QUAND FAUT-IL REMPLACER L’OUTIL?
DECELER L’USURE VIA DES TECHNIQUES DE VISION INTELLIGENTES
L’un des principaux pilotes d’un processus d’usinage classique est la situation de l’outil. Chaque outil est conçu pour prester de façon optimale dans une interaction spécifique (matériau de pièce, qualité de finition, opération …). Dès qu’il a usiné tout un temps et commence à s’user, toutefois, ceci ne va plus.
USURE AU NIVEAU MACRO ET MICRO
Diminution
L’usure de l’outil peut être quantifiée de différentes manières. Au niveau macro, on regardera uniquement quelle est la réduction ou quel est le changement de diamètre pendant le processus. On le fait par exemple avec un système de mesure laser. Ces changements sont corrigés dans la base de données afin de rester dans les tolérances. Cependant ceci ne dit rien sur la longévité. Pour cela, on doit analyser l’arête plus en détails.
Usure de l’arête
Pendant l’usinage, on pourra discerner différentes sortes d’usure sur l’arête. L’usure ‘en cas d’usage normal’ est dénommée l’usure frontale. Avec des paramètres moins optimaux – quand on est confronté à des températures trop élevées, un refroidissement trop faible, l’échec du revêtement … –, on peut voir apparaître des phénomènes tels que l’effritement, la formation de déchirures, la déformation plastique ou la formation d’une arête. Ces types d’usure contraignent d’adapter les conditions en vue d’une utilisation la plus économique possible de l’outil; dans le cas d’une usure frontale ordinaire, la durée d’utilisation de l’outil est normale.
Cassure
Un outil ne s’use toutefois pas selon une courbe linéaire. La première usure interviendra un peu plus vite. Puis ceci se stabilise avant d’augmenter à nouveau rapidement vers la fin de la durée de vie. Ceci peut finalement entraîner la cassure d’une dent, voire de toute la fraise. En effet, les forces augmentent sur un outil qui s’émousse parce qu’on pousse plus qu’on ne coupe. Les températures peuvent aussi augmenter. Un tel échec est très néfaste dans la production et peut même entraîner des collisions sur une opération suivante parce que tout le matériau n’a pas été emporté lors de la passe précédente. On voit souvent aussi des traces sur la pièce lors d’une cassure.
Vibration
Un autre problème est l’apparition de phénomènes vibratoires, ce qui peut être renforcé par l’usure croissante. Il est donc extrêmement important pour les utilisateurs de les changer à temps, même si ceci ne peut pas non plus se faire trop tôt, dans l’optique d’une utilisation optimale de l’outil.
QUAND CHANGER L’OUTIL?
La grande question pour les utilisateurs est de savoir quand changer les outils. Les fabricants indiquent des conditions d’usinage (matériaux adéquats, réglages pour une opération précise), mais étant donné que celles-ci ont été établies dans des conditions de laboratoire (et qui divergent quasi toujours des conditions dans la production), ce sont tout au plus des directives.
Chaque outil peut en outre présenter de minimales divergences (par exemple, il peut provenir d’un autre batch de matériau), si bien que la durée de vie peut varier, même si le reste demeure identique. On doit dès lors adopter une certaine méthode de travail dans la production proprement dite. Ceci se fait généralement de deux manières, quoique des variantes et des formes mixtes soient possibles.
Contrôle visuel
Une première méthode consiste à contrôler régulièrement (visuellement) l’état d’un outil, afin de déterminer sur cette base si l’on peut poursuivre le travail ou pas. Ceci exige de bonnes connaissances de la part de chaque opérateur afin de pouvoir bien interpréter et les accessoires requis près de la machine (comme une loupe ou un microscope).
L’avantage de cette méthode est de pouvoir pousser un outil jusqu’à sa limite, à condition de bien le traiter. L’inconvénient est que cette méthode est fastidieuse: primo on devra procéder à des contrôles assez fréquents, secundo une analyse prend vite une minute.
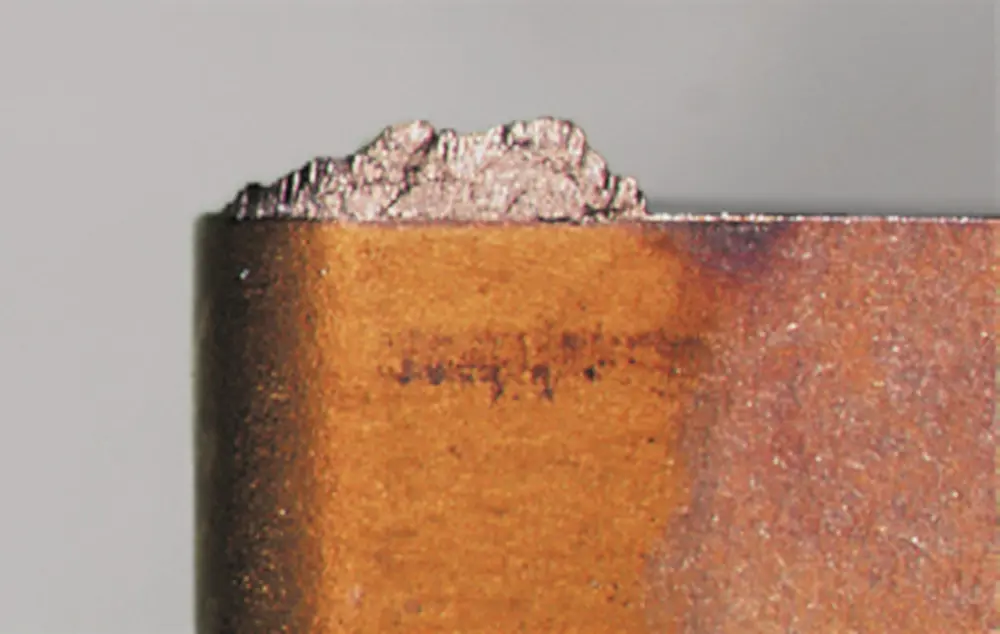
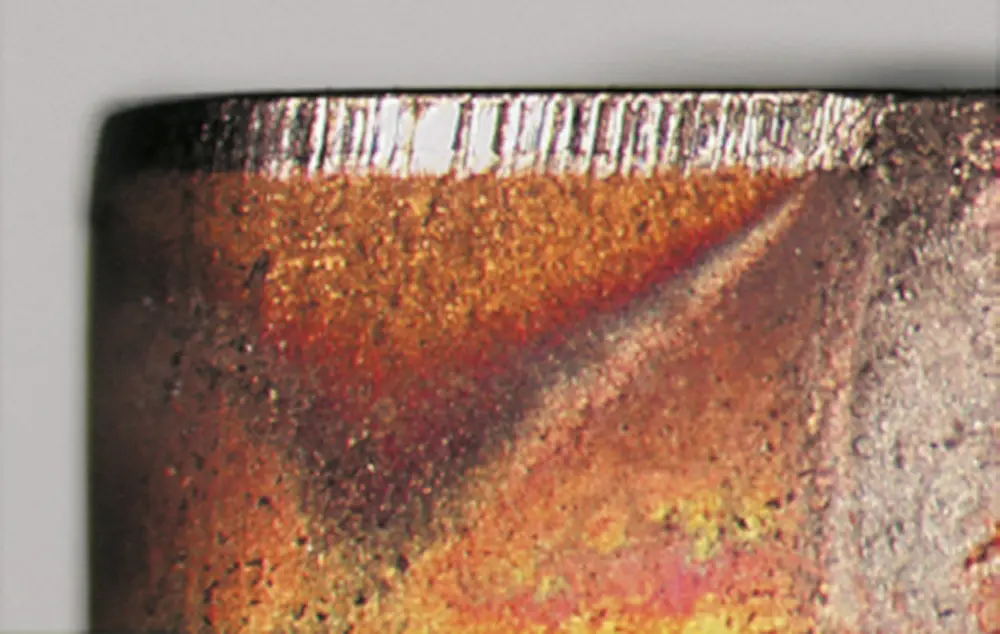
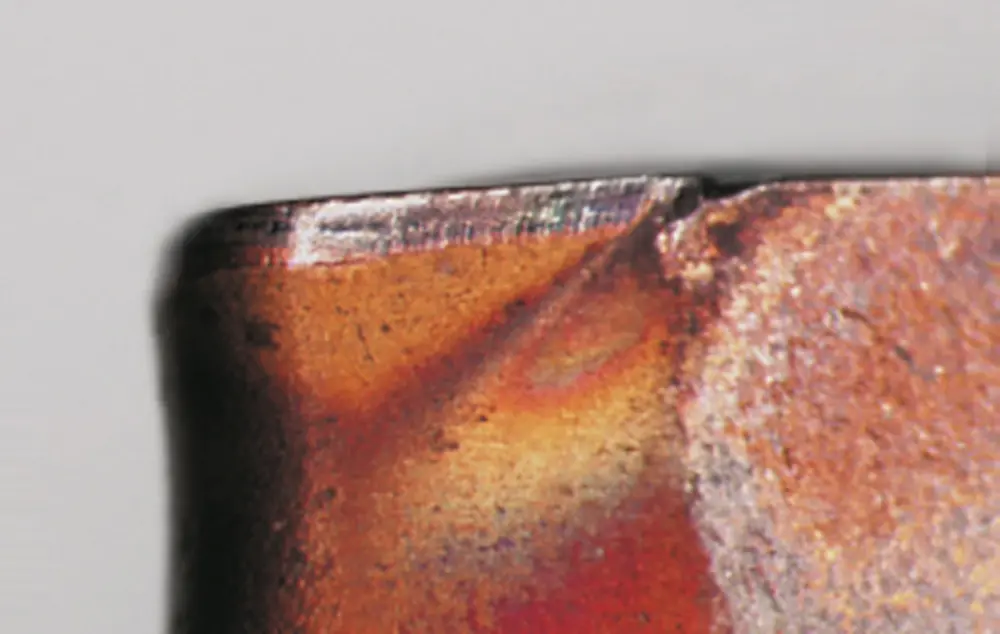
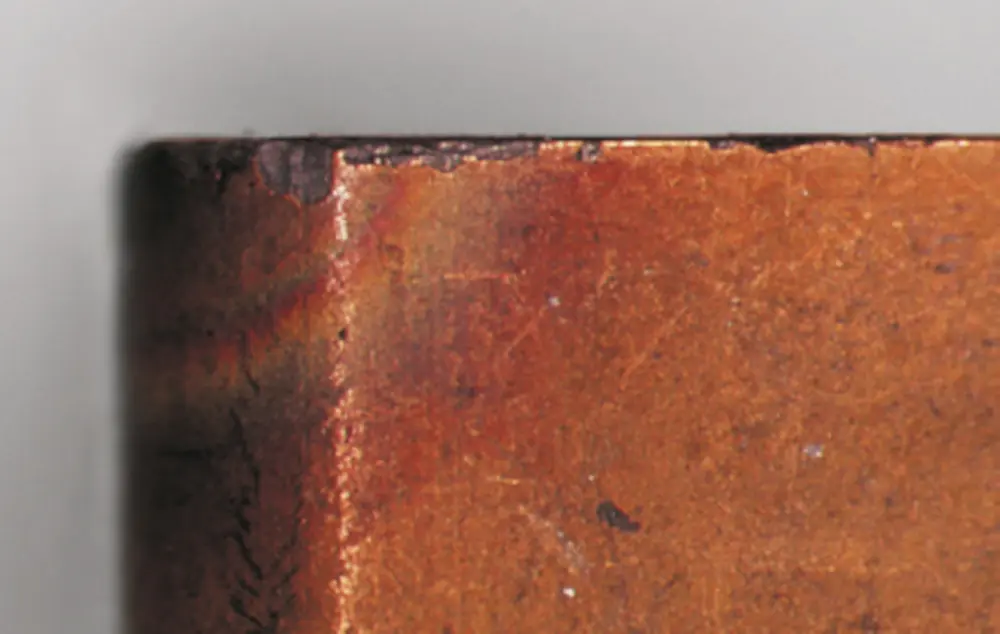
Estimation
Une seconde méthode consiste à faire une estimation grossière de la durée de vie sur base de données historiques. Dans ce cas, on regarde combien de temps un certain outil a pu usiner en moyenne dans le passé et on inclut, selon le cas, une marge de sécurité, puis l’outil est changé automatiquement, quel que soit l’état dans lequel il se trouve à ce moment-là. Bien que l’utilisation de l’outil soit moins efficace, cette méthode de travail peut bel et bien être plus intéressante pour des volumes plus grands et des outils moins chers et/ou pouvant être réaffûtés.
AUTOMATISATION
A l’instar d’autres facettes des processus de production, l’automatisation est aussi un thème qui vit. En effet, on veut connaître l’état d’un outil avec de plus en plus de précision, en temps réel et de façon plus objective, et on examinera de quelles manières ceci est possible. De nombreux développements au sein de l’Industry 4.0 peuvent être d’une grande utilité pour faciliter ce processus d’analyse et de surveillance.
En ce moment, ces solutions sont encore en phase de recherche (académique), mais de récents développements et publications montrent que les avancées sont rapides. La recherche se concentre sur deux pistes: la surveillance directe (inspection visuelle) d’une part et la surveillance indirecte (estimation) d’autre part.
Algorithmes de traitement d’image
Dans les méthodes directes, on utilise des algorithmes de traitement d’image pour déterminer l’usure. Ceci est objectif et précis, et peut être intégré comme étape intermédiaire dans un processus analogue aux mesures laser pour déterminer la longueur ou le diamètre. L’approche classique est ce qu’on appelle l’analyse des pixels. On divise une image (caméra) en pixels ayant une certaine couleur ou valeur de gris et les algorithmes sont rédigés de telle sorte qu’une certaine limite de couleur est définie comme usure. De là, l’algorithme peut extraire divers paramètres (par exemple l’usure maximale, la surface), qui remplacent les mesures microscopiques classiques.
Récemment a encore été publié un travail de recherche (2019, ‘Measurements of Tool Wear Parameters Using Machine Vision System’, A. Thakre, A. Lad, K. Mala) dans lequel un tel algorithme a été rédigé. Sur base d’un système de caméra simple et bon marché (avec éclairage LED), on a pris des images des matrices des outils usés. Les images ont été traitées via un algorithme. L’usure a été déterminée par le biais des valeurs de gris et de différents seuils, et écrite dans Matlab à l’aide d’un script. Puis ceci a été comparé aux analyses via le microscope et a donné un écart moyen d’à peine 3% sur 12 outils.
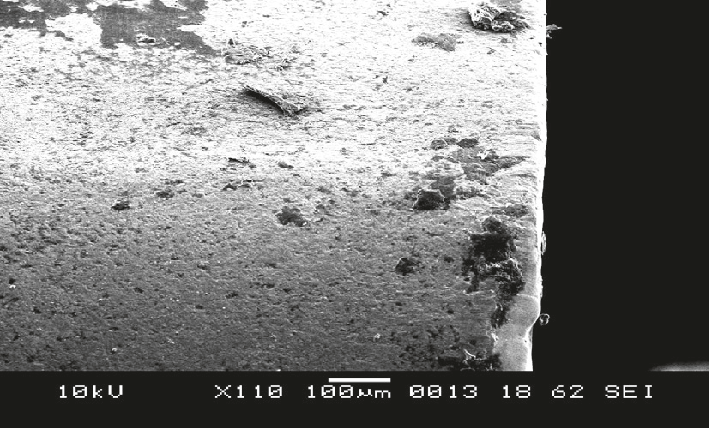
pour prendre des images des matrices des outils usés
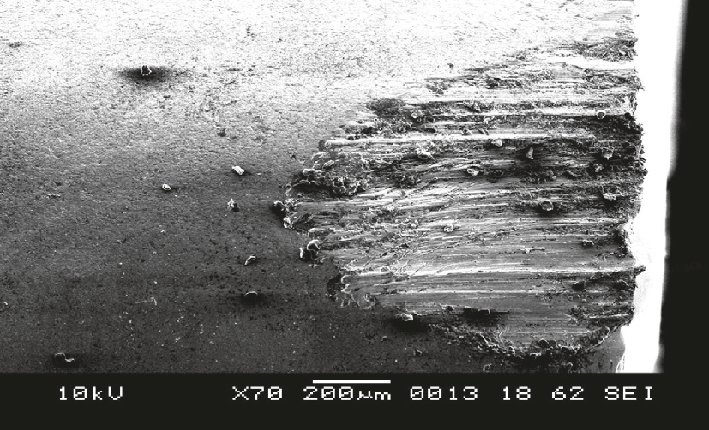
déterminée par le biais des valeurs de gris et de différents seuils,
et écrite dans Matlab à l’aide d’un script.
L’IA pour l’inspection visuelle
Cependant des analyses plus modernes sont possibles, avec l’engagement de l’intelligence artificielle (IA) pour identifier automatiquement ces zones. On utilise souvent le ‘deep learnong’ au sein de la vision, ce qui est un puissant réseau neural pour identifier et classifier les images. De plus en plus de fabricants commercialisent ce genre d’outils, qui permettent à l’utilisateur de configurer lui-même en fonction de sa propre application. On doit fournir à l’algorithme des photos suffisantes de l’usure. Le but final de cette méthode directe sera un système de caméra intégré dans la machine qui peut envoyer les valeurs souhaitées de l’usure sans intervention de l’opérateur. Des stratégies de changement peuvent se baser ci-dessus.
La rédaction de l’algorithme n’est toutefois qu’un seul aspect. Pour implémenter ceci efficacement, plusieurs défis doivent être surmontés, dont le positionnement de l‘outil par rapport à la caméra, la filtration des particules de saleté, le bon éclairage en fonction du matériau de l’outil, et ainsi de suite.
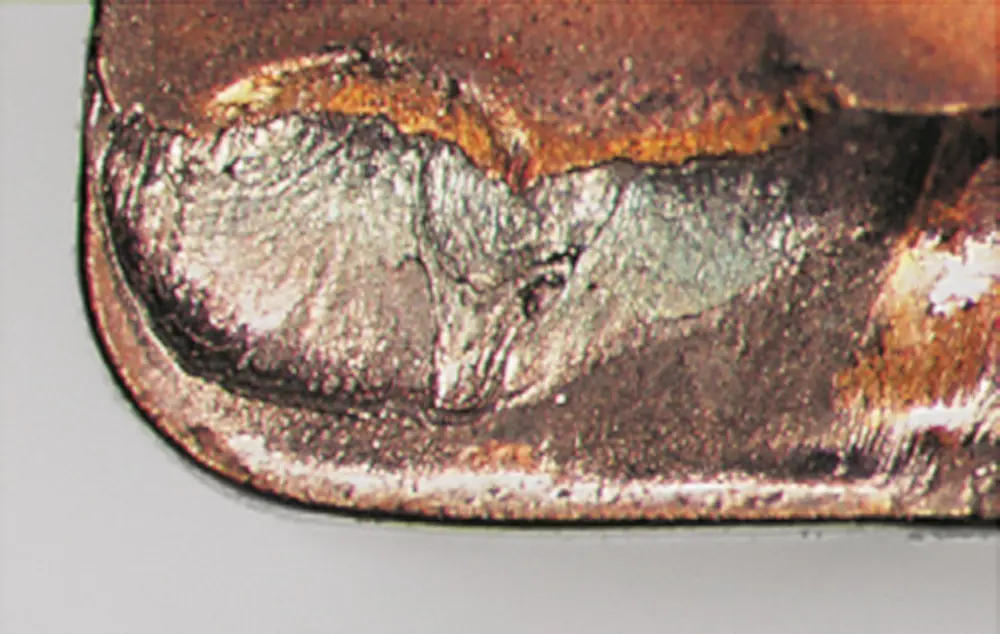
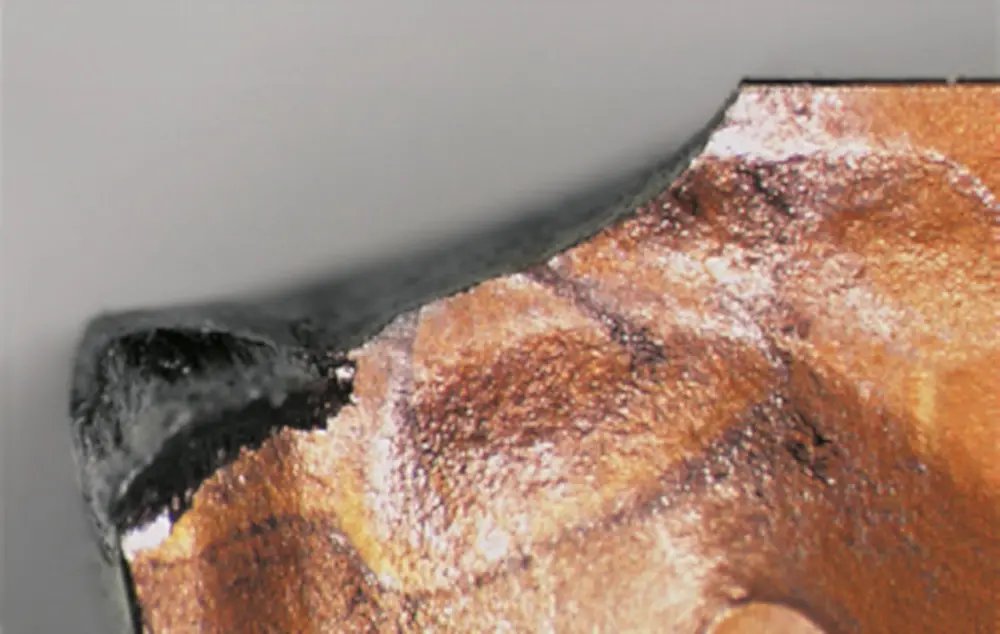
Analyse in-process via des capteurs
La méthode indirecte demande une tout autre approche. On exécutera des mesures pendant le processus via des capteurs dans la machine, ou des capteurs placés en supplément. Ils enregistrent des propriétés physiques qui sont notamment influencées par l’usure de l‘outil. Songez aux accélérations, à l’acoustique, aux forces, à la puissance, à la consommation d’électricité aux températures … Dans cette méthode, il s’agit de corréler ces données avec l’état de l’outil.
Cependant il n’est pas évident d’établir un algorithme générique, si bien que cette méthode est très intensive. En effet, les paramètres dépendent par exemple aussi de la pièce (des variations locales dans une pièce peuvent induire de fausses informations), des conditions ou d’autres propriétés. Une rédaction complète et optimale nécessite donc encore pas mal de travail.
Toutefois ceci est un domaine de recherche qui est suivi depuis déjà très longtemps, avec ces dernières années des résultats sans cesse meilleurs grâce notamment à la progression des data analytics et à des capteurs précis et mieux placés (par exemple captation des données dans l’outil pour se rapprocher au mieux de l’intersection).
La rédaction efficace d’un algorithme nécessite toutefois pas mal de données et c’est un exercice fastidieux. Le grand avantage de cette méthode indirecte est en tout cas la possibilité de réaliser des analyses in-process et d’intervenir au parfait moment, sans perturber le processus (pas de mesure supplémentaire nécessitant l’arrêt de l‘outil). Les résultats actuels se situent en moyenne à +/- 10 à 20 % dans la littérature via des analyses big data. On s’attend à ce que ceci s’améliore encore dans les prochaines années.
EN SAVOIR PLUS?
Chez Sirris, on étudie de façon intensive et en collaboration avec divers partenaires des solutions pour l‘automatisation de la méthode à la fois directe et indirecte.
Les entreprises intéressées peuvent toujours contacter Tom Jacobs via tom.jacobs@sirris.be ou par téléphone au +32 (0)498/91.93.78