Digitalisering verkleint risico op productie-uitval
Gereedschapsbeheer succesfactor voor automatisering
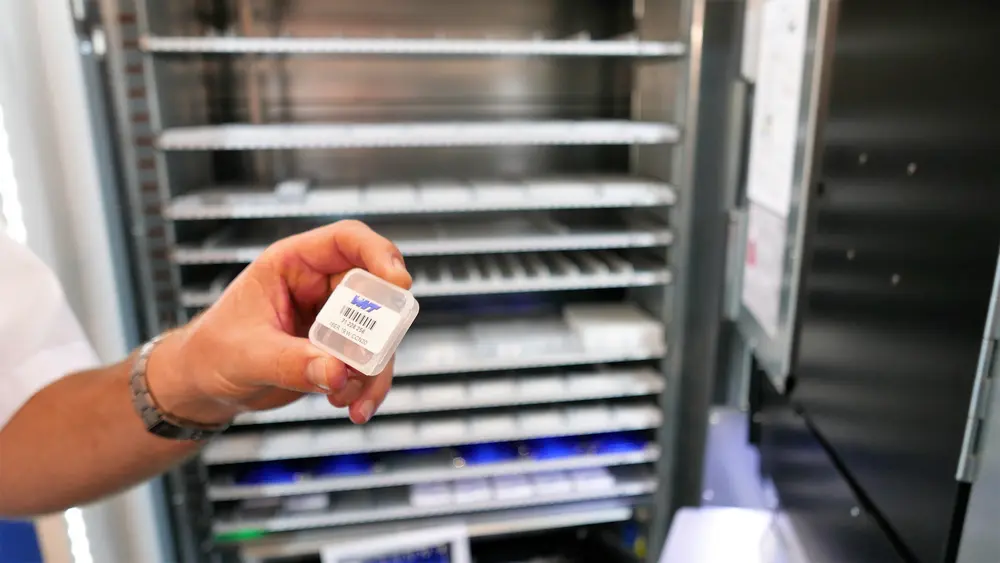
Wie aan verspanende bedrijven die de eerste ervaringen met robotisering hebben opgedaan vraagt naar de grootste verandering, hoort vaak het omgaan met gereedschappen. Zodra de CNC-operator niet meer voor elke batch of elk stuk lange tijd aan de machine staat, wordt goed gereedschapsbeheer een succesfactor. Daarmee voorkom je onder andere onverwachte storingen doordat een gereedschap voorbij de standtijd is.
Digitalisering cruciaal in gereedschapsbeheer
Gereedschappen zijn gemiddeld goed voor zo'n 3 tot 5 procent van de kostprijs van een CNC-verspaand product, afhankelijk van het materiaal en de complexiteit. Dat relatief geringe percentage weerspiegelt niet het belang van goed gereedschapsbeheer.
Dat thema speelt tegenwoordig door het hele maakproces een rol, vanaf programmeren en beheer van voorraden tot en met de bewerkingsprocessen zelf. Het trefwoord in de hele ontwikkeling van gereedschapsbeheer is digitalisering.
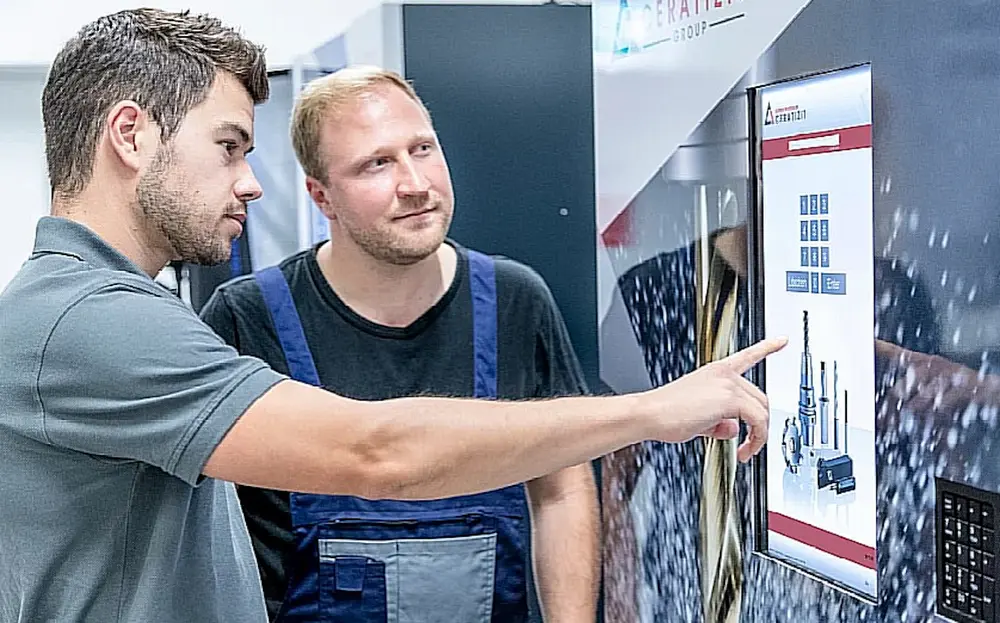
Wat voor uitgiftesysteem?
Operators die de juiste frees, boor of beitel voor een draaimachine zoeken, zijn niet met hun feitelijke werk bezig: spanen maken. Het aandeel gereedschapskosten in de totale kostprijs mag dan beperkt zijn, dat geldt niet voor de loon- en machinekosten die vaak al snel meer dan de helft van de totale kostprijs zijn. Een operator die een gereedschap zoekt, veroorzaakt kosten doordat een machine stilstaat.
Een oplossing hiervoor is het concentreren van het gereedschapsbeheer op één plek. Daar wordt de voorraad bewaakt, vindt het voorinstellen plaats en worden de juiste insteldata naar de machine gestuurd in de ideale situatie. Wie het voorinstellen liever aan de operators laat, kan het gebruik van automatische uitgiftesystemen overwegen.
Deze kasten bieden plaats aan de hele voorraad gereedschappen, zodat telkens als een operator iets uitneemt, de voorraad automatisch wordt aangepast. In feite zijn er twee opties voor deze systemen: een uitgiftesysteem van een gereedschapsfabrikant of een onafhankelijk systeem, waarin gereedschappen van meerdere fabrikanten opgeslagen worden.
Een operator die een gereedschap zoekt, veroorzaakt kosten doordat een machine stilstaat
Besparen
Beide oplossingen hebben voor- en nadelen. Het grootste nadeel van een leveranciersafhankelijk systeem is dat de afhankelijkheid van de leverancier groter wordt.
Anderzijds biedt deze oplossing wel de kans om de bestelprocessen verregaand te automatiseren. Dat voorkomt onnodige stilstand van een machine doordat een gereedschap niet op voorraad is.
Sommige gereedschapsproducenten gaan zover dat ze de tooling in consignatie geven: de gereedschappen in de uitgiftekast blijven eigendom van de producent en er wordt enkel afgerekend wat de operator uitneemt. Als men zo'n systeem met een leverancier goed opstelt, kunnen ook kleinere bedrijven jaarlijks behoorlijk besparen op de orderkosten.
Bovendien: nadenken over standaardisatie kan als het om gereedschappen gaat geen kwaad. Dat levert vaak al een eerste besparing op.
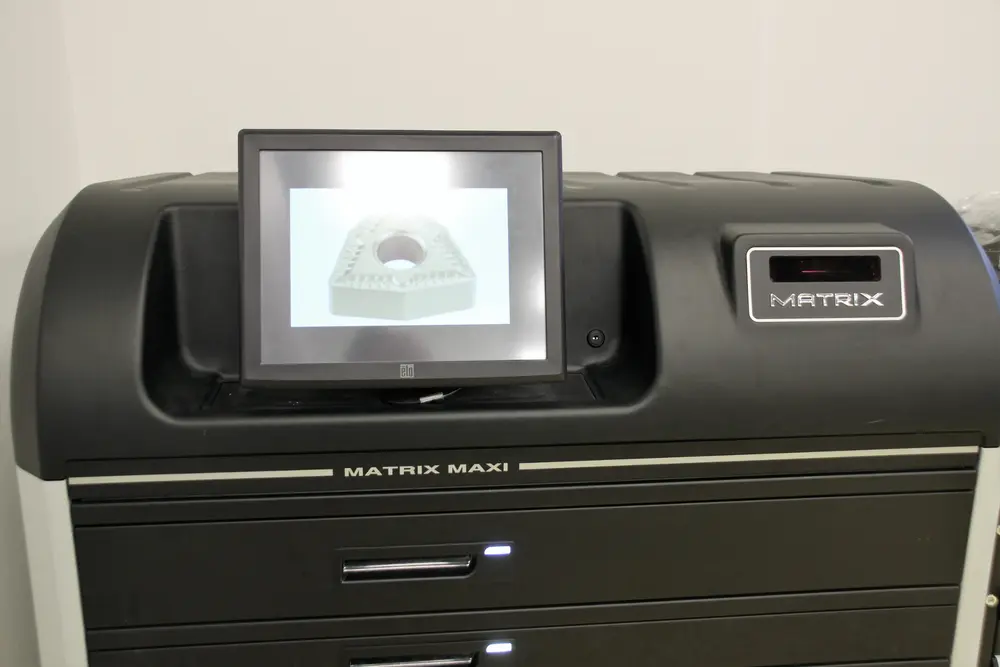
Halvering van de kosten
Het grote voordeel van een uitgiftesysteem in de dagelijkse praktijk is dat er geen tijd verloren gaat aan zoeken van een specifieke wisselplaat, frees of draaibeitel. Ook nemen de voorraden af omdat operators anders hun eigen voorraadje aanhouden bij de machine. Dat leidt dikwijls tot hogere voorraden dan nodig.
Bovendien verliest men het centrale overzicht en krijgt men geen inzicht in het daadwerkelijke verbruik. Wil men met een onafhankelijk uitgiftesysteem werken, dan dient men er in elk geval op te letten dat de software gekoppeld kan worden aan het ERP-systeem dat men gebruikt of aan de gangbare ERP-systemen.
Bestellingen kunnen dan geautomatiseerd worden als voorraden onder een minimumniveau komen. Men kan dan eveneens het gereedschapsverbruik toewijzen aan projecten of orders en men kan het verbruik analyseren.
Cijfers over de praktijk wijzen in de richting van een halvering van de gereedschapskosten als men het gereedschapsbeheer digitaliseert door uitgiftekasten aan een centrale database te koppelen.
Dat lijkt misschien hoog, maar de besparing komt ook tot stand doordat men de gereedschappen efficiënter benut door enerzijds standaardisatie en anderzijds een betere controle van de standtijd. Hiermee kan men de gereedschapskosten per werkstuk fors reduceren.
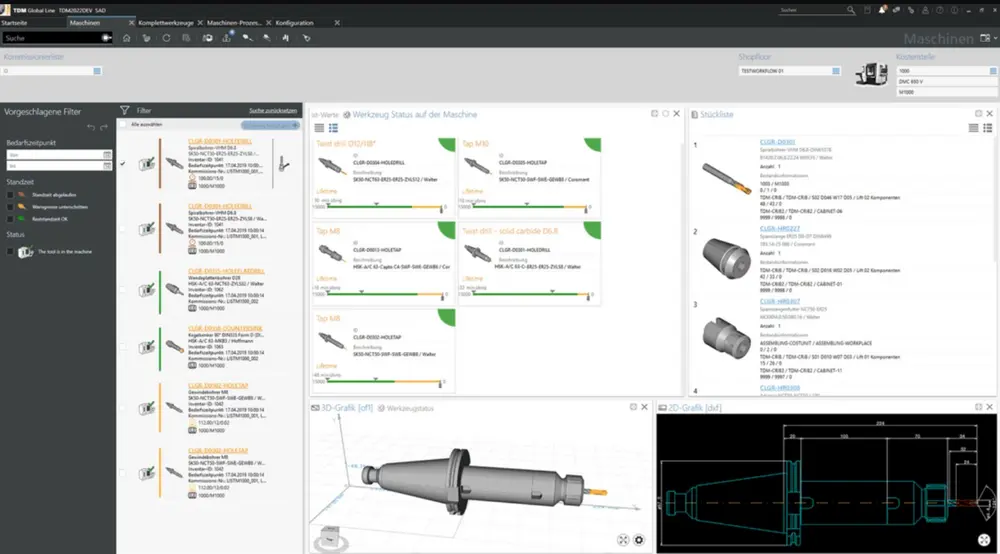
Standtijd bewaken
Nog altijd is het getrainde oor van een CNC-operator een van de beste monitoringsystemen voor de standtijdbewaking. Alleen: door de toenemende automatisering is dat oor niet meer altijd bij de machine beschikbaar. Wie automatiseert en in onbemande uren de spindels laat draaien, zal het gebruik van gereedschappen moeten bewaken.
Dat is een absolute voorwaarde voor succesvolle onbemande productie. Standtijdbewaking van gereedschappen kan onderdeel zijn van de software van de robotcel of gebeurt op de CNC-machine. In dat laatste geval betekent het in feite een stap extra.
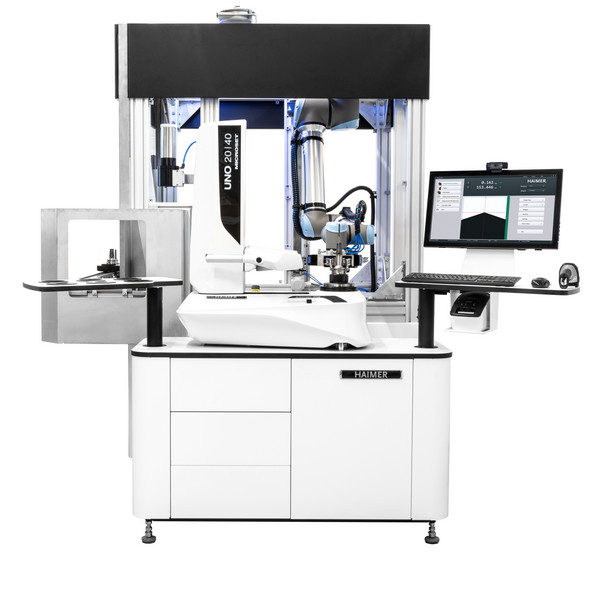
Standtijdbewaking geïntegreerd in de software van de robotcel betekent dat er bij het plannen van de orders automatisch gekeken wordt of de gereedschappen beschikbaar zijn, nog voldoende standtijd hebben en of er eventueel een zustergereedschap aanwezig is.
Een nieuwe trend is dat dit soort gegevens door de CNC-machines na elke bewerking worden doorgegeven aan de centrale database waarin alle informatie over gereedschappen is opgeslagen.
Bij moderne machines verloopt deze communicatie via gestandaardiseerde protocollen, zoals umati of OPC UA. Bij oudere machines zal hiervoor een interface ontwikkeld moeten worden.
Single source of truth
Eigenlijk toont dit het belang om alle gereedschapsdata op een centrale plek te bewaren. Hiermee voorkomt men fouten door gebruik van verkeerde data. Door gereedschapsbeheer digitaal te centraliseren, kan men in de planning en programmering met echte data werken.
Bijvoorbeeld voor het CAM-programmeren. Als men hiervoor met standaard 3D-modellen van houders en gereedschappen programmeert, zullen er afwijkingen ontstaan doordat gereedschappen slijtage vertonen.
Bedrijven willen hun gereedschapsdata in één database opslaan en die koppelen aan alle stappen in het proces
Slaat men alle gereedschapdata centraal op, en is er terugkoppeling vanuit de machine naar deze database, dan is deze database de single source of truth. Dan zijn altijd actuele data beschikbaar en neemt het risico op een botsing van het gereedschap met het werkstuk in kritische situaties af.
In z'n Tool Management System slaat men tevens echte standtijden van gereedschappen op zodat men daarmee in de planning kan rekenen. Dat is dan ook de belangrijkste trend momenteel: bedrijven willen hun gereedschapsdata in één database opslaan en die koppelen aan alle stappen in het proces.
Sommige bedrijven willen met deze gegevens vooruitkijken naar het werk dat de volgende maanden moet worden gedaan en dan bepalen welke gereedschappen hiervoor op voorraad moeten zijn.
Code op de houder
Enkele jaren geleden zag men dat gereedschapsdata dikwijls werden opgeslagen op een chip in de houder. Dat gebeurt nog steeds, maar er zijn ook andere manieren. Het nadeel van een chip is namelijk dat de manier waarop data op de chip worden weggeschreven afhankelijk is van de machinefabrikant.
Elke producent heeft z'n eigen parametervolgorde. Hierdoor kan men deze houders niet zomaar wisselen van de ene naar de andere machine. Een eenvoudige RFID-chip of een dot-matrixcode die verwijst naar de data in het gereedschapsbeheersysteem, is een betere oplossing als men flexibel gereedschappen wil wisselen van machines.
Dat is een goedkoper systeem dan geavanceerde chips die men kan uitlezen en beschrijven. Daarmee ontstaat een doorlopende gegevensuitwisseling tussen de verschillende processtappen in het verspaningsproces. Ook is de gegevensuitwisseling dan bereikbaar voor verschillende machinebesturingen.
De enige stap die nodig is, is het scannen van de dot-matrixcode voordat het gereedschap in de ketting wordt gehangen. Zelfs deze stap kan men met een cobot automatiseren. De foutkans wordt hierdoor praktisch nul.