L'électro-érosion connaît une seconde jeunesse
La technologie devient plus accessible
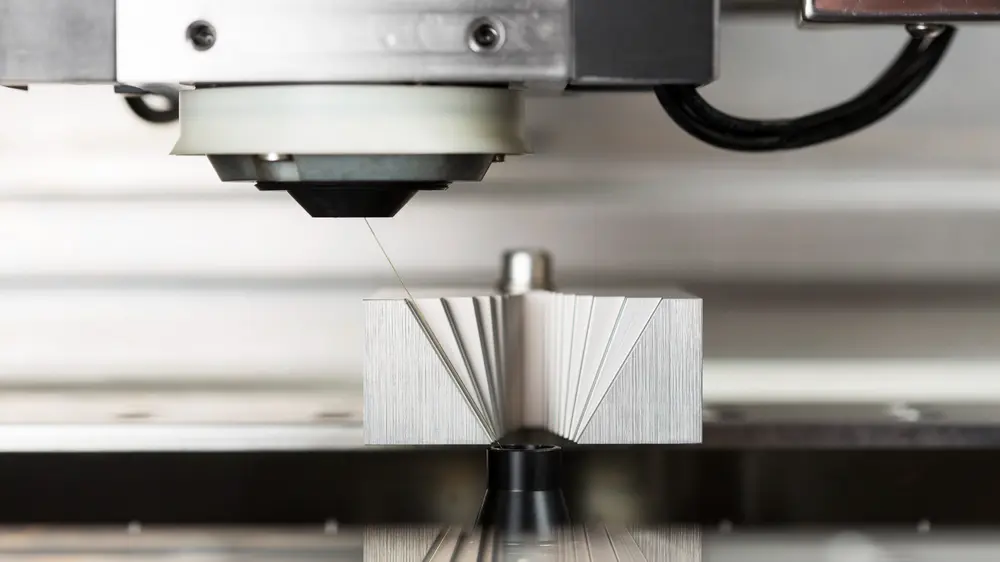
L'électro-érosion à fil et l'électroérosion par enfonçage n'ont jamais totalement disparu. Pendant quelques années, la technologie a peut-être été un peu moins présente à l'esprit des usineurs de précision, mais les développements récents, tant au niveau de la technologie que des précisions exigées par le marché, rendent l'électro-érosion à nouveau d'actualité. Et maintenant, non seulement dans les entreprises qui réalisent des applications d'étincelage traditionnelles, mais aussi dans de nombreuses usines de machines.
Évolution au fil des ans
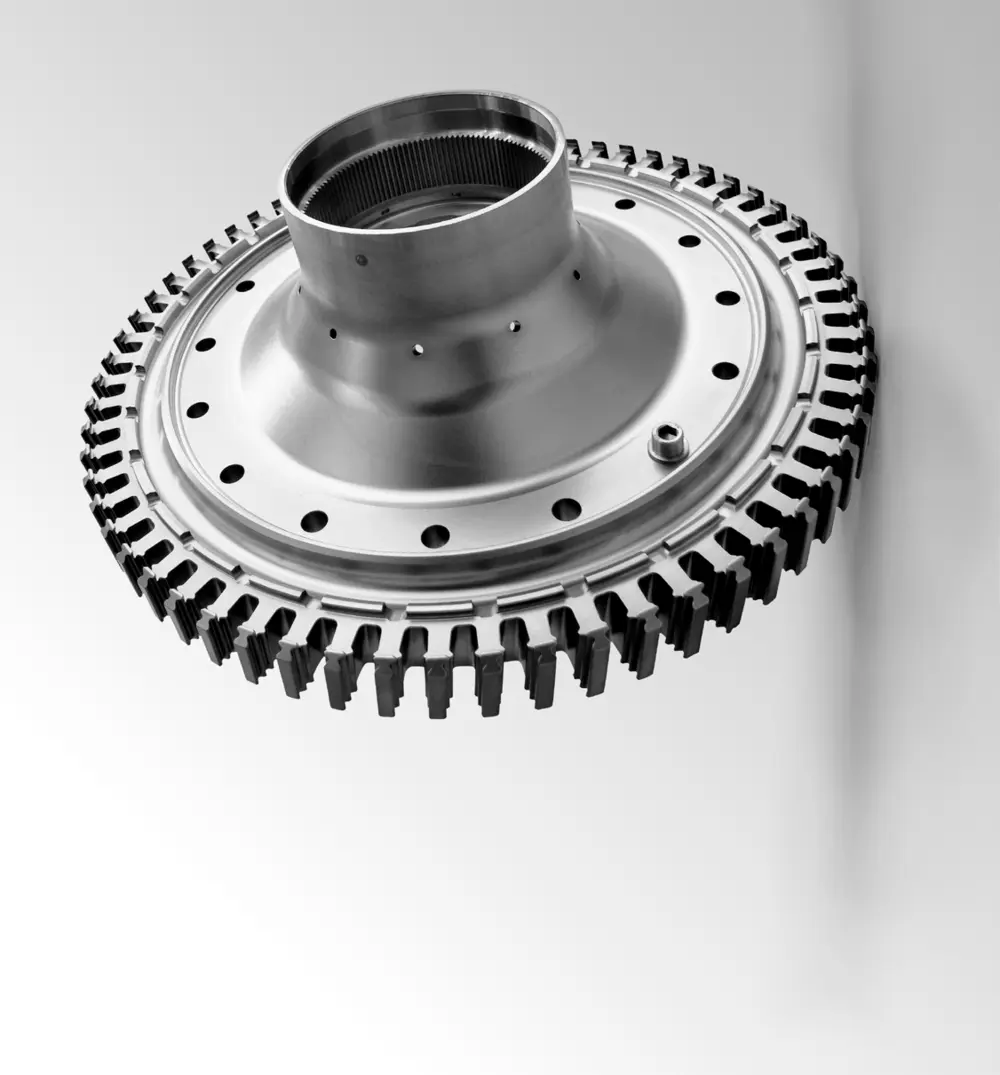
Dans l'usinage par enlèvement de matière, l'électro-érosion est une technologie relativement jeune, qui n'a réellement pénétré l'industrie manufacturière qu'il y a environ 60 ans. Cependant, la découverte que l'on peut enlever du métal avec une étincelle électrique entre deux électrodes remonte à 1770. Mais ce n'est qu'à la fin de la Seconde Guerre mondiale que des chercheurs russes ont découvert que le trempage des électrodes (l'électrode de l'outil et celle de la pièce) dans un diélectrique rendait le processus plus contrôlable.
Ce fut le début du véritable développement de l'électro-érosion par enfonçage (pour le formage 3D), suivi plus tard par l'électro-érosion à fil. Ce n'est qu'à la fin des années 1960 que la technologie est devenue commercialement disponible, le fait de pouvoir usiner le carbure ayant constitué la véritable percée dans les années 1980.
L'un des principaux avantages de cette technologie est qu'elle n'endommage pas la surface de la pièce, car il n'y a pas de contact avec l'électrode de l'outil. Cela permet d'obtenir des précisions de surface élevées.
AVANTAGES par rapport aux autres usinages
Le regain d'intérêt pour l'électro-érosion est également dû à l'utilisation croissante de matériaux difficiles à usiner, à la miniaturisation et à la complexité croissante de nombreux produits, ainsi qu'au fait que les équipementiers fixent des exigences de précision toujours plus élevées. L'électro-érosion par enfonçage, en particulier, offre une grande précision dimensionnelle et formelle car l'électrode n'est soumise à aucune contrainte mécanique.
L'électro-érosion offre une solution pour les matériaux difficiles à usiner
Certaines caractéristiques, comme les très petits rayons internes, ne peuvent être appliquées qu'avec l'électro-érosion par enfonçage. Une autre application judicieuse est la réalisation de dentures spline. Il est vrai que ceci est réalisé à l'aide d'une fraise-mère à un rythme beaucoup plus élevé et donc à un coût moindre par engrenage, mais ces outils sont très coûteux. Cela n'a donc de sens que si une série décente doit être réalisée. Pour les prototypes ou les petites quantités, c'est l'électro-érosion à fil qui l'emporte.
De même, dans certaines applications de meulage, l'électro-érosion par enfonçage peut être une meilleure alternative en termes de coût. La lenteur de l'électro-érosion à fil est donc un concept relatif: ce qui compte, c'est l'application et son coût. L'opération prend beaucoup de temps, mais se fait presque entièrement sans personnel et même automatisée en ce qui concerne l'électro-érosion par enfonçage. Dans l'électro-érosion à fil, les constructeurs de machines étendent l'autonomie en proposant des bobines de fil d'une capacité allant jusqu'à 25 kg, ou une double bobine qui se change automatiquement.

Surmonter l'inconvénient grâce à la technologie laser
Un inconvénient Important de l'électro-érosion est la création de ce que l'on appelle la zone affectée par la chaleur: la couche blanche située sur le bord de la pièce, de quelques microns à quelques centaines de microns (lors de l'ébauche). La chaleur entraîne une modification des propriétés de la couche extérieure de la pièce. Dans ce cas, des microfissures peuvent se former sous la surface et les contraintes peuvent affecter négativement, par exemple, la durée de vie d'un outil fabriqué par électro-érosion.
Les lasers modernes à impulsions ultracourtes permettent de supprimer cette zone affectée par la chaleur, car la très courte durée des impulsions n'entraîne pas de nouvel apport de chaleur. Des études récentes menées par des universités suisses, entre autres, montrent que la durée de vie des outils d'injection, par exemple, est prolongée par l'étape de post-usinage dite d'ablation à froid, par rapport aux outils étincelés sans ce post-usinage. Avec la technologie laser, on peut supprimer localement la zone affectée par la chaleur, si nécessaire.
La concurrence pour EDM?Qu'en est-il des autres techniques, telles que l'ECM et le PECM ((Precision) Electrochemical Machining)? Font-elles concurrence à l'électro-érosion? Il y a dix ans, on disait encore que l'ECM pourrait devenir compétitif par rapport à l'électro-érosion dans les 10 à 15 ans. L'avantage mentionné alors était que les outils ne s'usent pratiquement pas, voire pas du tout. L'inconvénient : il ne s'agit pas encore d'une technologie standard. Pour l'ECM, c'est toujours vrai. Le PECM, quant à lui, commence à gagner du terrain dans le Benelux.
Le PECM est un procédé à froid, sans apport de chaleur dans la pièce. Il s'agit d'un avantage important dans les applications où la zone affectée par la chaleur est indésirable. L'axe Z, sur lequel se trouve l'électrode, se déplace à chaque fois à 10 µm de la pièce et enlève environ 30 nm de matière avec l'impulsion de courant à ce moment-là. Immédiatement après, l'électrode se rétracte (la différence avec l'ECM ordinaire) et est rincée avec de l'électrolyte. Comme l'outil ne touche pas du tout la pièce, aucune usure ne se produit. Les ions métalliques dissous n'ont pas la possibilité d'adhérer à l'outil, car ils sont immédiatement éliminés par l'électrolyte.
La rugosité de surface est généralement meilleure que pour l'élecrtro-érosions ; 2 à 4 µm Ra pour la PECM contre 6 à 8 pour l'EDM.
Pour de nombreuses applications de haute technologie, il est avantageux que la technologie fabrique des produits absolument sans bavures. L'ébarbage est l'un des goulots d'étranglement dans des secteurs tels que les semi-conducteurs et l'industrie médicale, car il s'agit souvent d'une opération manuelle qui suit un processus automatisé. C'est donc là que le PECM l'emporte sur les autres processus. Cette technologie est toutefois mieux adaptée à la production en série, en raison de l'investissement dans l'outillage.
L'entraînement détermine la précision
La précision d'une machine d'électro-érosion à fil ou à enfonçage provient en grande partie du système d'entraînement. Les entraînements sans frottement constituent le point de départ, mais à l'intérieur de ceux-ci, les constructeurs de machines choisissent leurs propres solutions.
En fait, on voit toujours des moteurs linéaires. Mitsubishi Electric applique son propre système breveté: Tubular direct drive, une variante de l'entraînement linéaire. La différence est que le concept Tubular direct drive ne ressent aucune résistance lors de la transition entre le pôle nord et le pôle sud.
La commande reste le moteur de l'innovation
Si un stator et un robot tournent lentement, cela peut provoquer une vibration lors du changement de direction, qui est visible à la surface de la pièce. Mitsubishi résout ce problème avec une technologie dérivée du secteur médical, comme les scanners IRM. Le constructeur de machines utilise des aimants à disque non ferreux entourés d'un tube (d'où le nom de Tubular).Le moteur se déplace par-dessus. Sur toute sa longueur, cela donne une précision de positionnement de 2 µm.
Le fabricant japonais Sodick utilise un nouveau type de guide dans les machines d'électro-érosion à fil les plus précises. Dans ces derniers, les billes ont été remplacées par de petits barils, de sorte qu'il n'y a plus de charge ponctuelle. La plus grande surface augmente la rigidité du guide. Cette amélioration, ainsi qu'un certain nombre d'autres, permet de doubler la précision du pas de la machine, par rapport à l'électro-érosion à fil standard de Sodick.
La technologie devient plus accessible
Pendant longtemps, l'électro-érosion était une technologie de niche qui nécessitait de nombreuses connaissances spécifiques de la part de l'opérateur. L'électro-érosion à fil et l'électro-érosion par enfonçage ne sont pas encore aussi répandues que le fraisage et le tournage CNC, mais les constructeurs de machines ont fait beaucoup au cours de la dernière décennie pour rendre cette technologie plus accessible.
Le fil conducteur est la numérisation et l'utilisation croissante des algorithmes d'apprentissage automatique. Cela permet aux fabricants d'intégrer des bases de données de matériaux, dans lesquelles l'opérateur peut déjà trouver de nombreux paramètres pré-validés. Les paramètres des matériaux à hautes performances tels que le titane et certains alliages de cuivre sont également disponibles via la base de données en quelques clics lors de la programmation.
Intelligence artificielle
L'intelligence artificielle, à commencer par l'apprentissage automatique, est la prochaine étape. Les nouvelles commandes 'apprennent' de chaque usinage et utilisent ces données pour le suivant. L'utilisation d'une machine d'électro-érosion est ainsi facilitée et les fabricants parviennent à abaisser le seuil d'entrée. Les contrôleurs les plus récents surveillent en permanence ce qui se passe dans le processus, détectant tout problème à un stade précoce et ajustant automatiquement les paramètres du processus.
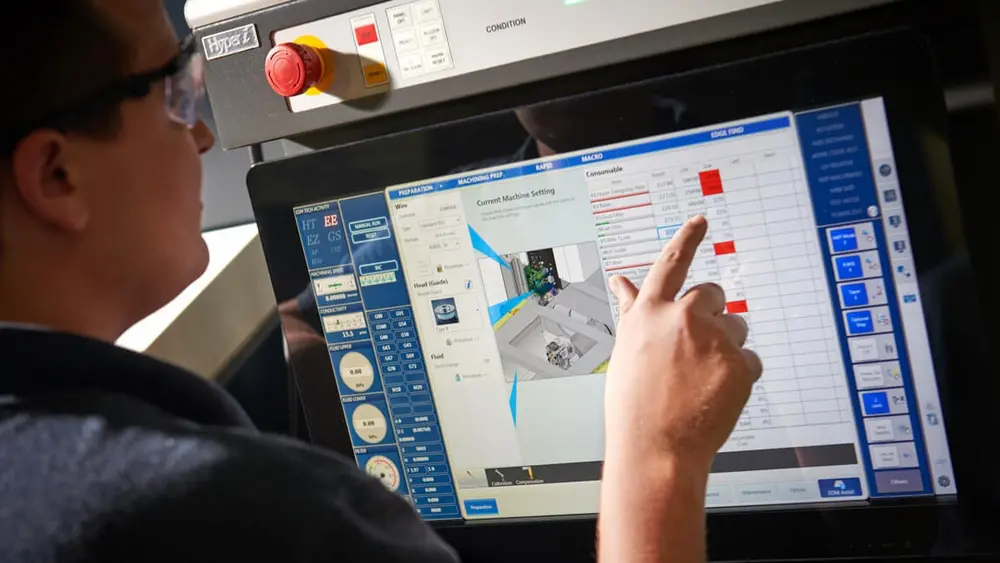
Par ailleurs, les constructeurs de machines parviennent à réduire l'usure des électrodes grâce aux algorithmes. Les générateurs les plus récents réagissent beaucoup plus rapidement à ce qui se passe dans le processus, grâce aux informations que la commande extrait des données.
Industrie aéronautique
L'un des nouveaux développements permettant d'augmenter la vitesse des machines d'électro-érosion à fil est la technologie à double fil. C'est ce que propose GF Machining Solutions sur la nouvelle série CUT X: en plus d'une bobine avec du fil plus épais, il y a également une bobine avec du fil fin sur la machine.
En fonction de l'usinage - enlèvement d'une grande quantité de matériau en peu de temps ou étincelage plus lent mais très précis - l'un des deux types de fil est sélectionné dans le programme. Cela évite à l'opérateur de devoir changer de fil lorsqu'il passe de l'ébauche à la finition.
Cette technologie peut également être utilisée pour étendre l'autonomie du système en travaillant avec deux fils identiques. Comme la machine change automatiquement lorsqu'une bobine est vide, l'autonomie est doublée.
Fil tournant
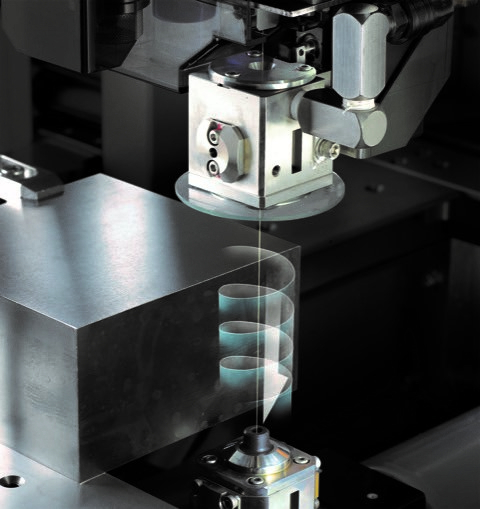
Même après des années, il est toujours possible d'innover dans le processus d'électro-érosion à fil. Le contrôleur reste le moteur de l'innovation.
Jusqu'à présent, le fil dans une électro-érosion à fil est contrôlé par la tension et la vitesse de défilement, tandis qu'il est contenu par une matrice dans le guide. En ajoutant un mécanisme de rotation au fil, la fonction iGroove de Sodick augmente à la fois la précision géométrique et la qualité de surface.
Le fil tourne autour de son propre axe pendant le mouvement descendant. Par conséquent, la pièce est toujours usinée avec la surface neuve et non utilisée du fil, ce qui garantit une meilleure qualité, en plus d'une consommation de fil réduite. Le risque de rupture diminue également, car la surface avec laquelle le fil travaille la pièce ne s'use pas en un seul endroit en raison de la rotation, mais de manière très régulière. La nécessité de compenser une paroi conique est éliminée.