SLAAT DE VONK OVER?
GROEIVOORUITZICHTEN VONKEROSIE BLIJVEN OVERWEGEND POSITIEF
De belangstelling voor vonkerosie groeit. De alsmaar hogere eis tot nauwkeurigheid, oppervlakteruwheden en complexere werkstukken zijn belangrijke drijfveren achter deze trend. Daarnaast hebben intelligente besturingssystemen de technologie toegankelijker gemaakt. Vonkeroderen past hierdoor in moderne machinefabrieken.
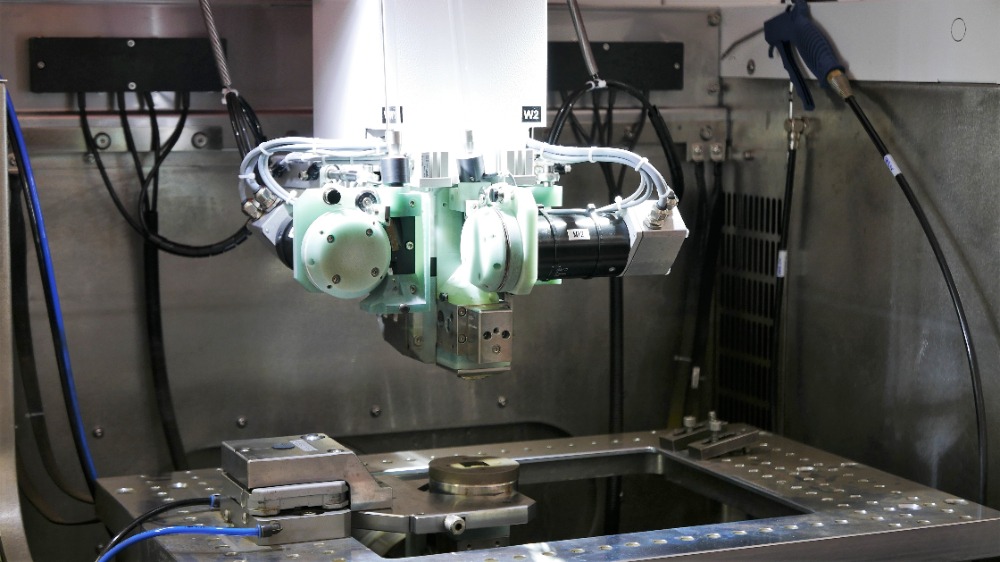
Draad- en zinkvonken wordt omschreven als een vrij recente technologie, die pas gedurende de voorgaande vijftig jaar tot ontwikkeling is gekomen. Strikt genomen klopt dit; de komst van gestuurde pulsgeneratoren in de jaren 60 hebben voor het eerst de technologie een plek gegeven in specifieke segmenten van de discrete industrie. De eerste ideeën om met een vonk metalen te bewerken, dateren echter al van eind 19e eeuw.
Onderzoekers vroegen zich destijds af waarom de laselektrode aan de pluspool sneller sleet. Rond 1942 werd in de VS een patent toegekend voor een technologie die gebruikmaakte van een onderbroken lichtboog om tanden uit een zaagblad te snijden. Twintig jaar later zorgden gestuurde pulsgeneratoren ervoor dat men grafiet als elektrodemateriaal kon gebruiken. Vanaf 1970 kwamen daar nog eens de numeriek bestuurde vonkerosiemachines bij, die gewild zijn in de gereedschapsindustrie.
DE TECHNOLOGIE
Bij vonkerosie verspaant men materiaal door middel van een vonk. Tussen de gereedschaps- en werkstukelektrode wordt een elektrische spanning opgewekt, zodat een vonk van het gereedschap overslaat naar het werkstuk en het materiaal daar verdampt. Hoe kleiner de vonkspleet, des te meer energie er overslaat. Elektrische energie wordt omgezet in thermische (met temperaturen in het plasmakanaal van 8.000 tot 12.000 °C, met uitschieters tot wel 20.000 °C). Deze hoge temperatuur zorgt ervoor dat het materiaal verdampt.
Voordelen
Het werkstuk wordt mechanisch niet belast. Bij draadvonken bijvoorbeeld wordt het draadgereedschap quasi elke keer vernieuwd, waardoor het materiaal langer intact blijft. Naast de machine – het gereedschap in de vorm van draad of bij zinkvormen in de vorm van een elektrode – is er een diëlektricum nodig. Deze vloeistof koelt het werkstuk en verwijdert het losgekomen materiaal uit de vonkspleet. Spoelen is een van de belangrijkste procesparameters.
Nadelen
Het grootste nadeel aan deze techniek is dat ze traag is. Daarnaast kunnen alleen materialen die elektrisch geleidend zijn, bewerkt worden. Daar staat tegenover dat de hardheid van het materiaal in principe niets uitmaakt en dat de machine quasi onbemand bestuurd kan worden.
WANNEER VONKEROSIE?
Door de opkomst van 5-assig frezen, high speed milling en het hardmetaal frezen, lijkt vonkerosie in de marge te worden geduwd. Met voorgenoemde nieuwe technieken kan men immers erg nauwkeurig werken en behalen zij resultaten die voordien enkel maar met vonkerosie gerealiseerd konden worden. Daar komt nog eens bij dat veel verspaners die geen specifieke ervaring hebben met vonkeroderen, ook niet naar deze techniek zullen grijpen. Deze trend is inmiddels aan het afnemen. De hoge nauwkeurigheidseisen, kleinere radii en scherpere hoeken vragen om via vonkerosie precies te worden uitgevoerd. In de medische industrie en in de matrijzenproductie bijvoorbeeld blijft vonkeroderen een belangrijke rol spelen.
Uit een recent Amerikaans marktonderzoek blijkt dat de groei van de EDM-markt de komende jaren onder de 4% blijft. Tegen 2023 zal de wereldwijde EDM-markt ongeveer $ 885 miljoen bedragen. Dit toont aan dat ontwikkelingen zoals Industrie 4.0, elektrisch en autonoom rijden en de vooruitgang in de gezondheidszorg deze techniek uit de niche zullen halen en zo het fundament zullen leggen voor haar toekomstige groei. Wanneer er bijvoorbeeld diepe ribben in een werkstuk of matrijs nodig zijn, of heel kleine radii, blijft draadvonken de aangewezen technologie. In een aantal toepassingen kan vonkeroderen efficiënter zijn dan 5-assig frezen, bijvoorbeeld als het om heel dunwandige producten gaat waaraan hoge nauwkeurigheidseisen gesteld worden. Een combinatie is soms een nog betere oplossing: 5-assig voorfrezen en nadien nabewerken met EDM. Belangrijk is altijd om alle processtappen te bekijken die nodig zijn om tot het eindproduct te komen. Als de oppervlaktekwaliteit in één keer behaald wordt met vonkeroderen, kan de doorlooptijd toch korter zijn.
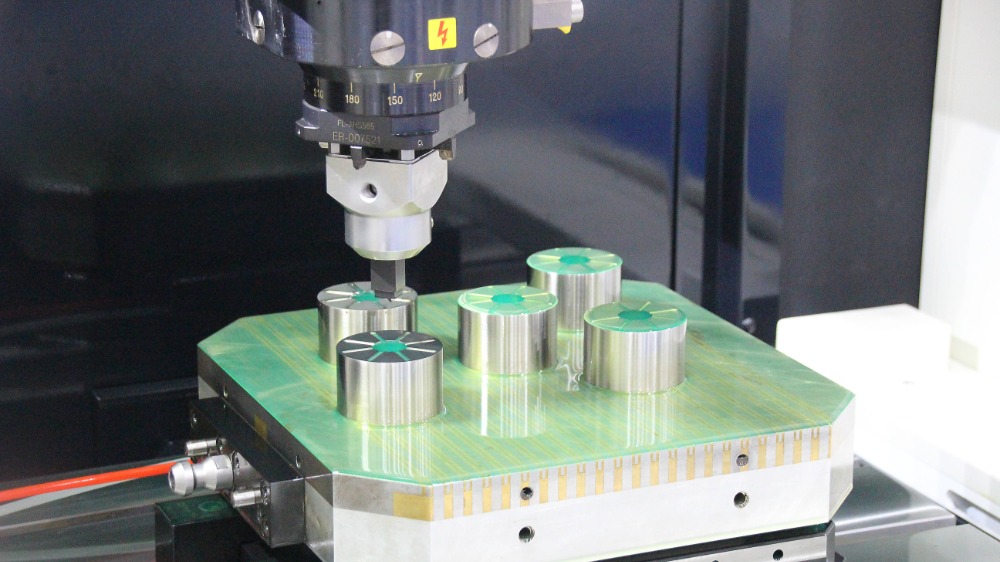
Luchtvaartindustrie
In de vliegtuigindustrie neemt het aantal toepassingen van vonkerosie toe dankzij ontwikkelingen bij de machine-industrie. Tien jaar geleden weigerden fabrikanten van vliegtuigmotoren nog gevonkte onderdelen, omdat hierbij altijd een Heat Affected Zone (HAZ) ontstaat. Dat is het dunne witte laagje op de werkstukken als gevolg van warmte-inbreng. In de luchtvaartindustrie vreesde men lange tijd het ontstaan van microcracks. Door de verbeteringen aan de pulsgenerator kunnen de EDM-machinebouwers tegenwoordig de puls veel beter controleren, zowel qua duur als qua vorm. Hierdoor is de HAZ kleiner en voorspelbaarder geworden. In bepaalde gevallen is deze zelfs verwaarloosbaar.
Tegenwoordig wordt vonkeroderen onder andere ingezet voor het maken van kritische turbinecomponenten voor vliegtuigmotoren. De verbeterde vonktechnologie leidt tot betere oppervlakken, waarbij men bijna polijstkwaliteit haalt (Ra-waarde 0,04 micron). Enerzijds impliceert dit een trager proces, maar in toepassingen waarin dergelijke ruwheden gevraagd zijn, kan men een extra processtap (polijsten) uitsparen. Het verder bijschaven van de oppervlakteruwheden is een van de belangrijkste thema’s bij machinebouwers. Anderzijds vormt het spoelen een aandachtspunt. Spoelen is noodzakelijk, maar leidt tegelijkertijd tot slijtage aan de elektrode (bij het zinkvormen). Naast alternatieve spoelmethoden onderzoekt men de juiste samenstelling van het diëlektricum. Olie lijkt daarbij voor nog betere oppervlaktekwaliteiten te zorgen.
PRECISE ECM VS ZINKVONKEN
De laatste jaren komt men in de fijnmechanische industrie in de BENELUX her en der Precise ECM tegen, een variant op elektrochemisch verspanen (een combinatie van EDM met ECM). Bij P-ECM brengt de hydraulische Z-as de elektrode tot op 10 µm van het werkstuk.
Daarna oscilleert de elektrode en wordt er telkens een elektrische impuls gegeven, wanneer de elektrode dicht bij het werkstuk is. Direct daarna beweegt de elektrode weer in tegengestelde richting en komt er een 30 nanometer dun laagje materiaal los. Het belangrijke verschil met vonkeroderen is dat de elektrode niet slijt. Dat heeft te maken met het elektrolyt, in dit geval een zoutoplossing. Doordat er direct gespoeld wordt, kunnen de elektroden zich niet aan het gereedschap hechten. Verder gaat het hier over een koud proces waarin geen warmte wordt ingebracht.
LAGERE INSTAPDREMPEL VOOR EDM
Naast het feit dat de fabrikanten van draad- en zinkvonkmachines intensief hebben gewerkt aan betere generatoren, is ook het besturingssysteem veranderd. Typerend voor de technologie is het grote aantal procesparameters dat van invloed is op de productiviteit en nauwkeurigheid. Machinebouwers slagen erin om steeds meer knowhow van de technologie in de besturing te integreren, waardoor het programmeren en bedienen van de machine eenvoudiger wordt. De komende jaren mag met de komst van artificiële intelligentie (AI) en Machine Learning (ML) nog wel het een en ander verwacht worden. Daarmee haalt men voor veel machinefabrieken de drempel weg om in EDM te stappen. Sommige fabrikanten passen in hun besturing een helpfunctie toe, die zelfs de minder ervaren operator stap voor stap door het proces loodst. De inzet van EDM wordt verder vereenvoudigd door innovaties als een automatische draadwissel.
“In een aantal toepassingen kan vonkeroderen efficiënter zijn dan 5-assig frezen"
VARIATIES OP DRAAD- EN ZINKVONKEN
Op het traditionele draad- en zinkvonken bestaan er enkele varianten. Eén hiervan is het ultrasoon vibreren van de elektrode om de prestaties te verhogen. Door de trilling ontstaat er meer agitatie in het diëlektricum, wat voor een hogere druk zorgt in de vonkspleet (tussen het werkstuk en de elektrode). In sommige onderzoeken wordt gezegd dat deze technologie de voordelen van vonkeroderen combineert met die van ultrasoon verspanen. Daarnaast bestaat er ook een hybride proces: laserverspanen wordt gecombineerd met vonk-eroderen voor de laatste eindbewerkingen. Ook tijdens het slijpen wordt EDM al ingezet, voornamelijk om de productiviteit te verbeteren. Een vrij recente ontwikkeling is de komst van elektrisch geleidende keramieksoorten. Er wordt onderzocht of dit bruikbaar is voor elektrodes, omdat dit hun slijtagegevoeligheid zou doen afnemen. Aangezien bij zinkvonken tot 50% van de totale proceskosten bepaald worden door de elektrokosten, wordt dit thema vaak aangekaart.
INVLOED ADDITIVE MANUFACTURING
Een andere ontwikkeling die draadvonken interessant maakt, is 3D-metaalprinten. Bij de laserpoederbedtechnologie worden de werkstukken geprint op de bouwplaat. Draadvonken is hiervoor de geknipte technologie. Meerdere machinebouwers zien een potentiële markt en beginnen hun machines reeds aan te passen aan dit specifieke doel. Sommigen brengen relatief eenvoudige draadvonkmachines op de markt, omdat de bewerking eigenlijk niet meer vraagt. Anderen passen dan weer bestaande machines aan, omdat bij draadvonken de draad normaal altijd verticaal loopt. Om de werkstukken los te kunnen snijden van de bouwplaat, wordt een kantelmechanisme gebruikt.