Les systèmes d'outils modulaires ont le vent en poupe
Des concepts normalisés et modulaires à la base de tout
Les systèmes d'outils modulaires sont de plus en plus utilisés en raison de leur capacité à créer un ensemble personnalisé pour une application spécifique à partir d'articles standard. La normalisation est donc grandement facilitée par le fait que les ensembles d'outils optimisés prennent en charge une large gamme d'applications et de machines. En outre, les outils modulaires réduisent les stocks d'outils et accélèrent la préparation de l'outillage en permettant d'assembler une large gamme d'outils à partir d'un nombre limité de composants interchangeables.
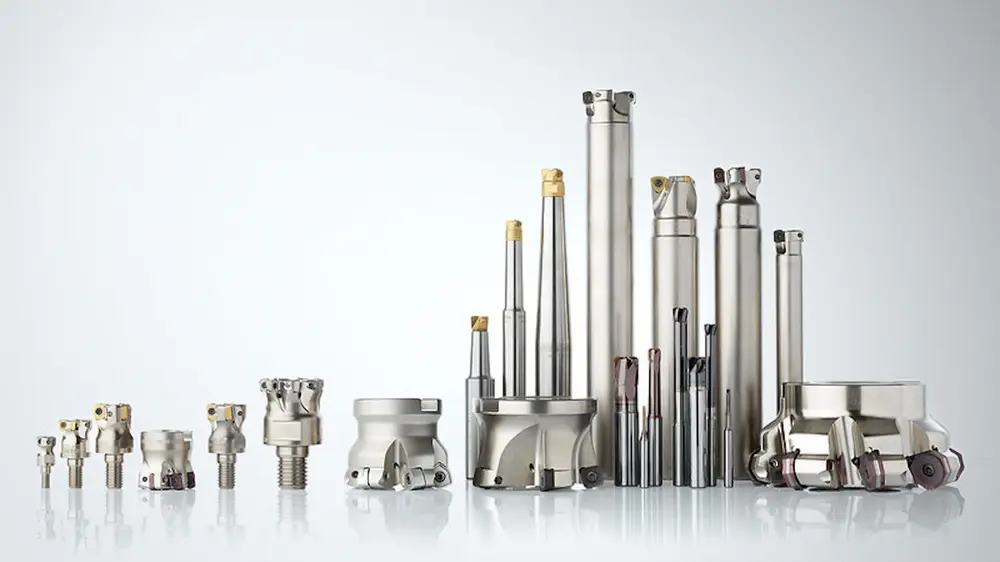
pour une application spécifique (Seco Tools)
Configurations
Un système modulaire peut être comparé à un outil de jardinage de Gardena, par exemple. Tous les types d'accessoires peuvent être placés sur un seul et même manche ou accessoire au moyen d'un système de fixation tout aussi simple et efficace. Le principe de base est le même, mais une configuration modulaire dans l'industrie de transformation exige un concept beaucoup plus complexe. Cette nouvelle tendance nous vient des fabricants d'outils de coupe. Initialement conçu et développé pour les opérations de tournage, le concept d'outil modulaire s'est rapidement avéré avoir un potentiel pour toute une gamme de machines-outils, et pas seulement pour les versions CNC.
Les outils dont la configuration est facilement modifiable réduisent les stocks d'outils et accélèrent la préparation des outils, notamment parce qu'une large gamme d'outils peut être assemblée à partir d'un nombre limité de composants interchangeables. C'est pourquoi l'intérêt pour les outils modulaires ne cesse de croître, car pourquoi dépenser des milles et des cents pour des outils séparés pour chaque machine, composant et/ou fonction, alors que vous pouvez disposer d'une solution standardisée pour toutes les machines, où que vous vous trouviez dans l'atelier ?
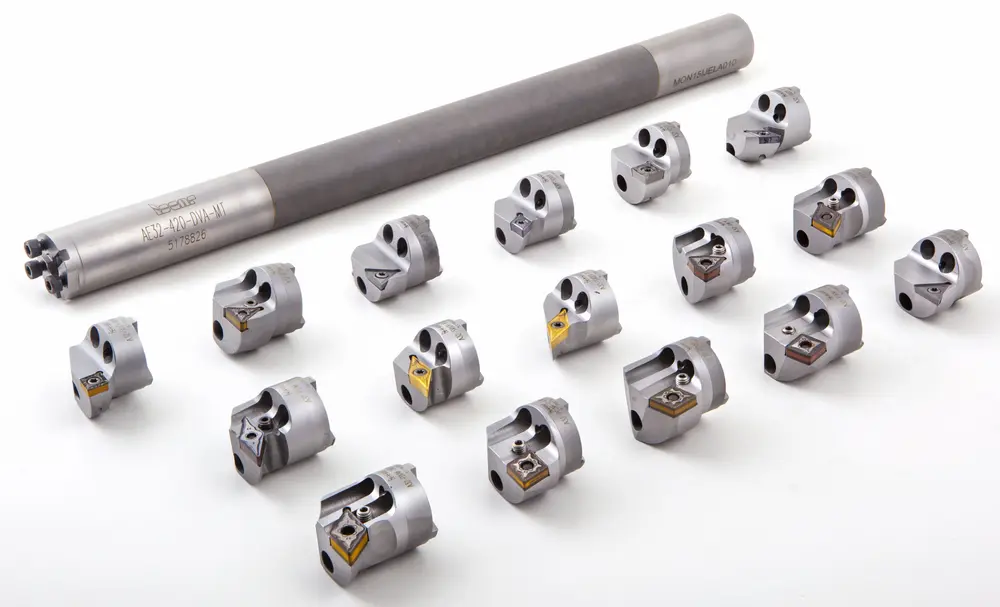
"Les outils dont la configuration est facilement modifiable réduisent le stock d'outils et accélèrent leur préparation"
Éléments de construction
Les systèmes d'outillage modulaires - à ne pas confondre avec les systèmes à changement rapide - permettent d'utiliser une sélection d'éléments de base pour construire un assemblage personnalisé pour une application spécifique. Cela rappelle un peu les blocs 'Lego'. Même avec un nombre relativement faible d'éléments 'de construction" - par exemple des outils de tournage ou de coupe, des têtes de fraisage, des forets et/ou des ciseaux - l'utilisateur peut réaliser un grand nombre de combinaisons. Cela ouvre la possibilité d'utiliser des systèmes d'outils correspondants dans toute l'usine, indépendamment de l'interface machine. Au lieu de changer l'outil entier, seule une partie spécifique est modifiée. Par exemple, lors du perçage, ce ne sont pas le foret en carbure et la tige qui sont remplacés dans leur ensemble, mais uniquement l'outil de coupe, car seule cette partie est soumise à l'usure.
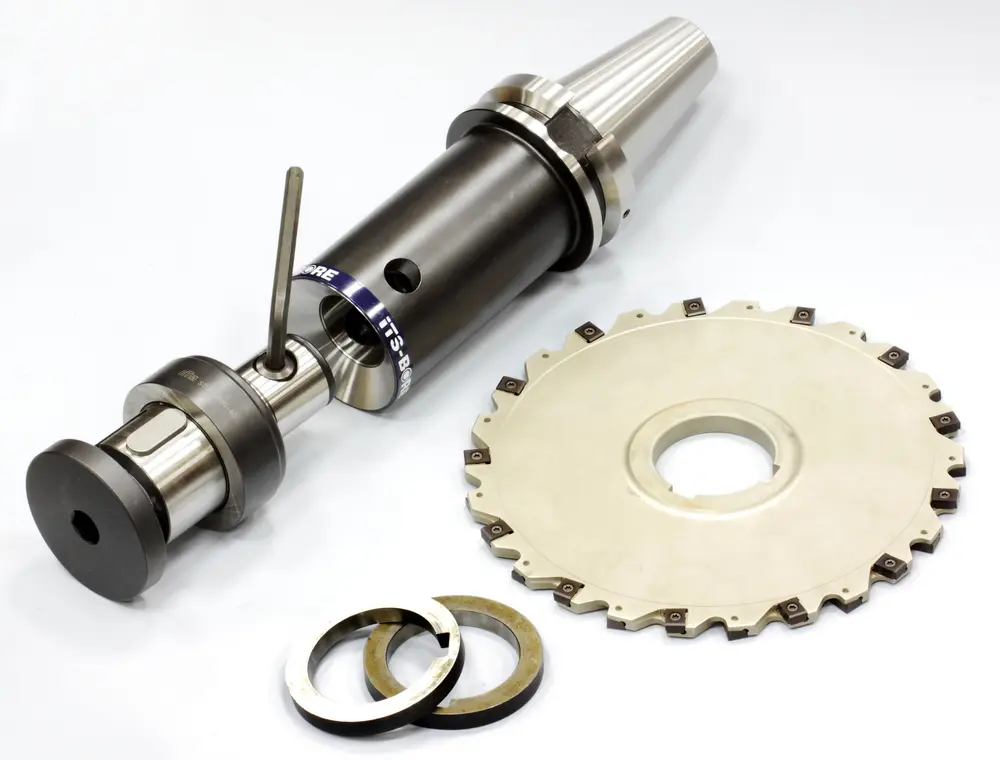
Montage de l'outil
L'expérience montre qu'il est important de réduire autant que possible le facteur humain lors du montage des outils. Dans ce contexte, on distingue actuellement trois niveaux :
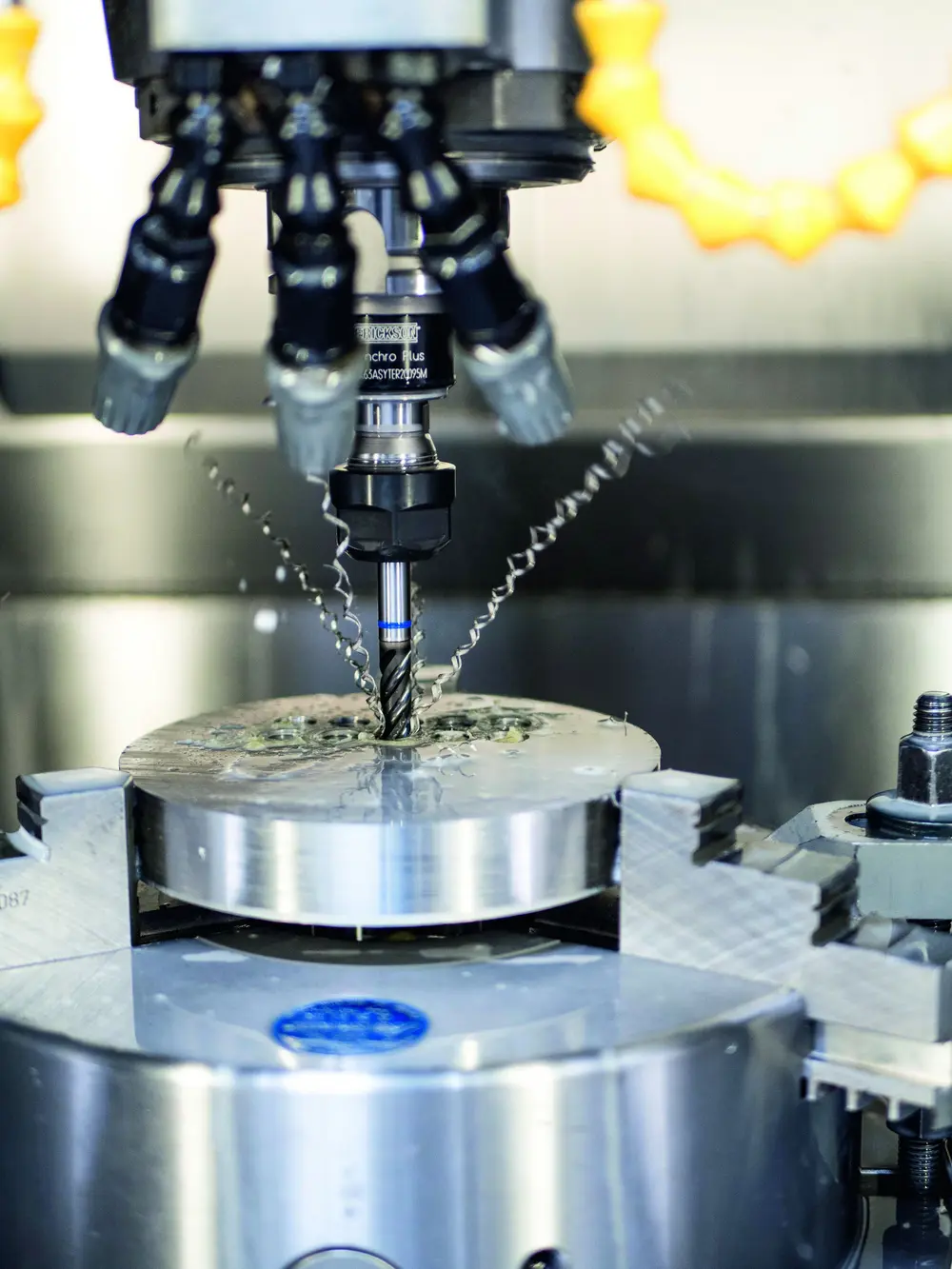
Assemblage non automatisé. Cela se fait sur la base des connaissances de l'opérateur/outilleur. Les outils sont sélectionnés parmi ceux qui sont disponibles sans contrôle supplémentaire et/ou stratégies d'usinage, et il n'y a pas de gestion supplémentaire des outils. Il est important de sélectionner les lignes d'outils et de les documenter dans un système de gestion des outils avec un manuel pour l'assemblage des outils respectifs.
L'assemblage partiellement automatisé. Cela se fait conformément aux spécifications et aux instructions de montage du fournisseur. Les stratégies d'usinage ne sont pas optimisées et le choix d'un outil particulier n'est pas documenté dans un système de gestion des outils. Le changement d'outil manuel peut être automatisé à l'aide d'un changeur d'outil, lorsque cela est nécessaire et souhaité.
L'assemblage entièrement automatisé. Là encore, l'outillage est assemblé selon les spécifications et les instructions de montage du fournisseur, mais à ce niveau, il est réalisé par un robot ou une machine. Les stratégies d'usinage sont entièrement mises en œuvre dans le processus d'usinage et les outils eux-mêmes sont définis dans des systèmes de gestion des outils.
SYSTÈMES DE CHANGEMENT RAPIDE
Les systèmes d'outillage modulaire sont parfois confondus avec les systèmes d'outillage à changement rapide. Ces systèmes fournissent une interface entre l'outil réel et le porte-outil dans la broche. Avec un tel adaptateur, un outil peut être réglé à l'extérieur de la machine et le changement effectif ne prend qu'une fraction du temps nécessaire au réglage à l'intérieur de la machine. Il s'agit notamment de porte-outils à changement rapide avec intégration directe dans la broche et d'une grande variété d'extensions et d'adaptateurs de réduction. Cela permet de combiner des outils de différentes longueurs et caractéristiques de conception, indépendamment de l'accouplement de la machine. Contrairement à un système d'outils modulaire, un système de changement rapide n'est pas dépendant du fournisseur. Tant que l'outil est adapté à l'adaptateur choisi, on est libre dans le choix de l'outil et du fabricant de l'outil.
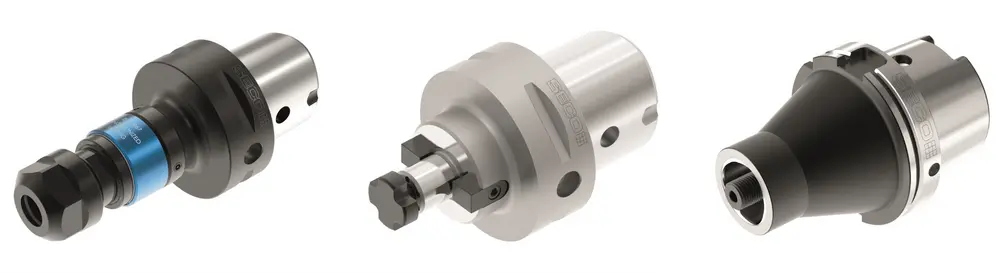
Photo (cadre) : Dans un certain nombre de cas, un système modulaire et un système de changement rapide sont combinés. Un exemple fréquemment utilisé est le Capto, également défini dans la norme ISO (Seco Tools)
Spécifique
Ces dernières années, un grand nombre de fabricants se sont concentrés sur le développement et la production de systèmes d'outils modulaires. Ce faisant, ils s'emploient à répondre aux exigences que les clients imposent à ces systèmes, exigences qui s'ajoutent à leur tour à la demande de produits, laquelle fluctue généralement : parfois, les mêmes pièces sont nécessaires en grandes quantités, parfois elles sont très variables et il suffit d'en produire un petit nombre. Les systèmes d'outillage modulaires sont donc disponibles à la fois dans des versions standard et dans des solutions spécifiques au client. Par exemple, il existe des systèmes dans lesquels le pré-usinage et le post-usinage sont intégrés dans le même système d'outils. Cela permet d'économiser un espace supplémentaire dans le magasin d'outils, mais surtout, le fait de travailler de cette manière entraîne une augmentation considérable de la productivité. L'inconvénient, pour ainsi dire, des systèmes d'outillage modulaires est qu'ils constituent généralement une solution liée à un fabricant spécifique, et souvent aussi à une ligne d'outils spécifique.
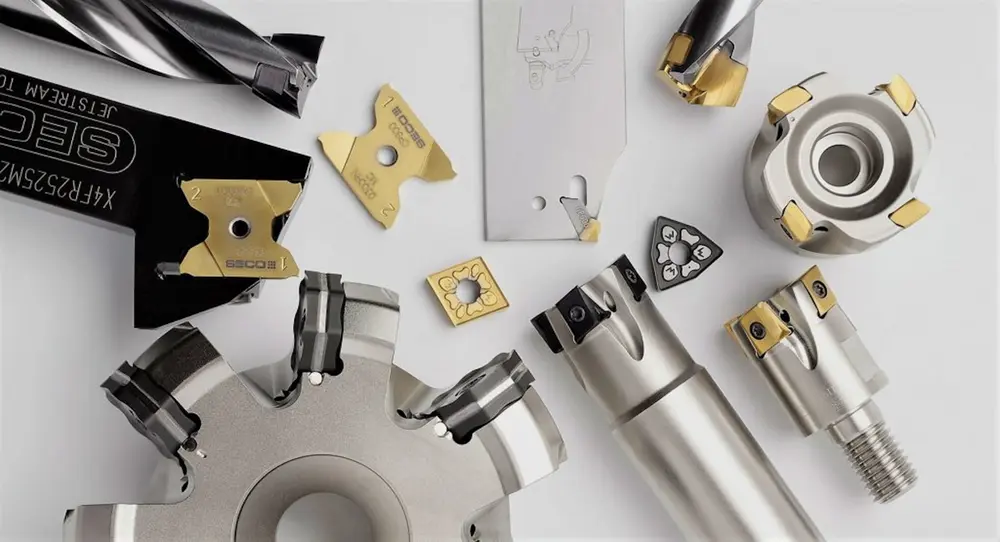
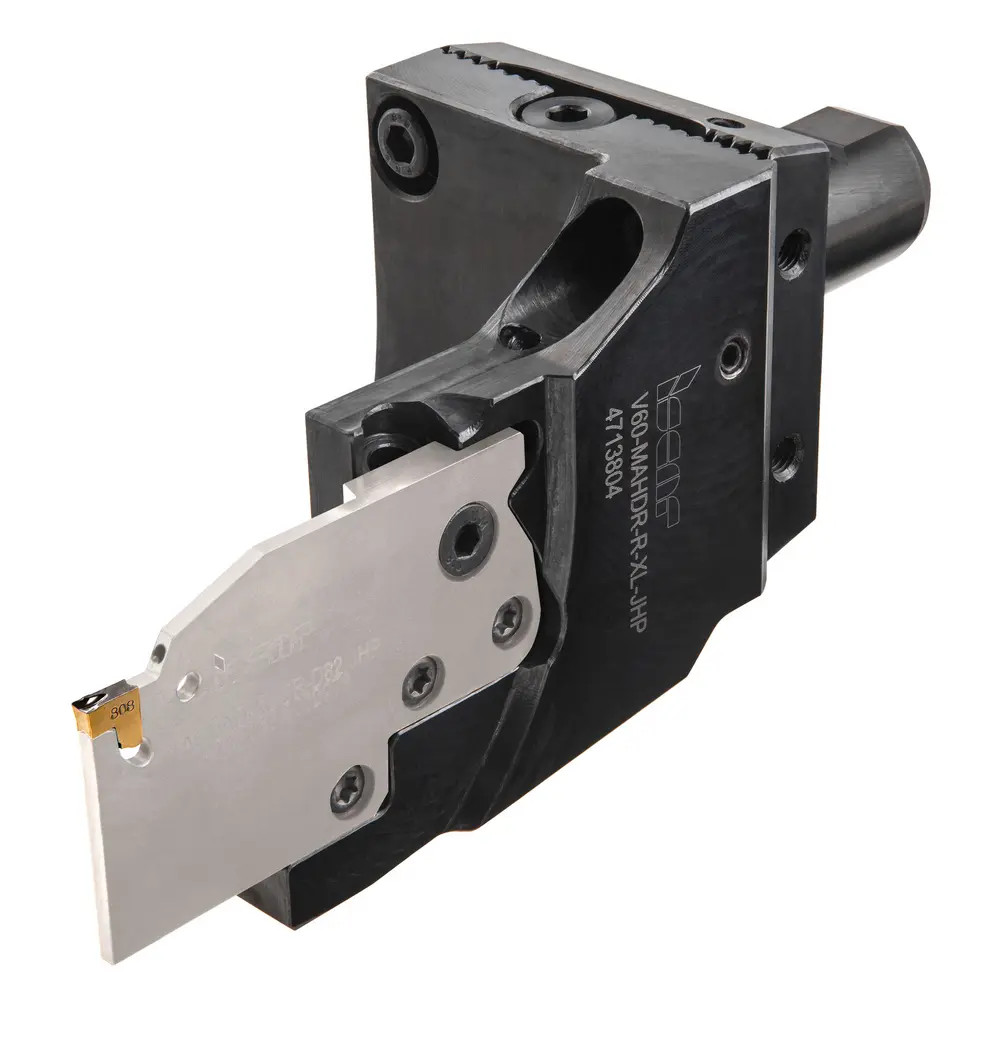
État d'esprit
Les outils modulaires peuvent apporter une contribution importante à la standardisation des processus de production dans les entreprises de métallurgie. La VDMA - la plus grande organisation de réseau et un important porte-parole de l'ingénierie mécanique européenne - formule son influence comme suit : La normalisation et la modularisation visent à obtenir un portefeuille présentant moins de variations et de complexité et un niveau de coût global plus faible, sans réduire l'étendue et l'individualité de la gamme de produits. À titre d'exemple, des recherches ont montré que l'utilisation d'outils modulaires et rapidement interchangeables pendant la durée de vie de la machine peut réduire les coûts d'outillage jusqu'à 40 %.
Mais qu'il s'agisse de modularité, de fonction de changement rapide ou d'une combinaison des deux, ces applications ne porteront leurs fruits de manière optimale que si elles s'accompagnent de changements structurels au sein de l'organisation. Lorsqu'on travaille avec de tels systèmes, un tiers concerne le matériel, un tiers l'information et un tiers la discipline. Ce dernier point requiert un état d'esprit différent et la formation joue ici un rôle crucial. Non seulement les opérateurs de machines et les gestionnaires d'outils doivent savoir comment travailler avec ces applications, mais les ingénieurs de processus, les programmeurs CN, les estimateurs, les planificateurs, les inspecteurs et les gestionnaires doivent être conscients de ce que le nouveau système implique et des conséquences de son utilisation sur la façon dont la production future se déroulera.
"Des recherches ont montré que l'utilisation d'outils modulaires à changement rapide pendant la durée de vie de la machine peut réduire les coûts d'outillage jusqu'à 40 %"
CONSEILS POUR LES OUTILS
Comme nous le savons tous, s'équiper de bons outils, c'est déjà la moitié du travail, mais avoir le bon outil au bon moment reste souvent un tour de force. Quelques conseils à cet égard :
- ne mélangez pas différents systèmes d'outils ;
- regardez ce qu'un fournisseur a de plus à offrir, y compris la documentation technique et le support technique ;
- assurez-vous que tous les outils sont correctement documentés et prévoyez également un bon système de stockage ;
- assurez-vous que le système de gestion des stocks est le plus optimal possible, de sorte que tous les outils soient effectivement disponibles au moment où l'on en a besoin ;
- veillez à ce que tous les outils soient immédiatement prêts à l'emploi, de sorte que l'on ne perde pas de temps à affûter les ciseaux, par exemple ;
- examinez s'il est possible de travailler avec des outils qui peuvent effectuer plusieurs opérations dans un seul et même serrage.
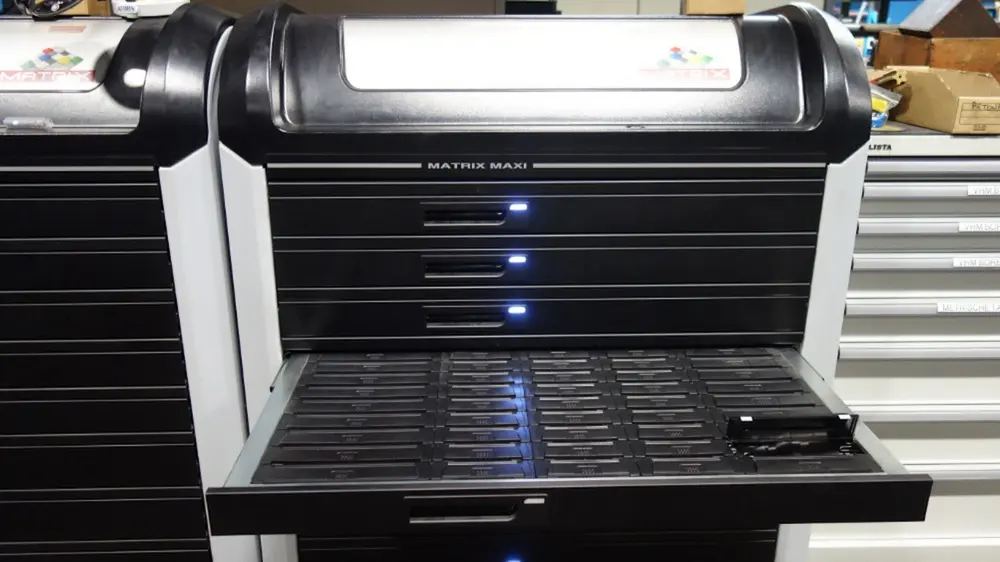
Merci à : Iscar, Hoffmann Group et Seco Tools