Innovations continues dans le protocole IO-Link
Plus que jamais une référence internationale
Lors de son lancement en 2008, le protocole IO-Link promettait de s'imposer comme norme de référence en matière de communication entre les machines, les plateformes de contrôle et les capteurs. Des années plus tard, le protocole est en effet utilisé partout, mais il continue en plus de veiller à fournir la meilleure solution aux entreprises qui souhaitent pousser toujours plus loin l'automatisation de leurs processus.
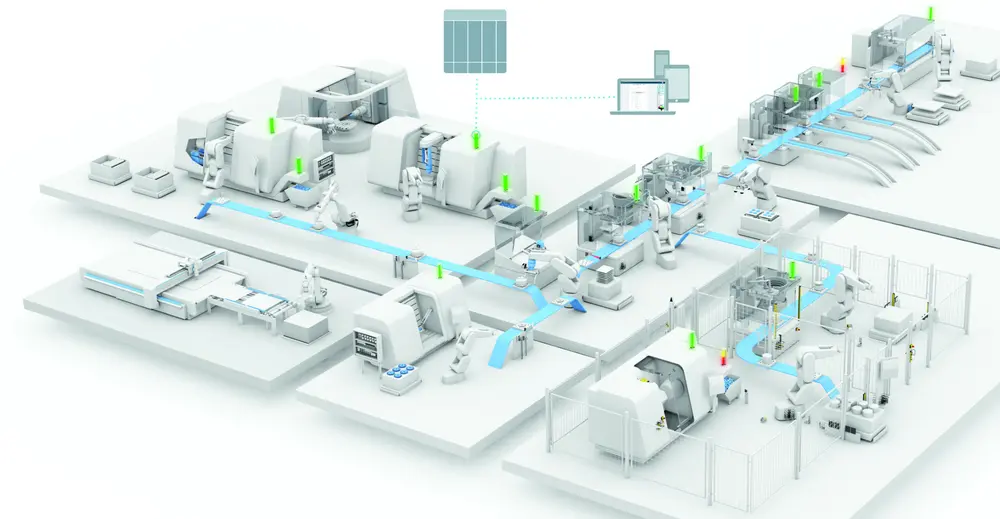
IO-Link est devenu une norme internationale en termes de communication entre les machines, les plateformes de contrôle et les capteurs (illustration: Balluff)
IO-Link, qu'est-ce que c'est?
La normalisation de la communication entre les différents composants est une condition préalable essentielle à la création d'un environnement de production rationalisé. Il existe de nombreux protocoles, mais ils sont souvent liés à des fonctions, des machines ou des marques spécifiques. Des langages différents, donc, qui peuvent mettre à mal l'automatisation des processus de production.
C'est pour remédier à ce problème qu'IO-Link a vu le jour, une technologie indépendante des fabricants. Le grand avantage de ce protocole est qu'il est largement adopté. Presque tous les grands acteurs du marché belge font partie de l'IO-Link Group Belgium, qui souhaite ainsi promouvoir le protocole en tant que norme absolue.
Comment fonctionne IO-Link? Le système point à point est conçu pour rendre le niveau de champ inférieur accessible à l'utilisateur de l'installation. Il est ainsi possible de consulter les informations sur les capteurs, les réglages des paramètres et les diagnostics, et d'évaluer ainsi de manière optimale l'état de l'installation. IO-Link implique un protocole de communication point à point bidirectionnel en série, pour la transmission des signaux et l'alimentation électrique.
Il existe de nombreux protocoles, ce qui est préjudiciable à l'automatisation des processus de production
Ce niveau inférieur de l'IO-Link se compose de deux éléments: un maître et un appareil. Le maître IO-Link est une interface avec un système de bus. La connexion entre le maître et l'appareil (ou device, en anglais) est établie par le biais d’un câble à 3 fils d’une longueur maximale de 20 mètres. Le câblage est normalisé sur la base de connecteurs M5, M8 et M12. Le maître gère la communication avec les E/S et sert de passerelle vers l'automate, le bus de terrain ou l'Ethernet. L'appareil remplit donc une fonction d'E/S et communique des données au maître.
Le maître et l'appareil peuvent échanger des données de deux manières: cyclique et acyclique. La communication cyclique est utilisée pour les informations critiques (telles qu'une mesure de position, la détection d'un objet, une mesure de pression...), tandis que la communication acyclique est généralement utilisée pour la configuration ou le diagnostic de l'appareil. Chaque appareil IO-Link est entièrement décrit par un fichier IODD. Le fichier IODD, c'est-à-dire le fichier de description de l'appareil IO-Link, est une sorte de carte d'identité de ce dernier.
Pourquoi IO-Link?
Les avantages de cette interface sont nombreux. IO-Link est parfois appelée la réponse des fournisseurs de capteurs et d'actionneurs à l'industrie 4.0, précisément parce qu'elle est indépendante des bus de terrain. Un exemple est la normalisation largement soutenue offerte par IO-Link, définie dans la norme IEC 61131-9. De nombreuses entreprises - tant des multinationales que des acteurs plus petits - proposent des composants très divers qui fonctionnent sur la base d'IO-Link.
En outre, la mise en service est très facile: les paramètres sont co-sauvegardés dans le maître et transférés automatiquement. De plus, si un capteur ou un actionneur doit être configuré, cela se fait via le maître. Les différents appareils sont ainsi configurés à partir d'un point central, sans qu'il soit nécessaire d'utiliser un logiciel dépendant de l'appareil. Les paramètres peuvent également être ajustés à la volée; aucun technicien ne doit se rendre sur place pour manipuler physiquement les appareils.
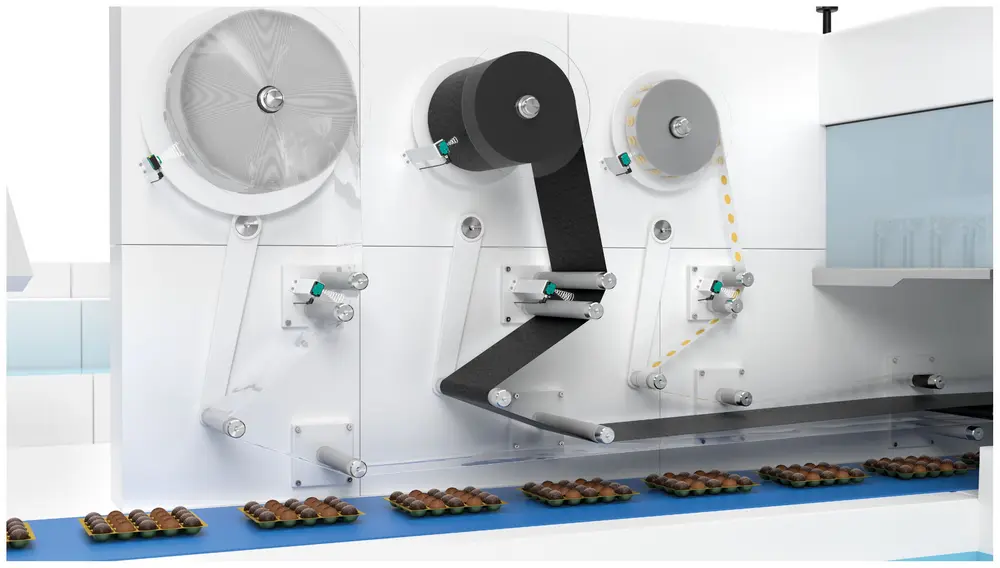
Les capacités de diagnostic étendues contribuent également à réduire les temps d'arrêt des machines, car il est facile de prendre des mesures préventives. Les capteurs génèrent de plus en plus d'informations et, grâce à IO-Link, il devient possible de traiter et de consolider le flux de données plus facilement, en se connectant directement à un automate ou même à la plate-forme MES ou ERP.
Un capteur IO-Link peut effectuer plusieurs mesures et, grâce à la communication numérique , différentes mesures peuvent être transmises à un port maître IO-Link commun. En fonction du capteur, il est donc possible d'effectuer différents types de mesures avec un seul et même capteur. Pensez à un capteur de pression qui peut également mesurer la température, ou à un capteur de position qui peut fournir des informations supplémentaires sur les vibrations. Grâce à IO-Link, on peut donc réduire le nombre de capteurs dans la machine, ainsi que le coût et l'encombrement de la machine.
Le système IO-Link, c'est aussi un concept de câblage très performant, avec des connecteurs standards et l'utilisation de concentrateurs et de commutateurs. Cela permet de réduire les coûts d'installation et de mise en service, et de simplifier l'architecture de l'ensemble de l'installation. Le risque d'erreur s'en trouve réduit.
Innovation permanente
Il y a donc de nombreuses raisons d'utiliser IO-Link, et ce depuis le lancement du protocole. Cependant, IO-Link ne reste pas inactif: de nouvelles fonctionnalités sont systématiquement ajoutées, afin que le protocole reste une arme puissante dans le monde de l'automatisation à l'avenir. Nous vous proposons un aperçu des innovations les plus importantes.
IO-Link Wireless
Les réseaux de communication sans fil sont de plus en plus utilisés pour transmettre des données entre des points critiques dans des systèmes non stationnaires. Ils réduisent les temps d'installation et l'absence de câbles réduit le risque de défaillance du câblage ou de contamination du système (par exemple dans le domaine alimentaire). IO-Link Wireless est un exemple de ce type de système de communication.
IO-Link Wireless est un protocole déterministe fiable et en temps réel pour les systèmes de contrôle dans l'automatisation industrielle. Il peut être utilisé pour transmettre des données et des signaux provenant de capteurs de commutation et de mesure et d'actionneurs simples. Les données de processus de 2 octets ou moins sont collectées et transmises au système de contrôle. Avec l'application IO-Link Wireless, les câbles traditionnels dans les applications de contrôle peuvent être complétés par des voies de transmission sans fil. Cette approche augmente la fiabilité et la flexibilité du système ainsi mis en place.
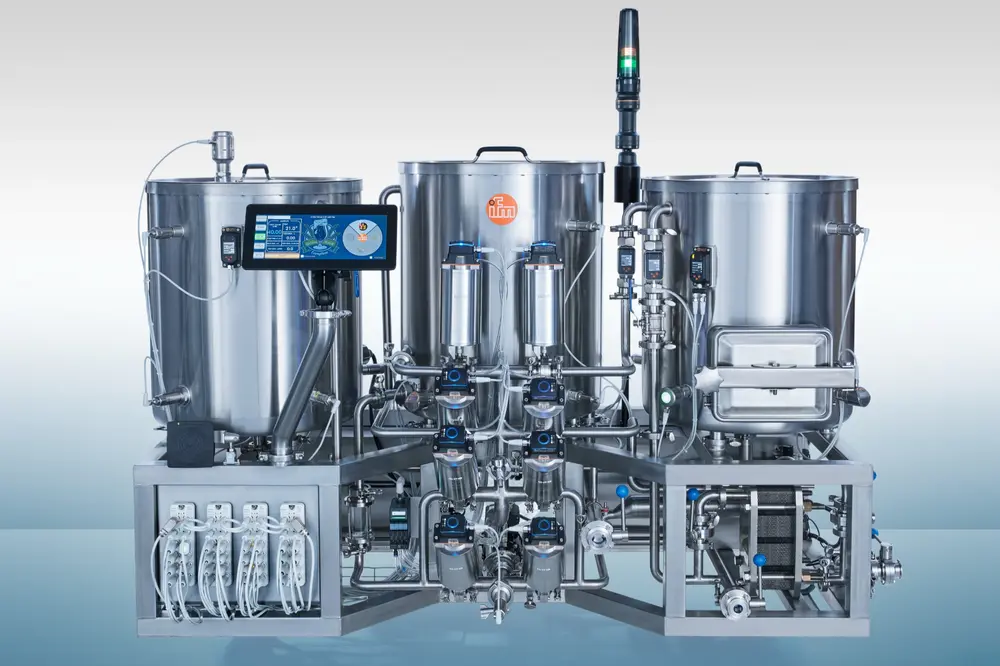
IO-Link Wireless est basé sur la technologie standardisée IO-Link(IEC 61131-9) et offre la même fiabilité de communication que la version câblée. Cette solution flexible peut être intégrée assez facilement dans l'infrastructure existante et être progressivement étendue à d'autres zones.
Un maître peut gérer jusqu'à cinq canaux de transmission, chaque canal pouvant prendre en charge jusqu'à huit appareils. Comme trois maîtres peuvent fonctionner en parallèle dans une cellule, il est possible de placer jusqu'à 120 appareils dans une seule cellule. Pour les appareils mobiles, il n'y a pas de limite de vitesse pour se déplacer à l'intérieur d'une cellule. Un mécanisme de transition défini assure une itinérance contrôlée des appareils entre différents maîtres.
Il n'y a pas de différence entre le traitement des données provenant de réseaux IO-Link câblés ou de la version sans fil. L'interface d'application pour les données cycliques et acycliques est compatible avec la description IO-Link existante. Le fonctionnement avec d'autres systèmes sans fil est assuré par un mécanisme de liste noire. Les fréquences et l'interaction avec ces autres systèmes peuvent être ajustées davantage, ce qui permet d'obtenir un taux d'erreur comparable à celui des systèmes câblés.
À l'avenir, les dispositifs à faible consommation d'énergie seront également pris en charge par le système avec un temps de cycle prévu de 5 ms. Pour respecter les réglementations existantes, la puissance de transmission sera limitée à une PIRE inférieure ou égale à 10 dBm (10 mW). Même avec ces limites, une distance de transmission de 20 m à l'intérieur d'une cellule maîtresse avec un seul canal de communication est possible. Lorsqu'on utilise plus d'un canal, on peut compter sur une distance de communication jusqu'à 10 m.
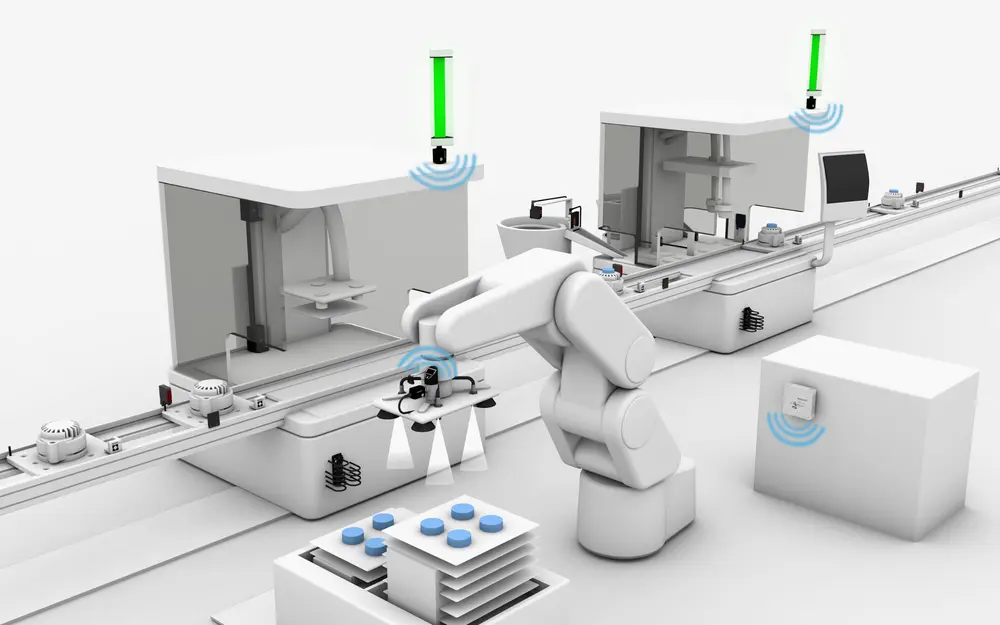
IO-Link Safety
Il s'agit de la nouvelle option permettant d'étendre les machines et systèmes automatisés avec des composants et une communication fonctionnellement sûrs. Outre les composants connus, il existe désormais des FS-Masters et des FS-Devices. Les technologies de connexion et de transmission d'IO-Link peuvent être utilisées telles quelles et les nouvelles versions FS s'appuient sur les fonctionnalités existantes. Il est ainsi facile d'intégrer des fonctions de sécurité. IO-Link Safety est normalisé à l'échelle mondiale selon la norme IEC 61139-2.
IO-Link Safety est indépendant des niveaux supérieurs, où les FS-Devices peuvent être des capteurs ou des actionneurs de sécurité, ou une combinaison de ceux-ci, ou même de la mécatronique avec sécurité intégrée. Grâce à cette fonctionnalité, un seul type d'appareil de sécurité est nécessaire pour le marché mondial, au lieu de plusieurs appareils de sécurité pour plusieurs bus de sécurité. Étant donné que des appareils non sécuritaires peuvent également être connectés aux FS-Masters, il est parfaitement possible d'équiper ces derniers en vue d'une expansion future ou d'un changement de fonctions.
Les FS-Devices peuvent être paramétrés à l'aide d'outils IO-Link (IODD) et peuvent également être fortement miniaturisés. Même avec toutes ces fonctions de sécurité, il est toujours possible de remplacer facilement le FS-Device sans outils. IO-Link Safety fournit une infrastructure pour les technologies d'automatisation et de sécurité jusqu'à PLe/CAT4/SIL3.
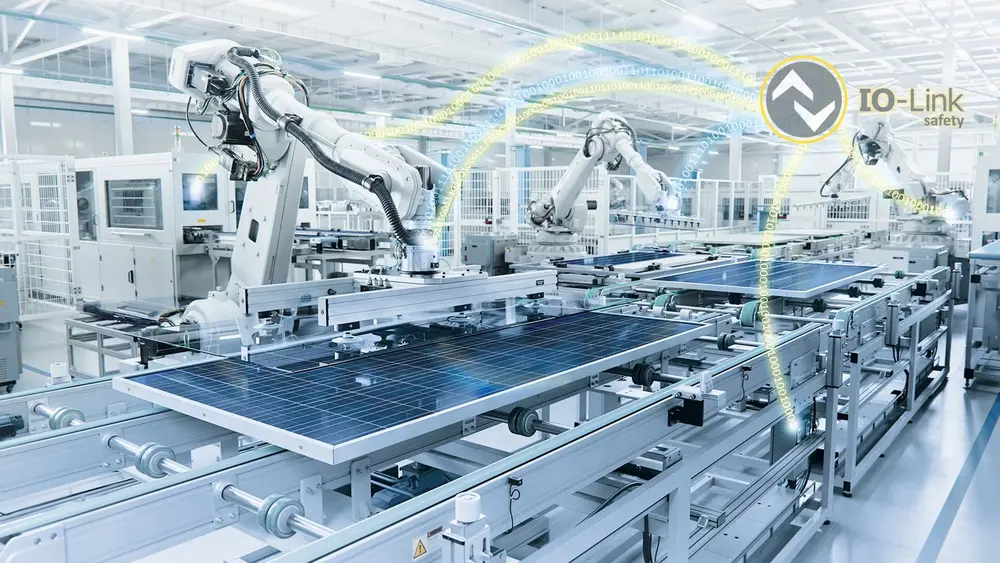
Smart Sensor Profiles d'IO-Link
IODD fournit des informations détaillées sur les appareils compatibles IO-Link, telles que l'identification du fabricant, le numéro de série, le numéro de pièce, l'état de fonctionnement, les caractéristiques électriques et mécaniques... Pour de nombreux types d'appareils, les données de processus, les paramètres de configuration et les fonctions ne sont pas encore totalement standardisés. Les profils d'appareils (Device Profiles) apportent une solution à ce problème et sont continuellement étendus et améliorés.
Par exemple, on dispose du Smart Sensor Profile depuis un certain temps. Il normalise le comportement et la nomenclature des paramètres des capteurs et facilite l'intégration et la manipulation de capteurs compatibles, indépendamment du fabricant ou du type de capteur. Cela permet d'intégrer le contrôleur avec peu d'efforts et de remplacer les capteurs sans restriction de flexibilité.
IO-Link reste très actif: de nouvelles fonctionnalités sont systématiquement ajoutées au protocole
Une nouvelle version de ce profil a été publiée en 2019, acceptant la classification intertechnologique suivante des classes d'appareils:
- Capteurs binaires avec Fixed Switching Sensors (FSS).
- Capteurs binaires avec Adjustable Switching Sensors (AdSS).
- Capteurs de mesure Digital Measuring Sensors (DMS).
L'objectif de tous les profils est de permettre aux appareils de ne différer que par leur identification. Le programme de l'automate peut alors être utilisé sans modification, même lorsque l'appareil est remplacé. Cela permet également une utilisation sans connaissance détaillée de l'appareil spécifique. Actuellement, nous travaillons également sur des profils pour les actionneurs intelligents, l'éclairage et l'indication, et les systèmes d'alimentation intelligents.
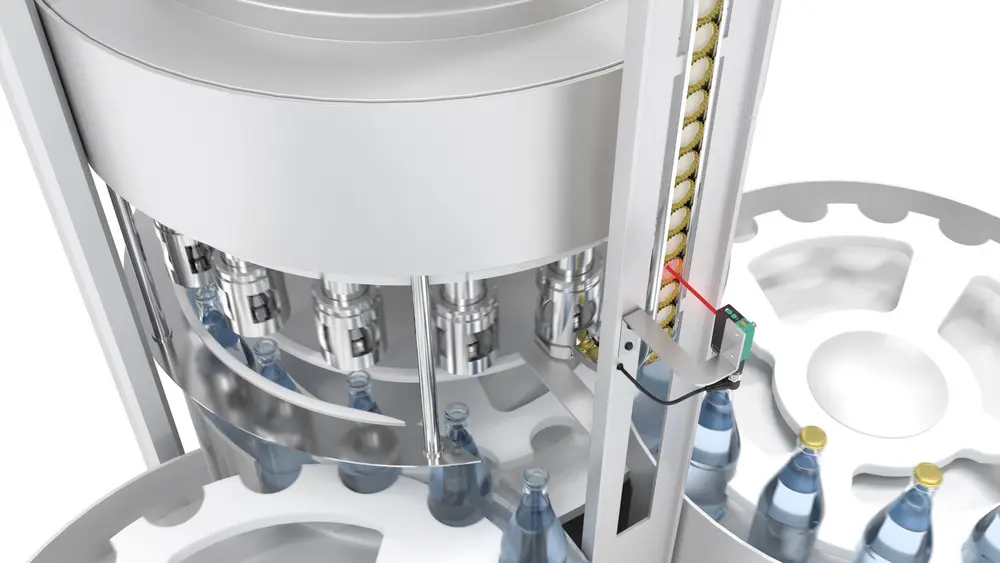
Intégration IO-Link avec OPC UA et JSON
Pour rendre les données du niveau IO-Link utilisables dans les systèmes parents ou les services basés sur le cloud, on utilise des passerelles qui effectuent une conversion de protocole selon certaines règles. Cette conversion est généralement connue sous le nom d'intégration verticale des données et doit être aussi transparente et simple que possible.
La conversion de protocole continue et orientée vers la demande (également appelée mapping) devrait normaliser le support des applications pertinentes pour l'automatisation. Pour IO-Link, deux mappings ont été développés pour l'intégration verticale des données: l'un selon OPC UA et l'autre selon JSON via REST ou MQTT.
IO-Link via OPC UA élargit la gamme des solutions d'automatisation possibles en tant qu'intégration indépendante du bus de terrain. Les données peuvent désormais être utilisées de manière normalisée par les clients OPC UA, tels que les systèmes ERP et les systèmes de gestion des ressources humaines. OPC UA, tels que les systèmes ERP, en dehors de la pyramide classique de l'automatisation.
JSON est un format de données simple qui peut être envoyé par l'intermédiaire d'un protocole REST (Representational State Transfer) API ou via MQTT. Ce format d'échange est très léger et son utilisation est moins intensive que celle d'OPC UA. Cela signifie que les données à destination et en provenance du niveau informatique peuvent être envoyées et utilisées de manière fluide et facile à interpréter.
En collaboration avec Balluff, Beckhoff Automation, ifm, Murrelektronik, Pepperl+Fuchs, Pilz et Sick