les défis des plaquettes de tournage
Les nouvelles technologies de coupe et l'e-mobilité stimulent l'innovation
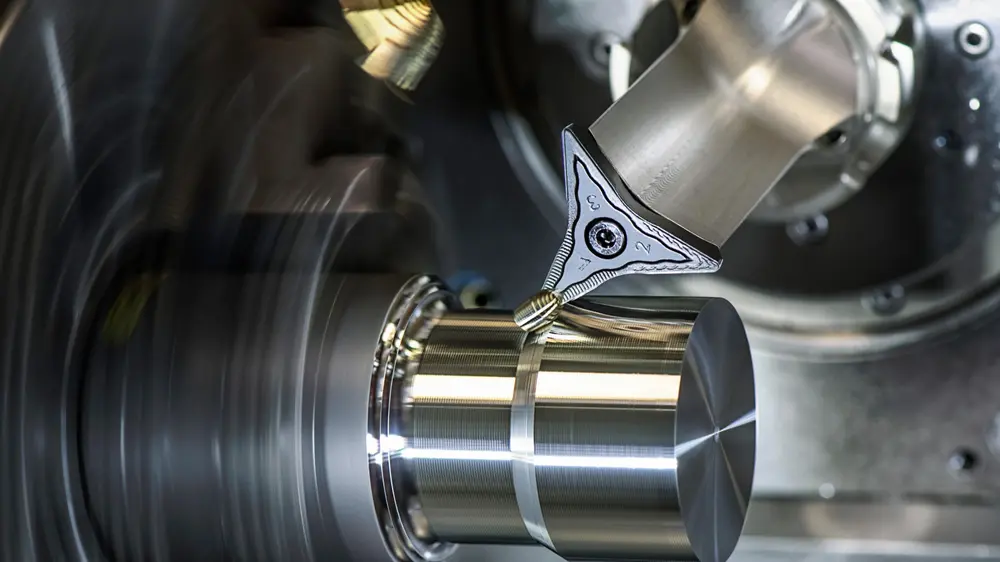
Diverses tendances mondiales affecteront le marché des plaquettes dans les années à venir. Ces évolutions vont imposer de nouvelles exigences aux outils de coupe. Les fabricants anticipent et s'y préparent déjà pleinement.
les EVOlutions dans l'industrie automobile ...
L'industrie automobile représente 43 % de toutes les machines-outils produites chaque année par les fabricants allemands. Il en sera de même en Europe. Ce secteur, avec tous ses fournisseurs, est l'un des plus gros acheteurs de machines et d'outils CNC, avec les constructeurs de machines eux-mêmes et leurs chaînes d'approvisionnement. Une proportion importante d'entre eux est utilisée pour la production de composants de moteurs à combustion interne et l'usinage du bloc moteur lui-même.
Les exigences strictes en matière de CO2 obligent désormais les fabricants à se tourner vers d'autres concepts d'entraînement. À court terme, il s'agit notamment de la batterie du véhicule électrique, de la voiture électrique qui tire son énergie de ses batteries, et des modèles hybrides. Cependant, une telle chaîne de traction électrique comporte beaucoup moins de composants de fraisage et de tournage qu'un moteur à combustion interne. En termes économiques, cela a un impact majeur sur le secteur. En termes de technologie d'usinage, cette transition apportera également des changements.
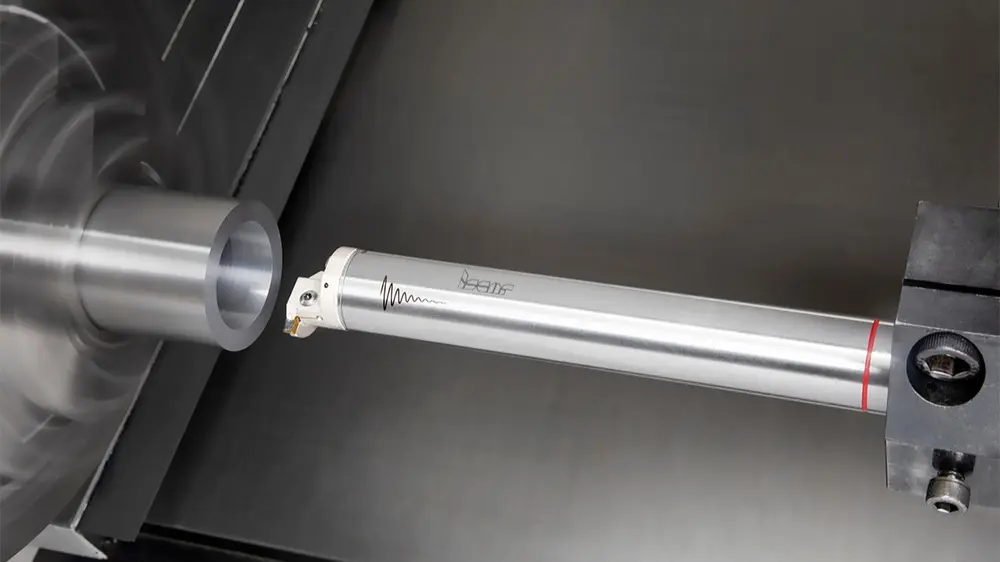
... entraînent des changements dans le segment des plaquettes
Autres types de matériaux
L'allègement est encore plus important pour une voiture à moteur électrique que pour une voiture à moteur à combustion interne. Une voiture de taille moyenne peut donc contenir jusqu'à 160 kg de composants en aluminium. Depuis quelque temps, l'aluminium gagne du terrain en tant que matériau léger. Bien que le boîtier de la batterie soit souvent en aluminium également, les fabricants de modèles électriques sportifs et haut de gamme optent souvent pour des matériaux tels que les plastiques renforcés de fibres de carbone. Ils veulent réduire encore plus le poids du véhicule tout en augmentant sa rigidité.
Des avances plus élevées
Il y a aussi l'évolution des technologies de production. Le moulage de précision gagne des parts de marché, tout comme le forgeage de précision et l'impression 3D. Cela augmente la quantité de matière à usiner. Dans le cas des pièces moulées et des pièces imprimées en 3D, la surépaisseur qui doit encore être usinée est relativement faible. Cette petite surépaisseur nécessite des outils qui permettent des avances et des vitesses de coupe élevées.
Plus d'arêtes de coupe
En outre, les tailles des séries diminuent, de sorte que les changements de pièces seront plus fréquents. Les plaquettes de tournage aux arêtes plus tranchantes offrent un élément de solution, car elles durent plus longtemps. La durabilité devenant un thème explicite dans l'industrie métallurgique, les principaux fabricants s'efforcent également de réduire le gaspillage de matériaux de cette manière. Des arêtes de coupe plus tranchantes signifient une utilisation plus longue du carbure, que de plus en plus de fabricants reprennent dans des programmes de recyclage pour la fabrication de nouveaux outils. Les améliorations proviennent également des nouvelles géométries de coupe, qui réduisent les vibrations et augmentent la capacité de coupe.
plaquettes en céramique
Une amélioration spectaculaire de la vitesse de coupe et donc de la productivité peut être obtenue en utilisant des plaquettes en céramique, qu'elles soient ou non à base de nitrure de silicium comme dans le cas des plaquettes SiAlON ou des plaquettes en céramique renforcées par un whisker (SiCw), ce qui les rend plus résistantes. Les céramiques SiAlON combinent les avantages du réseau de whiskers renforcé avec une stabilité chimique supérieure. Par conséquent, ces matériaux de coupe en céramique se prêtent très bien à l'usinage des superalliages résistants à la chaleur.
L'utilisation de ces matériaux de coupe en céramique conduit à une vision complètement différente du facteur vitesse de coupe. Elle peut être multipliée par un facteur allant jusqu'à 50 lors de l'usinage de superalliages, par exemple. Des vitesses de coupe allant jusqu'à 1.000 m/min sont réalistes. Ces matériaux de coupe sont très résistants à l'usure, ce qui se traduit par une longue durée de vie des outils. Un inconvénient, cependant, est que l'usure ne se manifeste pas réellement comme avec une plaquette conventionnelle, mais devient seulement visible dans la diminution soudaine de la qualité de la surface de la pièce usinée. C'est ainsi que vous constatez le niveau d'usure de la plaquette.
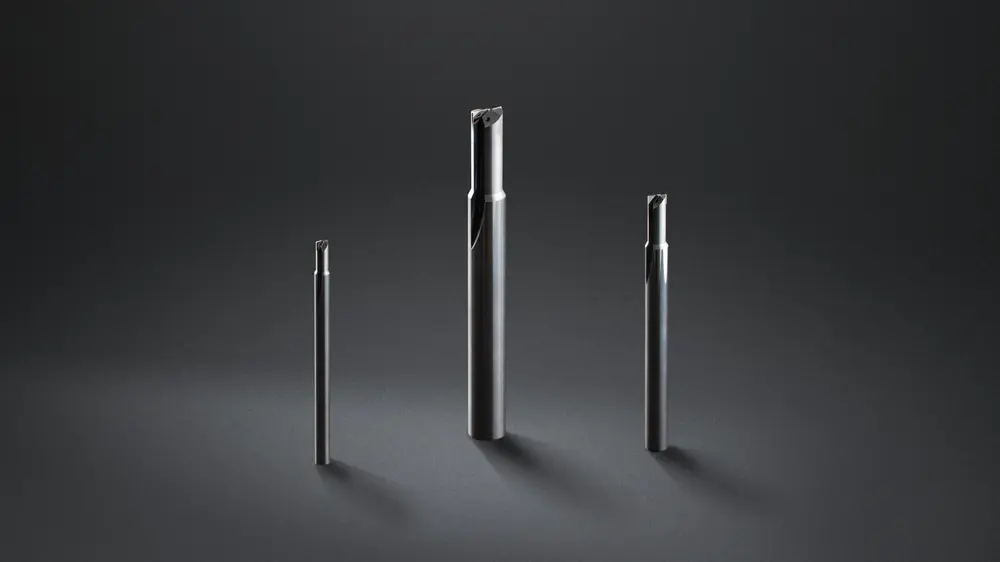
Impact des logiciels de FAO
Les changements survenus du côté des machines obligent également les fabricants d'outils à procéder à des ajustements, tels que de meilleures capacités de tournage sur l'axe Y. Dans ce cas, les forces sont mieux déviées vers le porte-outil, permettant des conditions de coupe plus élevées de manière stable. Les inserts seront mieux adaptés à cela. Les petites séries et la pression sur les coûts conduisent à une augmentation du nombre de machines multitâches permettant de finir complètement les pièces en une seule étape de traitement. La programmation FAO est indispensable à cet effet et offre la possibilité d'appliquer des stratégies d'usinage intelligentes. Un exemple de ce dernier point est le High Dynamic Turning sur les machines multitâches. Dans ce cas, une seule plaquette remplace plusieurs plaquettes qui étaient auparavant nécessaires pour diverses opérations d'usinage.
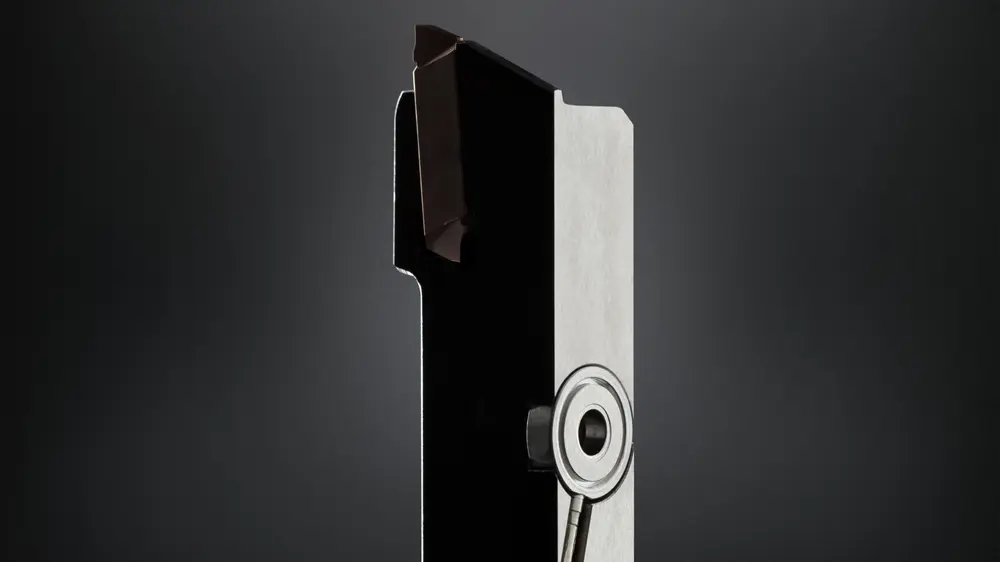
La nouvelle génération de plaquettes convient à la fois à l'ébauche et à la finition, ainsi qu'au tournage de contours et au tournage long. Il en résulte une efficacité accrue. Le nouveau logiciel de FAO donne aux opérateurs de la machine CNC les outils nécessaires pour programmer des opérations d'usinage qui étaient auparavant impensables. Sur la machine multitâche, le tournage est effectué avec l'axe B, la broche de fraisage proprement dite. Cela permet de régler dynamiquement l'angle d'attaque auquel la plaque d'indexation pénètre dans le matériau, contrairement au tournage CNC conventionnel. La commande de la machine surveille le contour de la pièce et effectue simultanément des réglages pour maximiser les performances de la plaque de changement.
Une fois programmés, la trajectoire de l'outil et les angles d'attaque sont automatiquement compensés pour assurer un volume de coupe et une efficacité maximum. Les essais sur le terrain montrent que les mouvements de la machine sont réduits jusqu'à 90 % et que les vitesses d'avance peuvent être augmentées jusqu'à 40 %. L'angle d'attaque variable améliore également la qualité de la surface. La rotation de la plaquette sans faille permet d'obtenir une finition de surface parfaite entre les transitions du tournage parallèle au tournage de contour. Cette stratégie de rotation a un effet positif sur la durée de vie de la plaquette car une plus grande partie de l'arête de coupe est utilisée que la normale.
Nouvelles techniques de revêtement
La technologie des revêtements est également en constante évolution. Non seulement les revêtements eux-mêmes, mais aussi la technologie utilisée pour les appliquer. Le revêtement de la plaquette affecte à la fois les performances de coupe d'un outil et sa durée de vie. Au lieu du procédé PVD (évaporation à basse température, après laquelle un métal réagit avec, par exemple, de l'azote) ou des revêtements CVD (réaction chimique à des températures de 700 - 1.050 °C), la pulvérisation par micro-ondes à impulsions à haute puissance utilise un fin brouillard de pulvérisation. La pulvérisation cathodique permet d'appliquer le revêtement de manière beaucoup plus fine et lisse sur le substrat métallique dur. On obtient donc, en toute logique, des bords de coupe qui conservent davantage leur tranchant.
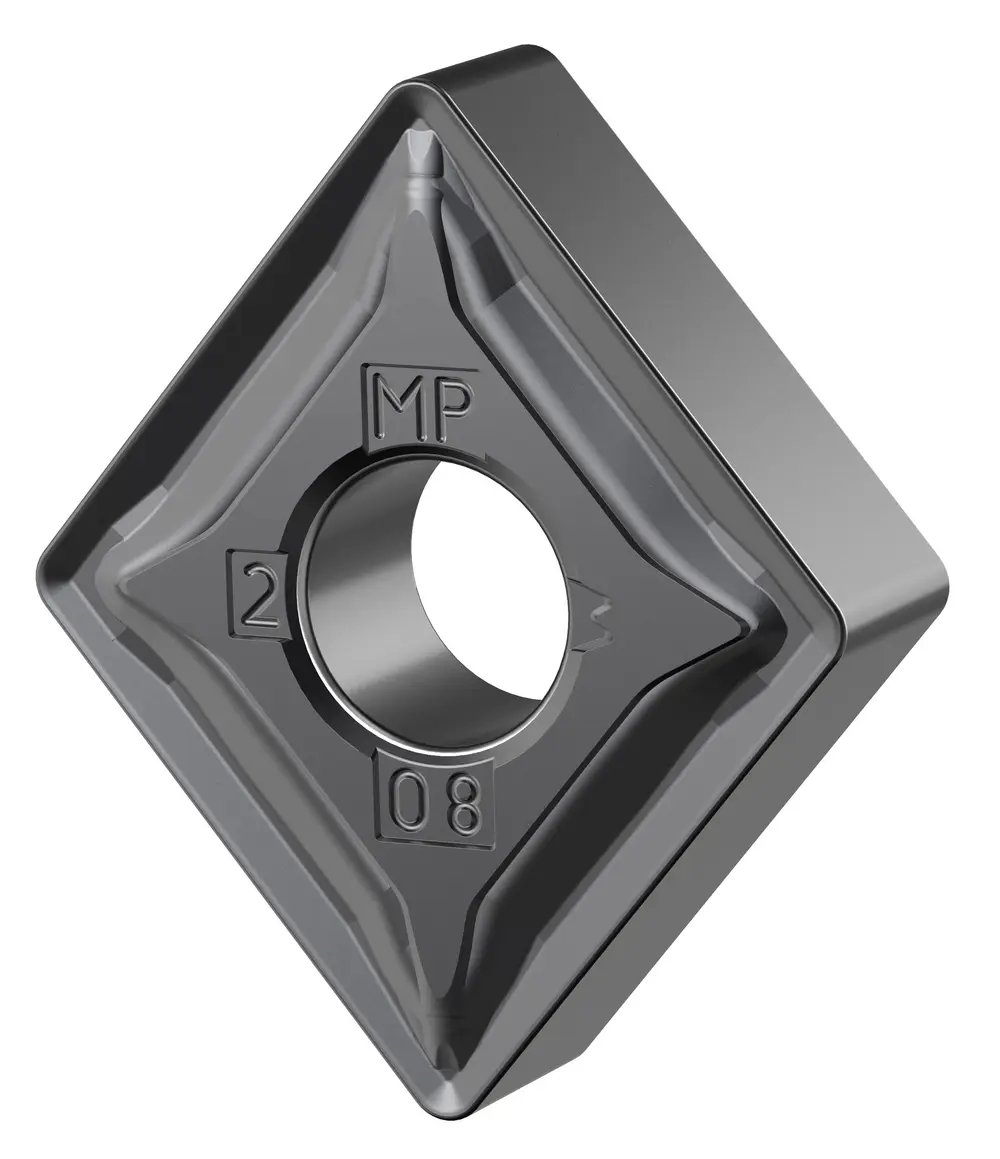
La technologie High-PIMS (pulvérisation magnétron à impulsion haute puissance) permet également d'obtenir des revêtements plus résistants aux températures élevées qui se produisent lors du traitement des superalliages, tels que le titane. Cela permet d'éviter la formation d'une arête de coupe, ce qui entraîne non seulement une réduction de la durée de vie de l'outil, mais aussi une baisse de la productivité. Le revêtement PVD traditionnel peut entraîner des défauts de surface ; un revêtement High-PIMS sera moins sujet à ce type de défaut. Le revêtement appliqué à l'aide de la nouvelle technologie de pulvérisation peut augmenter la durée de vie de la plaquette par un facteur de 2 à 3. Lors de l'usinage de superalliages, cela représente une différence non négligeable à la fois en termes de productivité - en utilisant souvent des vitesses d'avance plus élevées - et de durée de vie des outils.
Entreprises totalement intégrées et impression 3D
Une tendance plus commerciale sur le marché des plaquettes est que certains fabricants choisissent de s'intégrer plus profondément dans la chaîne. Cela concerne, entre autres, la production de métaux durs. D'une part, cela permet aux fabricants de répondre plus rapidement à l'évolution de la demande du marché ; d'autre part, cela leur permet de mieux utiliser les connaissances issues des différentes phases de développement et de production des outils dans l'ensemble de l'entreprise.
Une deuxième évolution observée est qu'après l'impression 3D des fraises à queue et des porte-outils, les fabricants d'outils ont maintenant également produit les premières plaquettes imprimées en 3D. Les essais portent surtout sur des demandes de géométries très spécifiques ou de solutions pour mieux contrôler le liquide de refroidissement. L'impression 3D représente alors parfois la seule solution. L'une des pierres d'achoppement reste la densité du matériau et la prévention des microfissures dans le carbure imprimé. Les fabricants effectuent encore les recherches nécessaires à ce sujet. Pour l'instant, l'impression 3D reste une option intéressante pour la production de prototypes de nouvelles plaquettes et de séries limitées.