Le rôle croissant du logiciel dans le processus de FA
Le logiciel joue un rôle de plus en plus important dans le flux de travail de la fabrication additive
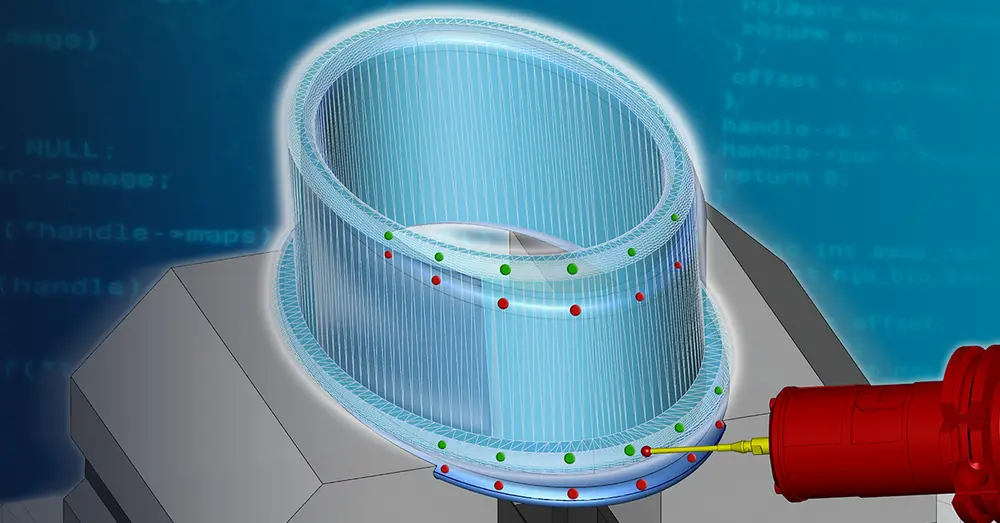
La fabrication additive est une technologie de production numérique, il est donc logique que le logiciel y joue un rôle important. Cela s'applique non seulement à la commande de la machine proprement dite, mais aussi à l'extérieur de celle-ci: préparation et simulation du travail et, après l'impression, intégration avec le post-traitement. Les logiciels du premier groupe, en particulier, doivent garantir le 'first time right' dans la fabrication additive, ce qui n'est encore qu'un rêve dans le cas du métal.
L'impression 3D métal reste un processus difficile, en particulier en ce qui concerne sa technologie la plus connue, la Laser Powderbed Fusion (LPBF), ou impression laser sur lit de poudre. Le principal problème de l'impression 3D métal sur lit de poudre laser est la distorsion du métal. En effet, celui-ci se dilate d'abord sous l'effet de la chaleur introduite par le laser, puis se rétracte relativement vite lors du refroidissement.
Cela peut entraîner des déformations et des tensions. Ces deux phénomènes ne sont pas souhaitables dans une pièce complexe et critique. Les structures de support constituent une solution pour dissiper la chaleur supplémentaire et minimiser ce problème. Cependant, ce genre de structure doit être imprimée, ce qui entraîne des coûts supplémentaires en termes de matériau et de temps d'impression. Ensuite, la structure doit être retirée, ce qui entraîne également des coûts supplémentaires. Les structures de support constituent un facteur de coût dans la fabrication additive.
Ouvert ou fermé
L'industrie de la FA recherche donc d'autres solutions, en particulier des solutions logicielles. Souvent, les fonctions de support de base se trouvent dans le logiciel de tranchage, qui est principalement utilisé pour calculer les trajectoires du laser et planifier les supports. Le choix du logiciel de tranchage est relativement limité.
Soit les fabricants d'imprimantes 3D métal développent leur propre logiciel de tranchage (par exemple EOS avec EOSprint, Renishaw avec QuantAM et 3D Systems avec 3DXpert), soit ils optent pour un logiciel indépendant de la marque, souvent Magics de la société belge Materialise. Magics peut gérer à la fois la CAO et le maillage. Il s'agit du logiciel de préparation du travail pour un projet de construction.
La question que doit se poser l'acheteur d'une imprimante 3D métal est la suivante: veut-il un système ouvert ou fermé?
Ce logiciel génère la stratégie de numérisation, mais aussi le positionnement optimal sur la plaque de construction, la stratégie de support, les motifs de remplissage si l'on ne veut pas remplir complètement une partie de la pièce pour gagner du poids ou réduire le temps d'impression. Ce logiciel est également utilisé pour l'imbrication des pièces dans un travail de construction.
La question que doit se poser l'acheteur d'une imprimante 3D métal est la suivante: veut-il un système ouvert ou fermé? Les logiciels fermés ne fonctionnent qu'avec le matériel du fabricant de la machine, tandis que les systèmes ouverts sont indépendants de la marque. Chacun de ces systèmes présente des avantages et des inconvénients.
Avantages et inconvénients
L'avantage d'un système fermé est que le fabricant peut doter le logiciel de fonctions spécifiques pour son propre matériel et que tout est parfaitement harmonisé.
Un système fermé signifie que le logiciel doit être plus générique et qu'il faut beaucoup d'expérience pour régler la machine avec précision. Aujourd'hui, des start-ups et des acteurs établis choisissent délibérément une stratégie ouverte et développent des logiciels basés sur le cloud qui fonctionnent avec plusieurs systèmes.
L'intelligence artificielle joue généralement un rôle à cet égard, d'où le choix de solutions basées sur le cloud. Oqton, la plateforme logicielle de 3D Systems, en est un exemple. Après avoir acquis la plateforme belge, 3D Systems a opté pour une stratégie ouverte.
Les projets de construction sur des imprimantes 3D métal autres que celles de 3D Systems peuvent également être préparés et contrôlés avec Oqton. L'objectif est d'accélérer l'adoption de la fabrication additive.
Outils de simulation
Comme nous l'avons mentionné, la déformation due au comportement thermique est le problème numéro un de l'impression métal LPBF. L'une des façons dont l'industrie de la FA tente d'éviter ce problème est de simuler le processus d'impression à l'avance. Le processus d'impression 3D est simulé couche par couche dans un environnement virtuel, qui est un jumeau numérique de l'imprimante métal avec les paramètres correspondants.
Grâce à la puissance de calcul des ordinateurs actuels, cette simulation est beaucoup plus rapide que l'impression 3D proprement dite. Le résultat de cette simulation est une image de l'endroit où la pièce va se déformer et où des contraintes excessives vont se produire. Il est possible de réduire ces problèmes en ajustant l'orientation. On peut aussi placer un support pour contrecarrer les contraintes ou les déformations. La troisième possibilité offerte par les logiciels les plus récents consiste à adapter le design.
On compense la déformation, ce qui permet d'obtenir une pièce dont la géométrie est très proche ou similaire à celle du résultat final souhaité. Il s'agit d'un facteur de réussite essentiel pour l'impression 3D de composants critiques.
Il n'est donc pas surprenant que les développeurs de logiciels pour l'industrie manufacturière, tels que Siemens, Dassault Systemès et Hexagon, s'engagent pleinement dans cette voie. Ils sont tous à la recherche du Saint-Graal du first time right pour l'impression 3D de pièces métalliques afin de réduire le temps de développement d'une nouvelle application.
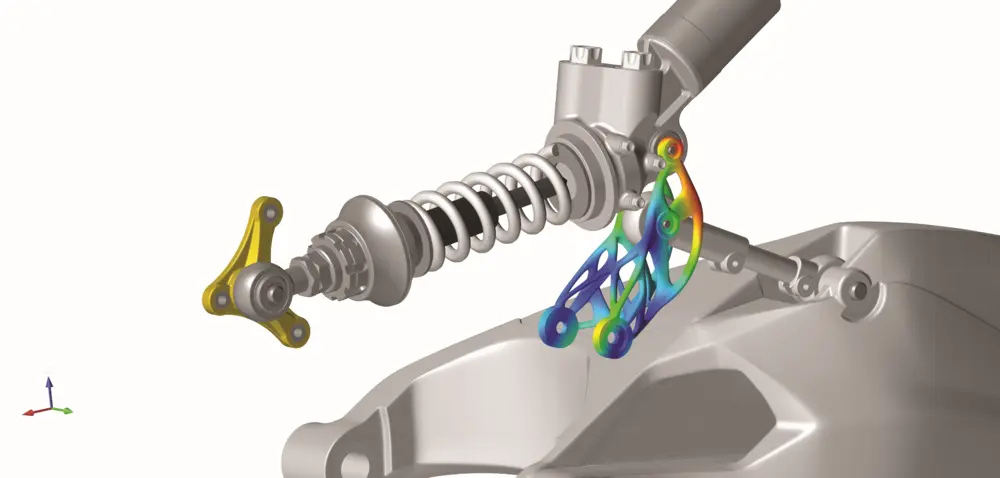
Élargissement des offres
Les développeurs de ces logiciels ne restent pas les bras croisés. Certains se concentrent entièrement sur la simulation de la déformation et tentent de maximiser l'efficacité dans ce domaine. D'autres, au contraire, cherchent à élargir leur champ d'action et incluent d'autres aspects dans leur simulation, comme la prédiction de la porosité et de la microstructure ou la résistance et la stabilité structurelle de la pièce après l'impression 3D.
En général, il s'agit de modules dans le logiciel que l'on peut acheter en plus s'ils sont vraiment nécessaires. L'optimisation de la topologie est un autre aspect que l'on aime inclure à ce stade. En effet, une fois que la conception est prête et avant l'impression 3D, il est logique d'analyser s'il est possible d'enlever de la matière quelque part sans compromettre les propriétés de la pièce.
Dans le cas de l'impression 3D, l'ajout de matériau est toujours synonyme d'augmentation des coûts
En effet, dans l'impression 3D, l'ajout de matériau est toujours synonyme d'augmentation des coûts. Le logiciel calcule mathématiquement où le matériau est nécessaire pour atteindre les charges et les résistances requises pour la pièce. La plupart des logiciels vous permettent de fixer vos propres limites à cet égard en entrant des contraintes.
Un exemple d'optimisation topologique est nTop, qui est utilisé pour la conception rapide de gabarits et d'accessoires de serrage, entre autres. Les développeurs ont largement automatisé la conception en utilisant le modèle à fixer comme point de départ.
Avec un nombre limité de paramètres, le logiciel crée le projet. Ainsi, l'ajustement des trous est toujours correct. La dernière version du logiciel va toujours plus loin dans l'optimisation de l'impression.
Prédire la qualité
D'autres vont même jusqu'à dire qu'avec le logiciel, la simulation prédit la qualité de la pièce à usiner, ce qui permet de valider les processus de FA basés sur la simulation. On constate qu'en particulier dans l'aérospatiale, ces logiciels de simulation avancés trouvent rapidement leur chemin vers les utilisateurs. C'est compréhensible car il s'agit souvent de pièces de grande taille qui sont coûteuses à imprimer en 3D.
En outre, le temps joue un rôle. Il faut parfois plus d'une semaine à l'imprimante 3D métal pour imprimer en 3D une grande pièce. Il s'agit donc de trouver les bons réglages en procédant le moins possible par essais/erreurs. Afin d'accroître la précision des simulations, les développeurs étalonnent leurs modèles de simulation à l'aide de données réelles issues des tests qu'ils effectuent. L'apprentissage automatique joue un rôle important à cet égard, comme dans d'autres logiciels de contrôle de la qualité.
Pour éviter de mesurer chaque pièce imprimée individuellement, il existe des systèmes qui scannent automatiquement les pièces et comparent ces données avec celles du modèle CAO. C'est là que l'intelligence artificielle est largement utilisée.
En outre, ces données sont désormais directement transmises à d'autres logiciels du processus de fabrication, par exemple le contrôle des imprimantes 3D. Les fabricants souhaitent ainsi créer des processus en boucle fermée et augmenter les rendements de la fabrication additive.
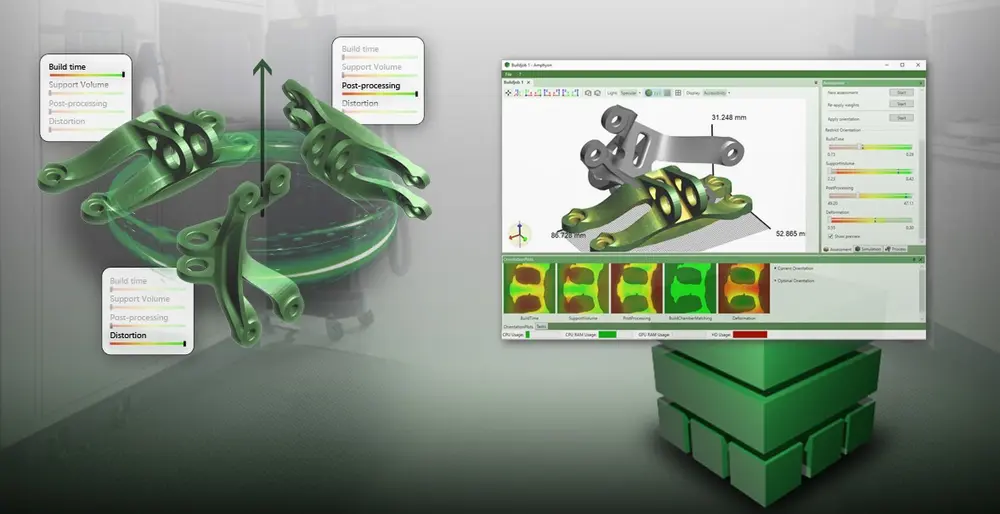
L'un des fournisseurs de logiciels intégrés pour le processus de fabrication additive est l'entreprise belge Oqton, qui fait aujourd'hui partie de 3D Systems. Outre sa plateforme d'exécution, elle propose diverses options pour ajuster ou gérer les composants du processus de fabrication additive. Il s'agit notamment de 3DXpert et d'Additive Works Amphyon. Le premier est un logiciel de FAO pour la programmation et le post-traitement des imprimantes 3D métal, le second est un logiciel de simulation permettant d'éviter les déformations pendant l'impression métal
Intégration du post-traitement
Presque toutes les pièces imprimées en 3D sur métal nécessitent encore un certain type de post-traitement. Il s'agit souvent d'un fraisage, d'un tournage ou d'un meulage CNC pour appliquer des surfaces précises. Jusqu'à récemment, ces opérations nécessitaient deux logiciels différents. La programmation d'une machine CNC pour le fraisage d'une pièce de FA s'effectue généralement dans un autre logiciel que la préparation du processus d'impression lui-même.
Petit à petit, le nombre de développeurs de logiciels de FAO qui intègrent les deux opérations dans un seul logiciel de FAO augmente. Pour la première fois, cela se fait pour les technologies DED (Direct Energy Deposition). Depuis plusieurs années, pour WAAM, entre autres, il est possible de programmer les opérations en une seule fois en même temps que l'opération CNC.
Le fait que cette solution ait été la première à être développée est lié aux machines hybrides dans lesquelles l'impression 3D métal et la finition mécanique peuvent être réalisées dans le même dispositif. Pour cela, il faut ce logiciel intégré.
Certains développeurs proposent également une solution complète pour les systèmes de FA sur lit de poudre laser, mais l'imprimante métal et la machine CNC sont toujours programmées dans deux environnements distincts. Elles sont toutefois liées l'une à l'autre. Si une structure de support est retirée pendant la préparation d'un travail de préparation, elle disparaît également dans le logiciel de programmation de post-traitement. Pour la majorité des pièces fabriquées par FA, on continue de s'appuyer sur le post-traitement.
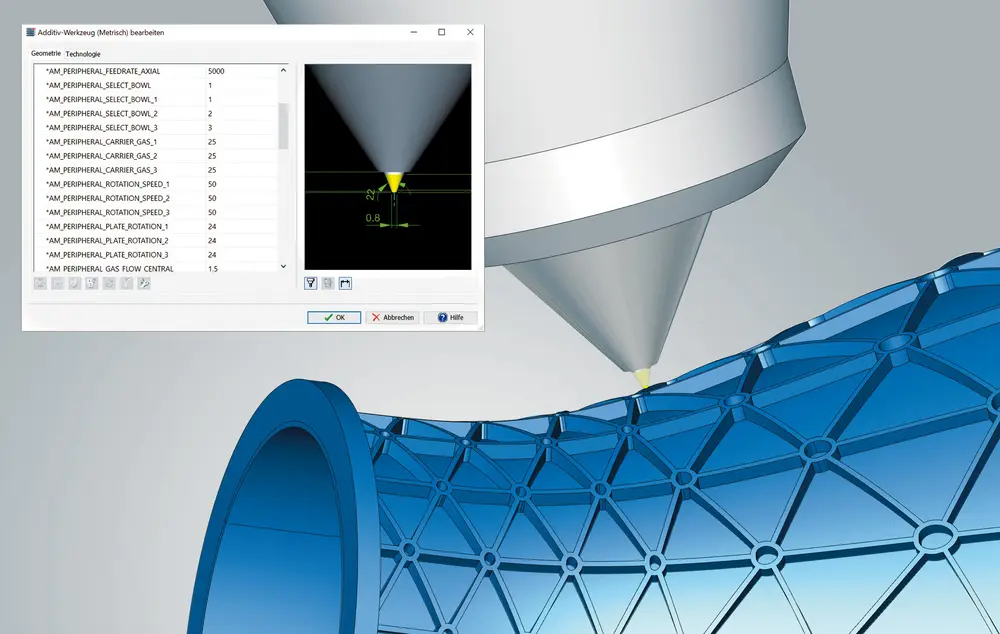