Double récompense pour le fabricant de remorques Stas
Après Tournai, Waregem est aussi une usine du futur
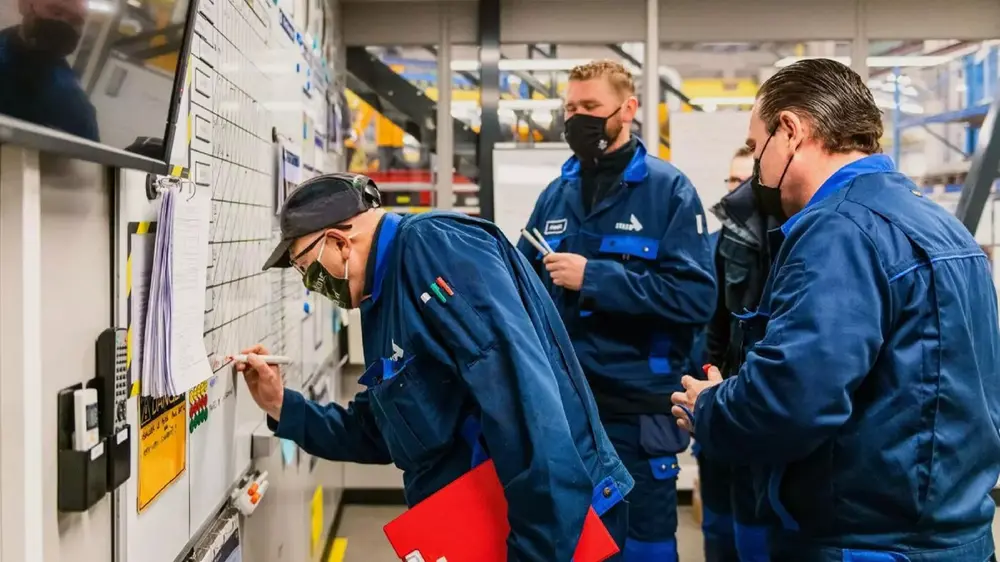
Obtenir le titre d'Usine du Futur est déjà un défi de taille. Mais répéter cet exploit trois ans plus tard est tout aussi impressionnant. Chez Stas, on a estimé que ceci n'était pas encore suffisant, car trois ans après avoir remporté le prix pour le département à Tournai, l'entreprise a également remporté le prix pour le site de Waregem.
Une longue histoire
L'histoire de l'Usine du Futur de Stas sera probablement reconnaissable pour beaucoup, mais commençons par un peu d'histoire.
Depuis 1899
Les premières traces de Stas remontent à 1899, lorsque le maréchal-ferrant Jan Heyse ferrait des chevaux et réparait des roues de charrettes à Aarsele. Avec ses deux fils Urbain et Léon, Jan est ensuite revenu à Stasegem, où l'entreprise a été officiellement créée. Avec l'évolution du cheval et de la charrette vers le transport motorisé, Stas se lance dans la fabrication de remorques. Plus tard, les frères ambitieux ont continué à renouveler leur gamme et ont commencé à produire des véhicules agricoles et les toutes premières semi-remorques.
Dans les années 1960, Willy Heyse et son épouse Lydie prennent la direction de l'entreprise. En 1974, ils déménagent l'entreprise à Waregem, ce qui lui donne l'espace nécessaire pour se développer. Il est important de noter que Stas a déjà commencé à produire des semi-remorques en aluminium à cette époque. De plus, ils diversifient la gamme en produisant également des semi-remorques sur mesure. Les premières étapes de l'intégration de machines automatisées dans le processus de production avaient déjà été franchies.
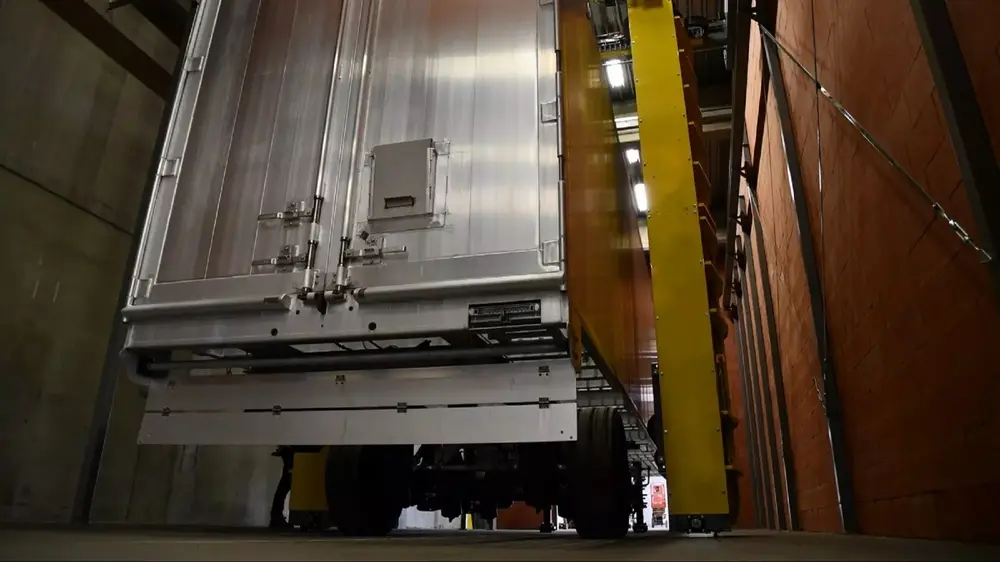
Troisième génération
Une nouvelle référence est apparue dans les années 1990, lorsque leur fils Francis Heyse s'est spécialisé dans les bennes et les semi-remorques à fond mouvant. Le réseau de distribution a été étendu à plus de 40 distributeurs certifiés dans plus de 20 pays européens. L'automatisation a permis d'augmenter considérablement la production, sans pour autant compromettre le savoir-faire et la qualité des produits.
Aujourd'hui, Stas est une entreprise familiale de troisième génération. La production de bennes et de semi-remorques à fond mouvant en acier et en aluminium est actuellement répartie dans quatre usines: Waregem (Belgique), Tournai (Belgique), Freudenberg (Allemagne) et Mediaș (Roumanie). Ces usines emploient plus de 500 salariés et produisent en moyenne 1.800 bennes et 900 semi-remorques à fond mouvant par an. Cela va des petites bennes pour le transport de sable, de gravier et d'asphalte, aux semi-remorques à fond mouvant pour le transport de déchets et de biomasse pour le secteur des énergies renouvelables, en passant par les grandes bennes pour le transport de gros volumes de produits agricoles en vrac.
Premier prix en 2019
Le premier pas vers une Usine du Futur a été fait sur le site de Tournai, qui a été créé en 2001. Après un parcours de deux ans, ils y ont remporté le prix convoité en 2019.
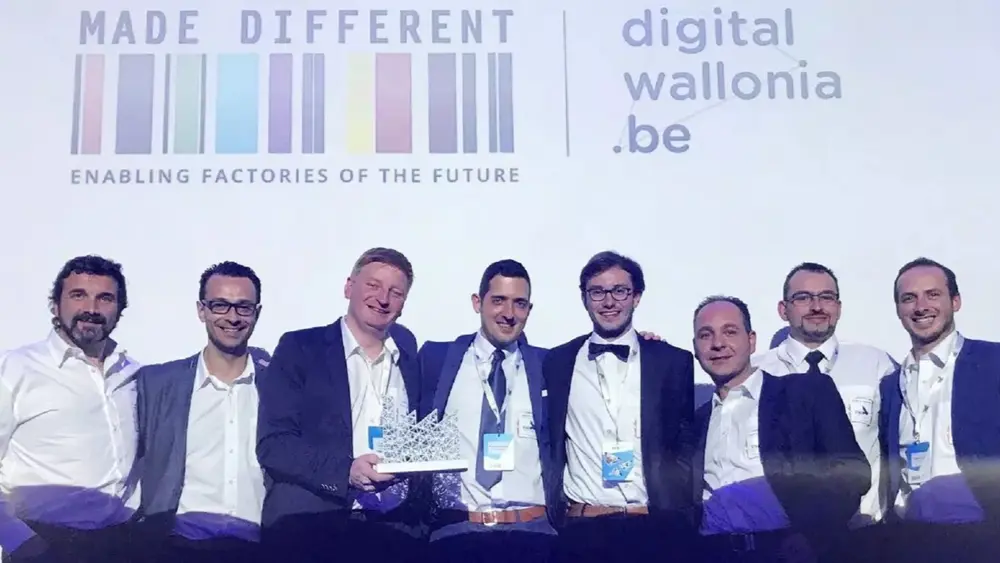
Fabrication intelligente
"Pour les entreprises de production, les défis dans notre pays sont suffisamment connus: coûts de main-d'œuvre élevés par rapport à l'étranger et rareté du personnel. La réponse est souvent recherchée dans une plus grande efficacité: produire moins cher pour rester compétitif. Nous sommes allés plus loin, car le modèle d'entreprise a également été modifié. De l'ingénierie à la commande, nous sommes passés à la configuration à la commande", explique le directeur Pieter-Jan De Man pour justifier leur participation.
"Ainsi, un client peut entièrement personnaliser sa remorque lui-même grâce à un outil de configuration, après quoi la remorque est automatiquement intégrée au processus de production. Cela nécessite non seulement une approche innovante, mais le processus numérique sous-jacent et l'implication du personnel ont également été des fers de lance."
Technologies de fabrication avancées
L'accent mis sur l'innovation se retrouve non seulement dans le produit final, mais aussi dans les différentes étapes de la production. L'automatisation du soudage en est un bon exemple. Au lieu de travailler avec un gabarit de soudage, les robots de soudage mesurent eux-mêmes chaque pièce avant le début du soudage. Cela facilite l'approche de la configuration à la commande et présente le grand avantage d'éliminer le temps de conversion. Chaque semi-remorque à fond mouvant peut donc être traitée à la même vitesse qu'un produit de série, sans travail supplémentaire. Cela permet à l'entreprise de répondre de manière très flexible aux demandes du marché.
"Les employés ont été fortement impliqués dans les trajets dès le début"
Une organisation centrée sur l'homme
L'importance de l'employé dans l'approche de Stas est frappante. "On ne devient pas une Usine du Futur du jour au lendemain. C'est un vaste trajet le long duquel on rencontre parfois des obstacles inattendus. Au cours du premier trajet, nous avons reçu le prix en 2019, mais nous avons commencé à prendre les premières mesures deux ans auparavant. En fait, même avant cela, nous travaillions depuis longtemps sur des projets dans l'esprit de l'Usine du Futur. Nous avons toujours impliqué les employés dans les plans, parce que nous avons réalisé que de telles mesures ne peuvent être prises sans heurts que si les employés sont également sur la même longueur d'onde", déclare Pieter-Jan De Man.
"Au cours du premier trajet, l'accent a été mis sur la numérisation, avec, par exemple, le passage des bons de production sur papier aux bons numériques. Chaque employé reçoit des instructions personnalisées sur la base de la commande du client, et ces tâches sont adaptées à ses propres compétences. Cela permet de simplifier les choses, d'éviter les erreurs et de prévenir les frustrations dans l'atelier. Le logiciel fonctionne également de manière beaucoup plus intuitive que les systèmes ERP traditionnels. Il était important de développer le logiciel de manière à ce qu'il soit très familier aux employés. Enfin, je voudrais souligner l'importance d'une formation approfondie. Nous avons constaté que cette approche était payante. Les employés sont fiers de travailler dans une Usine du Futur, dans laquelle ils apportent eux-mêmes une contribution majeure."
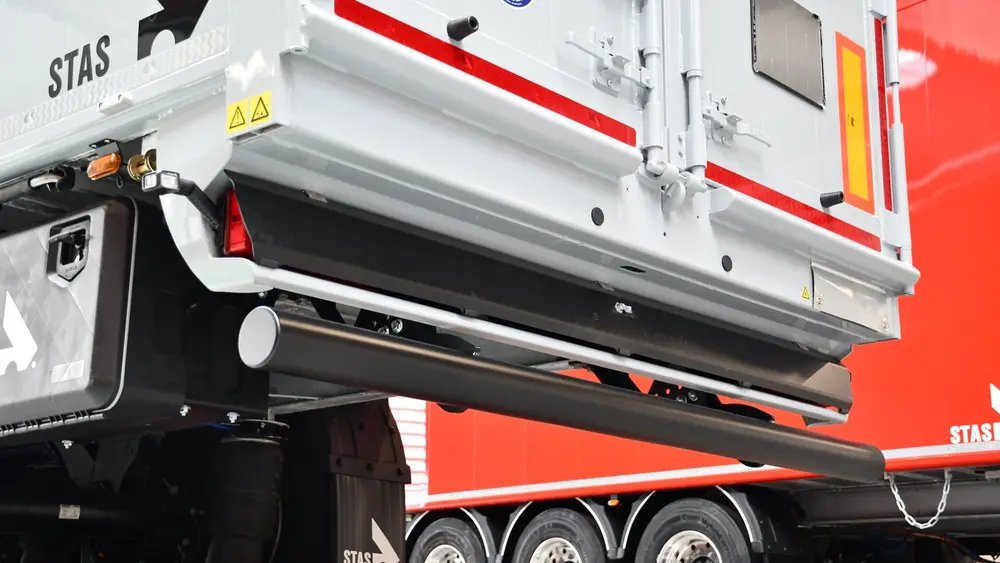
Renouvellement et nouvelle récompense
Pour Stas, il était clair dès le départ que le projet d'Usine du Futur ne se limiterait pas au site de Tournai. Trois ans plus tard, il n'y a pas seulement eu un renouvellement de la certification à Tournai; la division de Waregem peut désormais se qualifier à juste titre d'Usine du Futur.
Les employés au cœur de l'action
À Tournai, le changement le plus important est sans aucun doute l'expansion en profondeur. "Un nouveau bâtiment de 7.000 m2 a été construit, dont le fer de lance est une toute nouvelle chaîne de peinture automatisée pour les semi-remorques à fond mouvant", explique Alexandre Gonçalves Da Silva, ingénieur des procédés. "Par "automatisée", je ne veux pas dire que la ligne a été entièrement robotisée; il s'agit en fait d'une interaction entre les opérateurs et les robots. Les tâches les plus difficiles et les plus lourdes sont effectuées par les robots, tandis que les opérateurs peuvent se concentrer sur les tâches pour lesquelles leur expérience et leurs connaissances peuvent apporter une valeur ajoutée."
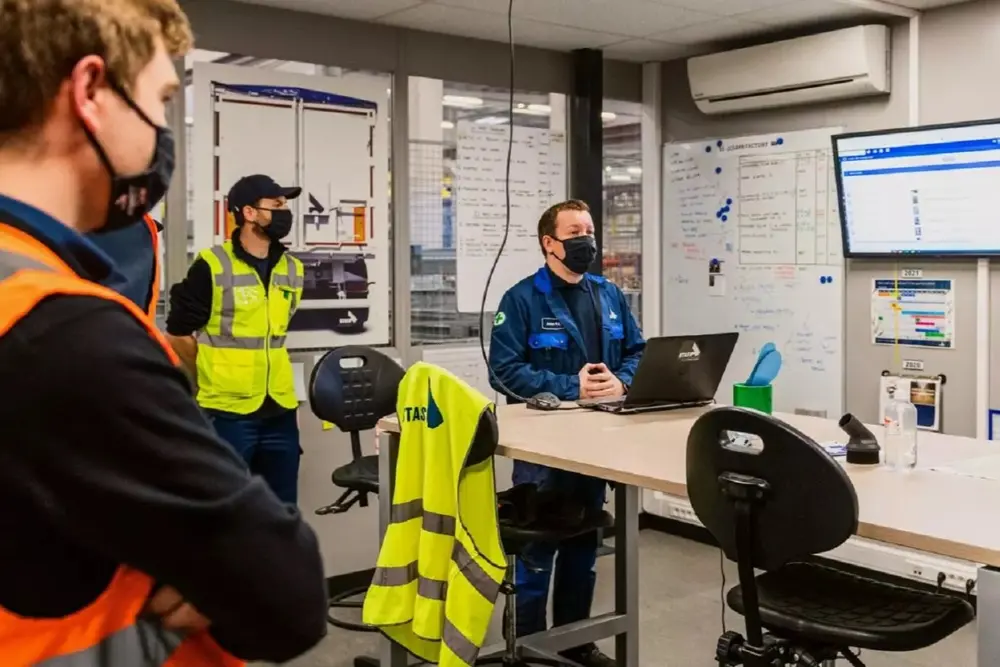
À Waregem, Stas a fait appel aux expériences de Tournai pour remporter également ce prix très convoité. En Flandre occidentale, la priorité a également été donnée aux employés, à la numérisation et à l'automatisation.
"Une nouvelle structure organisationnelle a vu le jour, pour laquelle nous avons mis en place l'équipe Squadron. Elle analyse en permanence les processus de production afin de proposer des améliorations. Il y a les brigades axées sur les produits qui se réunissent tous les jours selon la méthodologie scrum. Par ailleurs, nous travaillons également avec des challengers, qui visent à encourager le développement personnel, et il existe une plateforme de formation", explique Kevin Sablain, ingénieur process.
USINE NUMÉRIQUE
"Parallèlement à l'accent mis sur le personnel, une robotisation poussée a été mise en place afin d'augmenter la capacité de production. Ici aussi, les opérateurs ont été étroitement impliqués, ce qui a donné lieu à de nombreuses idées intéressantes. Celles-ci ont été structurées dans des tableaux d'amélioration, afin que chacun garde toujours le bon objectif à l'esprit. Il y a également eu une optimisation de l'agencement, que nous avons associée à un investissement dans de nouveaux robots de soudage. Cet investissement a également été intégré au réseau d'information. De cette manière, nous avons fait un grand pas en avant pour devenir une entreprise axée sur les données", poursuit Kevin Sablain.
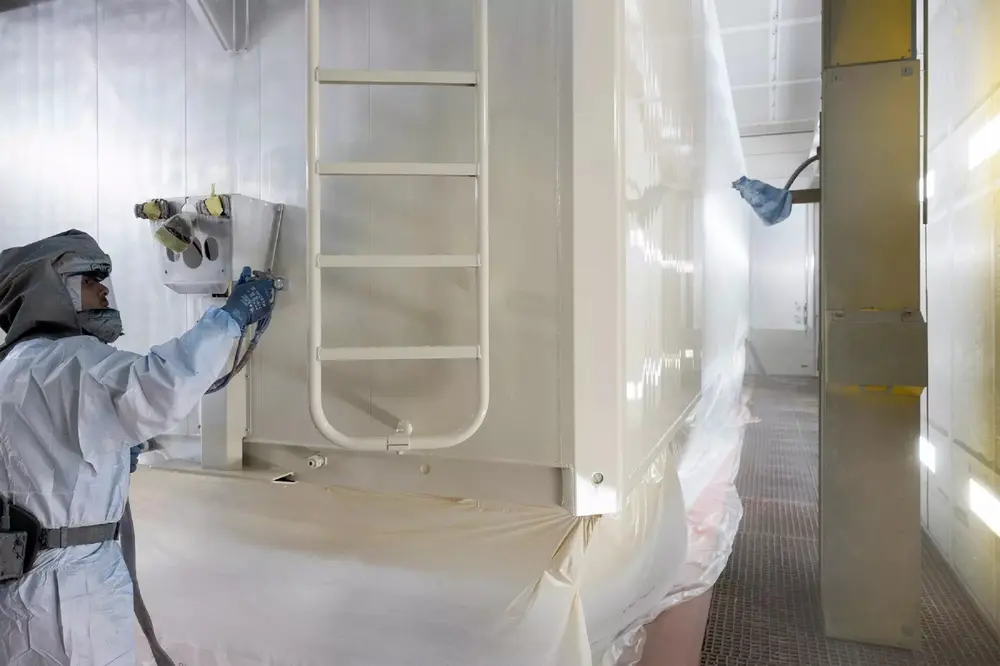

"Par exemple, nous travaillons sur notre propre système ERP – Fusion – pour lequel nous sommes actuellement dans la phase finale. Dans la section des ventes, nos revendeurs peuvent configurer les véhicules et planifier les créneaux disponibles. Lorsqu'une commande est passée dans le système, un certain nombre de choses sont lancées automatiquement: les matériaux nécessaires sont achetés s'ils ne sont pas en stock, les instructions pour la production sont créées et, s'il y a des demandes spéciales, l'équipe d'ingénieurs est impliquée. Ainsi, les commandes ne doivent pas passer par le bureau d'un ingénieur avant d'être mises en production, ce qui réduit les interventions. Les ingénieurs peuvent se concentrer sur les nouveaux développements."
En d'autres termes, Fusion garantit que les bonnes informations ou instructions de travail sont disponibles au bon moment pour les bonnes personnes. "Étant donné le large éventail d'options disponibles, chaque remorque est unique, ce qui signifie que le délai d'exécution est également unique à chaque fois. Grâce à l'algorithme de planification intelligent, nous pouvons en tenir compte et faire en sorte que la production se déroule le mieux possible", ajoute l'ingénieur process.