kindje geweest in het hele AM-proces
Designinvloed
Design heeft veel invloed op de kosten. Het eerste waar men bij nabewerken van AM-onderdelen aan denkt, is het verwijderen van de supportstructuren die nodig zijn bij laser poederbed metaalprinters (LPBF). Omdat het weghalen hiervan geld kost, is het belangrijk zo min mogelijk supportstructuren te printen. Design van het onderdeel maar ook de positionering ervan op de bouwplaat van de machine hebben invloed op de kosten van het nabewerken. Dat geldt overigens voor meer dan alleen support verwijderen. Als men bij LPBF-machines holle structuren print, blijft er los poeder achter. Bij het ontwerpen moet men daar rekening mee houden en zorgen dat dit verwijderd kan worden.
Zo gelden er meer ontwerpregels voor additive manufacturing die bedoeld zijn om zo efficiënt mogelijk te kunnen nabewerken. De eerste stap in het proces na het 3D printen is het verwijderen van poeder. Hiervoor zijn inmiddels machines op de markt die dit quasi geautomatiseerd doen. Hiervoor wordt de bouwplaat met daarop de onderdelen in een cabine rondgedraaid, eventueel aangevuld met trillingen om zo het poeder te verwijderen. De allernieuwste systemen laten zich beter programmeren. De bewegingen die nodig zijn om het poeder te verwijderen, zijn namelijk mede afhankelijk van de vorm en de complexiteit van het AM-werkstuk. Voor het verwijderen van titanium of aluminium poeder moet de ruimte gevuld worden met een beschermgas. Daarmee voldoet het systeem aan de ATEX-normen. Om het poeder ook automatisch uit interne kanalen te verwijderen, zetten sommige machinefabrikanten ultrasoon frequenties in.
ONDERDELEN VAN BOUWPLAAT VERWIJDEREN
Uiteindelijk zullen altijd de onderdelen van de bouwplaat moeten worden gehaald, althans bij een laser poederbed AM-proces. Hiervoor zijn twee opties beschikbaar: ofwel met een draadvonkmachine of met een nauwkeurige zaag. De meeste bedrijven kiezen voor een draadvonkmachine, omdat daarmee het minste materiaal van de bouwplaat verloren gaat. Deze wordt weer vlakgefreesd en is dan weer klaar voor een volgende buildjob.
Oppervlak verfijnen
OEM’ers die seriematig metalen onderdelen additief willen produceren, zoeken naar automatisering als het om verwijderen van supportmateriaal gaat. Meerdere fabrikanten hebben de afgelopen tijd machines ontwikkeld om met (elektro)chemische processen de supportstructuren automatisch te verwijderen. Hirtisation is een voorbeeld hiervan. Het gaat hierbij om de combinatie van een elektrochemisch proces, hydrodynamische stroming en chemisch verwijderen van ruwe delen aan het oppervlak waarbij ondersteuning komt van kleine deeltjes.
In drie stappen wordt de oppervlakteruwheid 100 µm teruggebracht tot uiteindelijk 0,5 µm, polijstkwaliteit. Dat laatste is de derde stap, met de eerste twee komt men al tot Ra 2 µm. Met elektrochemisch polijsten kan men ook inwendige oppervlakken gladder maken, bij dit proces de oppervlakteruwheid tot 80% verminderen. Dit is dan ook een technologie die vaker wordt ingezet voor het gladder maken van oppervlakken, met name als er moeilijk bereikbare plekken aan een werkstuk zijn. Het meerstappenproces is volledig geautomatiseerd, zonder dat mechanische bewerking nodig is.
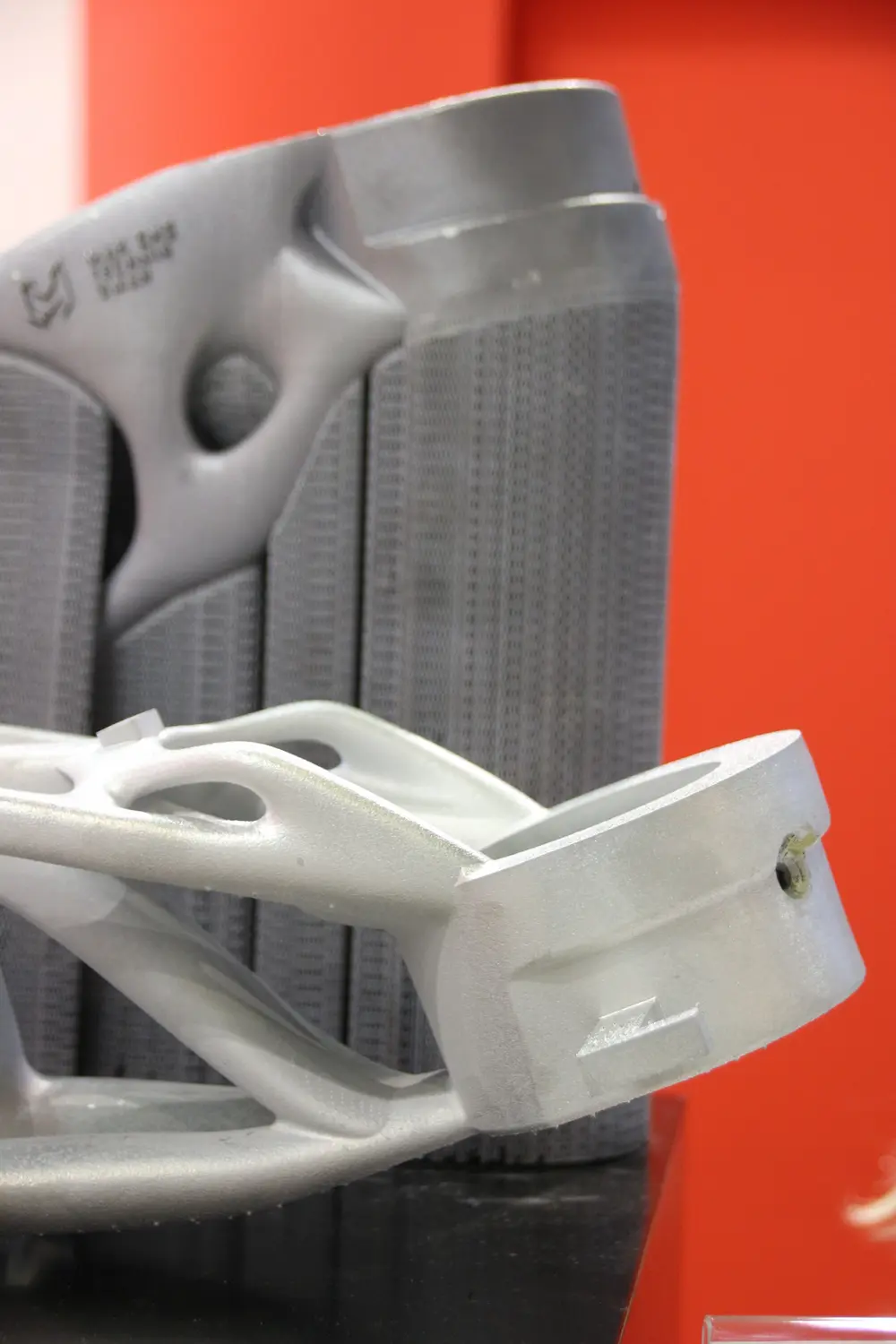
trommelen
Toepassingen voor deze technologie zijn bijvoorbeeld manifoldachtige producten, met interne koelkanalen. Of gereedschappen waar onder het oppervlak koelkanalen lopen die additief zijn vervaardigd. Soms combineert men chemisch polijsten (zuren) met trommelen, een in de metaalindustrie bekende technologie voor het verbeteren van oppervlakteruwheid. De chemische behandeling wordt gestuurd vanuit parameters, om te voorkomen dat er op plaatsen te veel materiaal wordt weggehaald.
Voor sommige toepassingen is de chemische nabewerking geen oplossing omdat dit soort chemicaliën niet zijn toegestaan. In dat geval zijn stralen en trommelen de meest aangewezen technieken om het ruwe oppervlak van additief geproduceerde stukken te verbeteren. Dat geldt eigenlijk ook voor toepassingen waarvoor het oppervlak geen polijstkwaliteit hoeft te zijn. Een recente ontwikkeling is het toevoegen van water aan het straalmiddel, wat een positief effect heeft op het eindresultaat. Een bijkomend voordeel is dat bij dunwandige producten het water een beschermende laag vormt waardoor de kans op veranderingen van vorm- en maatnauwkeurigheid wordt verminderd.
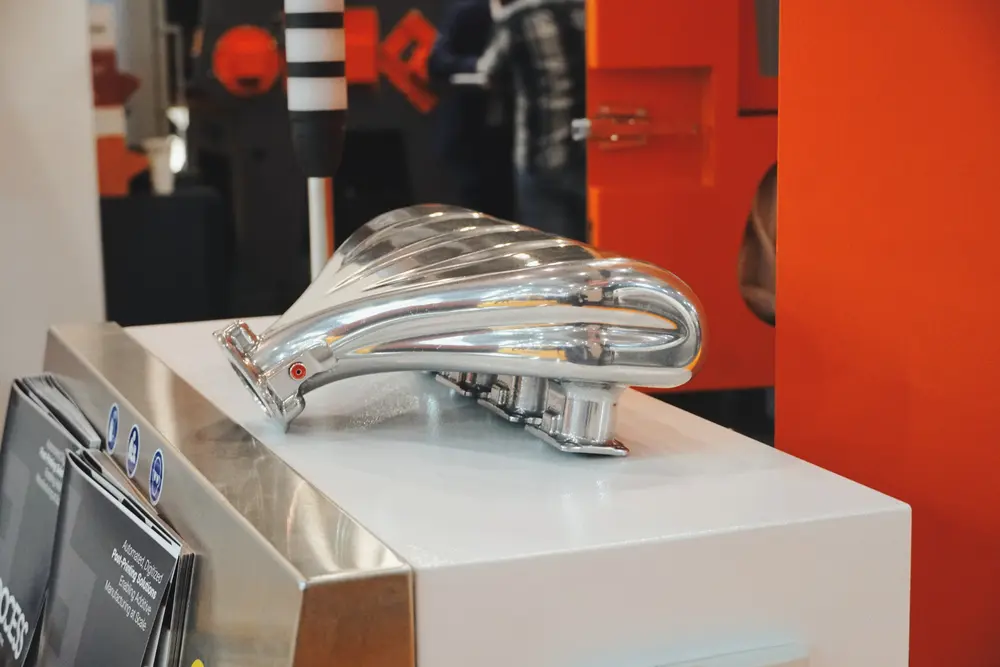
Laserbewerken
Een ontwikkeling die nog vrijwel aan het begin staat, maar wel potentieel biedt, is het laserpolijsten van AM-werkstukken. Op een aantal plekken in de wereld is hier onderzoek naar gedaan, waaronder in Nederland. Bij de Noorderburen is dit gedaan met een gepulste fiberlaser met een golflengte van 1.064 nm en een vermogen van 60 W. De laserstraal beweegt met hoge snelheden (tussen 1.000 en 4.000 mm per seconde) over het oppervlak eerst in de lengterichting en dan nog een keer kruislings. Hiermee worden de – alleen via een elektronenmicroscoop zichtbare - toppen opnieuw gesmolten en daarmee vult men de ‘dalen’ op. Het eindresultaat is dat in zeer korte tijd de ruwheid wordt teruggebracht van Ra 12 µm na het 3D-printen tot Ra 2 µm. De hardheid blijft vrijwel gelijk. Net als de maatvoering die slechts enkele honderden millimeters verandert (bij 316L of gereedschapstaal).
Het laserpolijsten is veel sneller dan mechanisch polijsten en laat zich gemakkelijker uitvoeren omdat er geen belastingen op het werkstuk komen. Chinese onderzoekers presenteerden vorig jaar op een conferentie over laserpolijsten in Aken een iets andere aanpak met andere resultaten. Zij hebben Inconel 718 gepolijst met een nanoseconde fiberlaer (90 W) en slagen er daarmee in om tot een Ra-waarde van 0,1 µm te komen en een Rz-waarde van 0,6 µm. Bij hun strategie verandert de hardheid wel, waar ze ook bewust naar op zoek zijn gegaan. De slijtageweerstand van Inconel verbetert met 90% door de onderdelen te laserpolijsten.
Ook de KU Leuven heeft dit onderwerp opgepakt maar zet de laser al tijdens het 3D-metaalprinten in. Zodra een laag is geprint, komt de tweede laser (een gepulste nanoseconde laser) die met een schokgolf restpoeder aan de randen of op het oppervlak van het werkstuk wegblaast. Daarna wordt de laag opnieuw door de eerste laser belicht en hersmelt de bovenste laag. Daarmee creëert men hetzelfde effect als in het Nederlandse project, het metaal vloeit naar de lagere delen. Dat zorgt voor een gladder oppervlak, precies wat in veel toepassingen nodig is. Het onderzoek in Leuven toont aan dat de ruwheid tijdens het printen al 80% verbetert.
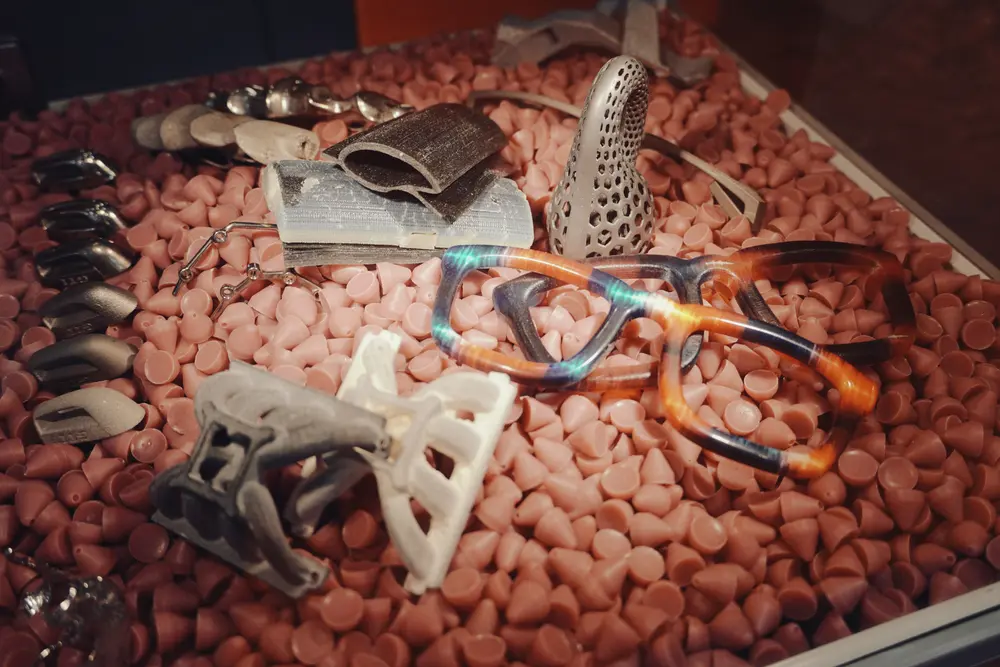
HIP en andere thermische nabehandelingen
Een van de post-processingstappen die wellicht de meeste tijd vergt is de thermische nabehandeling. Spanningsvrij gloeien om restspanningen die na het laser poederbed proces in het materiaal zitten, te verwijderen is een eenvoudige stap. Complexer wordt het al als men met een warmtebehandeling de materiaalstructuur wil verbeteren. Dat vergt al een betere beheersing van de opwarming en het afkoelen van de onderdelen in de oven, omdat het eindresultaat hierdoor bepaald wordt.
Hot Isostatic Pressing gaat een stap verder en is bedoeld om de porositeit te verkleinen. HIP’en, zoals de nabewerking vaak wordt genoemd, voorkomt dat microscheuren in de onderdelen ontstaan door insluitingen. Voor medische implantaten maar ook voor vliegtuigonderdelen is dit vaak een verplichte nabewerking, omdat hiermee de fatigue-eigenschappen met een factor tien tot honderd verbeteren. Bij Hot Isostatic Pressure wordt een onderdeel onder druk gezet en tegelijkertijd wordt de warmte sterk opgevoerd. Een nieuwe optie van het proces is het zeer snel afkoelen van de werkstukken waardoor porositeit tegelijkertijd met restspanningen worden verwijderd. Hiermee zou men in principe het printproces zelf kunnen versnellen doordat men niet voor de maximale dichtheid gaat. Deze ontstaan dan in de nabewerking tijdens de HIP-bewerking.