Fusion laser sur lit de poudre (LPBF): une technologie prometteuse
L'approche holistique du processus comme facteur de réussite
La fusion laser sur lit de poudre reste la technologie d'impression des métaux la plus utilisée, bien qu'elle soit coûteuse et complexe. Une vision globale du processus et une approche holistique permettent d'appliquer cette technique avec succès.
Introduction
Origine et principe
Le procédé de Laser Powderbed Fusion, ou fusion laser sur lit de poudre (LPBF, de l'anglais), comme son nom officiel l'indique aujourd'hui, est la technologie d'impression sur métal la plus ancienne et la plus développée. Cette technique remonte au siècle dernier et a été présentée lors d'un salon professionnel vers 2000. La KU Leuven et Fraunhofer ILT (Allemagne) ont joué un rôle important dans le développement de cette technologie et le font encore aujourd'hui.
Dans la fusion laser sur lit de poudre, de très petites poudres métalliques (d'un diamètre de 25 à 45 µm) sont pour ainsi dire soudées ensemble grâce à l'énergie du faisceau laser. La machine balaie la surface de la plaque de construction, sur laquelle la poudre a été étalée à l'aide d'un enduit, et n'expose que les particules de poudre à l'endroit où le matériau doit être placé dans le produit final. Les poudres métalliques sont soudées entre elles dans le plan horizontal et liées à la couche sous-jacente par la chaleur. Pour obtenir une bonne densité, il est nécessaire de répartir uniformément les poudres.
Après avoir exposé une couche entière de cette manière, le panneau de construction s'enfonce jusqu'à atteindre exactement l'épaisseur de la couche suivante. Une nouvelle couche de poudre est appliquée et repassée à plat, et tout le processus recommence à zéro. L'épaisseur de la couche détermine en partie les propriétés mécaniques de la pièce à imprimer.
En fonction de la hauteur de la pièce, des milliers de couches peuvent être imprimées l'une après l'autre. Certaines grandes constructions, par exemple pour des moteurs de fusée, durent ainsi plus d'une semaine.
Les variantes de la technologie et leurs fournisseurs
Le principe de la fusion laser sur lit de poudre remonte aux années 1980 et s'appelait à l'origine Selective Laser Sintering (frittage sélectif par laser). Les Américains ont développé le SLS pour les polymères. Plus tard, l'impression de métaux a été ajoutée, ce qui a donné les termes Selective Laser Melting (SLM) et Direct Metal Laser Sintering (DMLS). Aujourd'hui, on parle de fusion laser sur lit de poudre (LPBF).
Une variante consiste à remplacer le faisceau laser par un faisceau d'électrons, on parle alors d'EPBF. Dans ce cas, les poudres sont plus grosses (40 à 100 µm), ce qui donne une structure de surface légèrement plus grossière, qui peut être souhaitable pour les implants médicaux, par exemple.
Les principaux brevets pour le LPBF ayant expiré, le nombre de fabricants augmente plus vite que le marché. Il en va de même pour les imprimantes à faisceau d'électrons. Depuis l'expiration du brevet, de nouveaux fournisseurs sont entrés sur le marché.
Les sources laser
À l'origine, les imprimantes laser sur lit de poudre métallique utilisaient un laser CO2; aujourd'hui, le laser à fibre a pris le relais et certains fabricants expérimentent également les lasers à diode. Les niveaux de puissance sont aujourd'hui beaucoup plus élevés qu'auparavant. Dans les petites machines compactes, on travaille souvent avec des puissances de 250 à 500 watts; dans les grands systèmes AM, il s'agit de sources laser d'une puissance de 1.000 watts.
Pour gagner du temps, la technologie multi-laser a été développée: dans une machine, plusieurs faisceaux laser éclairent simultanément le lit de poudre. Au départ, il s'agissait de trois ou quatre lasers, par exemple 4x 500 ou 4x 1.000 watts, alors que des machines sont déjà construites avec 16 lasers ou plus.
Tous les fabricants ne participent pas à cette course. Certains limitent délibérément le nombre de lasers dans une machine. Ils invoquent non seulement les coûts d'investissement très élevés liés à l'utilisation de plusieurs sources laser, mais aussi le fait que l'apport de chaleur est plus difficile à contrôler. L'apport de chaleur est également plus difficile à contrôler lorsqu'il y a plusieurs lasers. Enfin, le risque de formation de fumée augmente lorsque les poudres métalliques sont fondues en plusieurs endroits du lit, de même que la formation de projections. La fumée et les projections de soudure peuvent affecter négativement le faisceau laser. Le flux de gaz dans la chambre de fabrication (gaz inerte, souvent de l'argon) est donc un aspect crucial dans une imprimante 3D métal.
En lieu et place d'un plus grand nombre de lasers, de nouvelles stratégies de balayage sont mises au point pour accroître la productivité. L'une d'entre elles consiste à ce que le laser n'attende pas que le dispositif de recouvrement expose la totalité de la couche de poudre, mais qu'il commence à l'exposer directement derrière le dispositif de recouvrement. La productivité peut ainsi être multipliée par 4.
La poudre
Dans la pratique, le procédé LPBF offre des avantages significatifs par rapport aux autres techniques d'impression 3D de métaux. Le plus grand avantage est que l'impression de métal sur lit de poudre laser produit la texture de surface la plus fine. Elle est beaucoup plus fine que la technique Wire Arc AM (WAAM), par exemple. Les propriétés mécaniques sont bonnes et de nombreux alliages sont désormais disponibles.
L'utilisation efficace des matériaux est un autre atout. On n'utilise que le matériau nécessaire au produit et peu de déchets de poudre. C'est très différent de certains produits de broyage pour lesquels jusqu'à 90% du matériau finit sous forme de copeaux.
Il convient toutefois de préciser que toute la poudre qui n'entre pas dans la pièce à usiner ne peut pas être réutilisée. Une partie de la poudre est affectée par la chaleur et peut s'agglomérer. C'est pourquoi la poudre est toujours tamisée avant le prochain travail de construction et il faut toujours mélanger de la poudre fraîche avec de la poudre usagée.
Le stockage de la poudre doit également faire l'objet d'une attention particulière. Non seulement pour garantir des conditions de travail sûres - il s'agit de nanoparticules - mais aussi pour assurer la qualité de la poudre. Les entreprises qui investissent dans la technologie LPBF doivent tenir compte du fait que le stockage et le transport de la poudre vers la machine nécessitent des investissements supplémentaires.
Étant donné que les coûts de production de la poudre sont élevés, en partie à cause de la composante énergétique, les coûts des matériaux sont beaucoup plus élevés que ce à quoi les gens sont habitués. Dans le produit final, ces coûts peuvent être inférieurs aux prévisions si l'on conçoit spécifiquement pour la fabrication additive et si l'on utilise l'optimisation de la topologie pour minimiser le poids. L'optimisation de la topologie est en fait une condition sine qua non pour cette forme d'impression métallique.
L'optimisation de la topologie est une condition sine qua non dans la fabrication additive, en raison des coûts des matériaux
Avantages de la LPBF: formes complexes
Étant donné que la chambre de construction est toujours remplie de poudre, la LPBF peut être utilisée pour créer des formes complexes, telles que des produits avec des contre-dépouilles ou des assemblages de composants. Comme les produits restent dans le lit de poudre, il est également possible d'imprimer des caractéristiques internes, telles que des canaux de refroidissement.
Actuellement, on voit de nombreuses applications où cette possibilité est décisive, par exemple pour les produits qui doivent être refroidis à l'intérieur. On peut alors placer les canaux de refroidissement près de la surface, exactement là où la plus grande partie de la chaleur doit être dissipée. Il est également possible d'optimiser les canaux de refroidissement afin de minimiser les turbulences, une application principalement utilisée par les fabricants de machines de précision.
L'intégration des fonctions est un autre avantage de la fabrication additive. Plusieurs pièces individuelles peuvent être imprimées en 3D en une seule fois, ce qui élimine les coûts d'assemblage. Cela a également une incidence sur les coûts de la chaîne d'approvisionnement.
Inconvénients de la LPBF: une technologie complexe et coûteuse
La précision avec laquelle on imprime en 3D avec la LPBF est relativement élevée par rapport à d'autres techniques de fabrication additive. Mais on n'atteindra jamais la précision et la rugosité de surface que l'on peut obtenir avec les techniques d'usinage, par exemple, parce qu'il s'agit essentiellement de souder deux particules de poudre ensemble.
Même la plus petite particule de poudre est beaucoup plus grossière qu'un morceau de métal fraisé ou poinçonné avec précision. Il faudra donc presque toujours procéder à un post-traitement, ce qui nécessite une attention particulière au début du processus. Par exemple, il faut s'assurer que les pièces complexes peuvent encore être serrées sans tension si un post-fraisage est nécessaire.
Toutefois, les deux principaux inconvénients de la technologie LPBF sont qu'il s'agit d'une technique complexe et coûteuse. Les coûts élevés sont en partie dus à la technologie laser. En outre, les entreprises sous-estiment souvent les coûts supplémentaires, par exemple pour le stockage de la poudre métallique, en particulier si elle doit être stockée dans un environnement conforme à la norme ATEX.
La complexité tient au fait que le résultat final dépend de nombreux facteurs. L'apport de chaleur dans la pièce à usiner peut changer la donne, par exemple en provoquant des déformations. Si un logiciel de simulation peut être utilisé pour réduire ce problème, l'éliminer complètement nécessite un processus de longue haleine.
Pour dissiper la chaleur, des structures de support sont souvent nécessaires. Cela implique un temps d'impression - et un matériau - supplémentaires, ainsi qu'un traitement ultérieur car elles doivent toutes être retirées à nouveau. L'industrie de la fabrication additive tente de réduire cet inconvénient en proposant à la fois des logiciels d'optimisation de ces structures de support et un système de retrait automatique.
Garantir la qualité
La validation d'un processus de fabrication additive peut prendre beaucoup de temps, surtout s'il s'agit de pièces critiques nécessitant une certification. Cela s'explique en partie par le fait que la façon dont on positionne une pièce sur la plaque de construction affecte les propriétés du matériau.
Contrairement à ce qui se passe couramment dans l'industrie métallurgique, les matériaux ne sont pas standardisés. En effet, les propriétés ne sont en grande partie déterminées qu'au cours du processus d'impression lui-même. C'est pourquoi une approche intégrale de l'ensemble du processus est considérée comme un facteur de réussite essentiel: l'ingénieur concepteur, le planificateur du travail et l'opérateur du processus sont conjointement responsables de la qualité du produit final.
Et comme il n'est pas possible de contrôler chaque pièce à l'aide de scanners, par exemple, le contrôle statistique des processus (CSP) est nécessaire pour garantir la qualité. Dans la production en série, la qualité d'une pièce en fabrication additive doit être assurée dès le processus. Les fabricants répondent à cette exigence par des systèmes de surveillance du bain de fusion, entre autres, qui utilisent des caméras à grande vitesse pour collecter des données sur le processus de fusion. L'apprentissage automatique est utilisé pour détecter tout écart dans une couche. Il appartient ensuite à l'ingénieur en charge du processus de déterminer si un écart est acceptable ou non.
Une approche globale du processus est le plus grand obstacle à surmonter lors du lancement de l'impression 3D de métaux
La surveillance in situ n'est pas au point
Cependant, l'institut de normalisation américain ASTM International a noté dans une étude réalisée l'année dernière que la surveillance in situ présentait encore des lacunes. La surveillance du bain de fusion est l'une des techniques ISM, au même titre que la surveillance du dépôt de matériaux et la surveillance globale du processus.
Les chercheurs interrogés par ASTM International concluent que les résultats de ces systèmes de surveillance des processus sont insuffisants pour certifier les pièces qui en sont équipées. Ils soulignent qu'une boucle fermée-où les réglages sont modifiés en fonction des valeurs trouvées, n'est pas compatible avec les normes actuelles. En effet, celles-ci supposent que les paramètres ne sont pas modifiés après la validation.
Si l'apprentissage automatique est considéré comme prometteur, il reste encore un certain nombre de défis à relever. Le principal obstacle réside dans le fait qu'une énorme quantité de données est nécessaire pour entraîner les algorithmes d'apprentissage automatique.
Intégration avec la CAO/FAO
L'approche intégrale de la fabrication additive est adoptée par le marché. Cela se traduit, par exemple, par le fait qu'un nombre croissant de développeurs de CAO/FAO proposent des logiciels qui préparent à la fois le travail de construction pour l'imprimante à métaux et la fraiseuse à commande numérique pour le post-traitement. Cela permet non seulement de gagner du temps dans la préparation du travail, mais aussi de l'automatiser, car les modifications apportées à la conception peuvent être immédiatement évaluées en fonction de leurs conséquences pour le post-traitement.
Lors de la programmation de l'imprimante 3D métal, il est également possible d'inclure du matériel supplémentaire, par exemple pour faciliter le serrage de la pièce. Des études montrent que les coûts de l'impression 3D métal sont principalement liés à tout ce qui se passe autour du processus d'impression proprement dit. En fonction de la complexité et de l'importance du post-traitement, ce coût peut atteindre 80% et plus.
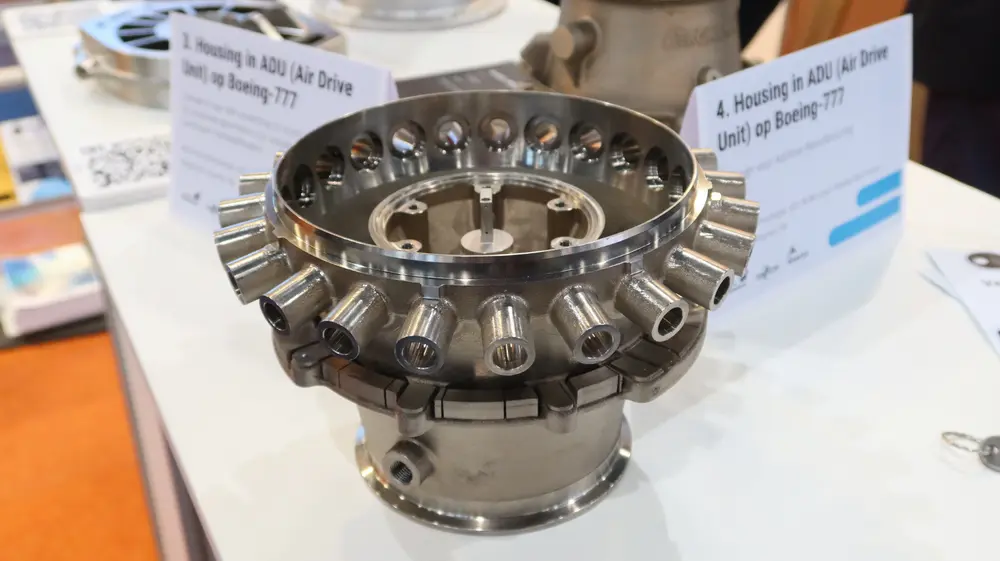
Conclusion
La technologie LPBF reste la technologie de choix pour la fabrication additive de composants haute performance. Mais cette technologie ne va pas simplement remplacer les autres techniques de fabrication. La valeur ajoutée de la fabrication additive doit clairement être recherchée pour que les investissements soient rentables. Pour ce faire, il faut aller au-delà des simples coûts de production.
En outre, la technologie nécessite une approche intégrale du processus, car l'optimisation d'un aspect partiel du processus de fabrication additive peut conduire à un résultat total sous-optimal. La co-impression de matériaux supplémentaires, qui augmente directement les coûts, peut permettre d'économiser tellement dans le post-traitement que le coût total est inférieur. Cette approche holistique est peut-être le plus grand obstacle à surmonter lorsqu'on se lance dans l'impression 3D de métaux.