Évolution des centres d'usinage 5 axes
La précision comme fondement
Le fraisage 5 axes est devenu une technologie de pointe dans de nombreuses entreprises d'usinage. Les avantages de l'usinage à cinq axes (sur des machines 3+2) sont bien connus et largement acceptés. Le fraisage simultané sur 5 axes, en revanche, reste une opération plutôt rare. En outre, les différences de prix entre les centres d'usinage à 5 axes sont importantes, ce qui n'est pas sans raison. La stabilité a son prix. Du coup: sommes-nous en train d'assister à une tendance au downsizing des machines à 5 axes?
Construction et matériaux
Les centres d'usinage à 5 axes sont presque devenus monnaie courante. On trouve aujourd'hui cette technologie non seulement dans les marques haut de gamme, mais aussi dans toute la gamme des machines CNC, depuis les modèles d'entrée de gamme jusqu'aux modèles les plus récents. La structure d'un centre d'usinage à 5 axes peut varier considérablement d'un type à l'autre, et nous ne parlons pas seulement du fait que les axes supplémentaires se trouvent dans la tête de fraisage ou dans la pièce à usiner.
Béton polymère pour le bâti de la machine
Une distinction importante peut être trouvée, par exemple, dans la base des machines CNC. Outre la fabrication de colonnes monoblocs pour une plus grande stabilité au lieu d'une extension libre pour un axe Z plus élevé, et l'utilisation de poutres plus épaisses pour une structure plus rigide, certains fabricants optent pour une base en béton polymère. Il s'agit de matériaux composites: ils sont constitués d'un mélange de composants minéraux, tels que le sable de quartz et les agrégats, et de résine polymère.
Le grand avantage du béton polymère est qu'il est moins sensible à la chaleur qui peut s'accumuler à l'intérieur de la machine. C'est pourquoi il est aujourd'hui sous les feux de la rampe, car la production sans personnel impose des exigences élevées en matière de stabilité thermique de la machine. Le coefficient de dilatation du béton polymère est inférieur à celui de la fonte et de l'acier. Pour la fonte, il est d'environ 11,8 x 10-6 par degré Celsius, tandis que le coefficient de dilatation de l'acier varie entre 10,8 x 10-6 et 13,2 x 10-6 par degré Celsius, selon le type d'acier. Le béton polymère, quant à lui, a un coefficient de dilatation d'environ 5 x 10-6 par degré Celsius, soit moins de la moitié.
Cela signifie qu'il se dilate moins avec les fluctuations de température, ce qui contribue à maintenir la précision du fonctionnement de la machine. En outre, le béton polymère amortit plus efficacement les vibrations et constitue un matériau plus rigide, bien que la taille et le matériau à usiner influent également sur cette précision. Le Fraunhofer Institut für Produktionstechnik und Automatisierung, en Allemagne, a constaté une amélioration de la précision d'environ 50% par rapport à un banc de machine en fonte in situ.
Le béton polymère est plus cher que les autres matériaux utilisés par les constructeurs de machines, mais il est plus rapide à mettre en œuvre dans la production. Son principal inconvénient est qu'il est susceptible de se briser. Il est vrai que cet inconvénient l'emporte sur les avantages qu'il présente pour les machines de précision. Néanmoins, sa part de marché dans la construction mécanique est encore relativement faible, puisqu'elle est estimée à environ 20%. Toutefois, cette part augmente au fur et à mesure que les avantages du matériau sont mieux connus et que la technologie se développe.
Le carbone dans l'ingénierie mécanique
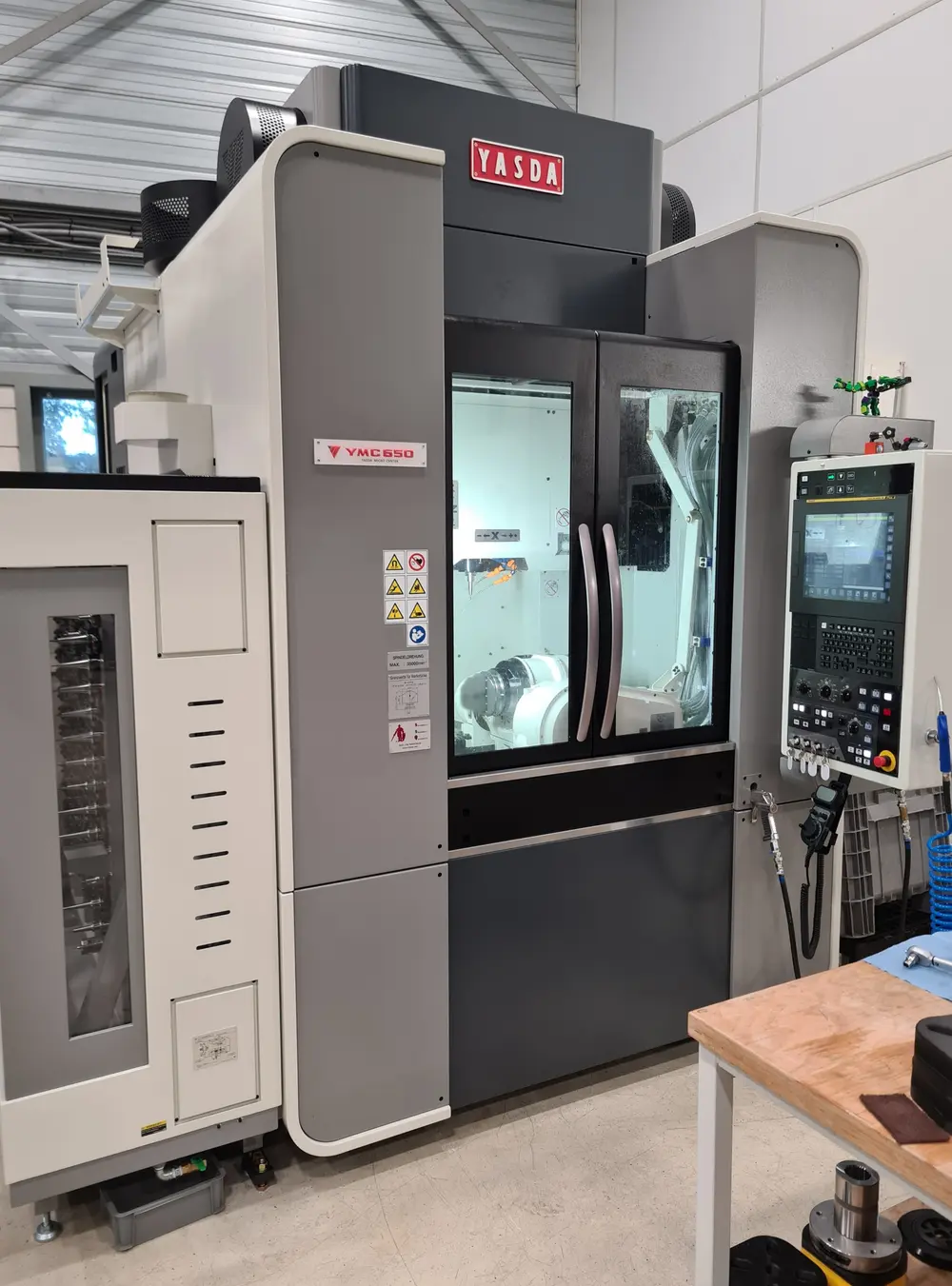
Un matériau que l'on trouve rarement dans les machines à commande numérique est le composite, par exemple le carbone. Chez quelques constructeurs de machines, on voit parfois ce matériau dans l'axe Z, pour y gagner du poids - en vue d'un déplacement plus rapide - et pour minimiser l'influence de la température.
Il y a quelques années, des chercheurs chinois ont étudié l'impact de la fabrication de la table en fibre de carbone. En construisant une table en fibre de carbone avec une structure bionique en nid d'abeille, ils ont réussi à réduire le poids d'environ 45%. En effet, le poids de la table était de 1.100 kg, contre 2.023 kg dans la version originale.
Selon le positionnement de la structure en nid d'abeilles, la déformation de la table sous une charge verticale est légèrement inférieure à celle de la version originale en acier. En outre, elle ne présente que des avantages, notamment une dynamique beaucoup plus élevée en raison du poids plus faible que la machine doit déplacer. L'amortissement plus important des vibrations du matériau contribue également à une plus grande précision.
Ainsi, l'utilisation de matériaux composites permet d'obtenir une plus grande rigidité avec une machine plus légère, ce qui se traduit par des vitesses de coupe plus élevées et de meilleures performances. Cependant, la fibre de carbone reste un matériau exotique dans l'usinage CNC et certainement dans celui des centres d'usinage à 5 axes.
5 axes simultanés ou 5 axes avec indexation?
Lorsque l'on investit dans un centre d'usinage 5 axes, la question peut se poser: 5 axes simultanés ou avec indexation? Il s'agit essentiellement de deux concepts de machines, au sein desquels les fabricants disposent de plusieurs options pour le positionnement des quatrième et cinquième axes.
Le fraisage simultané à 5 axes signifie que les cinq axes se déplacent tous en même temps. C'est un avantage pour les pièces très complexes et pour l'usinage de chambres profondes. La précision est généralement plus élevée, car il est possible de travailler avec des outils plus courts. Cela se traduit notamment par un meilleur état de surface. En fonction de l'application et du matériau, la différence entre la rugosité de surface du fraisage simultané 3+2- et 5-axes peut être importante. Il peut également être utilisé pour réaliser des contre-dépouilles.
Le fraisage simultané en 5 axes présente toutefois des limites. Par exemple, les programmes ne peuvent réellement être créés qu'à l'aide d'un logiciel de FAO, ils sont plus chers à l'achat et la simulation du programme est d'autant plus importante que le risque de collision de l'outil ou de la broche est plus élevé. En revanche, une machine à 5 axes avec indexation est suffisante pour la plupart des applications. Il est important de noter que cinq faces peuvent être usinées dans un seul montage, ce qui permet déjà d'obtenir une plus grande précision que si l'on rechoque la pièce à chaque fois.
Petites machines à 5 axes
Certains fabricants de machines CNC de haute précision ont récemment opté pour un downsizing, comprenez une réduction de la taille de leurs machines. En d'autres termes, des centres d'usinage CNC plus petits utilisés pour le fraisage 5 axes de pièces plus petites. Deux questions sont en jeu dans cette évolution. L'un est la durabilité, l'autre la flexibilité.
L'évolution vers des centres d'usinage CNC plus petits repose sur deux considérations: la durabilité et la flexibilité
Ces centres d'usinage compacts utilisent une fraction de l'énergie d'une grande machine. Certains se contentent même d'une connexion standard de 230 V. Le développement durable et les coûts énergétiques élevés devenant de plus en plus importants, les entreprises manufacturières prennent de plus en plus en compte cet argument.
En déployant plusieurs de ces petits centres d'usinage à 5 axes, les entreprises augmentent leur flexibilité. Cela a tout à voir avec la diminution de la taille des lots. En répartissant la production sur plusieurs petites machines, elles peuvent répondre avec plus de souplesse aux demandes inattendues du marché que si la production est installée sur un grand centre d'usinage automatisé. Plusieurs centres d'usinage 5 axes compacts de ce type, reliés entre eux par l'automatisation, constituent un cadre idéal pour la production de faibles volumes à forte variabilité (high mix low volume).
garantir la précision
Les fabricants de machines CNC à 5 axes se donnent naturellement beaucoup de mal pour construire la machine la plus précise possible. Mais chaque machine perd de sa précision au cours de sa durée de vie avec l'utilisation. C'est pourquoi l'étalonnage est important. Pour ce faire, il existe plusieurs options.
Traditionnellement, il existe des systèmes d'étalonnage laser, souvent appliqués par les spécialistes des fournisseurs de machines. Souvent, les entreprises ne commandent un tel étalonnage qu'après un accident ou lorsqu'elles découvrent sur la machine à mesurer tridimensionnelle des écarts importants et constants dans la précision dimensionnelle.
Dans le cadre d'une production 24/7, ou proche de ce rythme, il est intéressant de calibrer le centre d'usinage 5 axes plus fréquemment. Il existe pour cela plusieurs systèmes sur le marché, qu'un opérateur expérimenté peut réaliser lui-même. L'objectif principal d'un contrôle régulier de la précision de la machine par l'opérateur est d'avoir une idée de l'évolution de la précision et d'intervenir à temps.
Avant de fraiser des pièces très précises, l'opérateur vérifie la précision de la machine par rapport à l'état d'origine. L'étalonnage de la machine elle-même est un processus continu qui doit être effectué régulièrement pour garantir la précision et les performances.