Technologie VGA: un nom qui en dit long, ou pas?
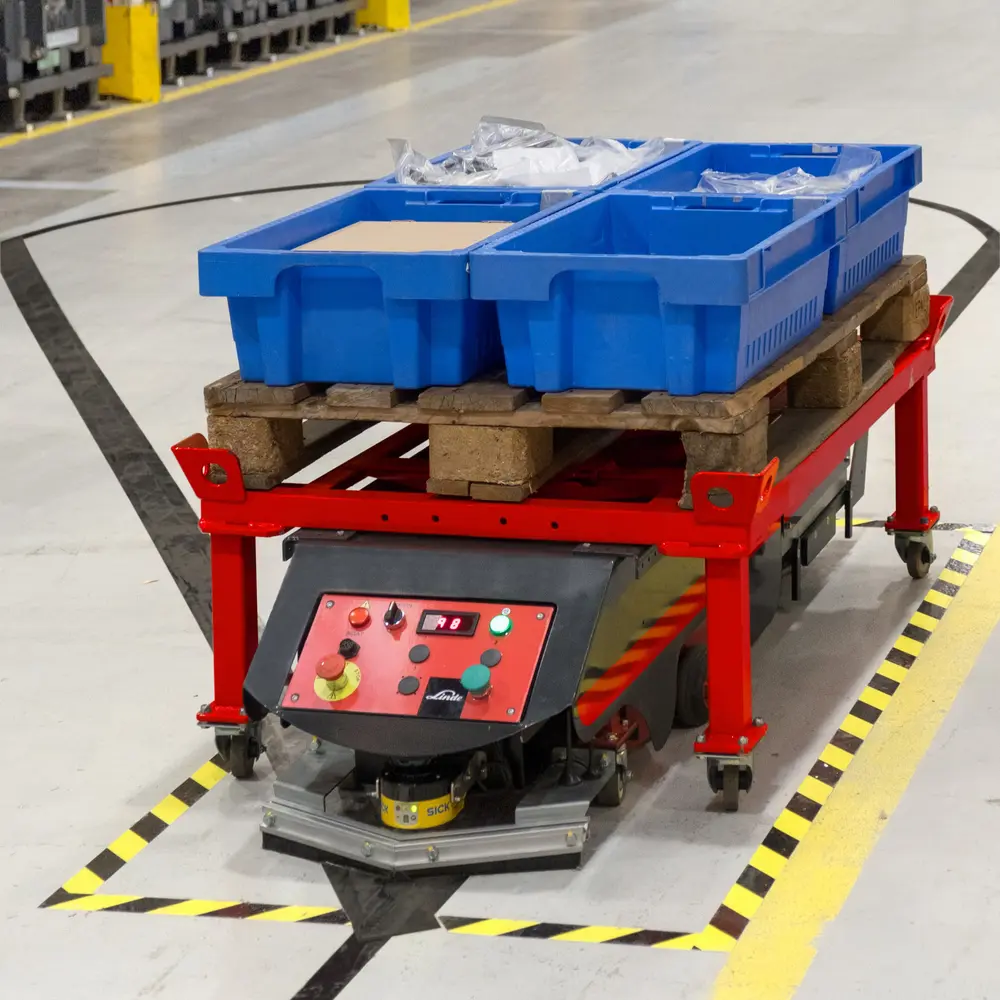
La technologie VGA est devenue une technologie familière que nous voyons fleurir de plus en plus souvent dans les entreprises. Ces dernières années, cependant, nous avons assisté à l'émergence de nombreuses abréviations chez les différents fabricants, parfois spécifiques à un produit, si bien que les utilisateurs ne savent plus toujours clairement de quelle technologie il s'agit exactement: VGA, RMA, SDV, IDV, DTS ... Nous avons rencontré Filiep Vincent de Sirris afin de mettre les choses au clair.
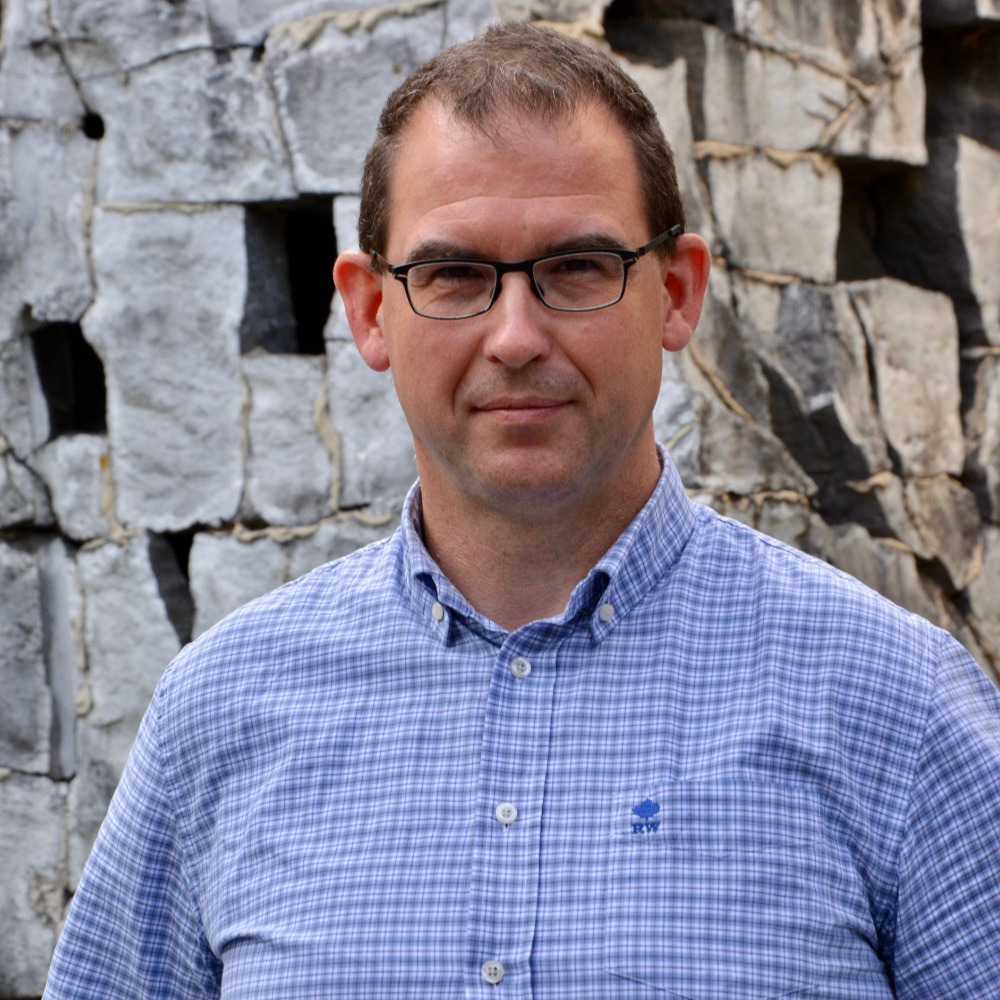
Distinction entre VGA et RMA
"Pour beaucoup, un chariot élévateur automatisé qui transporte des palettes est un VGA", explique Vincent ", tandis que les petites machines caractéristiques sont appelées RMA. Mais la distinction n'est pas toujours claire. Nous pensons que le mode de navigation des véhicules est un facteur de distinction beaucoup plus clair. Il existe plusieurs façons de procéder, chacune ayant ses propres mérites. L'une des premières méthodes pour les VGA - qui remonte aux années 1960 - consistait à faire passer un câble de cuivre dans une tranchée creusée dans le sol, en utilisant le champ magnétique généré pour faire avancer l'appareil. Cette méthode disparaît progressivement. Une autre méthode consiste à utiliser des bandes ou des étiquettes (magnétiques) sur le sol ou un convoyeur à chaîne dans le sol. En particulier la méthode de la bande magnétique que l'on voit encore parfois dans les entreprises. Ces trois méthodes ont une chose en commun: le guidage se fait sur un chemin fixe et prédéterminé. C'est ce qu'on appelle un VGA."
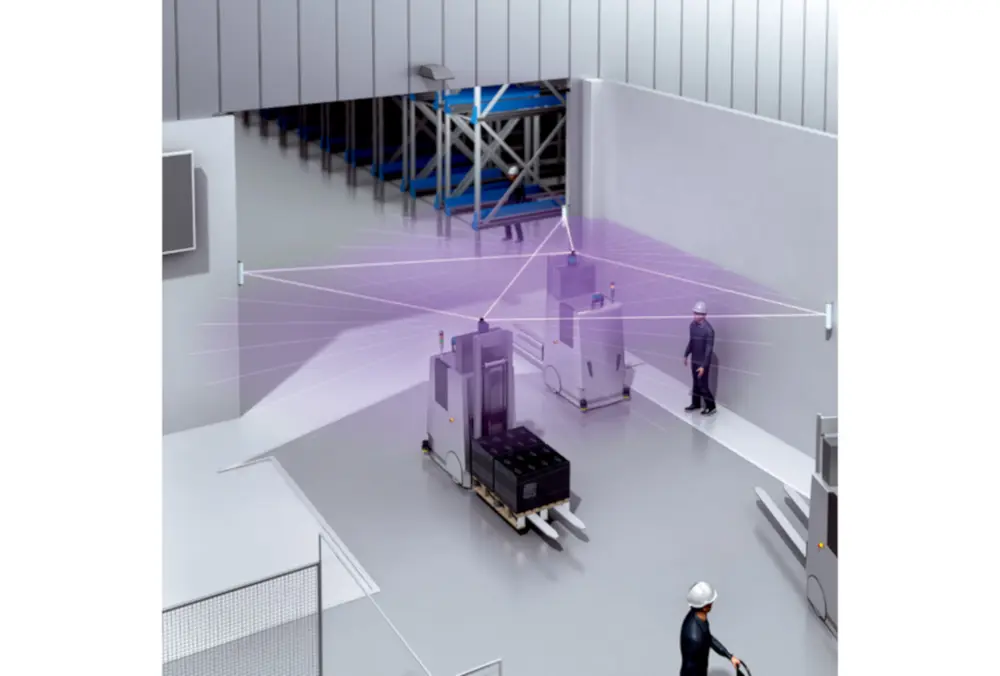
"Dans les RMA, la méthode de navigation est différente, ici les appareils se déplacent sur la base d'une carte interne, mais là aussi il y a plusieurs façons d'y parvenir."
"Les RMA se déplacent sur la base d'une carte interne"
"Une première est basée sur des points de référence fixes: les réflecteurs sont placés sur des entités fixes telles que des murs, des poutres ou des étagères rigides dans l'entreprise. Le RMA est équipé d'un LIDAR qui scanne constamment l'environnement pour trouver les réflecteurs. Si trois réflecteurs sont détectés, l'unité sait exactement où elle se trouve sur la carte qui a été lue. C'est une application très populaire aujourd'hui."
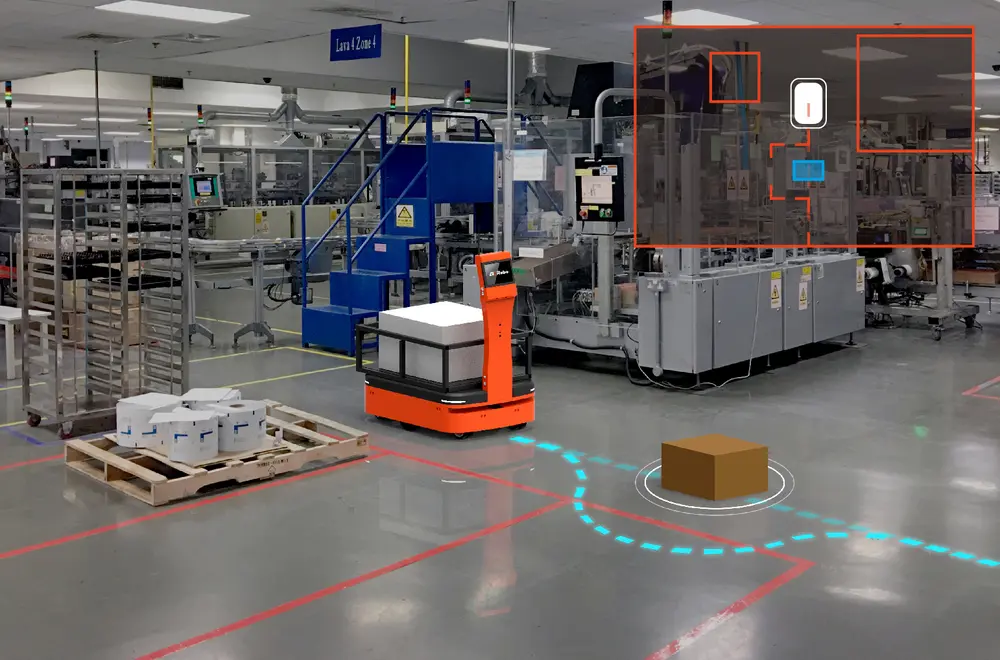
"Une deuxième méthode - qui gagne en popularité aujourd'hui - consiste à travailler avec des points de référence naturels au lieu de réflecteurs. On utilise ici des scanners laser qui sont placés à une hauteur d'environ 20 cm et qui balaient en permanence l'environnement par laser. Les informations provenant de la réflexion permettent au RMA de savoir ce qui se trouve sur son chemin. Mais là aussi, une lecture initiale est nécessaire, au cours de laquelle le RMA apprend à connaître les grandes structures - murs, racks, machines, etc. Ainsi, il peut se déplacer dans cet environnement, mais il peut aussi détecter des obstacles soudains en dehors des structures fixes."
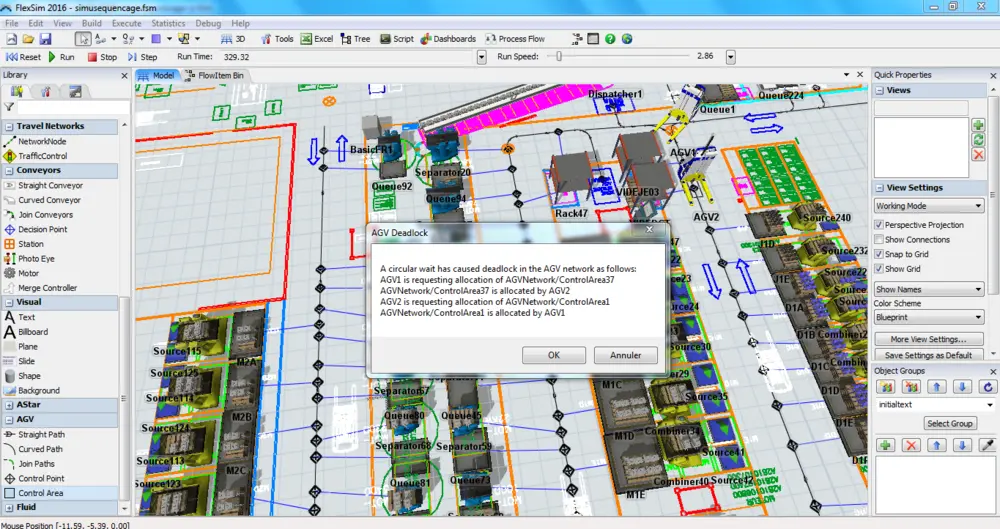
où deux véhicules s'arrêtent pour des raisons de sécurité
"À partir de là, il y a deux façons possibles de travailler: soit avec des zones de sécurité, où la détection d'un objet entraîne d'abord un retard puis, si nécessaire, l'arrêt du RMA. C'est évidemment très bien pour éviter de déplacer des personnes, mais si un travailleur pose une palette sur la voie, l'AMR va évidemment s'immobiliser complètement. Il existe également un risque de 'blocage'. Si deux AMR équipés de scanners de sécurité se croisent, ils détectent la présence de l'autre et ralentissent jusqu'à l'arrêt complet. Cela peut être évité en séparant leurs itinéraires. Dans le cas d'AMR de la même marque, le gestionnaire de flotte - voir ci-dessous - peut en tenir compte, mais ce n'est pas toujours le cas avec des appareils de fabricants différents. Dans la deuxième option, l'AMR calcule automatiquement un itinéraire différent pour éviter un obstacle. Cela nécessite, bien sûr, une certaine puissance de calcul."
Dynamisme et communication
"Nous pouvons être brefs sur la technologie d'entraînement, car elle est relativement simple. Il fonctionne généralement avec 2 roues motrices et 4 roues pivotantes ou à bloc (aux coins) pour la stabilité. Certains appareils peuvent effectuer un virage, mais pas conduire latéralement, alors que d'autres le peuvent. Dans certains cas, cela peut être un avantage, par exemple lorsque l'espace de manœuvre est limité. Un problème plus important est la communication. Le Wi-Fi est généralement utilisé à cette fin, mais il n'est pas toujours très stable dans un environnement industriel. De plus, la couverture doit être de 100% partout, à toute hauteur et dans tous les coins de la zone d'action. Dès que la connexion est perdue, le VGA s'immobilise de manière irréversible, ce qui entraîne une perte d'efficacité dans la production."
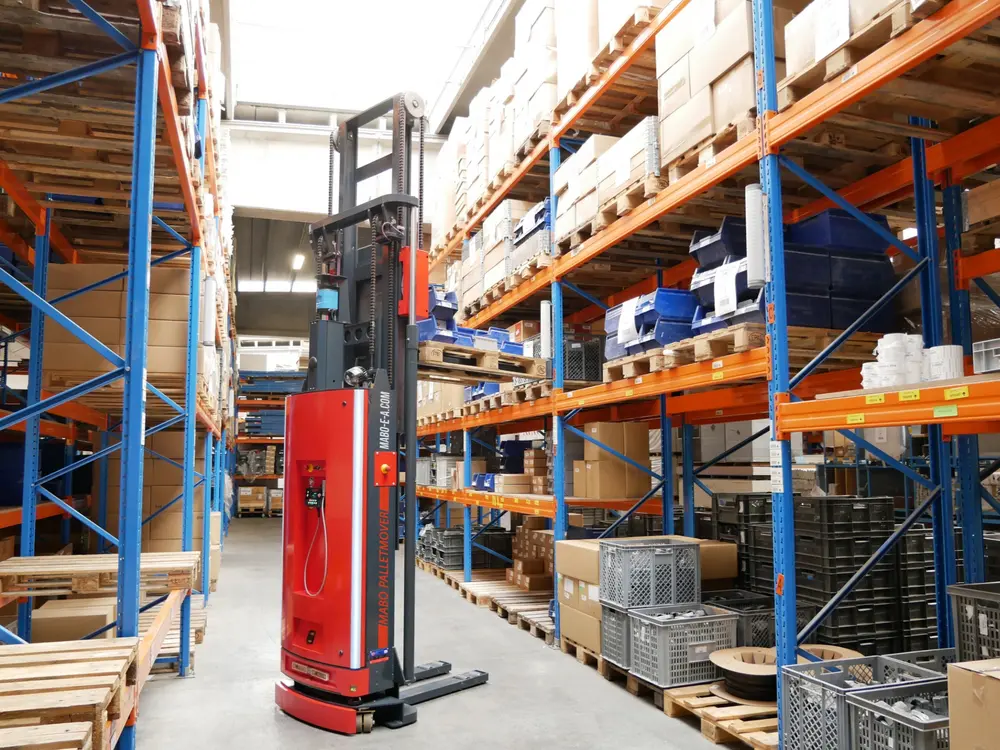
Défis
"Comme défis, je mentionnerais la sécurité - voir l'encadré ci-dessous - et l'intégration des AMR dans la chaîne de production. Chez Sirris, nous venons de terminer un projet pilote intéressant avec la société Altachem, dans lequel les AMR ont été utilisés pour éviter les déplacements inutiles des opérateurs. La combinaison avec les systèmes de cage Karakuri a été réalisée. Cela a abouti à une solution avec 2 types d'AMRs. Le premier transporte des composants de conteneurs en vrac via une construction de tuyaux et de joints sur mesure. Le VGA peut facilement transporter le bac et décharger le produit par gravité, sans aucune manipulation de la part de l'opérateur. L'autre AMR est doté d'un convoyeur à rouleaux motorisé en haut qui retient un paquet de produits, lequel peut ensuite être facilement introduit dans une autre partie du processus."
"En outre, je note certainement aussi le contrôle des différentes marques d'AMR, car elles disposent de leurs propres logiciels et interfaces utilisateur pour créer leur carte et leurs itinéraires. Dans ce cas, tous deux ont utilisé le principe SLAM (Simultaneous Localisation And Mapping), selon lequel les appareils créent leur propre carte en se déplaçant dans leur nouvel environnement. Mais il reste la question de la coordination de leurs communications. En général, un gestionnaire de flotte est utilisé pour contrôler plusieurs appareils, mais ceux-ci sont souvent limités à un seul fabricant. Mais que faire si vous avez besoin de contrôler des appareils de plusieurs fabricants? Nous avons résolu ce problème avec le logiciel Flagstone, qui peut dialoguer avec tous les systèmes via des API Rest. Il s'agit d'un document public fourni par le fabricant, sur la base duquel le logiciel peut obtenir les informations nécessaires sur le contrôle du RMA. À cet égard, l'initiative VDA 5050 mérite également d'être mentionnée, car elle vise à normaliser davantage la communication."
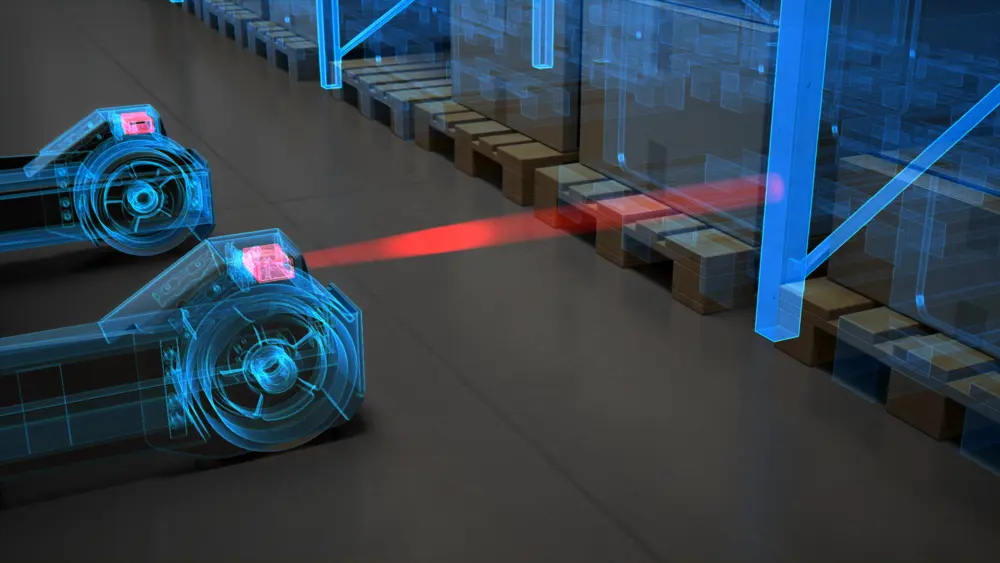
Les conditions environnementales présentent un risque
"En plus de ces défis, je voudrais également mentionner les obstacles spécifiques dans des secteurs tels que l'alimentation. Le transport de marchandises d'une zone de congélation à une température ambiante normale, par exemple, crée un risque de condensation, ce qui n'est pas bon pour les composants. La présence d'humidité n'est pas non plus optimale, tant pour les composants internes que pour le risque de glissement. Les environnements poussiéreux représentent également un défi considérable, par exemple pour l'efficacité du scanner laser. La condensation et la poussière peuvent amener le scanner à penser à tort qu'il est confronté à un obstacle et donc à s'arrêter, alors qu'il ne s'agit en fait que d'une goutte de poussière ou de condensation. La planéité du sol est également très importante. Les sols de l'entreprise ne sont pas toujours de niveau ou présentent des surfaces inégales, ce qui ne permet pas un fonctionnement efficace."
"La condensation et la poussière peuvent amener le scanner
à penser à tort qu'il est confronté à un obstacle"
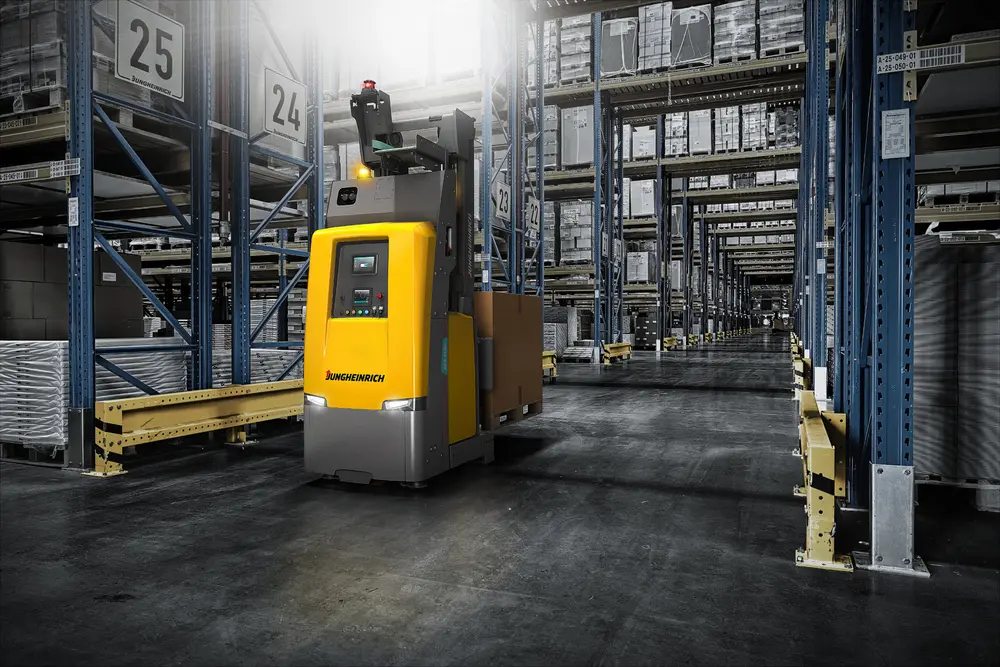
Précision
Les AMR qui se dirigent vers les machines, placent automatiquement leur produit sur la bande et poursuivent ensuite leur voyage vers la nouvelle tâche. Dans quelle mesure peuvent-ils le faire avec précision aujourd'hui?
Vincent: "Avec la technologie actuelle, des outils sont encore nécessaires pour cela. Cela dépend un peu de l'application, mais parfois un marqueur en V est suffisant. Cela permet au RMA de se positionner avec précision. Le reste de l'installation peut également contribuer à améliorer la précision. Par exemple, un robot qui doit décharger/charger le VGA peut être équipé d'un système de caméra avec des marqueurs de référence. De cette façon, l'imprécision du positionnement du VGA peut être compensée, bien que la position du VGA lui-même ne s'améliore pas.
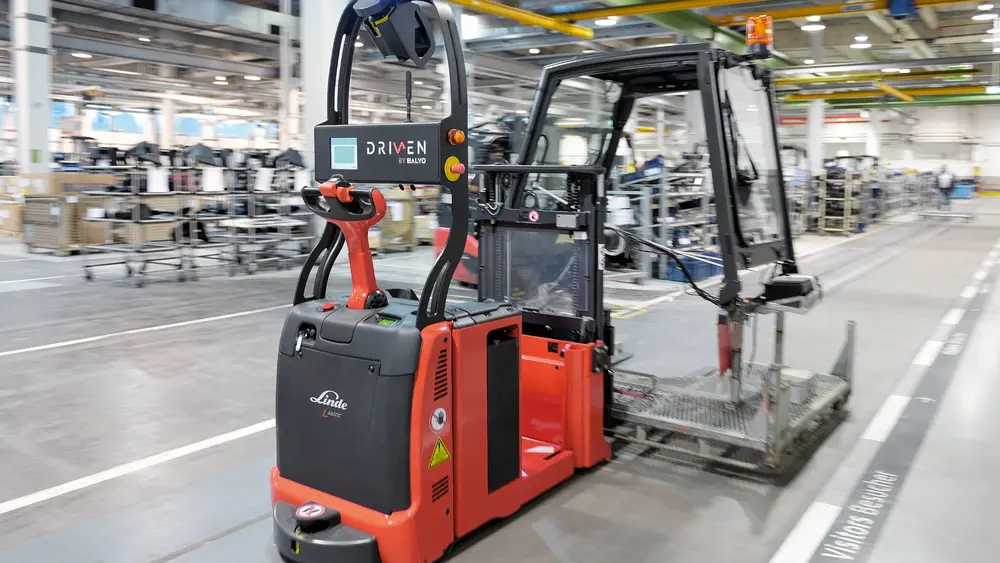
La préparation est cruciale
"Nous pouvons également donner un certain nombre d'éléments auxquels les entreprises se heurtent. Tout d'abord, vérifiez si le flux du produit est correct; c'est la base. Automatiser une structure chaotique est généralement inutile et ne résout aucun problème. Il vaut donc mieux commencer par réduire les mouvements, limiter les distances de transport et rendre le flux de production logique. Vous devez alors vous demander si un VGA est la meilleure solution, car parfois un simple convoyeur à rouleaux peut faire tout aussi bien l'affaire à un prix beaucoup moins élevé. Si vous optez pour un VGA, il reste encore des problèmes opérationnels. Par exemple, il y a beaucoup de différences entre les fabricants en ce qui concerne la facilité d'utilisation et de programmation. Si vous devez faire appel au fournisseur pour chaque petite chose parce que vous ne disposez pas des connaissances techniques nécessaires en interne, le prix augmentera considérablement. En outre, il faut également bien tracer l'itinéraire de conduite, par exemple en estimant l'espace nécessaire pour prendre un virage ou en fixant correctement les références."
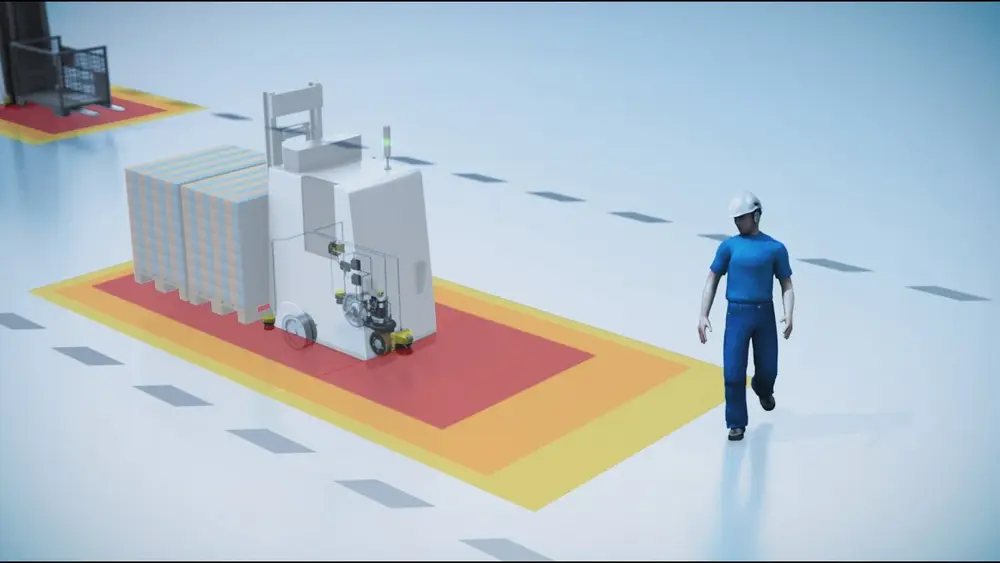
et à la validation des fonctions automatisées des véhicules
NOUVELLES NORMES DE SÉCURITÉ
La popularité croissante des VGA n'a pas échappé aux organismes de normalisation, ce qui est une évolution positive. Jusqu'à récemment, les VGA étaient principalement considérés comme une entité distincte, mais il existe des situations où cela n'est plus tenable. Pensez à un VGA qui ne se contente pas d'appliquer la matière première ou le produit semi-fini, mais qui le place également sur la machine: le VGA devient alors une partie temporaire de la machine, avec une influence associée sur les risques possibles. L'ancienne norme datant déjà de 1997 (EN 1525:1997), il était grand temps de procéder à une mise à jour couvrant à la fois les véhicules guidés sans conducteur (VGA), les robots mobiles autonomes (AMR) et les équipements de transport avec conducteur pour les fonctions automatisées. C'est désormais chose faite avec la norme ISO 3691-4:2020, qui peut être considérée comme la principale norme internationale en matière de VGA. La norme VGA est encore élargie en Europe par l'introduction de la norme EN 1175: 2020, qui couvre certains aspects électriques et les fonctions automatisées des VGA et des chariots de manutention. Cependant, les deux normes attendent encore d'être harmonisées conformément aux directives européennes pertinentes.
Plus précisément, la nouvelle norme ISO 3691-4:2020 étend les exigences relatives aux fonctions de sécurité des VGA et à la validation des fonctions automatisées des véhicules. La norme adopte la méthodologie de conception de la norme EN ISO 13849 et prescrit le niveau de performance requis pour les différentes fonctions de surveillance du véhicule, les modes de fonctionnement et la commande des freins. Il est important de noter que la norme ne s'applique pas seulement au fabricant du VGA, mais qu'elle contient également des exigences pour l'opérateur du VGA. La cible principale est la nécessité d'un zonage approprié du VGA dans son environnement d'installation final. Le zonage doit être conforme au risque résiduel de l'application.
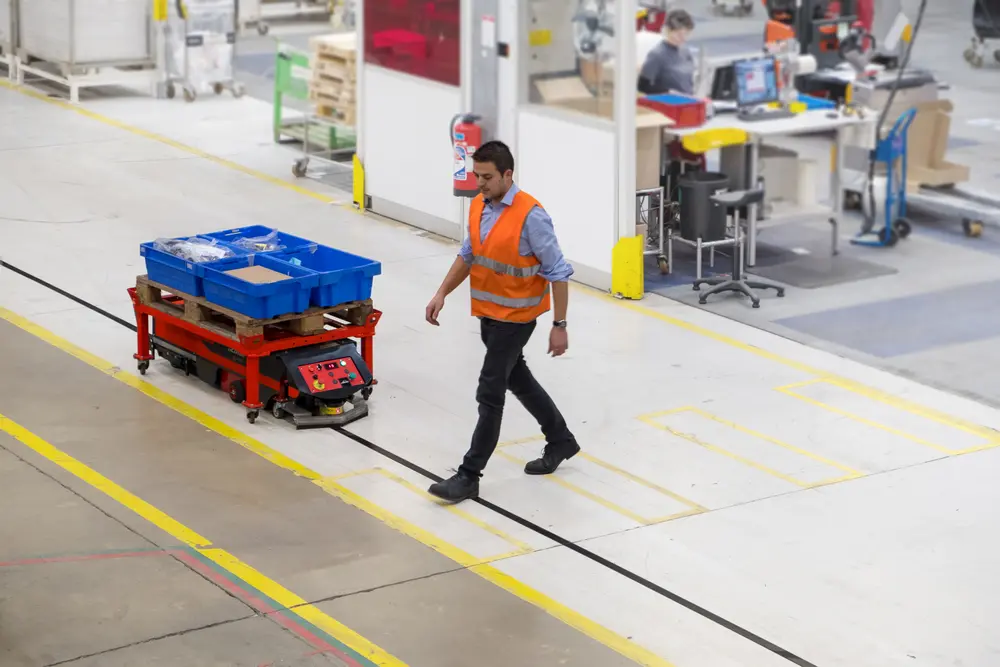