Plus de temps pour le controle de qualite apres l’automation au tour
Mockel investit dans le Halter Loadassistant pour des composants de haute precision
La mécanique de haute précision demande un contrôle de qualité stricte. Le progrès technique fait que beaucoup de pièces complexes sont usinées en moins d’étapes qu’il y a quelques années. Mais pour des pièces critiques, avec des tolérances exprimés en centièmes, le contrôle de ces pièces complexes est devenu plus difficile et demande du temps. Du temps qui manque cruellement puisque l’opérateur doit continuellement charger et décharger sa machine. Confronté à ce problème, la société Mockel a automatisé le chargement en installant un ensemble table de chargement/robot Halter LoadAssistant fourni par la société Buhlmann.
composants de precision de mockel
pour les secteurs de pointe
Historique
L’entreprise familiale Mockel voit le jour en 1947 et s’installe dans le centre d’Eupen. Comme beaucoup de sociétés dans la région, Mockel est spécialisé dans la production de composants et l’entretien de machines pour l’industrie textile encore florissante. Dans les années 70, Mockel se consacre de plus en plus à la fabrication de composants de haute précision après avoir fabriqué de composants pour la première fois pour la défense. Ensuite la société se spécialise dans la fabrication pour l’industrie aéronautique et spatiale.
A cet effet, les certifications ISO 9001, EN9100 et ISO13485 devraient être obtenues successivement. En 2000, suite à la forte croissance, les ateliers deviennent trop exigus, d’où le déménagement vers la ZI de Baelen. Depuis lors, Mockel a réalisé de grands investissements dans la modernisation du parc machines avec de plus en plus d’attention pour les possibilités d’automatisation plus poussés. Depuis 2018, Mockel a introduit le lean management en association avec un cluster allemand expert d’Airbus Hambourg et le programme Factory of the Future de la communauté française.
Activités
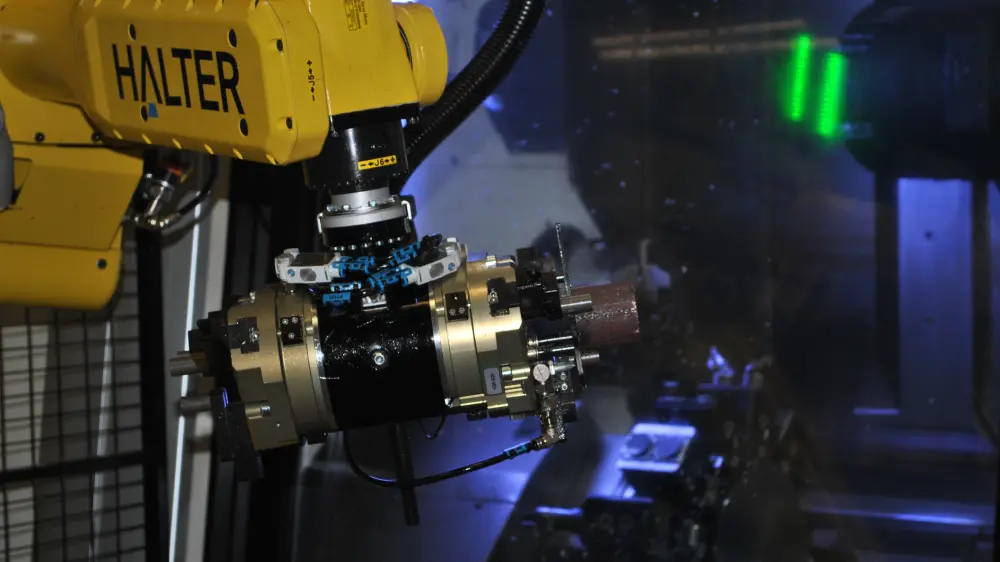
revient à une charge utile de 28 kg
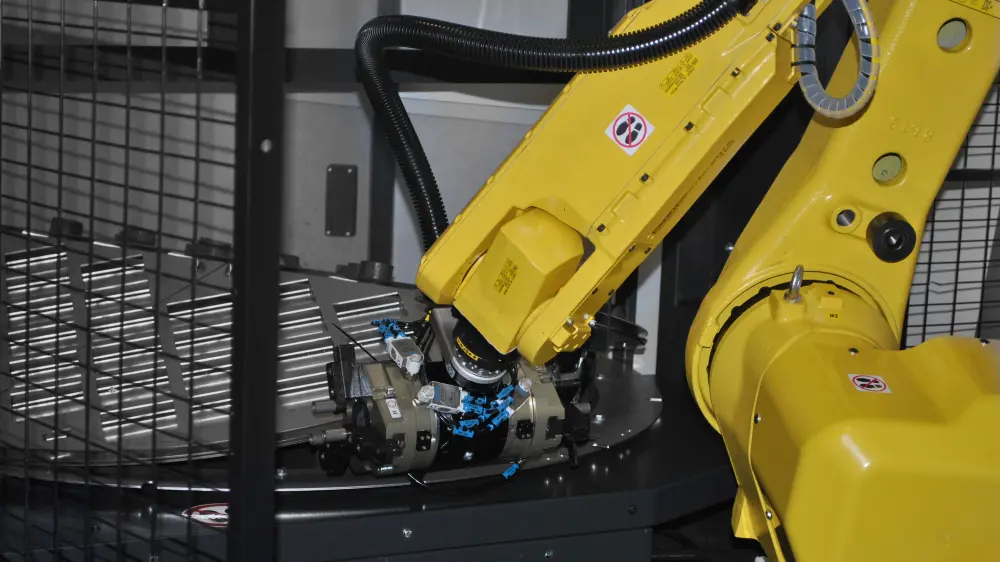
Mr. Manuel Reuter (DOP) responsable opérationnel décrit les activités de Mockel SA: “Nous produisons et faisons l’assemblage de composants de haute précision pour des secteurs de pointe comme la défense, l’aéronautique et l’industrie spatiale. Nous faisons du fraisage, du tournage, de la correction, le contrôle de qualité, la finition et l’assemblage. Outre ces différents services industriels nous sommes à même de proposer un service complet de gestion du projet, du supply-chain et de l’assemblage. Et comme nous sommes certifiés suivant les normes industrielles les plus strictes, nous pouvons aussi effectuer les contrôles de qualité agrées ce qui donne à notre client la possibilité d’intégrer ces pièces certifiées dans leur processus de production.“
Personnel
La SA Mockel emploie près de 50 personnes, dont 15 pour la préparation des travaux, le contrôle de qualité final, la gestion des projets et le suivi commercial. “Comme pour toutes les sociétés dans notre secteur, il est aussi difficile de trouver du nouveau personnel. C’est pourquoi nous recherchons des profils techniques à la source, c.a.d. en attirant des étudiants par des stages, pour ensuite les embaucher et faire leur formation complètement en interne. Ainsi, la plupart des programmeurs et responsables actuels sont passé par le stade d’usineur.“
Parc machines
Ces dernières années, le parc machines de Mockel SA a connu une évolution en réaction aux demandes des clients qui sont demandeurs de toujours plus de flexibilité. “En gros, nos tours avec embarreurs sont surtout employés pour des grandes séries avec peu de changements alors que les fraiseuses avec leurs grands magasins d’outils permettent d’être plus flexibles. Le parc machines à fortement évolué ses dernières années suite à la demande de petites séries ce qui nécessite un outil de production qui permet de faire des changements rapides. Du point de vue technique, d’organisation et de planning nous réussissons à satisfaire nos clients,“ nous assure Mr. Reuter, “mais nous rencontrons des problèmes à la machine au niveau du temps dont nous avons besoin pour effectuer les contrôles qui doivent se faire pendant la production.“
controle de qualite des pieces
Outre l’augmentation de qualité, le progrès technique des machines se concentre surtout sur le temps gagné par la diminution du nombre d’étapes qu’il faut pour réaliser une pièce. “Il y a quelques années nous avions des pièces qui nécessitaient six ou sept prises avant d’avoir une pièce finie alors que nous la réalisons en deux fois maintenant. C’est sûrement un grand gain de temps, mais on s’est rendu compte que l’opérateur à beaucoup plus de difficultés à mesurer les tolérances de la pièce puisque toutes les étapes intermédiaires avec leurs points de repères pour réaliser ses mesures ont disparus avec ces nouvelles stratégies d’usinage. Gagner du temps pour réaliser la pièce est positif mais nos opérateurs se retrouvaient dans une situation où il fallait charger/décharger plus fréquemment la machine tout en devant faire des mesures beaucoup plus complexes et prenant plus de temps.”
Automatiser pour aider le contrôle de qualité
C’est pourquoi Mockel voulait donner plus de temps aux opérateurs pour effectuer les mesures qui forment la base de la qualité des pièces fabriquées et de notre renom. “Pour cette raison il était essentiel d’automatiser le chargement et le déchargement de la machine.“
“Un exemple de cette évolution est une famille de pièces qui étaient produites sur des tours avec embarreurs. Ces pièces étaient tournées à partir de barres de près de 80 mm. Pendant l’usinage se produisait trop de vibrations ce qui avait une influence négative sur les tolérances requises. Comme il s’agit de pièces critiques qui doivent être exactes au centième, nous avons dû trouver une solution.“ La solution était d’employer des bouts de barre ronds, carrés ou octogonaux et avec l’achat d’un tour d’occasion qui par chance avait toutes les options requises pour usiner les pièces. Ainsi, on pouvait réduire les vibrations.
Halter Loadassistant
encrages à centrage automatique sont fixés sur le sol
Restait le problème du manque de temps. ”La solution trouvée est l’ensemble table de chargement et robot Halter LoadAssistant. Le LoadAssistant est très flexible et peut être employé aussi bien à côté d’un tour que d’une fraiseuse, centre d’usinage ou n’importe quelle autre machine avec laquelle le robot peut communiquer.”
Conçu pour de petites et moyennes séries (10 à 1.000 pièces), l’avantage de cet ensemble est la table rotative divisée en deux par une paroi. La table est tournée par le bras du robot et la moitié de la table peut être alimenté en temps masqué avec des pièces à usiner pendant que le robot charge l’autre partie de la table avec des pièces sortant de la machine CNC.
des pièces rondes, carrées ou octogonales
La capacité de la table est aussi très flexible grâce aux différentes grilles qui peuvent être montées. Il y a plusieurs grilles standard qui peuvent contenir des pièces rondes, carrées, octogonales. Et des grilles avec lesquelles des pièces à usiner peuvent être empilés. Dans tous les cas, le logiciel du robot sait parfaitement où se trouvent les pièces et où il doit les replacer après usinage. Les données des emplacements des pièces sont introduites par l’opérateur avant de lancer la production. Cette programmation peut évidemment être sauvée pour l’employer plus tard.
Configuration chez Mockel
Manuel Reuter nous donne un descriptif de la disposition du LoadAssistant: “Le Halter est placée à côté de notre nouveau tour acheté spécialement pour ce genre de pièces plutôt lourdes. Je dis placé, mais je devrais plutôt dire déposé, car le Halter est déplacé facilement à l’aide d’un transpalette pour être déposée plus loin à côté d’une autre machine CNC. Ainsi le Halter peut être programmé pour fonctionner sur quatre machines différentes. Afin de déposer la machine au bon endroit, trois encrages à centrage automatique sont fixés sur le sol ou encastrés dans le sol. Notre machine est équipée d’un bras Fanuc équipé de pinces doubles à trois doigts pour des pièces cylindriques et un système de changement rapide des pinces. Le bras a une capacité de 35 kg ce qui revient à une charge utile de 28 kg en employant qu’une seule pince ou de 2 x 14 kg quand on emploie les deux pinces. Enfin, nous avons pris l’option d’un plateau de retournement de pièce pour réaliser des pièces plus complexes.“
Zone de sécurité
Le robot est équipé d’un scanner de présence qui fonctionne en mode deux zones. La première zone est liée à la surface sol d’entrée de la zone machine où le robot ne saurait toucher personne. Pourtant, dès qu’il détecte quelque chose dans cette zone, la machine ralentit sa course à 10% de sa vitesse normale. Dès qu’il détecte quelqu’un dans la deuxième zone, dite de collision, le robot s’arrête immédiatement. Après un arrêt, l’opérateur doit donner son accord pour remettre la machine en route et le bras continue de travailler à l’endroit où la séquence de travail a été interrompue.
Installation clef en main
“Ce qui nous a beaucoup séduit dans cette machine, c’est l’installation clef en main, très facile et sans le genre d’intégration qui prend du temps et pour laquelle il faut plusieurs acteurs pour installer la machine. Ici, ce sont les équipes de Halter et de Buhlmann qui ont fait l’installation et la formation en même temps. Evidemment le tour et le Halter sont certifiés CE, mais l’ensemble devait aussi encore être certifié CE par l’installateur.“
Programmation
En pratique la programmation d’une nouvelle procédure de chargement est effectuée en douze étapes à l’aide d’un logiciel intuitif et graphique. Le logiciel ne requiert aucune connaissance en programmation robotique. Les différentes grilles ou les systèmes d’empilage sont déjà préprogrammés dans le logiciel. Il suffit d’introduire les données des pièces à usiner.
“Les données de l’emplacement de la machine CNC ayant été introduits par les techniciens de Halter et de Buhlmann pendant l’installation, le bras peut immédiatement commencer à charger le tour.“