LE CHANGEMENT D’OUTIL AUTOMATIQUE
FACILITE LE PLIAGE DE PETITES SERIES
Moins d’arret, temps de reglage plus courts
Il y a quelques ans, nous écrivions un article sur les changements d’outil automatiques sur deux presses-plieuses stand alone. La solution était encore relativement neuve, même si certains fabricants y travaillaient depuis longtemps. Les pionniers étaient déjà bien avancés, les autres ont mis à profit le temps qui s’est écoulé depuis lors pour optimiser leur solution, avec parfois comme conséquence une réduction de moitié du temps de changement. Aussi il nous est paru intéressant de reprendre ce sujet d’autant que les changements d’outil automatiques restent une solution intelligente pour minimiser les arrêts sur la presse-plieuse.
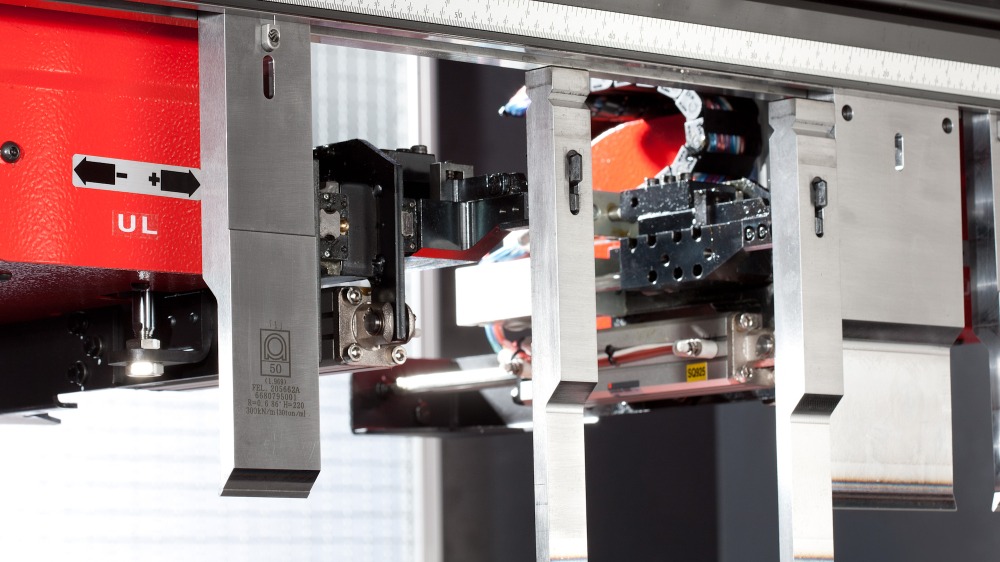
NOMBREUX TYPES ET POIDS
Il existe environ autant de noms pour un changeur d’outil automatique que de fabricants: Toolcell, Automatic Tool Changer (bref ‘ATC’), ToolMaster … Hormis la différence de nom, ils ont pas mal de choses en commun. Ainsi il s’agit le plus souvent d’une construction à côté de la presse-plieuse stand alone qui combine un magasin comportant les outils avec un ou plusieurs manipulateurs pour changer automatiquement les poinçons et les matrices. Dans un seul cas, le magasin se situe derrière les butées arrière, ce qui est normalement un espace perdu.
On peut stocker beaucoup d’outils dans les magasins. Un seul fabricant a même quadruplé la capacité de stockage par rapport à la fois précédente, atteignant 85 mètres, et surclasse donc largement la plupart des collègues qui libèrent par exemple 11,52 mètres pour les poinçons et 26,88 mètres pour les matrices ou qui prévoient 25 stations pour les matrices et 18 pour les poinçons, avec une station accueillant une longueur totale de 800 mm de poinçons ou de matrices. L’un ou l’autre a naturellement une répercussion sur l’empreinte des machines: pour pouvoir loger ces 85 mètres d’outils, il faut un espace accru de 10 m², où le changeur d’outil chez le dernier fabricant ne demande par exemple que 2 m de longueur en supplément.
Nous voyons bel et bien une grande variation dans la taille des outils. Dans un ordre croissant, la longueur maximale de l’outil atteint selon le fabricant respectivement 100 mm, 120 mm, 300 mm et 500 mm, jusqu’à un poids maximal de 25 kg. A l’inverse, la plus petite longueur varie de 5 mm à 30 mm. Ces grandes différences sont liées d’une part à la construction spécifique des manipulateurs entre autre, et d’autre part à une autre vision de l’efficacité ainsi que de la rapidité avec lesquelles vos outils sont changés.
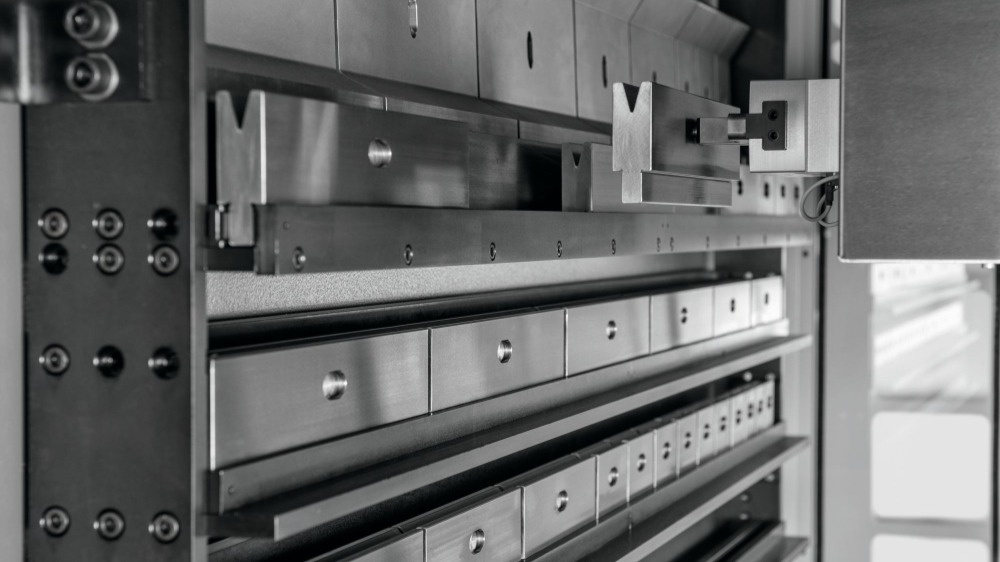
QUATRE PROBLEMES ABORDES …
Pour bien comprendre la différence d’approche, nous devons d’abord un peu rappeler pourquoi les fabricants ont eu l’idée des changements d’outil automatiques. Ils s’attaquent de cette manière à pas moins de quatre problèmes spécifiques. Nous commençons par la minimisation des ‘temps morts’ qui découlent du changement manuel des outils à chaque fois qu’un nouveau réglage s’impose. Hélas, au fur et et à mesure que les séries rapetissent, ceci est de plus en plus fréquent.
Du reste, il ne s’agit pas seulement de la manipulation pure du changement des outils, vous devez également penser à la programmation et au réglage des programmes de pliage. Nous approfondissons encore les possibilités du logiciel tout à l’heure mais sachez d’ores et déjà que la commande sur les changements rapides commute rapidement entre les programmes de pliage afférents aux différentes pièces.
Outre le changement des outils, l’opérateur doit désormais évacuer les pièces pliées et amener de nouvelles tôles. C’est également une source d’arrêts. En soi, l’automatisation des changements d’outils ne peut pas y remédier mais si vous synchronisez l’aspect logistique aux changements d’outil, vous pouvez au moins veiller à éviter toute perte de temps supplémentaire.
Un troisième aspect est lié à la qualité du pliage. En fonction du fabricant, les outils sont bien positionnés avec une tolérance de quelques centièmes. Certainement pour des formes complexes 3D, vous ne pouvez pas en sous-estimer l’importance pour la qualité finale parce que le dépliage pour ce type de pièces est calculé offline et que la distance entre les sections et les outils est très importante.
Enfin, vous avez le facteur ergonomie. L’opérateur prend du plaisir à travailler avec un changeur d’outil automatique, simplement parce qu’il ne doit plus soulever du sol des outils parfois lourds.
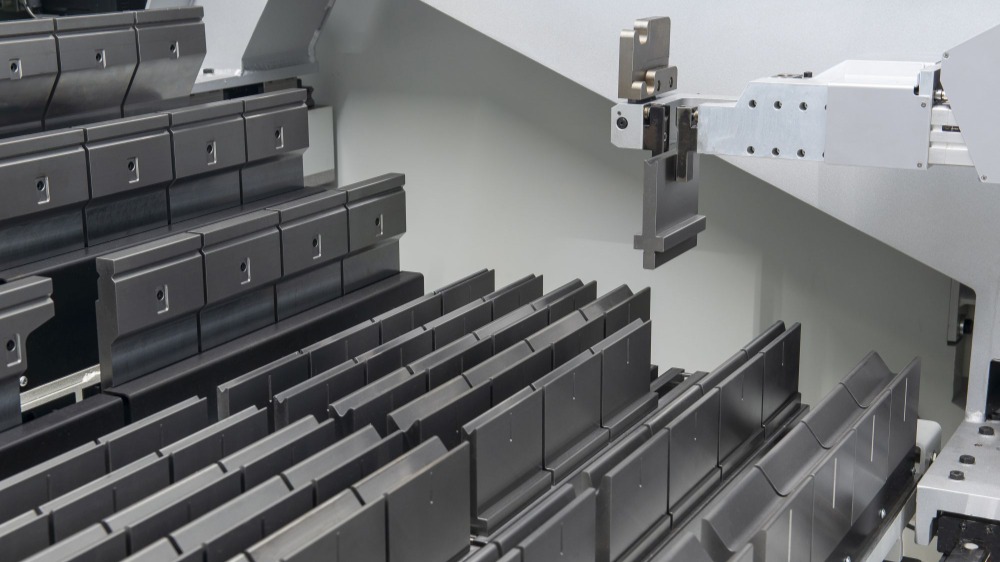
COURTS TEMPS DE CHANGEMENT
Il ressort de ce qui précède que la réduction des arrêts est probablement le principal atout d’un changeur d’outil automatique mais les fabricants ne peuvent concrétiser cette revendication que si les temps de changement sont suffisamment courts, de telle sorte que l’opérateur ne doit pas attendre (trop) longtemps près de sa machine tandis que les couteaux de pliage sont changés. Aujourd’hui, vous devez compter qu’un nouveau réglage, c’est-à-dire enlever les outils et en replacer d’autres, prend environ 3,5 minutes. Bien entendu, ceci dépend du nombre de postes de travail et de la complexité des usinages de pliage mais de nombreux facteurs propres à la machine jouent également. Nous songeons immédiatement aux possibilités des manipulateurs qui permettent de changer un outil en 8 à 11 secondes.
SEGMENTE OU MOINS D’OUTILS
Nous revenons à cette différence de vision, évoquée plus haut dans l’article. Le fabricant choisit avec les segments les plus petits possibles (5 - 100 mm) de travailler avec quatre manipulateurs entraînés de façon totalement indépendante. Avec ces manipulateurs spécifiques, la machine est en mesure de changer des segments jusqu’à 800 mm en une fois. Ceci vaut pour les poinçons et les matrices en même temps. De plus, on peut travailler de façon segmentée, ce qui signifie que tous les outils ne doivent pas être changés à chaque fois mais qu’ils peuvent être réutilisés pour le réglage suivant.
Plusieurs fabricants utilisent du reste ce petit truc parce que ceci marche également avec les manipulateurs robots. Et les préhenseurs dans les doigts de butée qui servent de manipulateurs (pour limiter le nombre d’axes pilotés; important dans l’optique du positionnement précis). Sur les systèmes linéaires, par contre, cela ne marche pas. Là, tous les outils doivent être changés un par un à chaque fois (dans ce cas à une vitesse de 10 secondes par outil). Pour écourter le temps de changement total, on utilise dès lors des outils moins nombreux mais plus grands: un segment de 500 mm face à cinq fois 100 mm.
OPTIMISATION DU CHEMIN
Avant de vous focaliser sur le temps précis d’un changement d’outil, sachez que l’impact du logiciel sur le temps de changement total est au moins aussi important. Sur base des outils disponibles, le logiciel de pliage calculera en effet le chemin optimal les changements d’outil. De plus, le progiciel calculera offline la composition idéale des outils de coupe, compte tenu des diverses pièces à plier – pour certains tout au long d’une production journalière et en mêlant toutes les épaisseurs – afin de minimiser le nombre de changements. Certains progiciels spécifiques vont même jusqu’à convertir automatiquement le programme de pliage quand un programme est chargé avec d’autres segments que ceux présents dans le magasin.
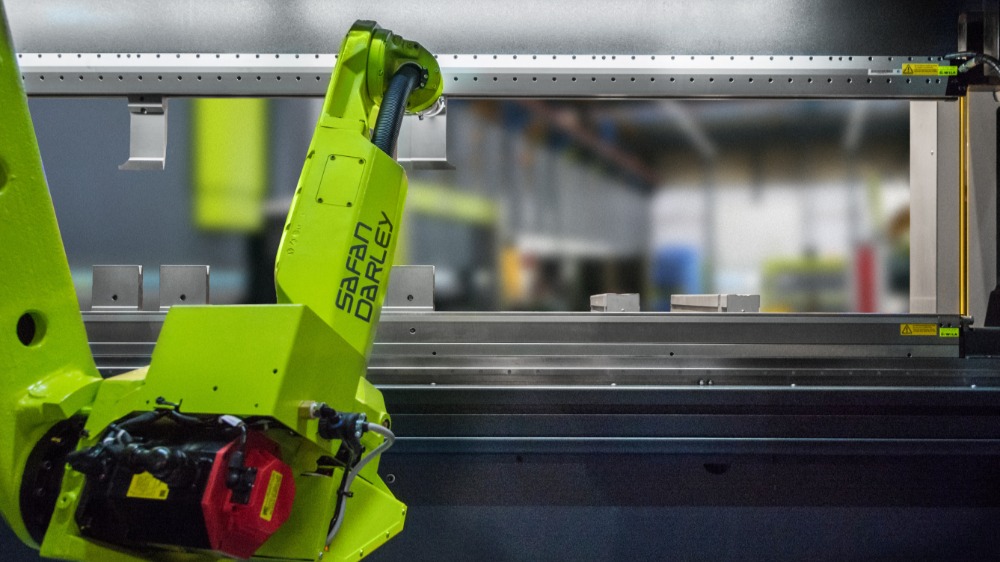
AUTRES FACTEURS IMPORTANTS
Outre les aspects déjà évoqués, les fabricants diffèrent encore sur bien d’autres points spécifiques: le nettoyage automatique de la prise de matrice, la rotation de l’outil supérieur … Dans la limite de ces deux pages, nous ne pouvons pas trop approfondir mais comme il s’agit de temps en temps de critères importants pouvant influencer le choix de l’un ou l’autre fabricant, nous les évoquons brièvement.
Outils standard ou pas?
Pour pouvoir saisir les poinçons et les matrices, les outils sont pourvus d’une fente ou d’une pièce rapportée supplémentaire dans le cas d’un changeur d’outil automatique. D’où le fait que les outils standard ne sont pas compatibles avec un tel système, du moins à l’exception d’un fabricant qui travaille bel et bien avec les outils ordinaires. Cela signifie l’obligation d’investir dans de nouveaux outils dans tous les autres cas. Naturellement, ce n’est pas un hasard que cette exception concerne l’un des fabricants permettant d’accoupler un changeur d’outil automatique à une presse-lieuse stand alone par la suite.
Mixed ou pas?
Supposons qu’un certain réglage spécifique demande cinq outils de pliage. Quatre de ces outils se trouvent dans le magasin mais l’un n’y figure pas. Chez certains fabricants qui disposent d’un système qui reconnaît les outils (par exemple via scanning), il est possible de changer manuellement et automatiquement en même temps, chez d’autres vous devez choisir un changement manuel ou un changement automatique.
Programmation supplémentaire ou pas?
Dès que la commande sait quels outils sont présents dans le magasin et où ils se trouvent, l’opérateur ne doit plus programmer davantage sur un changeur d’outil automatique, seuls certains fabricants sont un peu plus flexibles en ce qui concerne la position que d’autres du fait que chez eux les outils n’ont pas une place fixe. De cette manière, la commande peut déterminer elle-même l’emplacement idéal d’un outil sur base de l’historique.
CONCLUSION
Les changeurs d’outil automatiques sont une excellente solution pour les petites séries et les réglages complexes. La portée d’application d’un robot, par exemple, est totalement différente. Il existe sur le marché de nombreux systèmes qui diffèrent sur de nombreux points, petits et grands. Nous venons d’aborder la plupart de ces points. Espérons que cet article soit la première étape vers le bon choix.