Nieuwe kijk op kwaliteitscontrole van 3D-metaalprinten
Werkstuk geprint, maar is het OK?
Additive manufacturing beweegt zich in de richting van serieproductie. Het gaat nog niet om grote aantallen, maar er komen steeds meer toepassingen waarvoor onderdelen of complete modules 3D-geprint worden. Dat verhoogt de druk op adequate QC-technieken. Want hoe toon je aan dat een additief gemaakt werkstuk voldoet aan alle eisen; niet alleen de maatnauwkeurigheid?
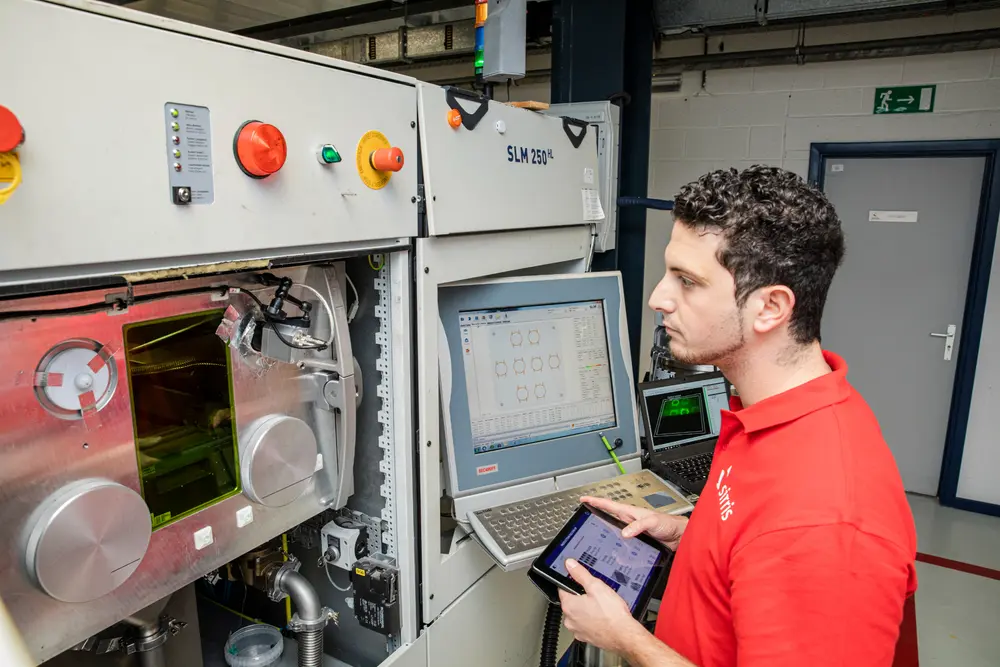
KWALITEITSCONTROLE
Meten is weten. Dat principe is in de maakindustrie al zo oud als de industrie zelf. In de verspanende industrie bestaat het meten vooral uit het controleren van de geometrische nauwkeurigheid, de oppervlakteruwheid en – in bijvoorbeeld de halfgeleiderindustrie – in toenemende mate de technische reinheid van het onderdelen. Bij sommige kritische onderdelen wordt er nog een NDT-test (‘Non Destructive Test’) gedaan, maar voor veel toepassingen volstaat het om met behulp van een certificaat de herkomst van het materiaal aan te tonen. In combinatie met de gevalideerde procesparameters en gereedschappen, volstaat dit om de kwaliteit aan te tonen.
Bij 3D-metaalprinten ligt dit anders. Typisch voor deze technologie is dat de mechanische eigenschappen van het werkstuk grotendeels pas ontstaan tijdens het AM-proces. Afwijkende parameters kunnen de oorzaak zijn van andere eigenschappen dan een soortgelijk product. Daarom zijn er andere oplossingen nodig dan de klassieke CMM (coördinatenmeetmachine).
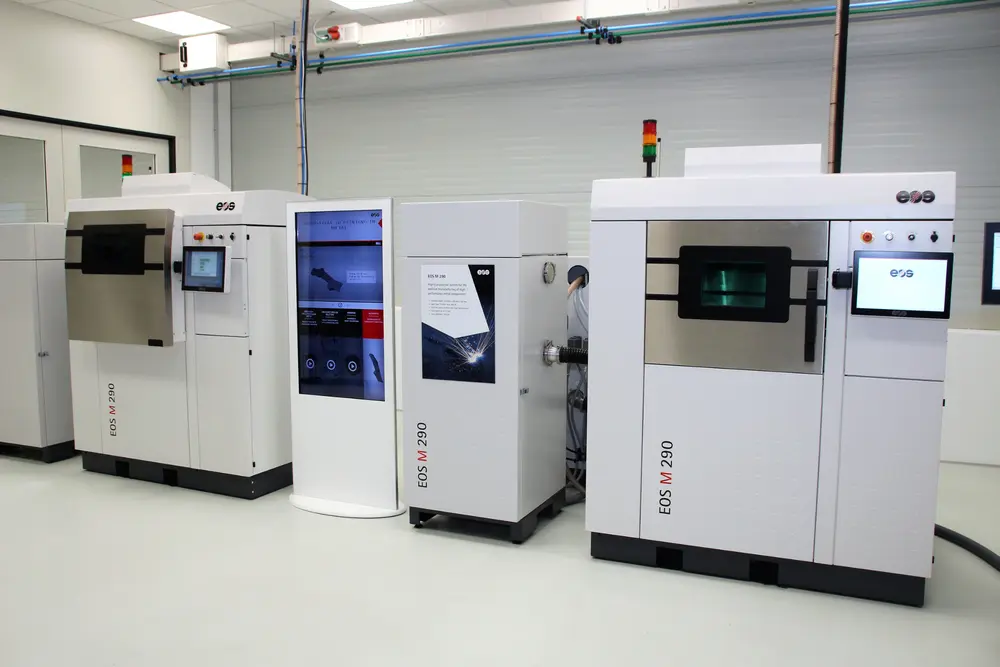
3D-scannen versus tactiel meten
Om de maatnauwkeurigheid van een 3D-geprint onderdeel te controleren, kan een klassieke CMM met meettaster worden gebruikt. Echt zinvol is dat echter niet, omdat de nauwkeurigheid waarmee de meetmachine werkt een factor 50 tot 100 hoger is dan de nauwkeurigheid van een gemiddelde 3D-metaalprinter, waarbij de focus in dit artikel ligt op het lasersmelten van metaalpoeders.
Een tweede tekortkoming van het tactiel meten, is dat 3D-geprinte producten vaak heel grillige vormen hebben, zeker wanneer de designs gemaakt zijn met ‘generative design software’ om zo min mogelijk materiaal te gebruiken. Dan zullen vlakken die men wil controleren misschien niet eens aangestipt kunnen worden met de taster.
Een oplossing hiervoor is optisch 3D-scannen. Met blauw- en witlichtscanners kan men snel en onbemand een complexe vorm in kaart brengen, in een voldoende hoge resolutie die goed aansluit bij de nauwkeurigheid van de 3D-metaalprinttechnologie. In de bijbehorende software worden de uitkomsten van zo’n 3D-scan over het oorspronkelijke CAD-model gelegd en worden afwijkingen direct zichtbaar. Deze methode kan ook gebruikt worden om verschillende printstrategieën met elkaar te vergelijken, bijvoorbeeld om de best mogelijke oppervlaktekwaliteit te bereiken.
In een onlangs afgesloten Europees onderzoeksproject zijn de projectpartners een stap verder gegaan: ze hebben de meetdata gebruikt om het nabewerken van de onderdelen te vergemakkelijken. Post processing is namelijk een van de struikelblokken, omdat het tijdrovend is; met name de werkvoorbereiding. Als het werkstuk 3D-gescand wordt, zit het al in de klem zodat de oriëntatie bekend is en de klem mét werkstuk op een CNC-machine geplaatst kan worden.
Additive manufacturing beweegt zich in de richting van serieproductie. Het gaat nog niet om grote aantallen, maar er komen steeds meer toepassingen waarvoor onderdelen of complete modules 3D-geprint worden
Algoritme
In het project is een algoritme ontwikkeld dat gevoed wordt met de uitkomsten van de 3D-scan. De software bepaalt eerst of het werkstuk dat van de 3D-metaalprinter komt wel voldoende overmaat heeft om na te bewerken. Het kan immers tijdens het printproces zodanig vervormd zijn dat op bepaalde punten de maatnauwkeurigheid niet meer gehaald kan worden. In dat geval heeft het geen zin om nog een kostbare post-proces stap te maken. Dat kan men zien als een eerste stap om de geometrische nauwkeurigheid te meten.
Vervolgens berekent het algoritme aan de hand van de scandata waar nog materiaal moet worden weggenomen en hoeveel dit is. Het is namelijk inherent aan het lasersmeltproces dat er verschillen kunnen optreden. Het algoritme vergelijkt de scandata met het originele CAD-model en past de bestaande NC-file aan, zodat de klem met het werkstuk direct op de CNC-freesmachine geplaatst kan worden om de laatste stap van de bewerking uit te voeren.
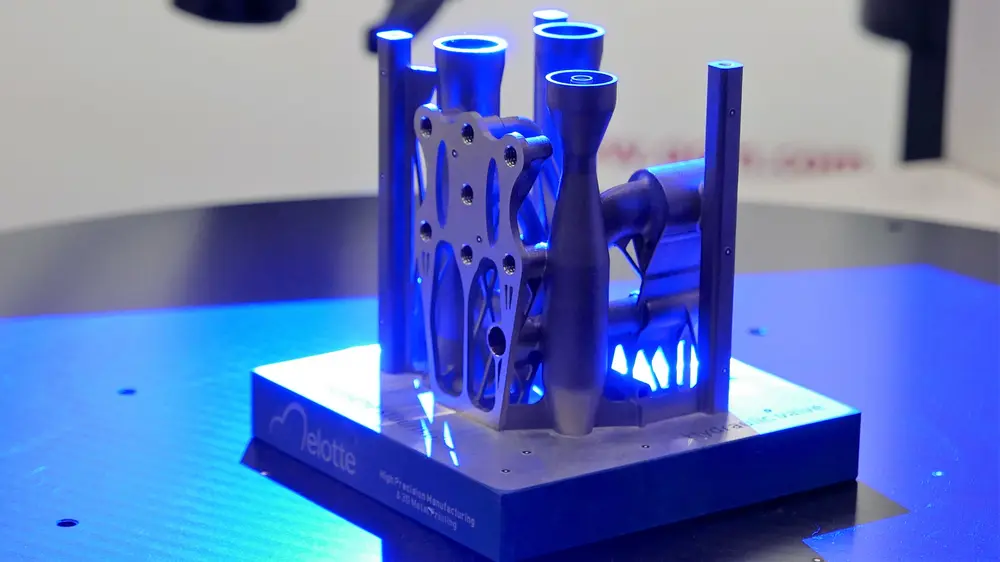
Software en sensortechnologie
Met 3D-scannen krijgt men zekerheid over de maatvoering van het werkstuk. Voor veel toepassingen zal men ook zeker willen zijn dat er tijdens het 3D-printen geen poriën of insluitingen in het werkstuk zijn ontstaan, die later tot microscheuren kunnen leiden. Dit is een zekerheid die de fabrikanten van 3D-metaalprinters vooral willen krijgen door in het proces data te verzamelen.
Hier tekent zich een fundamentele verschuiving van kwaliteitscontrole af ten opzichte van de klassieke mechanische bewerking. Zoals gezegd, worden klassiek de materiaaleigenschappen vooral aangetoond door te verwijzen naar gestandaardiseerde normen waaraan het ingekochte materiaal voldoet, met voor de heel kritische toepassingen het herkomstcertificaat als extra zekerheid. Omdat de materiaaleigenschappen bij additive manufacturing mede tijdens het proces ontstaan, vervalt deze mogelijkheid, hoewel deskundigen er op wijzen dat controle van de aangeleverde poeders de eerste stap in de kwaliteitscontrole hoort te zijn.
De kwaliteitscontrole van AM-stukken zal in toenemende mate in-situ gebeuren, laag voor laag. Het idee is dat – veelal met simulatiesoftware – een buildjob wordt geoptimaliseerd en dat het eerste stuk gecontroleerd wordt. Is dat goed en kan men daarna aantonen dat de volgende producten met dezelfde instellingen zijn geprint en sensoren en snelle camera’s geen afwijkingen constateren, dan mag men aannemen dat deze werkstukken dezelfde kwaliteit hebben als het eerste. Dit wordt ook wel ‘digitale X-ray’ genoemd, omdat men aan de hand van de parameters van elke laag een röntgenbeeld van het totale werkstuk opbouwt.
De kwaliteitscontrole van AM-stukken zal in toenemende mate in-situ gebeuren, laag voor laag
Twee sleutelelementen in de in-situ procescontrole zijn de goede verdeling van het poeder over het hele bed en de hoeveelheid energie die wordt ingebracht. De gelijkmatige verdeling van het poeder kan men controleren door van elke laag een beeld te maken dat vervolgens met onder andere Machine Learning en kunstmatige intelligentie geanalyseerd wordt. De energie meet men door in het smeltbad mee te kijken en door temperaturen tijdens het smelten te registreren. Veel van deze systemen geven achteraf uitsluitsel.
Meer geavanceerde systemen zijn al in staat om een waarschuwing te geven als er iets gebeurt in het proces dat tot afkeur van het werkstuk kan leiden. Het is dan aan de engineer om te beslissen of een mogelijke fout in deze laag en in dit deel van het werkstuk reden voor eventuele falen kan zijn. Dan kan het AM-proces worden afgebroken.
Terugkoppeling
De echte doorbraak van additive manufacturing vraagt echter om meer; om een ‘realtime closed feed-back loop’ waarin de meetdata worden teruggekoppeld naar de besturing van de machine om eventueel tijdens het 3D-printen parameters aan te passen. Een eerste aanzet tot zo’n oplossing is door een Japanse fabrikant van hybridemachines ontwikkeld. Nadat een bepaald aantal lagen is geprint en nabewerkt (de hybridemachine combineert AM met microfrezen), wordt de hoogte gemeten en vervolgens worden afwijkingen ten opzichte van het oorspronkelijke model geleidelijk gecompenseerd.
De ultieme closed-loop regelt niet alleen de 3D-metaalprinter tijdens het printproces bij, maar geeft eveneens input aan de design- en simulatiesoftware om daar aanpassingen te doen op basis van de geregistreerde data in de praktijk. De ontwikkeling van dergelijke closed feedback loops staat echter nog relatief aan het begin, waarbij de fabrikanten van bepaalde AM-technieken (zoals Electron Beam Melting) weliswaar verder staan dan andere (bijvoorbeeld Binder Jetting, wat zich niet leent voor thermische controle).
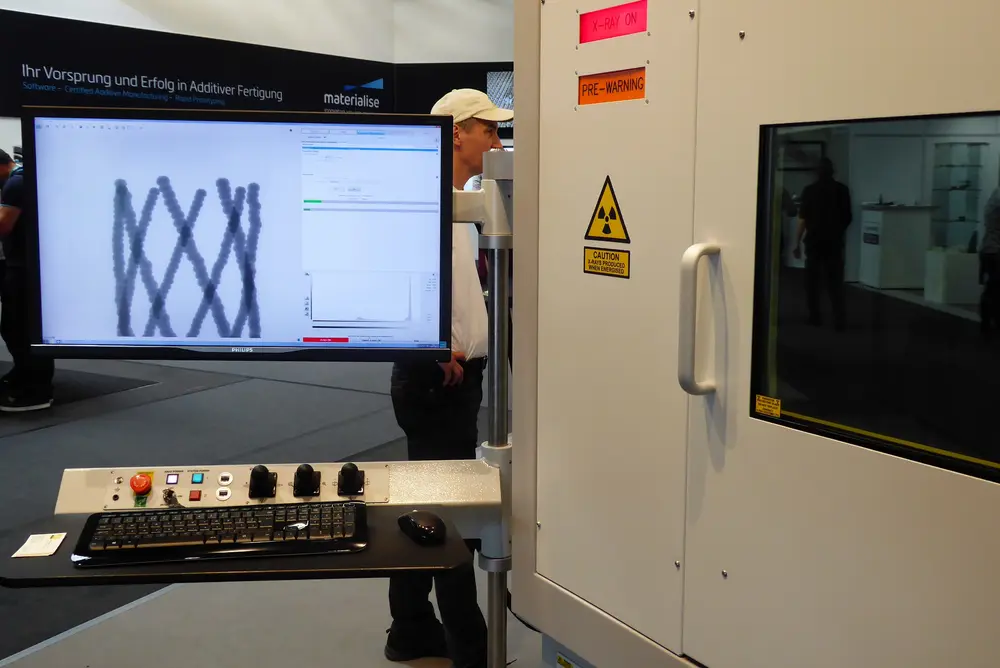
X-ray en CT-scan
Waarschijnlijk zullen NDT-technieken nog lange tijd nodig blijven in de AM-industrie, al is het maar voor de controle van het eerste juiste werkstuk. Dat men technieken zoals digitale X-ray en computertomografie (CT-scan) nodig heeft, heeft alles te maken met de designvrijheid die additive manufacturing biedt, naast het uitsluiten van poriën en microcracks. Men wil dwars door het werkstuk heen kunnen kijken. Defecten aan de buitenkant van het werkstuk kan men visueel detecteren; interne poriën echter niet. Daarnaast is er nog het risico op lagen die niet voldoende aan elkaar hechten, omdat er onvoldoende poeder gesmolten is.
Beperkingen
Eigenlijk geeft geen enkele NDT-test echter een een antwoord op alle mogelijke fouten. Een CT-scan detecteert wel externe fouten, oppervlakte- en inwendige porositeit en insluitingen, maar bijvoorbeeld niet of twee lagen onvoldoende aan elkaar hechten. Digitale X-ray, met camera’s die elke laag digitaal vastleggen en deze data analyseren, geeft bijvoorbeeld geen uitsluitsel over oppervlakteporositeit. Afhankelijk van de kwalificatie van AM-onderdelen zullen dus bepaalde metingen 100% uitgevoerd moeten worden. Daarom zet men zo sterk in op de ontwikkeling van betrouwbare software om, zodra voldoende meetdata beschikbaar zijn, de 100% controle van kritische onderdelen af te bouwen.
Computertomografie lijkt momenteel een belangrijke rol te gaan spelen in additive manufacturing, omdat de techniek niet alleen kan worden gebruik om defecten op te sporen, maar ook om bijvoorbeeld de wanddikte te controleren of om geometrische vervormingen vast te stellen. Hierbij gebruiken de fabrikanten van CT-scanners het oorspronkelijke CAD-model weer als referentie om de afwijkingen in weer te geven.
De beperking van deze meettechnologie is dat het een vergelijkende meettechniek is: wie de wanddikte met een CT-scan meet, moet deze vergelijken met een bestaand product. Bij 3D-printen betekent dit dat men waarschijnlijk niet onder één destructieve test uitkomt. Daarnaast zijn de meetresultaten afhankelijk van de mate waarin het CT-scansysteem de beelden kan samenstellen en reproduceren. Resolutie, artefacten en dataververvuiling kunnen het resultaat beïnvloeden. De derde belemmering is dat de technologie vandaag niet gebruikt wordt in het doorsnee maakbedrijf en dat de investeringen in de systemen hoog zijn.
Penetrant Testing
Een derde testtechniek die men gebruikt, is de zogenaamde Penetrant Testing, evenals de variant Fluorescent Penetrant Inspection. Deze oude techniek komt uit de gietindustrie en wordt gebruikt om oppervlaktefouten zoals cracks, vermoeiing, onvoldoende hechting van lagen en oppervlakteporositeit vast te stellen. Inwendige poriën kan men hiermee echter niet detecteren.
PT is gebaseerd op het principe dat een vloeistof met een lage oppervlaktespanning in een oppervlaktedefect vloeit. Afhankelijk van het type vloeistof (fluorescerend of niet), controleert men onder ultraviolet licht het werkstuk en worden fouten zichtbaar.
Een vliegtuigbouwer als Airbus eist deze test momenteel voor AM-stukken. Airbus verlangt echter ook nog destructieve testgegevens. De echte, allesomvattende meetoplossing voor AM bestaat momenteel nog niet.