Le manque de solutions de finition automatisées freine la croissance de l'impression 3D sur métal
Post-traitement AM: une étape coûteuse
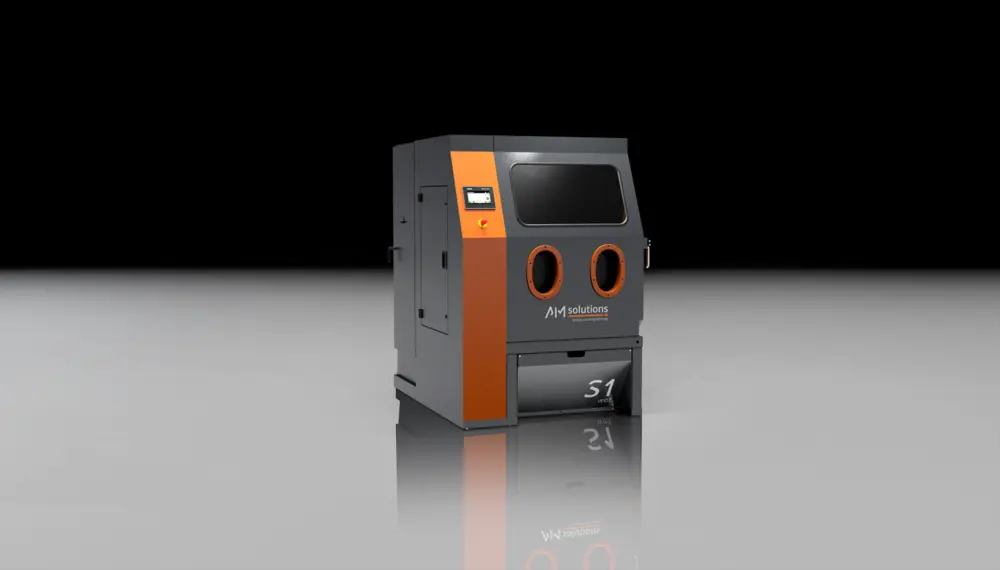
Le post-traitement des pièces produites de manière additive a longtemps été négligé dans l'ensemble du processus AM. Ce n'est que maintenant que les entreprises commencent à envisager sérieusement la production en série par impression sur métal que l'on s'y intéresse. Après tout, le post-traitement peut constituer un obstacle considérable si vous souhaitez utiliser la fabrication additive pour produire un grand nombre de composants finaux.
Le gourou américain de l'AM, Terry Wohlers, qui suit chaque année l'évolution du marché mondial de l'AM depuis plus d'un quart de siècle, a récemment publié une étude intéressante. Cette fois, il a examiné l'impact du post-traitement sur les coûts à la fois dans les entreprises de services d'impression 3D et dans les entreprises qui impriment en 3D des pièces en série pour leur propre production. Pour les polymères et le métal, M. Wohlers conclut que 27% du coût de l'impression 3D d'une pièce est dû au post-traitement. C'est presque le même niveau que celui trouvé dans une autre étude récente.
Dans le Additive Post-Printing Survey Trends Report 2021, les chercheurs ont constaté que 30% des participants à cette enquête dépensent plus de 26% de l'ensemble de leur budget AM pour le post-traitement. Un an plus tôt, ce chiffre était encore de 23%. Les points les plus problématiques sont les longs délais de post-traitement, la faible cohérence des résultats, la productivité limitée et le gaspillage qui en résulte. Un autre goulot d'étranglement pour 26% d'entre eux est la nécessité d'employer des travailleurs qualifiés.
Inhibition du passage à l'échelle
Ces deux études ne sont pas isolées lorsqu'il s'agit de l'impact réel du post-traitement sur la fabrication additive. Les grands équipementiers de l'industrie aérospatiale considèrent également le post-traitement comme un talon d'Achille. Boeing et Airbus affirment tous deux que la technologie actuellement disponible pour le post-traitement des pièces métalliques AM constitue un sérieux frein à l'utilisation de l'AM pour une production en plus grand volume. Une mise à l'échelle signifierait que tous les processus ultérieurs devraient également être mis à l'échelle. Cela nécessite des investissements supplémentaires et, surtout, beaucoup de mains supplémentaires. Boeing est d'avis que cela ralentit la croissance. L'un des experts en AM d'Airbus a récemment fait remarquer lors d'une conférence que 79% des coûts totaux de l'AM sont liés à autre chose que l'impression 3D proprement dite. Le post-traitement en est un élément important.
Le post-traitement des pièces fabriquées de manière additive a longtemps été une partie négligée de l'ensemble du processus AM
Influence du design
La conception a une grande influence sur les coûts. La première chose qui vient à l'esprit lorsqu'on pense au post-traitement des pièces AM est la suppression des structures de support requises par les imprimantes laser à lit de poudre métallique (LPBF). Comme leur suppression coûte de l'argent, il est important d'imprimer le moins de structures de soutien possible. La conception de la pièce, mais aussi son positionnement sur la plaque de construction de la machine, influent sur le coût de la finition. Cela ne s'applique pas seulement à la suppression du soutien, d'ailleurs. Si vous imprimez des structures creuses sur des machines LPBF, il reste de la poudre libre. Il faut en tenir compte dans le processus de conception et veiller à ce qu'il puisse être supprimé.
Il existe donc davantage de règles de conception pour la fabrication additive, qui visent à rendre le post-traitement aussi efficace que possible. La première étape du processus après l'impression 3D est l'élimination de la poudre. Il existe maintenant des machines sur le marché qui le font presque automatiquement. Le panneau de construction sur lequel se trouvent les pièces est mis en rotation dans une cabine, éventuellement avec des vibrations pour enlever la poudre. Les systèmes les plus récents peuvent être programmés plus facilement. Les mouvements nécessaires pour enlever la poudre dépendent également de la forme et de la complexité de la pièce AM. Pour éliminer la poudre de titane ou d'aluminium, l'espace doit être rempli d'un gaz protecteur. Ainsi, le système est conforme aux normes ATEX. Afin d'éliminer aussi automatiquement la poudre des canaux internes, certains fabricants de machines utilisent des fréquences ultrasoniques.
RETIRER LES PIÈCES DU PANNEAU DE CONSTRUCTION
Au bout du compte, les pièces devront toujours être retirées du panneau de construction, du moins dans le cadre d'un processus d'AM sur lit de poudre laser. Pour cela, deux options sont possibles: l'électroérosion à fil ou la scie de précision. La plupart des entreprises optent pour la machine à couper les fils, car c'est celle qui gaspille le moins de matériau du panneau de construction. Il est fraisé à plat et est alors prêt pour le prochain travail de construction.
finition de surface
Les équipementiers qui souhaitent produire des pièces métalliques en série de manière additive recherchent l'automatisation lorsqu'il s'agit de retirer le matériau de support. Plusieurs fabricants ont récemment mis au point des machines permettant de retirer automatiquement les structures de support à l'aide de procédés (électro)chimiques. L'hirtisation en est un exemple. Il s'agit de la combinaison d'un processus électrochimique, d'un flux hydrodynamique et de l'élimination chimique des parties rugueuses de la surface avec l'appui de petites particules.
En trois étapes, la rugosité de surface est réduite de 100 µm pour atteindre finalement 0,5 µm, qualité de polissage. Cette dernière est la troisième étape; les deux premières atteignent déjà Ra 2 µm. Le polissage électrochimique permet également de lisser les surfaces internes, ce procédé réduisant la rugosité de surface jusqu'à 80%. Il s'agit donc d'une technologie plus fréquemment utilisée pour le lissage des surfaces, notamment en cas de zones difficiles à atteindre sur une pièce. Le processus en plusieurs étapes est entièrement automatisé et ne nécessite aucun traitement mécanique.
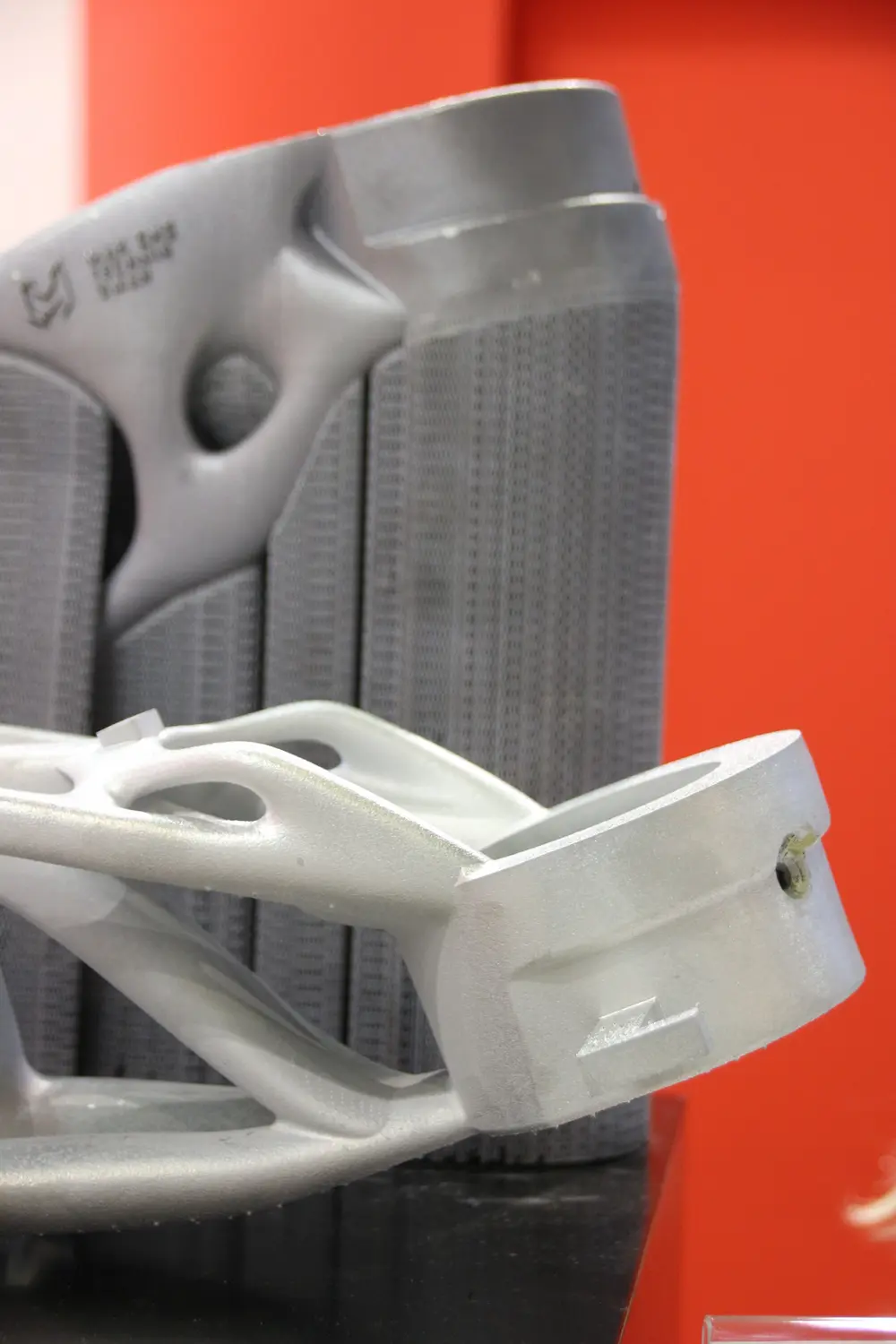
tambourinage
Les applications de cette technologie comprennent des produits de type collecteur, avec des canaux de refroidissement internes. Ou des outils où les canaux de refroidissement passent sous la surface et sont fabriqués de manière additive. Parfois, le polissage chimique (acides) est combiné au tambourinage, une technologie connue dans l'industrie métallurgique pour améliorer la rugosité de surface. Le traitement chimique est contrôlé par des paramètres, afin d'éviter d'enlever trop de matière par endroits.
Pour certaines applications, la finition chimique n'est pas une solution car ces types de produits chimiques ne sont pas autorisés. Dans ce cas, le sablage et le tambourinage sont les techniques les plus appropriées pour améliorer la surface rugueuse des pièces produites de manière additive. En fait, cela s'applique également aux applications où la surface n'a pas besoin d'être polie. L'ajout d'eau à l'agent de sablage, qui a un effet positif sur le résultat final, est une évolution récente. Un autre avantage est que pour les produits à paroi mince, l'eau forme une couche protectrice, ce qui réduit les risques de changement de forme et de précision dimensionnelle.
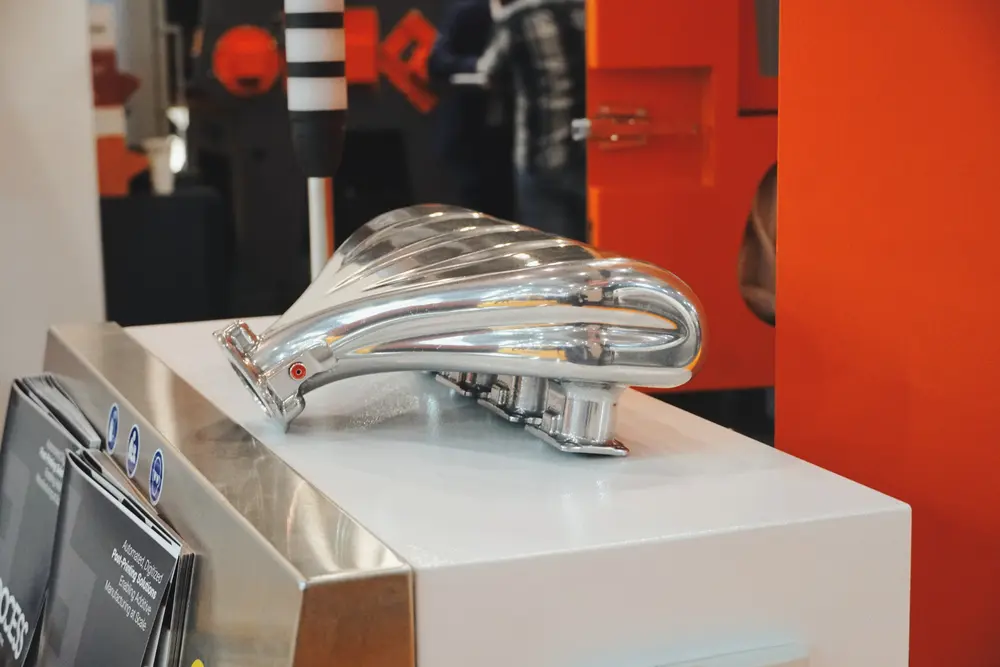
Traitement au laser
Un développement qui en est encore à ses débuts, mais qui offre du potentiel, est le polissage au laser des pièces en AM. Des recherches à ce sujet ont été menées dans un certain nombre d'endroits dans le monde, notamment aux Pays-Bas. Chez nos voisins du nord, cette opération a été réalisée à l'aide d'un laser à fibre pulsé d'une longueur d'onde de 1 064 nm et d'une puissance de 60 W. Le faisceau laser se déplace à grande vitesse (entre 1.000 et 4.000 mm par seconde) sur la surface, d'abord dans le sens longitudinal, puis dans le sens transversal. De cette manière, les pics - visibles uniquement au microscope électronique - sont refondus et les 'creux' comblés. Le résultat final est qu'en un temps très court, la rugosité est réduite de Ra 12 µm après l'impression 3D à Ra 2 µm. La dureté reste presque la même. Tout comme les dimensions qui ne changent que de quelques centaines de millimètres (dans le cas du 316L ou de l'acier à outils).
Le polissage au laser est beaucoup plus rapide que le polissage mécanique et est plus facile à réaliser car il n'y a pas de charge sur la pièce. Des chercheurs chinois ont présenté une approche légèrement différente, avec des résultats différents, lors d'une conférence sur le polissage au laser à Aix-la-Chapelle l'année dernière. Ils ont poli l'Inconel 718 avec un laser à fibre nanoseconde (90 W) et ont réussi à obtenir une valeur Ra de 0,1 µm et une valeur Rz de 0,6 µm. Leur stratégie modifie la dureté, ce qu'ils ont aussi consciemment recherché. La résistance à l'usure de l'Inconel s'améliore de 90% en polissant les pièces au laser.
La KU Leuven s'est également penchée sur le sujet, mais utilise le laser lors de l'impression 3D de métaux. Dès qu'une couche est imprimée, le second laser (un laser pulsé nanoseconde) vient souffler la poudre résiduelle sur les bords ou à la surface de la pièce avec une onde de choc. Ensuite, le premier laser illumine à nouveau la couche et refond la couche supérieure. Cela crée le même effet que dans le projet néerlandais, le métal coule vers les parties inférieures. Cela crée une surface plus lisse, exactement ce qui est nécessaire dans de nombreuses applications. Les recherches menées à Louvain montrent que la rugosité s'est déjà améliorée de 80% pendant l'impression.
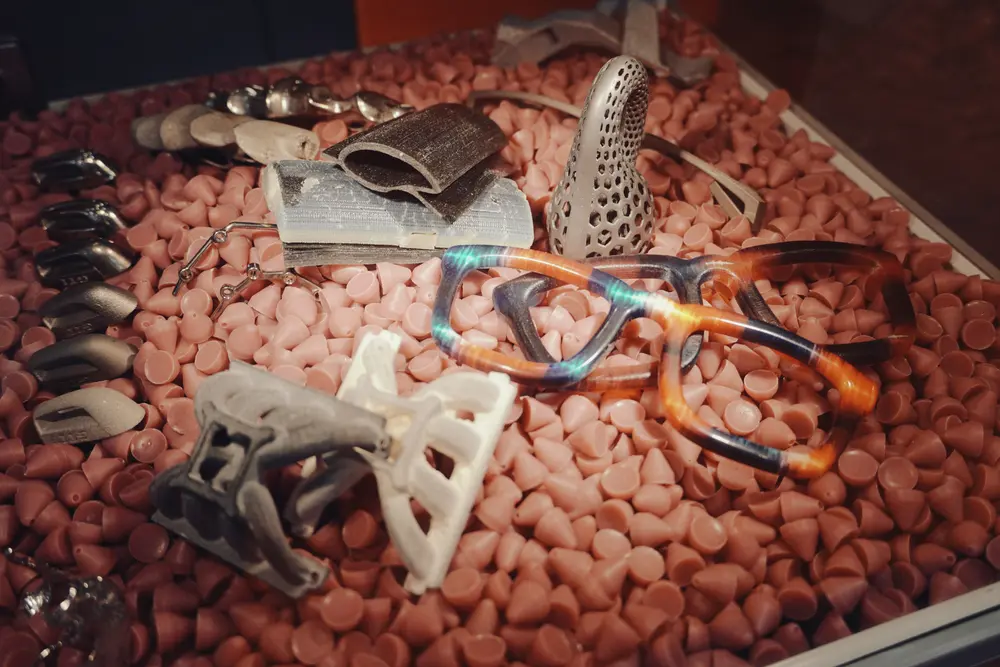
HIP et autres opérations de post-traitement thermique
L'une des étapes de post-traitement qui prend probablement le plus de temps est le post-traitement thermique. Le recuit de détente, qui permet d'éliminer les contraintes résiduelles dans le matériau après le processus de lit de poudre laser, est une étape simple. La situation devient plus complexe lorsque l'on souhaite améliorer la structure du matériau par un traitement thermique. Cela nécessite un meilleur contrôle du chauffage et du refroidissement des pièces dans le four, car cela détermine le résultat final.
Le pressage isostatique à chaud, ou Hot Isostatic Pressing, va un peu plus loin et vise à réduire la porosité. Le HIP, comme on appelle souvent le post-traitement, empêche la formation de microfissures dans les pièces. Pour les implants médicaux, mais aussi pour les pièces d'avion, il s'agit souvent d'une finition obligatoire, car elle améliore les propriétés de fatigue d'un facteur dix à cent. Avec la pression isostatique à chaud, une pièce est mise sous pression et, en même temps, la chaleur est fortement augmentée. Une nouvelle option du procédé consiste à refroidir très rapidement les pièces, ce qui élimine la porosité en même temps que les contraintes résiduelles. En principe, cela pourrait accélérer le processus d'impression lui-même, car il ne serait pas nécessaire de rechercher la densité maximale. Ceux-ci sont ensuite créés en post-traitement lors de l'usinage HIP.