Ontwikkeling CAM-software verlaagt risico op fouten
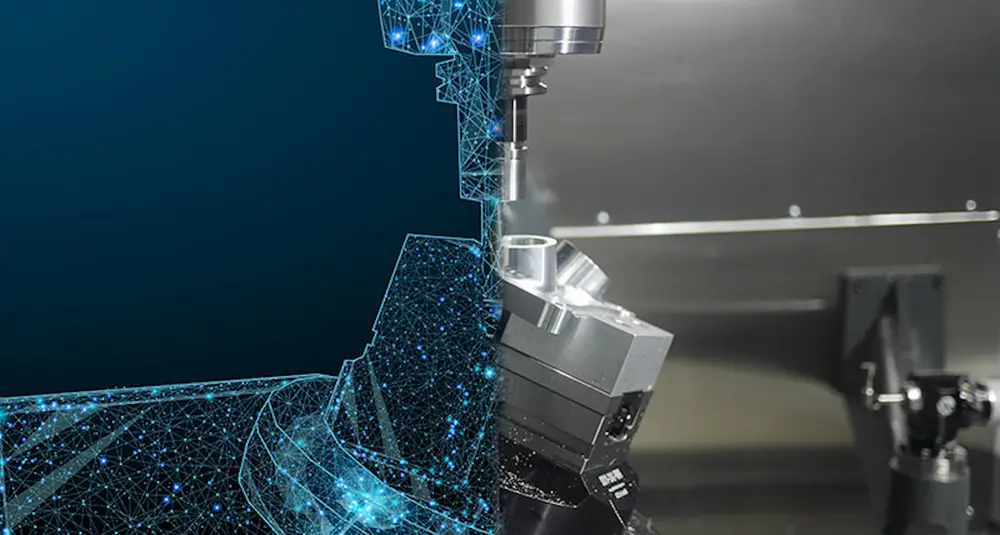
De komende jaren zullen verschillende trends een stempel drukken op de ontwikkeling en het gebruik van CAM-software. Allereerst het gebruik van Model-Based Definition (of beter gezegd PMI-data); ten tweede de digital twin, die onder andere CAM-software richting de cloud duwt en de integratie van additive manufacturing in de programmeersoftware voor subtractieve bewerkingen.
Onlineplatform
De grote CAD-ontwikkelaars hebben inmiddels allemaal hun onlineplatform waarop ze hun designsoftware inclusief simulatietools aanbieden.
Behalve dat ze met software in de cloud sneller hun producten kunnen upgraden en het eenvoudiger is om de rekenkracht vanuit hun datacenter op te schalen en te delen, speelt er ook nog mee dat de ontwikkelcycli in de maakindustrie zo kort worden dat de verschillende stappen in het proces van idee tot en met productie deels parallel plaatsvinden en niet meer stap voor stap.
Op het platform is het makkelijker voor partijen om samen te werken met de zekerheid dat iedereen altijd met het meest actuele 3D-model werkt. De digitale continuïteit wordt hiermee beter gewaarborgd. Het aantal CAD-gebruikers dat in de cloud werkt, groeit dan ook hard.
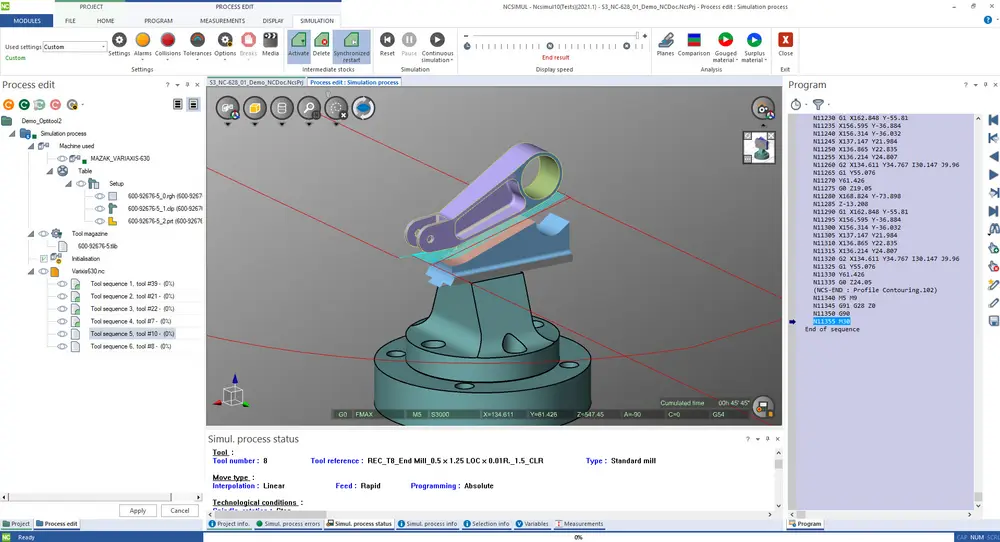
CAM en de digital twin
Bij CAM-software ligt het iets anders: er is CAM-software op cloudplatformen beschikbaar, zeker bij de aanbieders van geïntegreerde CAD/CAM-pakketten.
De stap naar de CAM in de cloud staat echter nog redelijk aan het begin. Onderwijsinstellingen gebruiken het wel, omdat het voor studenten gemakkelijk en aantrekkelijk is als ze enkel via een browser hoeven in te loggen.
Waarschijnlijk vinden veel maakbedrijven het een stap te ver om hun specifieke maakkennis van onderdelen te uploaden naar de cloud, ofschoon dat meer een gevoelsmatig argument is dan dat de cloud echter minder veilig is dan een eigen server in het bedrijf.
Qua prestaties en snelheid kan de cloud weleens verrassend goed presteren, vergeleken met software op eigen werkstations
Qua prestaties en snelheid kan de cloud weleens verrassend goed presteren, vergeleken met software op eigen werkstations. Nu de digitale tweeling een alsmaar grotere rol in productieprocessen speelt, zou deze transitie naar cloudgebaseerde software wel eens in een stroomversnelling kunnen geraken.
CAM-software wordt nog wel eens gezien als programmeersoftware om het machineprogramma mee te maken, in trek geraakt sinds de komst van de 5-assige en multitaskingmachines. Het gaat echter om het hele proces om van CAD-model tot een verspaand product te komen.
De digitale tweeling (digital twin) zal in de komende jaren een zwaarder stempel gaan drukken op de CAM-software. Op verschillende manieren. Allereerst kan men de virtuele CNC-machine gebruiken om het proces al in te richten en te optimaliseren voordat de machine geleverd is.
Men kan al starten met de ontwikkeling van de postprocessor voordat de machine fysiek in de productiehal staat. Daarna kan men de digitale tweeling gebruiken om het freesprogramma aan te passen voordat de eerste spanen worden geproduceerd. Om een CAD-model van het totale gereedschap, dus houder en snijgereedschap, in te laden in de CAM-software, is niets bijzonders meer.
Het inlezen van de digitale tweeling van de CNC-machine gaat een stap verder. Hiermee verloopt de simulatie completer en nauwkeuriger omdat niet alleen werkstuk, opspanning en gereedschap worden meegenomen, maar dat de kinematica van de machine wordt gebruikt voor de virtuele bewerking.
Bredere inzet van simulatie
Simulatie zoals we dat kennen en virtueel verspanen met een digitale tweeling zijn niet identiek. Bij simuleren interpreteert de software bepaalde zaken. Bij virtueel verspanen met een digitale tweeling wordt er gewerkt met een besturing die identiek is aan die op de fysieke machine. Problemen die zich op de machine voordoen, zullen bij virtueel bewerken sneller aan het licht komen dan bij een eenvoudige simulatie die alleen de freesbanen controleert op eventuele botsingen door de spil.
Met de digitale tweeling van de machine wordt de simulatie ook een middel om te controleren of het programma wel het meest optimale is. Sterker nog: bij sommige softwareaanbieders kan men al relatief eenvoudig virtuele bewerkingen op meerdere CNC-machines draaien om de meest geschikte voor een bepaalde bewerking te selecteren.
Ook kan men met de virtuele tweeling 5-assige bewerkingen optimaliseren, bijvoorbeeld om trillingen te vermijden. Wanneer de door CAM-software gegenereerde freesbaan in de buurt van het singulariteitspunt komt of hier doorheen gaat, kan de machine gaan trillen, waardoor er op het te bewerken productoppervlak chattersporen ontstaan.
Problemen die zich op de machine voordoen, zullen bij virtueel bewerken sneller aan het licht komen dan bij een eenvoudige simulatie
Met name bij het frezen van turbinecomponenten is dat problematisch. De nieuwste simulatietool die met digitale tweelingen werkt, voorspelt waar dit omslagpunt zich voordoet, waarna men de freescondities kan aanpassen om dit te vermijden. Doordat de simulatie tevens bepaalt wanneer een 5-assige verspaningsbewerking optimaal is, kan men beide zaken combineren. Door de ideale werkstukpositie te combineren met de optimale freesparameters, haalt men maximaal profijt uit de bewerking.
Door de eigen manier van werken, de specifieke eigenschappen van de machine en de kennis van de operator samen te brengen, kan het proces met grote stappen worden geoptimaliseerd. En deze verbeterslag kan in de toekomst nog worden verbreed door data uit de feitelijke productie terug te leiden naar het CAM-programma voor de noodzakelijke aanpassingen voor een volgende keer.
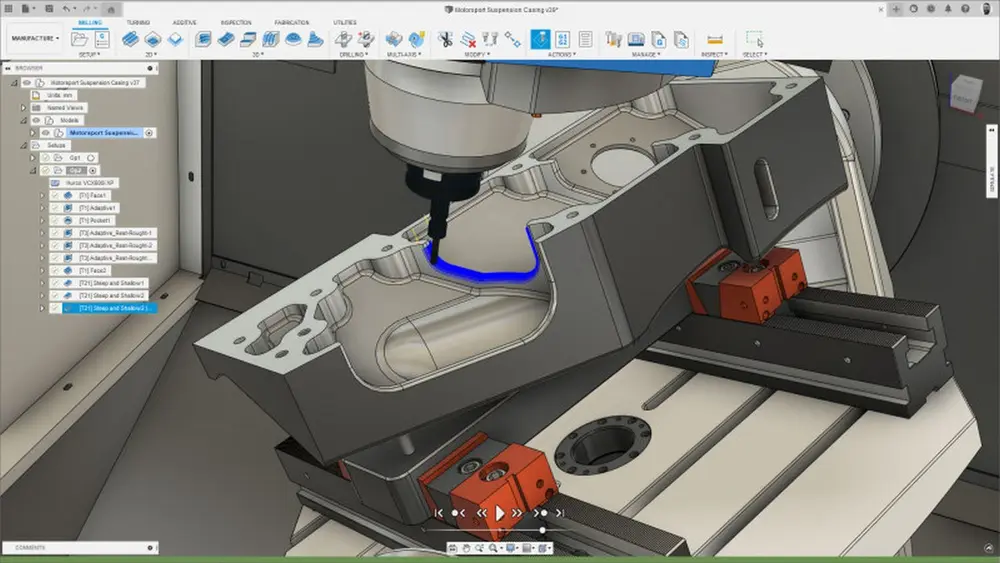
Model-Based Definition: minder fouten, minder werk
Het absolute sleutelwoord in de huidige ontwikkelingen van CAM-software is Model-Based Definition: met PMI-data (Product Manufacturing Information) worden details over het maken van het onderdeel aan het 3D-model toegevoegd. De toleranties, oppervlakteruwheden en andere details van de 2D-tekening worden als annotatie aan het 3D-model gekoppeld. OEM's die deze stap zetten, leveren alleen nog het 3D-model verrijkt met PMI-data aan hun toeleveranciers. Dus niet langer het 3D-model en de 2D-tekeningen van alle aanzichten.
Een van de grote drijfveren voor OEM's om met Model-Based Definition te gaan werken, is het verkleinen van de foutkans. In de toekomst wordt het namelijk steeds gemakkelijker om met speciale software de 3D-modellen van de constructeur te controleren op maakbaarheid.
Een van de grote drijfveren voor OEM's om met Model-Based Definition te gaan werken, is het verkleinen van de foutkans
Nu al kan speciale software herkennen dat een aangegeven tolerantie niet realiseerbaar is, of dat een constructeur een oppervlakteruwheid vergeten is te annoteren. In de toekomst zullen engineers overstappen naar regelgebaseerd construeren; de brij aan productiegegevens die ze vaak nog op een 2D-tekening plaatsen, is dan vervangen door een aantal standaarden waarmee toleranties en oppervlaktespecificaties automatisch worden gegenereerd.
Het gebruik van Geometric Product Specification maakt het gebruik van PMI-data sneller lonend. Een belangrijk voordeel van MBD is dat er op een eenduidige manier wordt gecommuniceerd, op voorwaarde dat de engineer het 3D-model goed maakt met de juiste annotaties. Die mogen op geen enkele wijze voor verschillende uitleg interpreteerbaar zijn. Discussies over hoe toleranties te interpreteren, zouden niet meer mogen voorkomen. Ook is er geen risico meer dat het 3D-model op het laatste moment wordt gewijzigd maar de 2D-tekening niet.
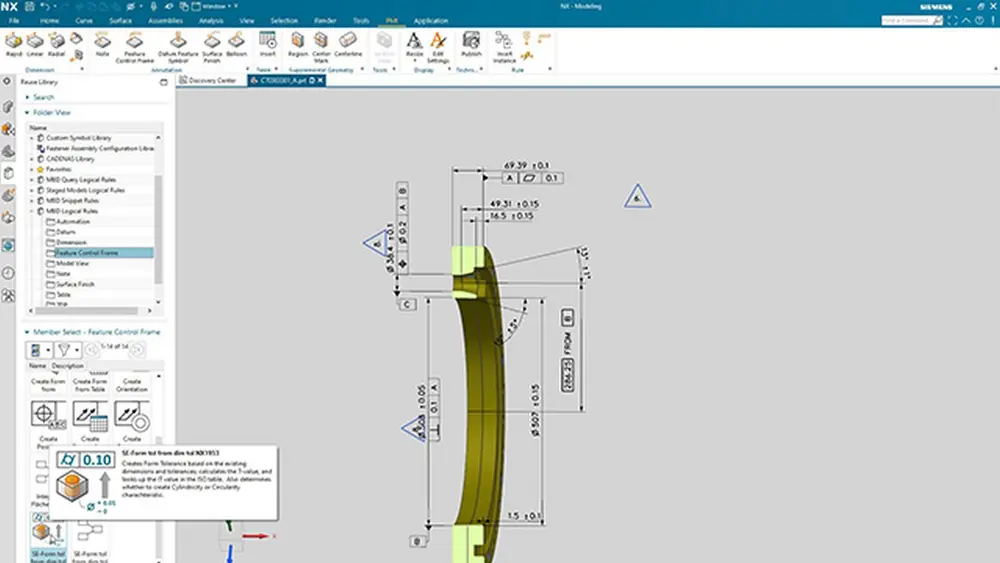
Onderzoek en eigen ervaring bij het energiebedrijf van Siemens tonen aan dat het gebruik van regelgebaseerde engineering een kritische succesfactor is voor MBD en PMI. Als de engineers alle info uit de 2D-tekening direct in de PMI-data plaatsen, zijn de kosten hoger dan de opbrengsten. Zodra men regelgebaseerd gaat werken, slaat dat om
Programmeren automatiseren
Toeleveranciers kunnen in bepaalde gevallen de PMI-data van het 3D-model gebruiken om hun machines deels geautomatiseerd te programmeren, feature-based machining. De software herkent bepaalde onderdelen van het design en koppelt daar specifieke bewerkingsstrategieën met gereedschappen aan. Dat scheelt handmatige handelingen bij het programmeren. Bij meetmachines lukt dat meestal behoorlijk en kan men tijd besparen.
Bij het programmeren van een CNC-bewerkingscentrum vanuit het MBD-model ontstaan er vaak problemen als de CAM-software van een andere aanbieder is dan de CAD-software waarmee het product is getekend. Converteren via een neutraal STEP-formaat kan helpen, maar in de praktijk gaan annotaties vaak verloren en wordt het voor een toeleverancier moeilijk om de efficiencystap te maken.
In dat laatste aspect schuilt de reden waarom de machinebouwindustrie nu pas met Model-Based Definition begint. Want andere industrieën, zoals de defensie-, automobiel- en luchtvaartindustrie, werken er al veel langer mee. Daar gebruiken toeleveranciers vaak dezelfde software als hun klanten, waardoor het gemakkelijker is de data te hergebruiken.
Een directe oplossing voor het probleem is nog niet beschikbaar. Een verbetering is het wel als de engineer het 3D-model en de PMI-data gescheiden aanlevert: dan verbetert de uitwisselbaarheid van de PMI-data.
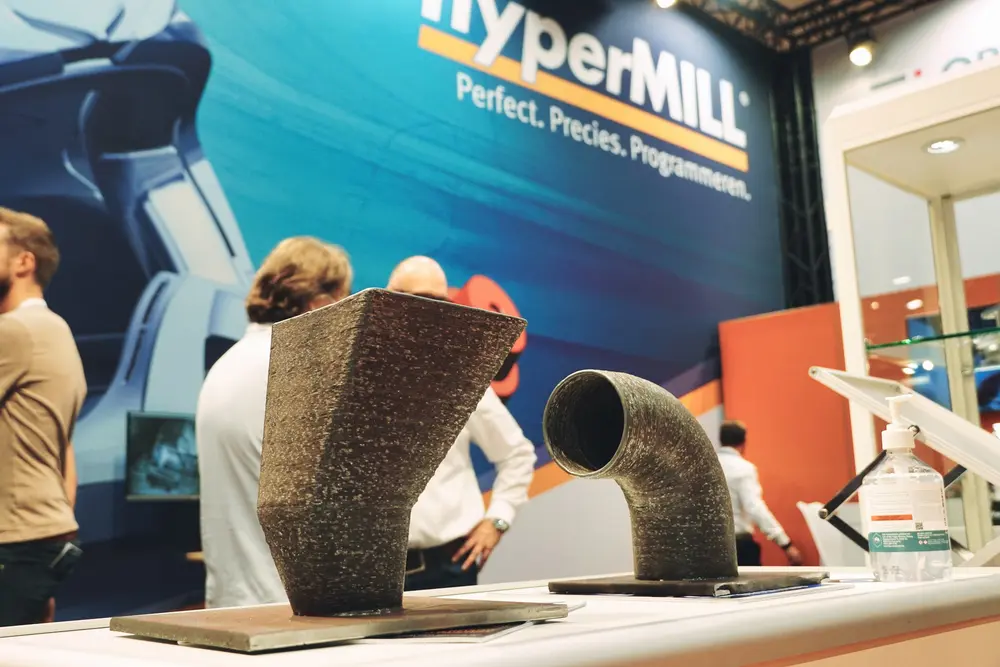
Het programmeren van 3D-metaalprinters gebeurt steeds vaker in dezelfde softwareomgeving als het programmeren van de CNC-machine voor de nabewerking van de onderdelen. Een van de CAM-ontwikkelaars die hierop inzet is hyperMILL, dat inmiddels een AM-module voor DED- en laserpoederbedfusiontechnologie aan de CAM-software heeft toegevoegd
Additive Manufacturing
Een derde ontwikkeling in CAM-software is de integratie van programmeersoftware voor additive manufacturing. In plaats dat men de beide bewerkingen afzonderlijk programmeert, kan dit met de nieuwe CAM-pakketten in één omgeving gebeuren, inclusief simulaties. Beide machines – of beide bewerkingen als het 3D-metaalprinten geïntegreerd is in de CNC-bewerkingsmachine – worden met dezelfde virtual machine gesimuleerd.
Een van de voordelen daarvan is dat men bepaalde handelingen kan automatiseren en dat de software automatisch rekening houdt met de gevolgen van veranderingen in de additieve opbouw voor de verspanende nabewerking. Zo kan men ook snel controleren of een bepaalde overmaat die met AM wordt aangebracht voldoende is voor de CNC-bewerking.