L‘impressioN 3D metal necessite de revoir le controle qualite
LA PIECE IMPRIMEE est-elle correcte?
La fabrication additive s‘oriente vers la production en série. Ces chiffres ne sont pas encore très élevés mais il existe de plus en plus d‘applications pour lesquelles des pièces ou des modules complets sont imprimés en 3D. Cela augmente le besoin de techniques de contrôle qualité adéquates. En effet, comment démontrer qu‘une pièce imprimée en 3D répond à toutes les exigences et pas seulement à la précision dimensionnelle?
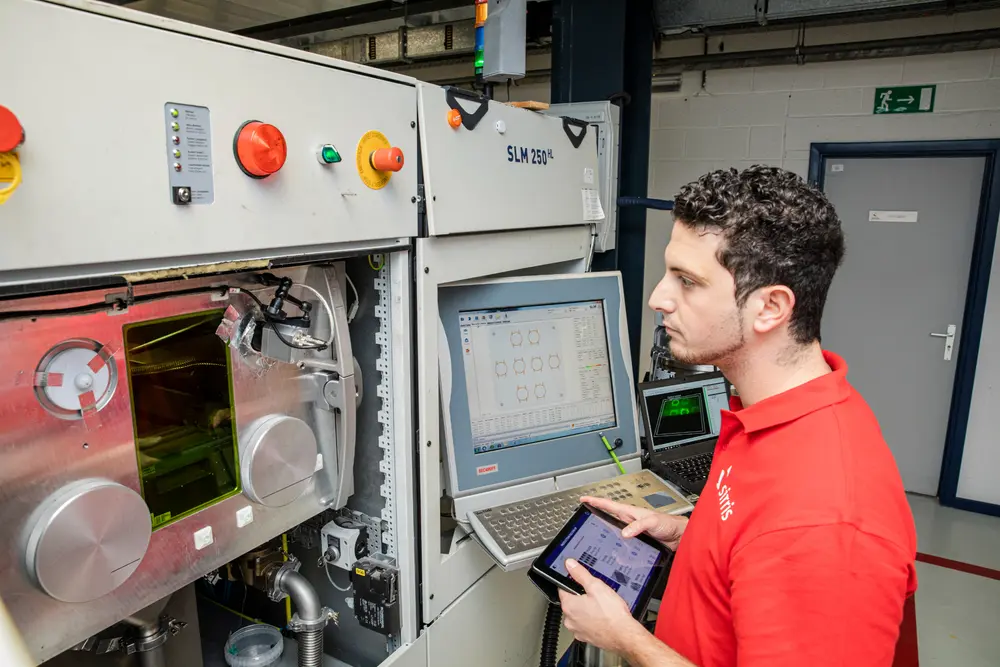
Controle qualite
Mesurer, c‘est savoir. Dans l‘industrie manufacturière, ce principe est aussi vieux que l‘industrie elle-même. Dans l‘industrie de l‘usinage, mesurer consiste principalement à vérifier la précision géométrique, la rugosité de surface et - dans l‘industrie des semi-conducteurs, par exemple - la propreté technique des pièces. Pour certaines pièces critiques, on effectue encore un essai non destructif (Non Destructive Test) mais pour de nombreuses applications, il suffit de prouver l‘origine du matériel au moyen d‘un certificat. Si l‘on ajoute des outils et des paramètres de processus validés, cela suffit à prouver la qualité.
Les choses sont différentes pour l‘impression 3D sur métal. Avec cette technologie, les propriétés mécaniques de la pièce n‘apparaissent que pendant le processus de FA. Des paramètres divergents peuvent entraîner des propriétés différentes de celles d‘un produit similaire. Il faut donc d‘autres solutions que la CMM (machine de mesure des coordonnées) classique.
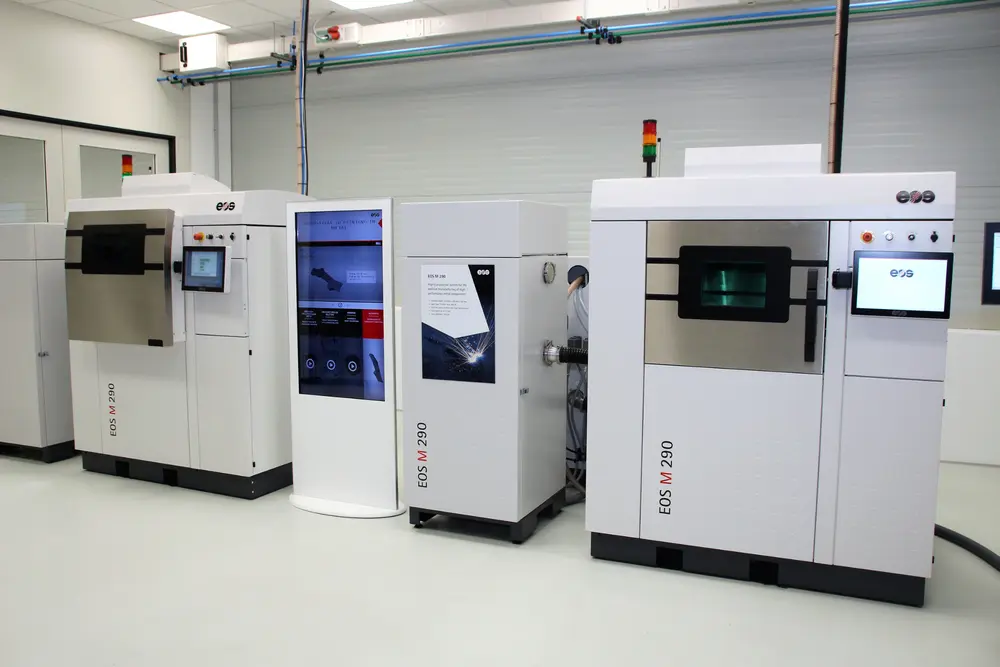
SCAN 3D CONTRE MESURE TACTILE
Pour vérifier la précision dimensionnelle d‘une pièce imprimée en 3D, on peut utiliser une CMM classique avec palpeur. Cependant, cela n‘a pas vraiment de sens car la précision avec laquelle la machine de mesure fonctionne est un facteur de 50 à 100 supérieur à la précision d‘une imprimante 3D pour métaux moyenne, l‘accent étant mis dans cet article sur la fusion laser de poudres métalliques.
Un deuxième défaut de la mesure tactile est que les produits imprimés en 3D ont souvent des formes très capricieuses, surtout lorsque les projets sont réalisés avec un logiciel de conception générative afin d‘utiliser le moins de matériau possible. Dans ce cas, il est possible que les surfaces à vérifier ne puissent même pas être touchées par la sonde.
Une solution à ce problème est le balayage optique 3D. Des scanners à lumière bleue et blanche permettent de cartographier une forme complexe rapidement et sans intervention humaine, dans une résolution suffisamment élevée pour correspondre à la précision de la technologie d‘impression 3D sur métal. Dans le logiciel correspondant, les résultats du scan 3D sont placés sur le modèle CAO original et les écarts sont immédiatement visibles. Cette méthode peut également être utilisée pour comparer différentes stratégies d‘impression, par exemple pour obtenir la meilleure qualité de surface possible.
Dans un projet de recherche européen récemment clôturé, les partenaires du projet sont allés plus loin: ils ont utilisé les données de mesure pour faciliter le post-traitement des pièces. En effet, le post-traitement est l‘une des pierres d‘achoppement car il prend du temps; surtout la préparation du travail. Lorsque la pièce est scannée en 3D, elle est déjà dans la pince, de sorte que l‘orientation est connue et que la pince peut être placée avec la pièce sur une machine CNC.
La fabrication additive s‘oriente vers la production en série. Ces chiffres ne sont pas encore très élevés mais il existe de plus en plus d‘applications pour lesquelles des pièces ou des modules complets sont imprimés en 3D
Algorithme
Dans le cadre du projet, on a développé un algorithme qui est alimenté par les résultats du scan 3D. Le logiciel détermine d‘abord si la pièce provenant de l‘imprimante 3D sur métal a suffisamment de surplus pour être post-traitée. En effet, elle peut être déformée au cours du processus d‘impression à tel point qu‘on ne puisse plus atteindre la précision dimensionnelle à certains endroits. Dans ce cas, il est inutile de procéder à une nouvelle étape de post-traitement coûteuse. Cela peut être considéré comme une première étape pour mesurer la précision géométrique.
Ensuite, l‘algorithme calcule, sur base des données du scan, où il faut encore enlever de la matière et en quelle quantité. Des différences peuvent se produire: c‘est inhérent au processus de fusion laser. L‘algorithme compare les données du scan avec le modèle de CAO d‘origine et ajuste le fichier CN existant afin que la pince avec la pièce puisse être placée directement sur la fraiseuse CNC pour effectuer l‘étape finale de l‘usinage.
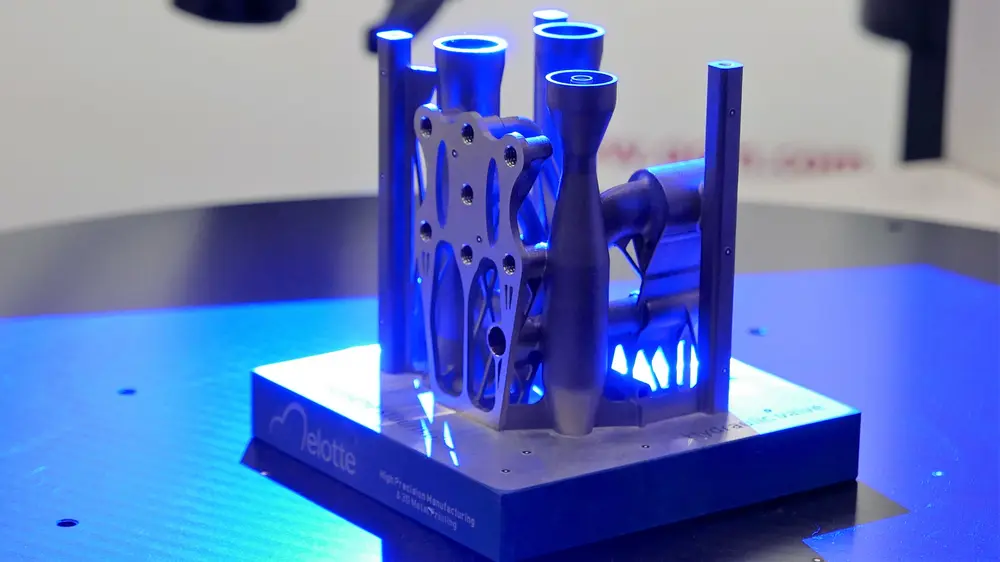
Logiciel et technologie de capteur
Le scan 3D permet de connaître avec certitude les dimensions de la pièce. Pour de nombreuses applications, ont veut également s‘assurer qu‘aucun pore ou inclusion ne s‘est formé dans la pièce lors de l‘impression 3D afin d‘éviter l‘apparition de microfissures par la suite. C‘est une certitude que les fabricants d‘imprimantes 3D sur métal veulent obtenir en collectant des données au cours du processus.
Un changement fondamental du contrôle qualité par rapport au traitement mécanique conventionnel devient donc une évidence. Comme on l‘a dit les propriétés classiques des matériaux sont principalement démontrées en se référant aux normes standardisées auxquelles répond le matériau acheté, le certificat d‘origine constituant une sécurité supplémentaire pour les applications très critiques. Cette possibilité est éliminée avec la fabrication additive car les propriétés des matériaux apparaissent au cours du processus. Toutefois, des experts soulignent que la contrôle des poudres fournies devrait constituer la première étape du contrôle qualité.
Le contrôle qualité des pièces imprimées en 3D se fera de plus en plus in situ, couche par couche. L‘idée est qu‘un travail de construction soit optimisé - souvent avec un logiciel de simulation - et que la première pièce soit contrôlée. Si c‘est bon et qu‘on peut prouver que les produits suivants ont été imprimés avec les mêmes réglages et que les capteurs et les caméras rapides ne détectent aucune déviation, on peut supposer que ces pièces ont la même qualité que la première. On parle aussi de ‘rayon X digital‘ car on construit une image radiographique de toute la pièce à l‘aide des paramètres de chaque couche.
Le contrôle qualité des pièces imprimées en 3D se fera de plus en plus in situ, couche par couche
Deux éléments clés du contrôle de processus in situ sont la bonne répartition de la poudre sur l‘ensemble du lit et la quantité d‘énergie qui est injectée. La distribution uniforme de la poudre peut être contrôlée en faisant une image de chaque couche, laquelle est ensuite analysée via le machine learning et l‘intelligence artificielle, entre autres. L‘énergie est mesurée en observant le bain de fusion et en enregistrant les températures pendant la fusion. Nombre de ces systèmes fournissent une réponse définitive par la suite.
Certains systèmes plus avancés sont déjà capables d‘envoyer un avertissement s‘il se produit dans le processus quelque chose qui pourrait conduire au rejet de la pièce. Il appartient ensuite à l‘ingénieur de décider si une erreur dans cette couche et dans cette partie de la pièce peut causer une défaillance. Si c‘est le cas, le processus de FA peut être interrompu.
Feedback
Mais la véritable percée de la fabrication additive exige davantage: une ‘realtime closed feedback loop‘ dans laquelle les données de mesure sont renvoyées à la commande de la machine pour ajuster les paramètres pendant l‘impression 3D. Une première étape vers cette solution a été développée par un fabricant japonais de machines hybrides. Après l‘impression et le post-traitement d‘un certain nombre de couches (la machine hybride combine la FA et le micro-fraisage), la hauteur est mesurée, puis les écarts par rapport au modèle original sont progressivement compensés.
La dernière boucle fermée permet non seulement d‘ajuster l‘imprimante 3D pour métal pendant le processus d‘impression, mais aussi de fournir des données au logiciel de conception et de simulation pour effectuer des ajustements sur base des données enregistrées dans la pratique. Toutefois, le développement de ces boucles de feedback fermées n‘en est encore qu‘à ses débuts car les fabricants de certaines techniques FA (comme l‘Electron Beam Melting) sont plus avancés que d‘autres (par exemple le Binder Jetting ne se prête pas au contrôle thermique).
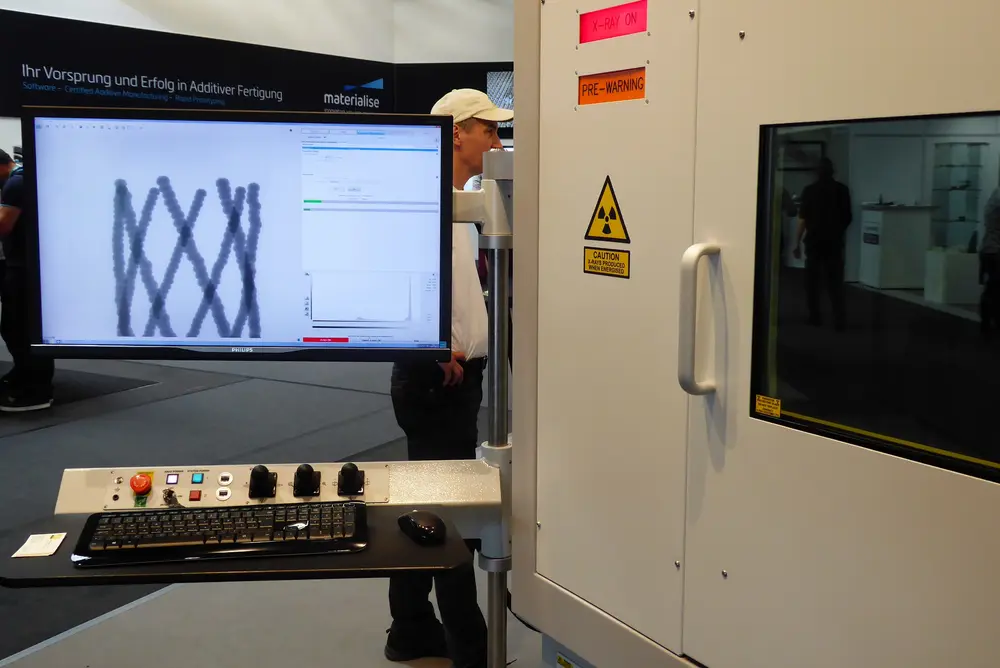
Rayon x et CT scan
Il est probable que les techniques NDT resteront encore longtemps nécessaires dans l‘industrie de la FA, ne serait-ce que pour contrôler la première pièce. Si l‘on a besoin de techniques telles que la radiographie numérique et la tomographie assistée par ordinateur (CT scan), c‘est dû à la liberté de conception offerte par la fabrication additive, en plus de l‘exclusion des pores et des microfissures. Les gens veulent pouvoir voir à travers la pièce. Les défauts sur l‘extérieur de la pièce peuvent être détectés visuellement, mais pas les pores internes. En outre, il y a aussi le risque que les couches n‘adhèrent pas suffisamment les unes aux autres parce qu‘une quantité insuffisante de poudre a fondu.
Restrictions
En fait, aucun essai NDT ne permet de répondre à toutes les erreurs possibles. Un CT scan permet de détecter les défauts externes, la porosité de surface et interne et les inclusions, mais ne détecte pas, par exemple, si deux couches n‘adhèrent pas suffisamment. La radiographie numérique, avec des caméras qui enregistrent numériquement chaque couche et analysent ces données, ne donne pas de réponse définitive quant à la porosité de la surface. En fonction de la qualification des composants FA, certaines mesures devront donc être effectuées à 100%. Voilà pourquoi on consacre autant d‘efforts au développement de logiciels fiables pour réduire le contrôle complet des pièces critiques dès qu‘on dispose de suffisamment de données de mesure.
La tomographie par ordinateur semble actuellement jouer un rôle important dans la fabrication additive car cette technique peut être utilisée non seulement pour détecter des défauts, mais aussi, par exemple, pour vérifier l‘épaisseur de la paroi ou pour déterminer des déformations géométriques. A cet effet, les fabricants de scanners CT utilisent le modèle CAO original comme référence pour afficher les écarts. La restriction ici est qu‘il s‘agit d‘une technique de mesure comparative: lorsqu‘on mesure l‘épaisseur d‘une paroi à l‘aide d‘un scanner, il faut la comparer avec un produit existant. Avec l‘impression 3D, cela signifie que l‘on ne peut probablement pas se passer d‘un test destructif. En outre, les résultats des mesures dépendent de la mesure dans laquelle le système de tomodensitométrie peut composer et reproduire les images. La résolution, les artefacts et la contamination des données peuvent influencer le résultat. Le troisième obstacle est qu‘aujourd‘hui, la technologie n‘est pas utilisée dans l‘entreprise de fabrication moyenne et que les investissements dans les systèmes sont élevés.
Penetrant Testing
Une troisième technique de test est le Penetrant Testing (ressuage), ainsi que l‘inspection par ressuage fluorescent. Cette ancienne technique provient de l‘industrie du moulage et est utilisée pour constater les défauts de surface tels que les fissures, la fatigue, l‘adhérence insuffisante des couches et la porosité de la surface. Cependant, cette technique ne permet pas de détecter les pores internes. Le PT est basé sur le principe qu‘un liquide ayant une faible tension superficielle peut s‘insérer dans un défaut de surface. Selon le type de liquide (fluorescent ou non), la pièce est contrôlée sous lumière ultraviolette et les défauts deviennent visibles. Un constructeur aéronautique tel qu‘Airbus exige actuellement ce test pour les pièces de FA. Cependant, Airbus souhaite également des données issues d‘essais destructifs. En fait, il n‘existe pas encore de véritable solution de mesure globale pour la FA.