Les cabines de pulvérisation modernes utilisent l'énergie de manière beaucoup plus réfléchie
Limitation du débit et récupération de la chaleur
Les cabines de pulvérisation consomment beaucoup d'énergie. Etant donné leur fonction, il est impossible d'y échapper. Le chauffage et les moteurs qui entraînent les ventilateurs consomment de nombreux kilowatts. Néanmoins, la génération actuelle de cabines de pulvérisation a une consommation beaucoup plus réfléchie, notamment en s'attaquant directement aux deux plus gros consommateurs. Les programmes éco qui limitent le débit en plus d'un contrôle de fréquence sont déjà assez courants dans la pratique et permettent une première réduction significative. Un récupérateur permettra de réduire encore la consommation totale d'énergie mais étant donné le montant de l'investissement, la récupération de chaleur est beaucoup moins répandue pour l'instant.
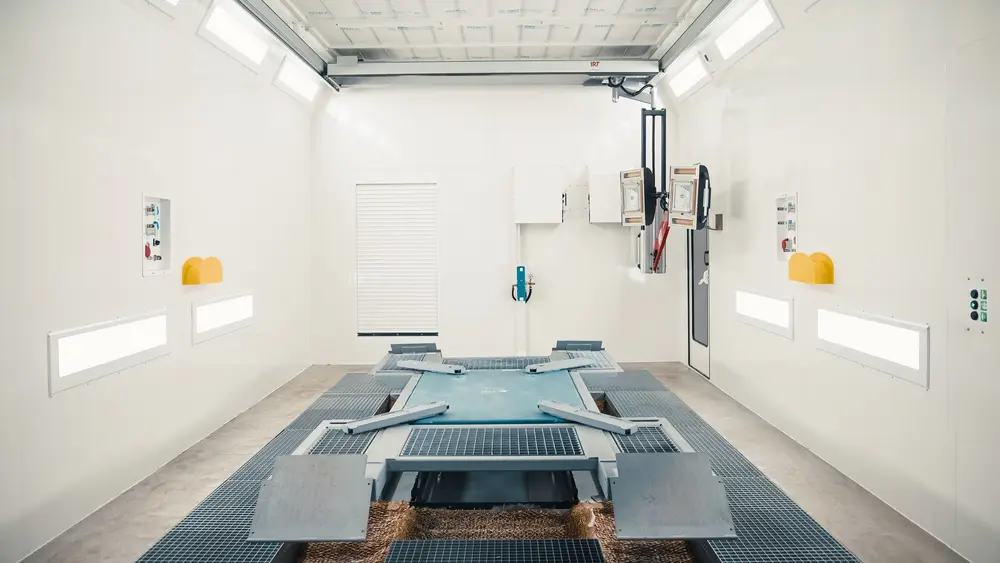
Jamais vraiment durables
Le terme 'durable' signifie que l'impact sur l'environnement est faible grâce à une utilisation limitée des ressources. Les cabines de peinture auront toujours du mal à tenir cette promesse. Il suffit d'un peu de mathématique pour comprendre pourquoi.
Grandes puissances installées
Vous savez que le législateur impose au secteur de travailler exclusivement avec de l'air extérieur pendant la phase de pulvérisation. Prenons un exemple extrême pour la Flandre: supposons qu'il fasse -10 °C à l'extérieur et que l'on veuille atteindre une température de 20 °C dans la cabine de pulvérisation. Il faut alors surmonter un ΔT de 30° avec une vitesse d'air de 0,3 m/s.
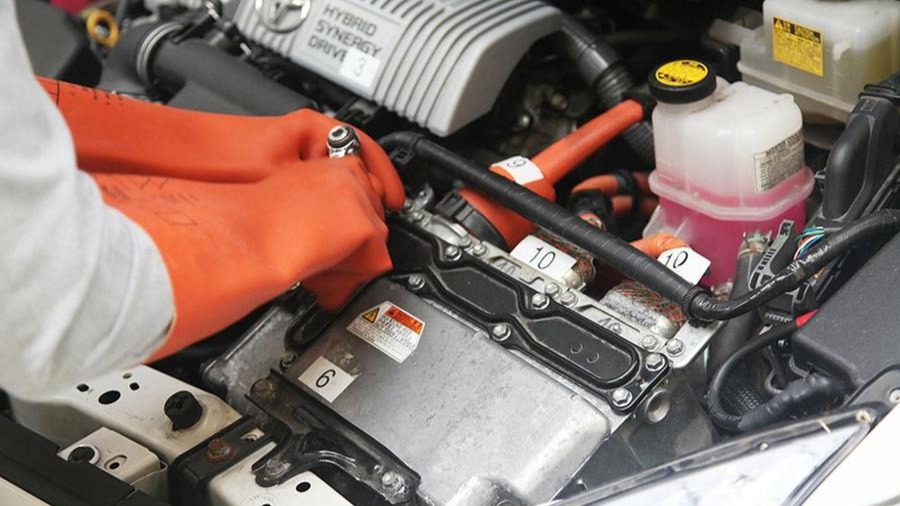
Pour une cabine de 7 x 4 m - pourtant pas très grande -, cela correspond à un débit de 30.000 m³/h, soit l'équivalent d'un bâtiment de 6.000 m² et de 5 m de haut. Cela suppose une énorme puissance calorifique.
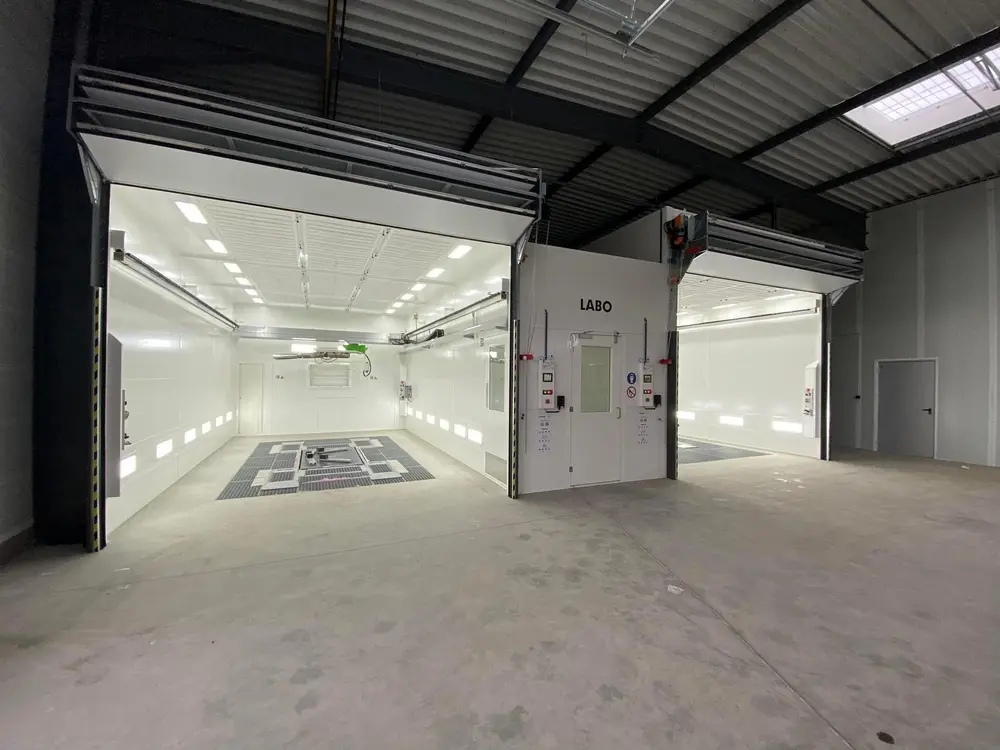
Le 100% électrique n'est pas économique
C'est précisément en raison de la haute puissance calorifique requise qu'on ne peut guère envisager des cabines de pulvérisation entièrement électriques (même dans le futur). Outre la forte sollicitation du réseau électrique et l'obligation d'investir dans une armoire à haute tension ainsi que dans des câbles électriques très épais, le coût de consommation actuel est encore trois fois plus élevé que le prix du gaz.
C'est pourquoi la grande majorité des cabines de pulvérisation actuelles utilisent des brûleurs à gaz modulants à combustion directe qui peuvent fonctionner au gaz naturel ainsi qu'au propane, au butane et au GPL.
Techniquement, l'hydrogène est également une possibilité, mais pour l'instant, les problèmes de stockage et d'autorisation soulèvent des obstacles d'ordre pratique. Par rapport aux brûleurs à gaz à combustion indirecte, le rendement des brûleurs à combustion directe est beaucoup plus élevé: 100% contre 80%. En outre, ces derniers montent en température beaucoup plus rapidement.
Une consommation rationnelle
Les cabines de peinture seront donc toujours caractérisées par des besoins énergétiques élevés, mais cela ne veut pas dire que la consommation ne peut pas être considérée de manière critique. Par rapport à il y a quelques années, les fabricants ont déjà fait des progrès considérables.
Les programmes éco qui limitent le débit en plus d'un contrôle de la fréquence sont déjà très répandus
Limitation du débit
Comme le chauffage est le plus gourmand et dépend directement du débit, c'est là que les gains sont les plus importants. Les programmes éco combinés à des moteurs régulés en fréquence permettent à un automate puissant de calculer le réglage correct de la ventilation.
Grâce à une détection d'air comprimé (le terme anglais 'flow switch' est plus courant) et à un écran tactile IHM, le contrôleur sait quand la pulvérisation a réellement lieu. Ainsi, la pleine puissance n'est sollicitée que pendant la courte période où elle est vraiment nécessaire pendant la pulvérisation.
Cela permet non seulement de réaliser des économies significatives en termes de consommation d'électricité, de l'ordre de 30% en moyenne, mais aussi de réduire considérablement la demande de chaleur en travaillant avec un débit plus faible, puisque 85% de la chaleur est recyclée.
Autres technologies
La réduction du débit est certainement la mesure la plus importante, mais les fabricants proposent également d'autres technologies pour réduire la consommation d'énergie. En voici quelques-unes:
Couche d'isolation plus épaisse
Sur le marché, une couche d'isolation de 50 mm de laine de roche est assez standard. Toutefois, certains optent pour une couche qui mesure 60 mm ou qui présente une densité plus élevée, et l'étendent jusqu'au plénum. Il est également important de réduire les ponts thermiques au strict minimum. Par exemple, en utilisant un système efficace de rainures et languettes et de grands panneaux.
Comme la plupart des laques sèchent aujourd'hui à l'air et que la température ne dépasse donc plus 30 °C, ce point a un peu moins de poids que par le passé. En outre, dans la plupart des cas, on perd plus de chaleur via le canal de soufflage.
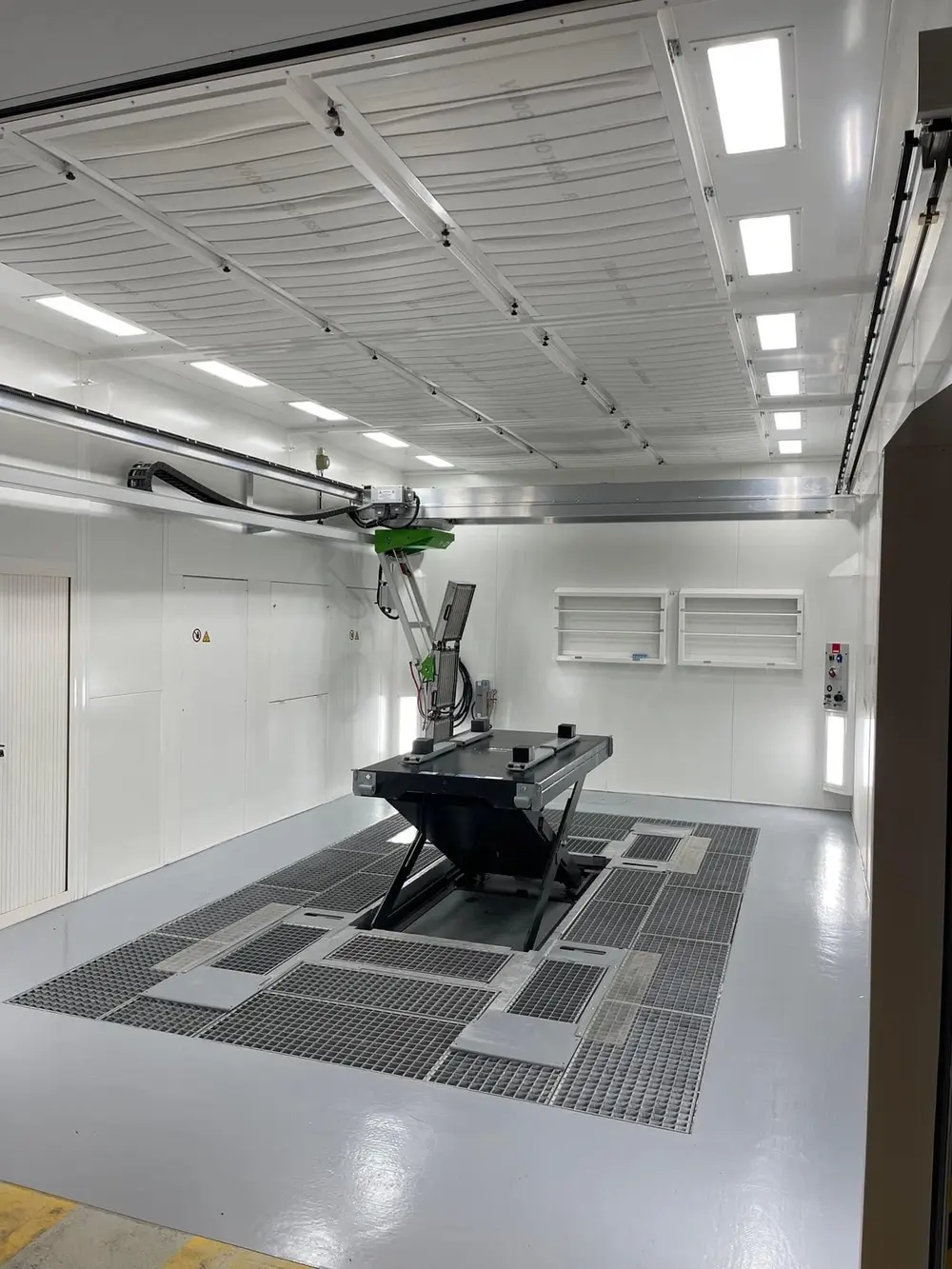
Quick Dry System
Après l'application de la peinture, il y a de toute façon une certaine période de séchage. En travaillant avec des températures plus élevées dans le même laps de temps que la normale, ce système - une sorte de troisième phase avec sa propre température et sa propre vitesse d'air - parvient à réduire le temps de séchage. Il s'applique principalement entre deux couches.
Séchage à température ambiante
Dans le prolongement du point précédent, les fabricants de peinture ont mis au point des peintures qui sèchent plus rapidement à température ambiante. Les analyses doivent montrer si cette solution est plus avantageuse pour votre carrosserie, car le séchage est toujours plus long que le séchage forcé.
Ventilateurs à haut rendement
Le choix du ventilateur détermine la puissance électrique des moteurs. Un ventilateur qui n'est pas sélectionné à son débit maximal nécessitera moins de puissance de la part du moteur et, en outre, fonctionnera plus silencieusement.
Installation modifiable
Chez certains fabricants, l'installation peut s'adapter à la taille de la pièce à peindre grâce à un support pour pièces, véhicules ordinaires (voiture particulière, petite camionnette) ou gros véhicules (SUV, fourgon). Plus le volume de la pièce est important, plus la consommation est faible.
Une cabine de pulvérisation économe en énergie nécessite une forme de récupération de la chaleur
Récupération de la chaleur
Tout ce qui a été dit jusqu'à présent peut être considéré comme assez standard de nos jours. Pour que l'on puisse vraiment parler d'économie d'énergie, il faut que la cabine de pulvérisation dispose d'une forme de récupération de la chaleur.
Deux systèmes courants
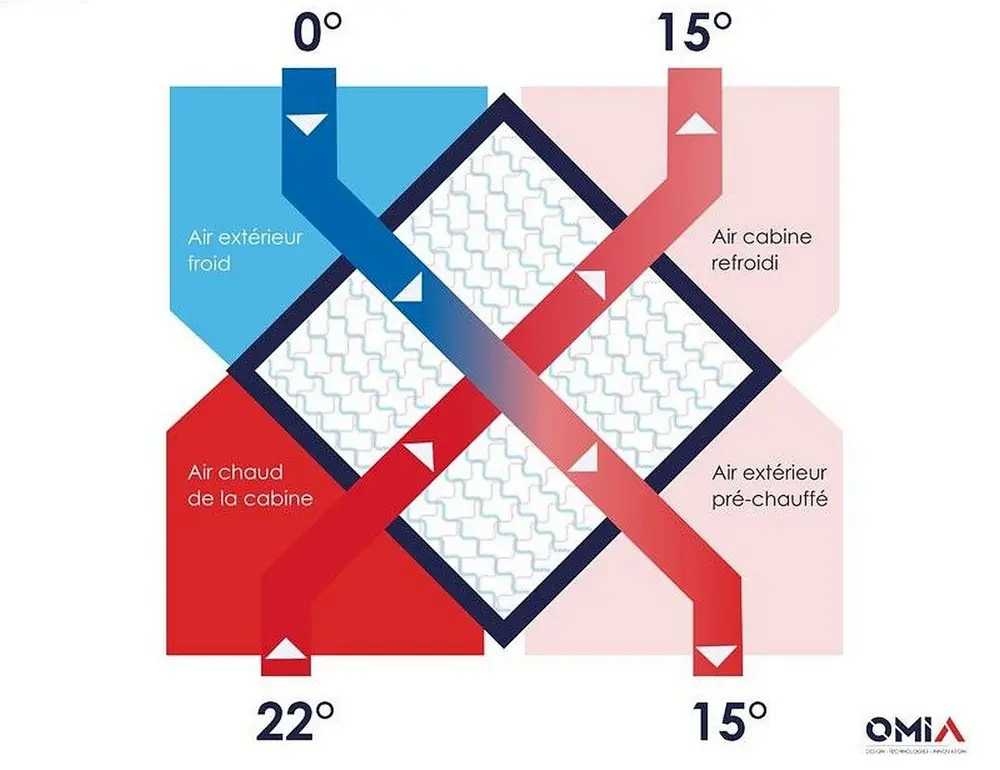
Si l'on souhaite récupérer une partie de la chaleur perdue, on opte généralement pour un échangeur à plaques ou un récupérateur. Il s'agit de préchauffer l'air extrait de l'extérieur avec la chaleur de l'air vicié au moyen d'un échangeur à plaques.
Une alternative au récupérateur est le système twin coil. Le principe de fonctionnement est similaire, sauf que ce système préchauffe l'air frais via un fluide intermédiaire (mélange eau-glycol): l'air sortant va chauffer l'eau avant qu'elle ne soit pompée vers l'endroit où passe l'air frais. En s'appuyant sur des pompes et des vannes, le système twin coil est légèrement plus complexe, ce qui rend également les problèmes techniques plus difficiles à résoudre.
Avantages et inconvénients
Il est évident que les économies d'énergie sont la raison d'investir dans ce genre de systèmes. Avec des phases plus longues, nous parlons toujours d'économies d'environ 50%. Dans le cas d'une utilisation mixte, ce gain tombe à 35-40%. Exprimé en euros, cela représente vite une économie annuelle de 6.000 euros. Bien sûr, ceci est contrebalancé par un investissement important qui, selon le fabricant et le type de cabine de pulvérisation, peut atteindre 30.000 euros.
En termes de retour sur investissement, on parle donc d'une période de 5 à 6 ans. En effet, sachez qu'il faut installer des filtres supplémentaires. Il s'agit souvent d'un post-filtre supplémentaire et d'une cassette de pré-filtre, si cette dernière n'est pas installée de série. Sachez également que la cabine de pulvérisation devra être équipée de moteurs plus lourds en raison d'une perte de charge plus importante. La puissance électrique installée augmentera en conséquence.
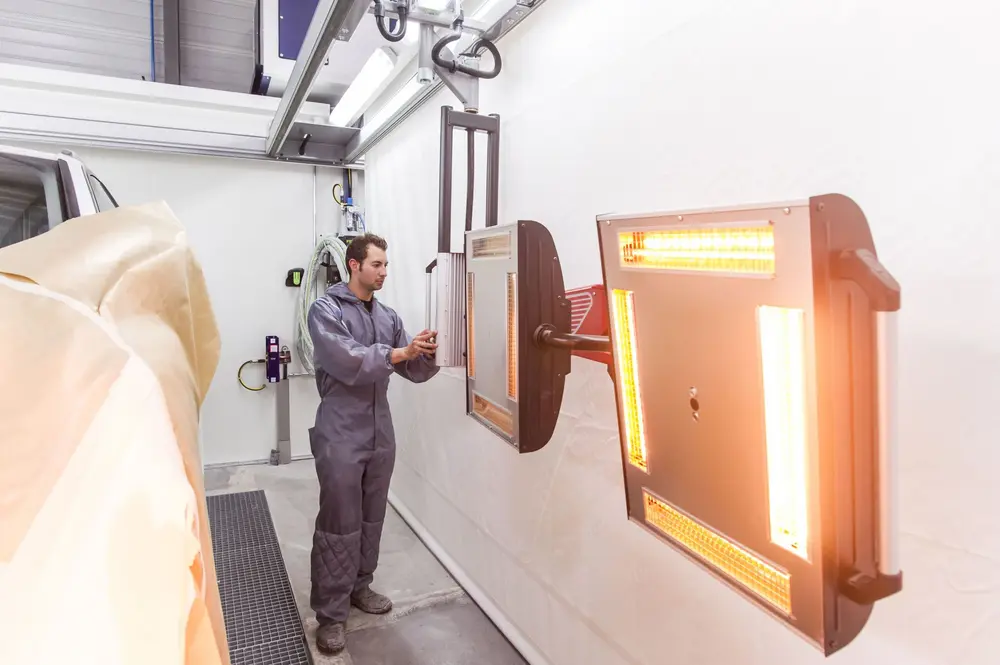
Que nous réserve l'avenir?
Presque tout le monde doute de la faisabilité économique des cabines de pulvérisation purement électriques, mais certains fabricants croient en des solutions hybrides qui tirent l'énergie de sources naturelles renouvelables d'une part et utilisent des combustibles fossiles tels que le gaz d'autre part.
Il est notamment question de la combinaison d'une batterie d'eau chaude et d'un brûleur à gaz direct. La source d'eau chaude pourrait alors être une pompe à chaleur, mais tout aussi bien un réseau urbain ou une production combinée de chaleur et d'électricité (cogénération).
Il faut dire qu'il y a aussi quelques sceptiques. Leur principal contre-argument est que, contrairement à d'autres secteurs, les ateliers de carrosserie ne peuvent pas utiliser la chaleur résiduelle des processus de production. Les partisans de la cogénération, quant à eux, font valoir que la production d'électricité elle-même fournit la chaleur résiduelle (générée lors du refroidissement du générateur) et qu'aucun autre processus de production n'est donc nécessaire.
Outre les solutions hybrides, qui ne sont certes pas nouvelles, les fabricants soulignent le développement des panneaux IR en combinaison avec des murs réfléchissants. L'IR présente l'avantage important de permettre un séchage beaucoup plus ciblé et donc plus efficace.
Avec la collaboration de CSB², Garmat et Sima