“Technologie zit verweven in onze mensen”
geert ostyn over ‘let’s make it together’ bij Picanol
Een naam als een klok … dat is het minste wat we kunnen zeggen over Picanol Group. De grootste weefmachinebouwer ter wereld, een voorloper in innovatie én bovendien stevig verankerd in de Ieperse grond. Wij vroegen ons af hoe een dergelijk imposant bedrijf de principes van Factory of the Future in de praktijk brengt. Geert Ostyn, senior vice president Business Transformation & Strategic Alignment van het bedrijf, gaf ons het antwoord.
Factory of the Future Award?
We kunnen Picanol Group met recht en reden benoemen als een bedrijf dat volop in de geest van Factory of the Future opereert. Toch beschikt de onderneming vooralsnog niet over een Factory of the Future Award. Geert Ostyn vertelt ons waarom: “Ikzelf ben al langer actief binnen alles wat met manufacturing te maken heeft binnen Agoria. Ik zat dus op de eerste rij toen het ‘Made Different’-programma opgesteld werd. Picanol was zelfs een van de testbedrijven die een doorlichting kreeg aan de hand van de 7 transformaties. We zijn ook een inspiratiebron geweest voor meerdere bedrijven die ondertussen een award konden binnenhalen. Voor ons zitten twee belangrijke voorwaarden de certificering wat in de weg: je moet op elk van die 7 transformaties een score van 4 op 5 halen én het moet over de volledige groep zijn. Voor ons is dat niet aan de orde, want we bestaan uit meerdere bedrijven (zie kaderstuk verderop) en we beschikken hier bovendien over het complete palet: we hebben de complete ontwikkeling, productie en aftermarket zelf in handen. Bovendien zijn er ook nog de onderlinge logistieke processen via de andere bedrijven uit de groep zoals Proferro en Psicontrol. Ook zij hebben op hun beurt dat complete proces in huis. Structureel is het daarom zeer moeilijk om over de complete groep een dergelijke award binnen te halen.”
‘Let’s make it together’
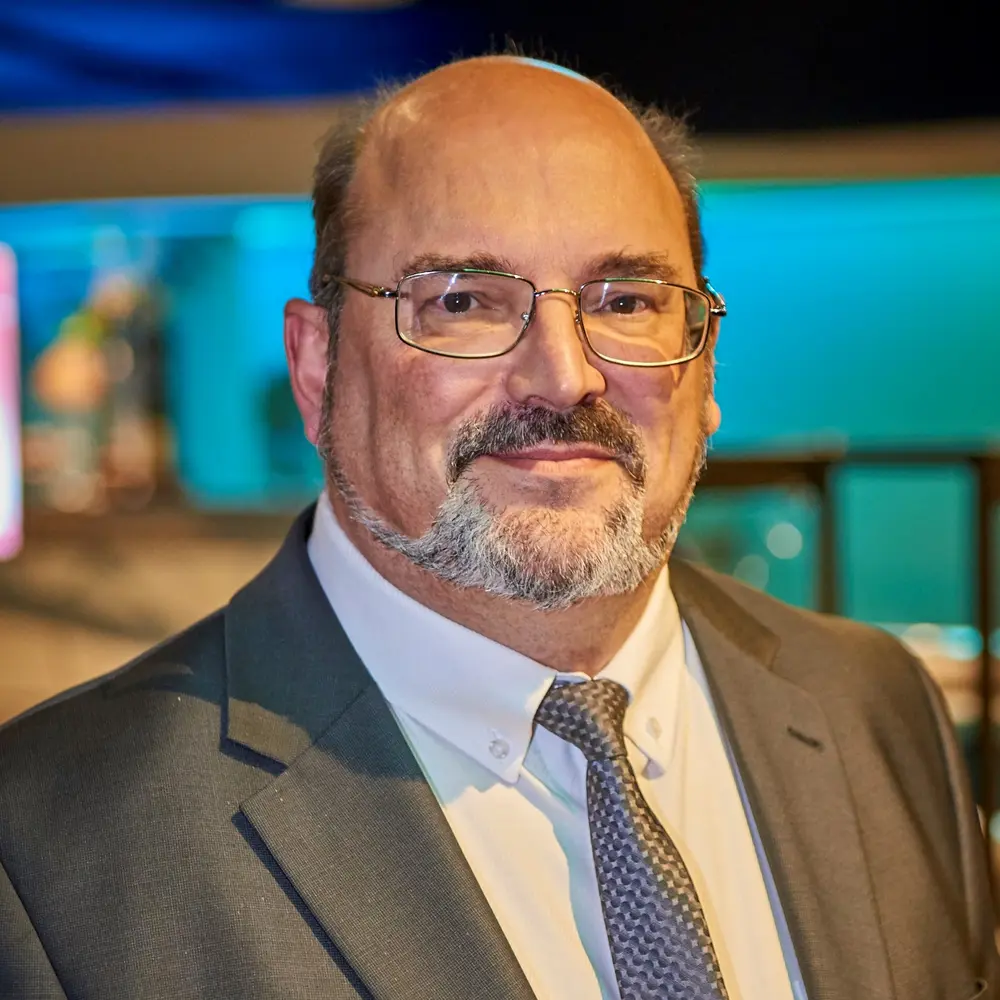
SVO Business Transformation & Strategic Alignment Picanol
“Maar dat betekent niet dat we het Factory of the Future-programma niet gebruiken. Meer nog: de transformaties waren de inspiratie voor het opstellen van een eigen insteek. Ons eigen intern programma heet ‘Let’s make it together’. De bedoeling hiervan is om de toekomst van de Picanol Group in Ieper te verankeren. Loonkost en een tekort aan technisch geschoolde arbeidskrachten zijn twee belangrijke handicaps in onze contreien. Met dit programma willen we deze hinderpalen counteren. We werken daarbij met drie belangrijke pijlers: World Class Manufacturing, Digital Factory en Human Centered Organisation. Die monden uit in wat wij een smart company noemen.”
“Drie jaar terug zijn we gestart met dat programma. Dat neemt niet weg dat we daarvoor ook al bezig waren met deze transformaties. Zo werd er al volop geïnvesteerd in digitalisering en is de focus op de mens hier altijd al belangrijk geweest. We hebben dus die drie pijlers niet echt gekozen, het was eerder een logisch gevolg van de realiteit.”
“Als we deze pijlers fileren zien we dat ze onderling sterk verweven zijn, met kwaliteit als de rode draad. Zo investeerden we onlangs volop in het machinepark: we beschikken over 50 volledig up-to-date CNC-machines en diverse robots bemannen de werkvloer. Ook het digitale aspect kwam aan bod in die investeringsronde: er kwamen tablets, het netwerk werd uitgebouwd en er werden productconfiguratoren ontwikkeld. Ook de uitbouw van MES-, EMS- en WMS-systemen stip ik graag aan. Maar ook in infrastructuur en veiligheid deden we aanzienlijke investeringen. Het is vaak moeilijk om de ROI daarvan te berekenen, maar het is wel belangrijk in de mindset van de mensen. Wie ziet dat zijn werkgever in pakweg nieuwe toiletten of een refter investeert weet: dit bedrijf is ‘here to stay’.”
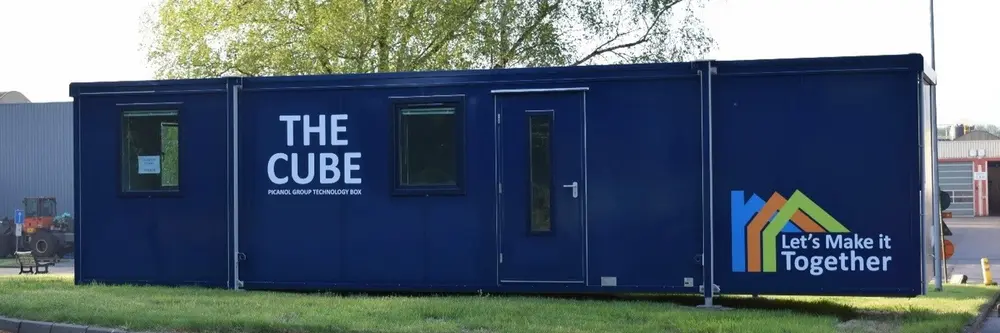
Technologiecontainer verlaagt drempelvrees
Dat brengt ons naadloos bij human centered production. Hoe pakt Picanol dat aan?
Geert Ostyn: “Ondertussen hebben we al meerdere deelprojecten rond dat aspect uitgevoerd. Een mooi voorbeeld is onze Cube. Uit een bevraging bleek dat onze werknemers veel vragen hadden over technologie. Zo wist 85% niet wat een 3D-printer was. Daarom zochten we een manier om hen meer vertrouwd te maken met dergelijke innovaties. Het resultaat was de Cube, een container waarin naast een 3D-printer ook een zorgrobot, een AR/VR-toepassing, een cobot en een exoskeleton getoond worden. Iedereen kreeg de gelegenheid om de Cube te bezoeken tijdens de werkuren. Het is voor alle duidelijkheid geen opleidingstool; sommige van deze technologieën worden zelfs niet gebruikt bij ons. Exoskeletons hebben we bijvoorbeeld wel uitgeprobeerd, maar dat is voorlopig even on hold gezet, omdat we eerst enkele praktische zaken willen aangepast zien: het makkelijk uittrekken bijvoorbeeld en het snel kunnen herinstellen als er een andere operator met het exoskelet aan de slag gaat. Binnen enkele jaren zijn ze wellicht wél inzetbaar in onze setting. Is dat traject dan verloren moeite geweest? Totaal niet. We hebben er ten eerste enorm veel uit geleerd én ten tweede: onze mensen voelen dat we hun gezondheid ter harte nemen.”
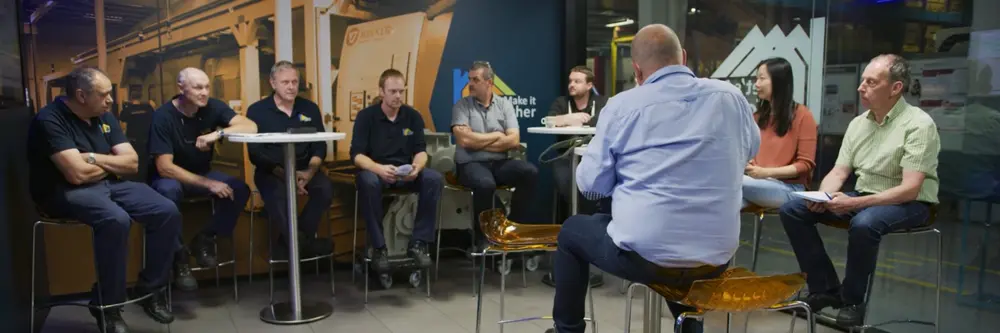
Dat zorgt voor onderlinge interactie en laat toe om weloverwogen actie te ondernemen
Technologiefora & V-box
“Een ander voorbeeld van die betrokkenheid vormen onze technologiefora. Als een investering afgerond is, geven de operatoren een demonstratie van de technologie – AVG’s bijvoorbeeld – aan geïnteresseerde collega’s. Daar komen telkens een 30-tal mensen op af, ook medewerkers uit pakweg HR of finance. Het bevordert de onderlinge verstandhouding enorm en het geeft aan dat ‘human centered’ en ‘world class manufacturing’ hier sterk doorweven zijn. Een ander goed voorbeeld is de V-box. Daarin kunnen werknemers alle relevante en recente data bespreken. Dat zorgt voor meer onderlinge interactie en laat toe om weloverwogen de nodige acties te ondernemen. Dat moment vindt enkele keren per dag plaats. Ook hier geldt terug dat de ROI van dergelijke zaken moeilijk te berekenen valt: 80% van de tijd is die box leeg. Als je dezelfde criteria zou hanteren zoals bij machines, geeft de ROI een compleet verkeerd beeld. Wie enkel door de kosten gedreven wordt, zal een aantal belangrijke zaken over het hoofd zien.”
Technologische roadmap
Picanol zien we wel vaker opduiken in allerlei onderzoeken i.s.m. organisaties als Flanders Make en de universiteiten.
“Uiteraard volgen we met argusogen de technologische innovaties. We willen een digitale fabriek uitbouwen en analyseren welke technieken het best aansluiten bij waar wij naar toe willen. Wij spreken in dat opzicht intern van een core- of een keyverhaal. In een coreverhaal ontwikkelen wij zelf de technologie in huis, daarmee maken we echt het verschil. Bij een keyverhaal zijn er andere organisaties beter geplaatst om de technologie te ontwikkelen en gaan we op zoek naar samenwerkingen, zoals dat gebeurt in ICON-projecten.”
Hoe bepalen?
“Innovatie kent 2 benaderingen. In een eerste geval ervaart een afdeling een zekere nood en gaat op zoek naar oplossingen. De technologie is vervolgens enkel in die afdeling beschikbaar. De hiërarchische leiding van die afdeling beschouwt het vaak niet als hun taak om die innovatie breder te trekken naar andere afdelingen binnen het bedrijf. Een tweede benadering bestaat eruit om mensen bewust te maken van technologie, hen zelf te doen nadenken over hoe wij innovaties kunnen inzetten. Daarom tonen we hen ook technologie in de Cube. Onze mensen moeten voelen dat ze mogen experimenteren, we willen ze daarin stimuleren door hen vertrouwd te maken met technologie. De nieuwe generaties zijn ook vragende partij om te kunnen experimenteren.”
Serieproductie met klantspecifieke eisen
“Het is een vraag waar meerdere bedrijven mee worstelen: op welke technologie moet je inzetten? Wij proberen onze technologische scope zo breed mogelijk te houden, om snel te kunnen schakelen als dat nodig is. We worden ook geconfronteerd met steeds kleinere reeksen. Dat ervaren we al sinds de bankencrisis in 2008. Toen worstelden bedrijven met een beperktere liquiditeit, omdat stocks overal vastzaten. De lessen die wij daaruit getrokken hebben, is dat we ons leveranciersnetwerk anders moeten benaderen zodat we snel kunnen schakelen. Nu zijn we aangepast aan die kleinere reeksen. We produceren niks op stock. Alles wat vandaag gemaakt wordt, is binnen de drie dagen vertrokken naar de klant. Onze productie is zo opgebouwd dat we pas op het einde van de lijn de klantspecifieke features aanbrengen. Zo blijft de prijs onder controle, maar kunnen we ook de broodnodige toegevoegde waarde aanbieden. Ook het plaatselijke netwerk is zeer belangrijk in onze verankering in België. Zonder de universiteiten, kennisorganisaties en plaatselijke kmo’s zou dat zeer moeilijk zijn. Zo zijn we sterk actief in Flanders Make, waar we samenwerken met andere bedrijven. We hebben momenteel ook projecten lopen met 4 van onze universiteiten. Die kruisbestuiving levert veel meer op dan enkel wat er in het project bereikt wordt. Je leert andere mensen en bedrijven kennen, en dat laat toe om in latere samenwerkingen meteen resultaat te boeken.”