ON FAIT JAILLIR UNE ETINCELLE?
PERSPECTIVES DE CROISSANCE LARGEMENT POSITIVES DE L’EROSION PAR ETINCELAGE
L’intérêt pour l’érosion par étincelage croît. L’exigence de précision sans cesse plus élevée, les rugosités surfaciques et pièces plus complexes sont d’importantes motivations derrière cette tendance. Par ailleurs, des systèmes de commande intelligents ont rendu la technologie plus accessible. L’érosion par étincelage cadre dans les usines de machines modernes.
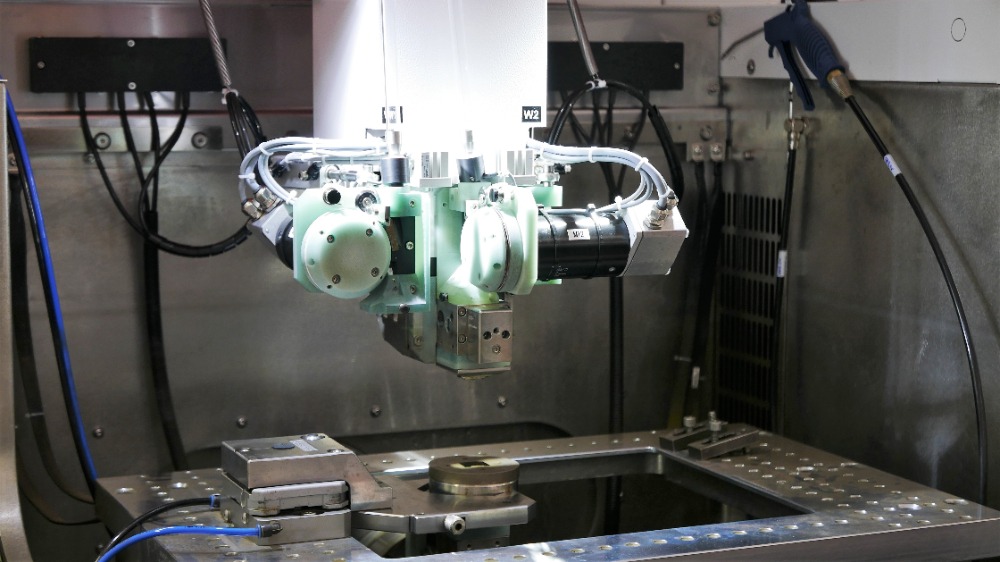
L’érosion fil et par étincelage est décrite comme une technologie assez récente, dont le développement n’est intervenu qu’au cours des 50 années précédentes. Au sens strict c’est exact; l’émergence des générateurs d’impulsion pilotés dans les années 60 ont pour la première fois donné une place à la technologie dans des segments spécifiques de l’industrie discrète. Or les premières idées d’usinage des métaux par une étincelle datent déjà de la fin du 19e siècle.
Des chercheurs se sont demandé à l’époque pourquoi l’électrode de soudage au pôle positif s’usait plus vite. Vers 1942, un brevet a été octroyé dans les Etats-Unis pour une technologie qui utilisait un arc électrique interrompu pour couper des dents d’une lame de scie. Vingt ans plus tard, des générateurs d’impulsion pilotés ont permis d’utiliser le graphite comme matériau d’électrode. A partir de 1970 se sont ajoutées les machines d’érosion par étincelage à commande numérique demandées dans l’industrie des outils.
LA TECHNOLOGIE
Dans l’érosion par étincelage, on usine le matériau par une étincelle. Entre l‘électrode de l’outil et celui de pièce est produite une tension électrique, de sorte qu’une étincelle saute de l’outil vers la pièce et que le matériau s’y évapore. Plus l’espace d’étincelage est petit, plus le saut d’énergie est grand. L’énergie électrique est convertie en énergie thermique (avec des températures dans le canal plasma de 8.000 à 12.000 °C, avec des pics jusqu’à bel et bien 20.000 °C). Cette haute température fait évaporer le matériau.
Avantages
La pièce ne subit aucune sollicitation mécanique. Dans l’érosion, par exemple, l’outil fil est renouvelé quasi à chaque fois, si bien que le matériau reste intact plus longtemps. Hormis la machine – l’outil sous forme de fil ou dans l’étincelage sous forme d’électrode – il faut un diélectrique. Ce liquide refroidit la pièce et élimine le matériau détaché de l’espace d’étincelage. Le rinçage est l’un des principaux paramètres du processus.
Inconvénients
L’inconvénient majeur de cette technique est sa lenteur. Par ailleurs, seulement des matériaux conducteurs électriques peuvent être usinés. En contrepartie la dureté du matériau n’a aucun effet en principe et la machine peut être commandée quasi sans intervention humaine.
QUAND L’EROSION PAR ETINCELAGE?
En raison de l’émergence du fraisage à 5 axes, du high speed milling et du fraisage au carbure métallique, l’érosion par étincelage semble être marginalisée. Les nouvelles techniques citées permettent en effet un travail très précis et obtiennent des résultats qui n’étaient réalisables que par l’érosion par étincelage. A cela s’ajoute le fait que des nombreux usineurs sans expérience spécifique de l’érosion par étincelage ne recourront pas à cette technique. Entre-temps cette tendance baisse. Les exigences de qualité élevées, les rayons plus petits et les angles plus vifs demandent une exécution précise via l’érosion par étincelage. Dans l’industrie médicale et dans la production de matrices, par exemple, l’érosion par étincelage continue de jouer un rôle important.
Il ressort d’une récente étude de marché américaine que la croissance du marché EDM restera sous les 4% dans les prochaines années. D’ici 2023, le marché EDM mondial atteindra environ $ 885 millions. Ceci montre que des développements tels qu’Industrie 4.0, la conduite électrique et autonome, les progrès dans les soins de santé extrairont cette technique de sa niche et jetteront la base de sa croissance future. Lorsque, par exemple, des nervures profondes sont nécessaires dans une pièce ou matrice, l’érosion fil reste la technologie préconisée. Dans certaines applications, l’érosion par étincelage peut être plus efficace que le fraisage à 5 axes, par exemple s’il s’agit de produits à paroi très mince soumis à des exigences de précision élevées. Une combinaison est parfois une solution encore meilleure: le pré-fraisage à 5 axes et puis le post-usinage avec EDM. L’important est de toujours examiner toutes les étapes du processus nécessaires jusqu’au produit fini. Si la qualité de surface est obtenue en une fois avec l’érosion par étincelage, le temps de passage peut être quand même plus court.
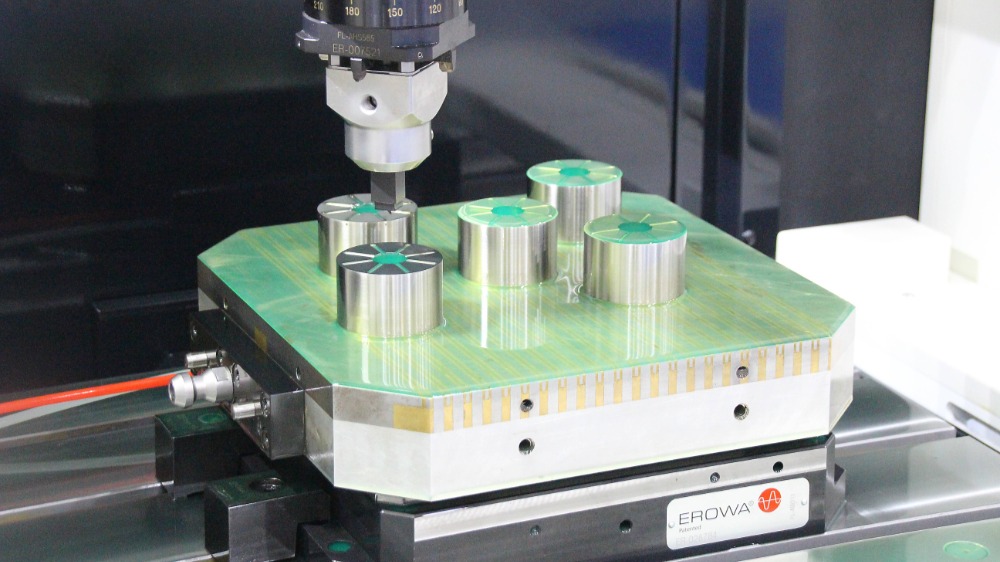
Ce Surge Pulse Generator, notamment pour les machines EDAC et EDAF, induit une rugosité de 0,04 µm
L’industrie aéronautique
Les applications de l’érosion par étincelage dans l’industrie aéronautique sont plus nombreuses grâce aux développements dans l’industrie des machines. Il y a dix ans, des fabricants de moteurs d’avion refusaient encore les pièces érodées par étincelage la création d’une Heat Affected Zone (HAZ), la mince couche blanche sur les pièces due à l’apport thermique. Dans l’industrie aéronautique, on redoutait depuis longtemps la création de microcracks. Grâce aux améliorations sur le générateur d’impulsions, les constructeurs de machines EDM contrôlent mieux l’impulsion, en termes de durée et de forme. La HAZ est plus petite et plus prévisible. Elle est même négligeable dans certains cas.
Actuellement, l‘érosion par étincelage est notamment aussi utilisée pour réaliser des composants de turbine critiques pour moteurs d’avion. La technologie d’étincelage améliorée induit de meilleures surfaces, atteint quasi une qualité de polissage (valeur Ra 0,04 micron). Ceci implique un processus plus lent mais dans des applications qui demandent de telles rugosités, on peut s’épargner une étape de processus (polissage). Affiner les rugosités de surface est l’un des principaux thèmes chez les constructeurs de machines. Un autre point d’attention est le rinçage. Il est nécessaire mais induit une usure sur l’électrode (lors de l’étincelage). Outre des méthodes de rinçage alternatives, on étudie la bonne composition du diélectrique. L’huile semble procurer des qualités de surface encore meilleures.
PRECISE ECM VS EROSION PAR ETINCELAGE
Ces dernières années, on rencontre ici et là dans l’industrie de fine mécanique du Benelux le Precise ECM, une variante de l’usinage électrochimique (une combinaison d’EDM avec ECM). Dans le P-ECM, l’axe z hydraulique amène l’électrode jusqu’à 10 µm de la pièce. Puis l’électrode oscille et une impulsion électrique est à chaque fois transmise, quand l’électrode est proche de la pièce.
Directement après, l’électrode se déplace en sens inverse et une fine couche de 30 nanomètres se détache du matériau. La différence importante avec l’érosion par étincelage est que l’électrode ne s’use pas. Ceci est lié à l’électrolyte, dans ce cas une solution saline. Le rinçage direct fait que les électrodes ne peuvent pas adhérer à l’outil. Et il s’agit ici d’un processus à froid, sans apport thermique.
SEUIL D’ENTREE ABAISSE POUR L’EDM
Hormis le fait que les fabricants de machines d’érosion fil et par étincelage ont travaillé de façon intensive à améliorer les générateurs, le système de commande a changé. La technologie se caractérise par le grand nombre de paramètres de processus qui influence la productivité et la précision. Les constructeurs de machines parviennent à intégrer de plus en plus de savoir-faire de la technologie dans la commande, ce qui facilite la programmation et la commande de la machine. Dans les prochaines années, l’émergence de l’intelligence artificielle (IA) et de l’apprentissage machine (AM) comportera son lot d’attentes. Pour de nombreuses entreprises, ceci apaise les craintes de s’engager dans l’EDM. Certains fabricants appliquent une fonction d’aide dans leur commande, qui guide l’opérateur moins expérimenté étape par étape à travers le processus. L’engagement de l’EDM est simplifié par des innovations telles qu’un changement automatique du fil.
VARIATIONS SUR L’EROSION
Outre l’érosion fil et par étincelage traditionnelle, il existe quelques variantes. L‘une d’entre elles est la vibration ultrasonique de l’électrode pour augmenter les performances. La vibration crée une plus grande agitation dans le diélectrique, ce qui augmente la pression dans l’espace d’étincelage (entre la pièce et l’électrode). Dans certaines recherches, on dit que cette technologie combine les avantages de l’érosion par étincelage avec ceux de l’usinage par ultrasons.
Par ailleurs, il existe un processus hybride: l’usinage laser est combiné avec l’érosion par étincelage pour les derniers usinages finaux. Pendant la rectification, l’EDM est aussi déjà engagé, essentiellement pour améliorer la productivité. Un développement assez récent est l’arrivée de sortes de céramique conductrice d’électricité. On en étudie la faisabilité pour les électrodes parce que ceci diminuerait leur sensibilité à l’usure. Comme dans l’érosion par étincelage jusqu’à 50% des coûts de processus finaux sont déterminés par les coûts électro, ce thème est souvent abordé.
INFLUENCE DE LA FABRICATION ADDITIVE
Un autre développement qui rend l’érosion fil intéressante, est l’impression 3D métal. Dans la technologie à lit de poudre laser, les pièces sont imprimées sur la plaque de construction. Après le processus additif, elles sont retirées. L’érosion fil est ici la technologie adéquate. Plusieurs constructeurs de machines voient ici une marché futur et commencent déjà à adapter leurs machines dans ce but spécifique. Certains commercialisent des machines d’électro-érosion relativement simples parce que l’usinage ne demande pas plus en fait, d’autres adaptent des machines existantes parce que normalement le fil évolue toujours verticalement dans l’érosion fil. Pour couper les pièces indépendamment de la plaque de construction, on utilise un mécanisme de basculement.