De toenemende rol van software in het AM-proces
software krijgt steeds meer een rol in AM-workflow
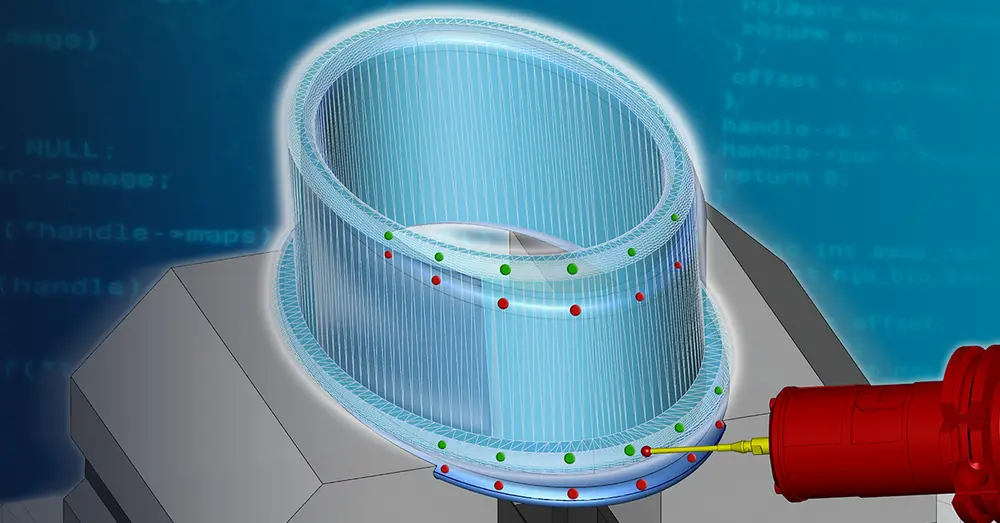
Additive manufacturing is een digitale productietechnologie, en dus is het logisch dat software een belangrijke rol speelt. Dat geldt overigens niet alleen voor het aansturen van de machine zelf, maar vooral daar buiten: werkvoorbereiding en simulatie én na het printen integratie met post-processing. Met name de software uit de eerste groep moet zorgen voor 'first time right' in additive manufacturing, bij metaal tot nog toe een droom.
3D-metaalprinten blijft een moeilijk proces, met name wat betreft de bekendste technologie, het Laser Powderbed Fusion (LPBF), of laserpoederbedprinten. Het grootste probleem bij laserpoederbed-3D-metaalprinten is de vervorming van het metaal. Dat komt doordat het eerst uitzet onder invloed van de warmte die met de laser wordt ingebracht en vervolgens relatief snel weer krimpt tijdens het afkoelen.
Dat kan zowel tot vervormingen als spanningen leiden. Beide zijn ongewenst in een complex en kritisch werkstuk. Supportstructuren zijn de oplossing om extra warmte af te voeren om dit probleem te minimaliseren. Zo’n structuur moet echter geprint worden en kost dus extra materiaal en printtijd. Daarna moet de structuur verwijderd worden wat eveneens tot meerkosten leidt. Supportstructuren zijn een kostenfactor bij additive manufacturing.
Open versus gesloten
De AM-industrie zoekt daarom naar andere oplossingen, met name softwaregedreven. Vaak zitten basissupportfeatures in de slicersoftware, waarmee men primair de laserbanen berekent en de supports plant. De keuze voor slicersoftware is relatief beperkt.
Ofwel ontwikkelen de fabrikanten van de 3D-metaalprinters hun eigen slicersoftware (bijvoorbeeld EOS met EOSprint, Renishaw met QuantAM en 3D Systems met 3DXpert) of ze kiezen voor een merkonafhankelijk pakket, vaak Magics van het Belgische Materialise. Magics kan zowel met CAD als mesh omgaan. Dit is de software voor de werkvoorbereiding van een buildjob.
De vraag die de koper van een 3D-metaalprinter zichzelf moet stellen is: wil hij een open of gesloten systeem?
Deze software genereert de scanstrategie, maar ook de optimale positionering op de bouwplaat, supportstrategie, infillpratronen als men een ruimte in het werkstuk niet volledig wil vullen om gewicht te besparen of printtijd te verkorten. En deze software wordt gebruikt voor het nesten van onderdelen in een buildjob.
De vraag die de koper van een 3D-metaalprinter zichzelf moet stellen is: wil hij een open of gesloten systeem? Gesloten software werkt alleen met de hardware van de machinefabrikant, open systemen zijn merkonafhankelijk. Elk heeft zijn eigen voor- en nadelen.
VOOR- en nadelen
Het voordeel van gesloten is dat de fabrikant de software specifieke features mee kan geven voor zijn eigen hardware en dat alles precies op elkaar is afgestemd.
Open betekent dat de software meer generiek moet zijn en het veel ervaring vergt om de machine te gaan finetunen. Tegenwoordig zijn er zowel startups als gevestigde partijen die bewust voor een open strategie kiezen en cloudgebaseerde software ontwikkelen die met meerdere systemen werkt.
Kunstmatige Intelligentie speelt hierin doorgaans een rol, vandaar de keuze voor cloudgebaseerde oplossingen. Oqton, het software platform van 3D Systems is hier een voorbeeld van. Na de acquisitie van het oorspronkelijk Belgische platform heeft 3D Systems gekozen voor een open strategie.
Ook de buildjobs op andere 3D-metaalprinters dan die van 3D Systems kunnen met Oqton voorbereid en gemonitored worden. Daarmee wil men de toepassing van additive manufacturing versnellen.
Simulatietools
Zoals gezegd is vervorming door het thermisch gedrag hét probleem bij LPBF-metaalprinten. Een van de manieren waarop de AM-industrie dat probeert te vermijden, is door het printproces vooraf te simuleren. In een virtuele omgeving, tegenwoordig een digitale tweeling van de metaalprinter met bijbehorende parametersettings, wordt het 3D-printproces laag voor laag nagebootst.
Dat gebeurt dankzij de hedendaagse rekenkracht van computers veel sneller dan het 3D-printen zelf. De uitkomst van deze simulatie is dat men een beeld krijgt waar het werkstuk gaat vervormen en er teveel spanningen ontstaan. Door de oriëntatie aan te passen kan men dit verminderen. Of men plaatst supportmateriaal om de spanningen of vervormingen tegen te gaan. De derde mogelijkheid met de nieuwste software is het design aanpassen.
Men gaat compenseren voor de vervorming met als eindresultaat dat het werkstuk qua geometrie heel dicht bij het gewenste eindresultaat zit of hiermee overeenstemt. Dat is een wezenlijke succesfactor voor 3D-metaalprinten van kritische componenten.
Het is dan ook niet verwonderlijk dat softwareontwikkelaars voor de maakindustrie, denk aan Siemens, Dassault Systemès en Hexagon, hier volop op inzetten. Ze zoeken allemaal naar de heilige graal voor first time right bij 3D-metaalprinten om daarmee de ontwikkelingstijd van een nieuwe applicatie te verkorten.
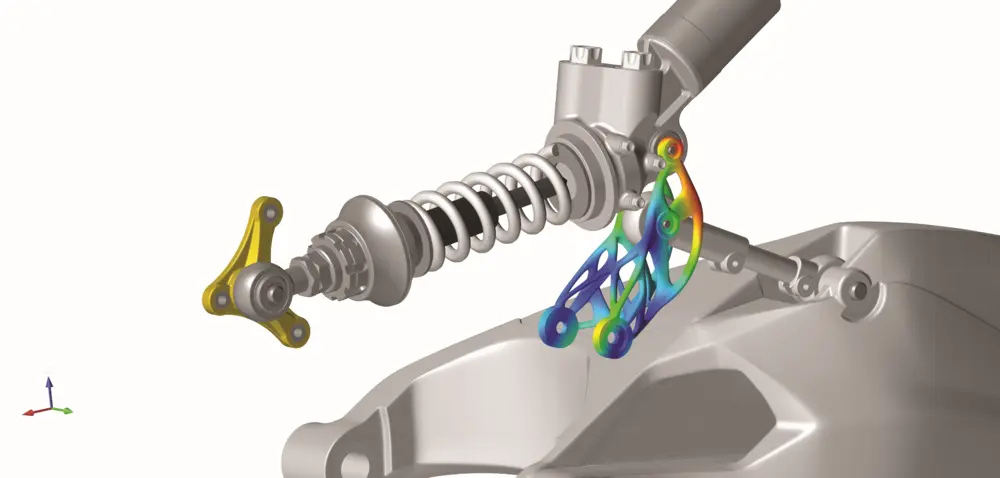
Verbreding van pakketten
De ontwikkelaars van deze software zitten niet stil. Sommigen richten hun aandacht volledig op het simuleren van de vervorming en proberen hier het rendement te maximaliseren. Anderen zoeken het juist in de verbreding en nemen ook andere aspecten in hun simulatie mee, zoals een voorspelling van de porositeit en de microstructuur of de sterkte en de structurele stabiliteit van het werkstuk na het 3D-printen.
Meestal zijn dit modules in het softwarepakket die men erbij kan kopen als ze echt nodig zijn. Topologie-optimalisatie is een ander aspect dat men graag in dit stadium meeneemt. Het heeft immers zin om als het design klaar is en voordat men gaat 3D-printen te analyseren of ergens materiaal kan worden weggelaten zonder dat de eigenschappen van het werkstuk in gevaar komen.
Bij 3D-printen betekent materiaal toevoegen altijd dat de kosten hoger worden
Bij 3D-printen betekent materiaal toevoegen immers altijd dat de kosten hoger worden. De software berekent mathematisch waar materiaal nodig is om belastingen en sterktes te halen die nodig zijn voor de functie. Bij de meeste pakketten kan men zelf de grenzen aan het weglaten van materiaal ingeven door constraints in te geven.
Een voorbeeld van topologie-optimalisatie is nTop, wat onder andere gebruikt wordt voor het snel ontwerpen van mallen en opspanhulpmiddelen. De ontwikkelaars hebben het design verregaand geautomatiseerd door het model dat opgespannen moet worden als uitgangspunt te nemen.
Met slechts een beperkt aantal instellingen creëert de software het ontwerp. Hierdoor is de pasvorm van gaten altijd goed. In de nieuwste versie van de software gaat men steeds verder richting het optimaliseren van de print.
Kwaliteit voorspellen
Andere gaan zover dat met de software de simulatie de kwaliteit van het werkstuk voorspelt en men zo simulatie gebaseerd het AM-proces kan valideren. Men ziet dat met name in de lucht- en ruimtevaart deze geavanceerde simulatie software snel zijn weg vindt naar de gebruikers. Begrijpelijk, omdat het hier vaak om grote werkstukken gaat die kostbaar zijn om te 3D printen.
Daarnaast speelt tijd een rol mee. Soms is de 3D metaalprinter meer dan een week bezig met het 3D printen van één grote componenten. Dan wil men zo min mogelijk via trial and error de juiste instellingen vinden. Om de nauwkeurigheid van de simulaties te verhogen kalibreren de ontwikkelaars hun simulatiemodellen met real live data van testen die ze doen. Machine learning speelt hierin een grote rol, net als bij andere software voor kwaliteitscontrole.
Om niet elk geprint onderdeel afzonderlijk na te meten zijn er systemen die de onderdelen automatisch scannen en deze data vergelijken met die van het CAD-model. Hier wordt veel gebruik gemaakt van Kunstmatige Intelligentie.
Daarnaast worden deze data inmiddels direct doorgestuurd naar andere software in het maakproces, bijvoorbeeld de aansturen van de 3D printers. Op die manier willen de fabrikanten aan closed loop proces creëren en de yield in de additieve productie verhogen.
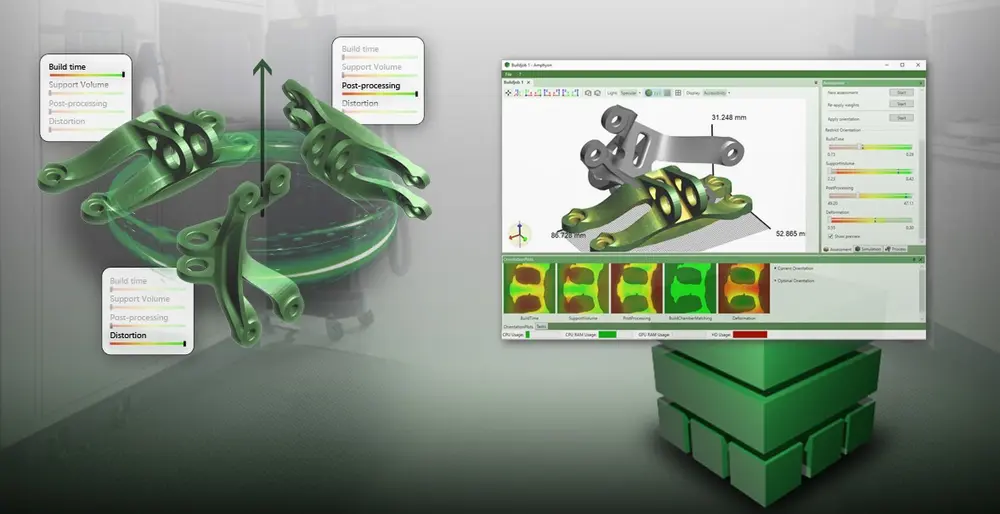
Een van de aanbieders van geïntegreerde software voor het AM proces is het van oorsprong Belgische Oqton, tegenwoordig onderdeel van 3D Systems. Naast het execution platform biedt het verschillende opties aan om de onderdelen van het AM-proces bij te sturen of te managemen. Hier horen onder andere 3DXpert en Additive Works Amphyon bij. Het eerste is een CAM-pakket voor zowel het programmeren van de 3D metaalprinter als de nabewerking, het tweede is simulatie software om vervormingen tijdens het metaalprinten te vermijden
Integratie post-processing
Bijna alle 3D-metaalgeprinte werkstukken hebben nog een of andere nabewerking nodig. Vaak is dat CNC-frezen, -draaien of -slijpen om de nauwkeurige vlakken aan te brengen. Tot voor kort had men hiervoor twee verschillende softwarepakketten nodig. Het programmeren van een CNC-machine voor het frezen van een AM-werkstuk gebeurt meestal in een ander pakket dan het printproces zelf voorbereiden.
Stap voor stap groeit het aantal CAM-ontwikkelaars dat de beide bewerkingen integreert in één CAM-pakket. Voor het eerst wordt dat gedaan voor de DED-technologieën (Direct Energy Deposition, het oplassen). Sinds enkele jaren kan men voor onder andere WAAM de bewerkingen helemaal in één keer samen met de CNC-bewerking programmeren.
Dat juist deze oplossing als eerste werd ontwikkeld, heeft te maken met de hybridemachines waarin men kan 3D-metaalprinten én mechanisch nabewerken in dezelfde opspanning. Hiervoor is deze geïntegreerde software noodzakelijk.
Er zijn ook ontwikkelaars die voor laserpoederbed-AM-systemen een volledige oplossing aanbieden maar dan worden de metaalprinter en de CNC-machine wel nog in twee aparte omgevingen geprogrammeerd. Die zijn wel aan elkaar gekoppeld. Stel dat bij de werkvoorbereiding van een buildjob een supportstructuur wordt verwijderd, dan verdwijnt die eveneens in de software voor het programmeren van de nabewerking. Voor het merendeel van de AM-stukken blijft men voor het nabewerken aangewezen.
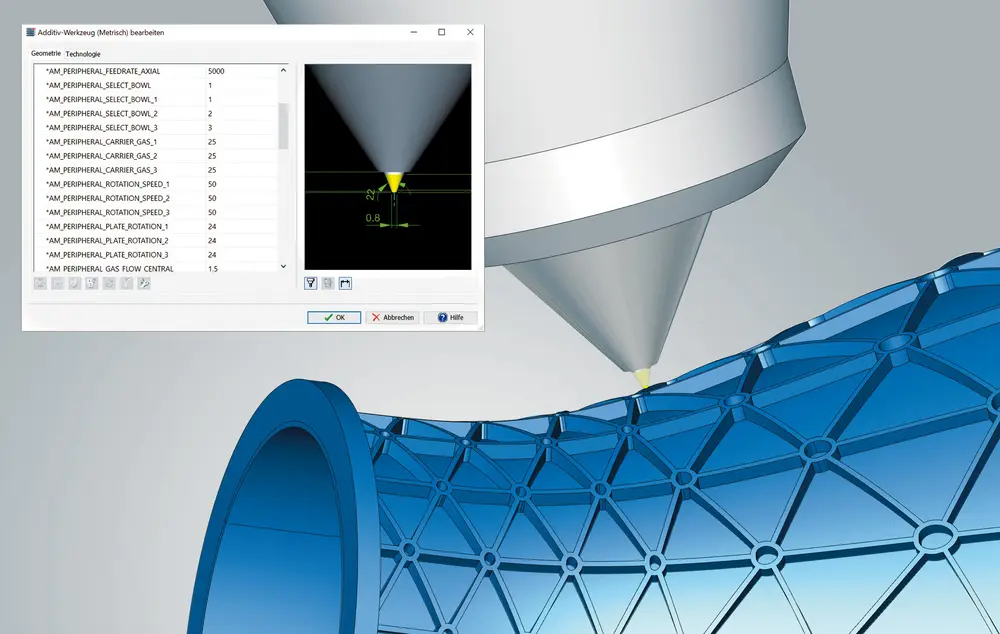