Automatiser la gestion de l'outillage permet un processus fluide
À mesure que la production s'automatise, une bonne gestion de l'outillage devient de plus en plus importante. La gestion des outils permet non seulement de réduire le risque d'erreur et les coûts d'outillage, mais aussi de garantir un processus d'usinage automatisé plus stable en vous donnant une meilleure idée de la durée de vie de l'outil.
Centraliser le stock d'outils
La situation où chaque opérateur CNC dispose près de sa machine de son propre stock d'outils, de fraises VHM, de porte-outils et de plaquettes, disparaît progressivement. Dans de nombreuses entreprises, le stockage des outils est déjà centralisé à un ou plusieurs endroits, éventuellement avec un système de distribution.
Ces armoires intelligentes ont d'abord été considérées avec méfiance: serait-ce une manoeuvre du fournisseur pour que nous n'utilisions plus que ses outils? Cette idée est en train de disparaître, notamment parce que des systèmes indépendants ont également fait leur apparition sur le marché. Aujourd'hui, les systèmes de distribution ont souvent des interfaces ouvertes pour faciliter leur connexion.
Économiser de l'argent
La centralisation et la numérisation des stocks d'outils peuvent permettre aux entreprises d'usinage d'économiser beaucoup d'argent. Une étude réalisée il y a quelques années par un fabricant suédois d'outils d'usinage a montré que, dans certaines entreprises, jusqu'à 60% des outils ne sont jamais utilisés. Ce chiffre est peut-être légèrement exagéré.
Un autre chiffre tiré de la même étude semble plus réaliste: 15% des commandes prennent du retard parce que les outils ne sont pas disponibles à temps. Et si les entreprises ne structurent pas la gestion de l'outillage, les opérateurs passent beaucoup d'heures chaque semaine à chercher des outils d'usinage.
L'avantage logistique d'une bonne gestion des outils se traduit par des résultats immédiats. En euros, mais plus encore en termes de fluidité de la production. Un fabricant allemand, qui fabrique notamment des dispositifs de préréglage, estime que l'introduction d'un tool management system et de la numérisation associée permet de réduire les coûts de 20% par rapport au coût d'outillage total.
La centralisation et la numérisation du stock d'outils peuvent permettre aux entreprises d'usinage d'économiser beaucoup d'argent
Conseils simples pour une bonne gestion de l'outillage
Système de distribution
L'étape la plus simple pour une bonne gestion consiste à installer un système de gestion des outils relié au système ERP, ainsi qu'aux systèmes de planification de la production et de FAO. Ce système surveille automatiquement le stock et, en fonction des accords conclus avec le fournisseur, commande automatiquement de nouveaux outils lorsque le stock descend en dessous d'un seuil critique.
Le deuxième avantage d'un tel système est qu'il est pratiquement impossible pour l'opérateur de se tromper d'outil. En effet, lorsqu'on scanne le QR code, c'est le bon tiroir qui s'ouvre. De cette manière, les entreprises d'usinage réduisent directement le coût pour la gestion de leurs outils.
(Ré)utilisation des données d'outils
L'étape suivante consiste à réutiliser plus souvent les données relatives aux outils. Ceux qui ne souhaitent pas encore passer à un système entièrement numérisé et automatisé peuvent utiliser une puce dans le porte-outil ou des codes sur les outils pour éviter les réglages incorrects sur la machine et obtenir un aperçu de l'utilisation de l'outil.
Cela peut se faire, par exemple, en équipant les porte-outils de puces RFID sur lesquelles les données sont écrites. Outre leur coût, ces puces présentent l'inconvénient que les porte-outils sont moins faciles à changer entre les différentes marques de machines CNC car la manière dont les données sont écrites et lues diffère d'un fabricant à l'autre. Les QR codes constituent donc une alternative plus flexible.
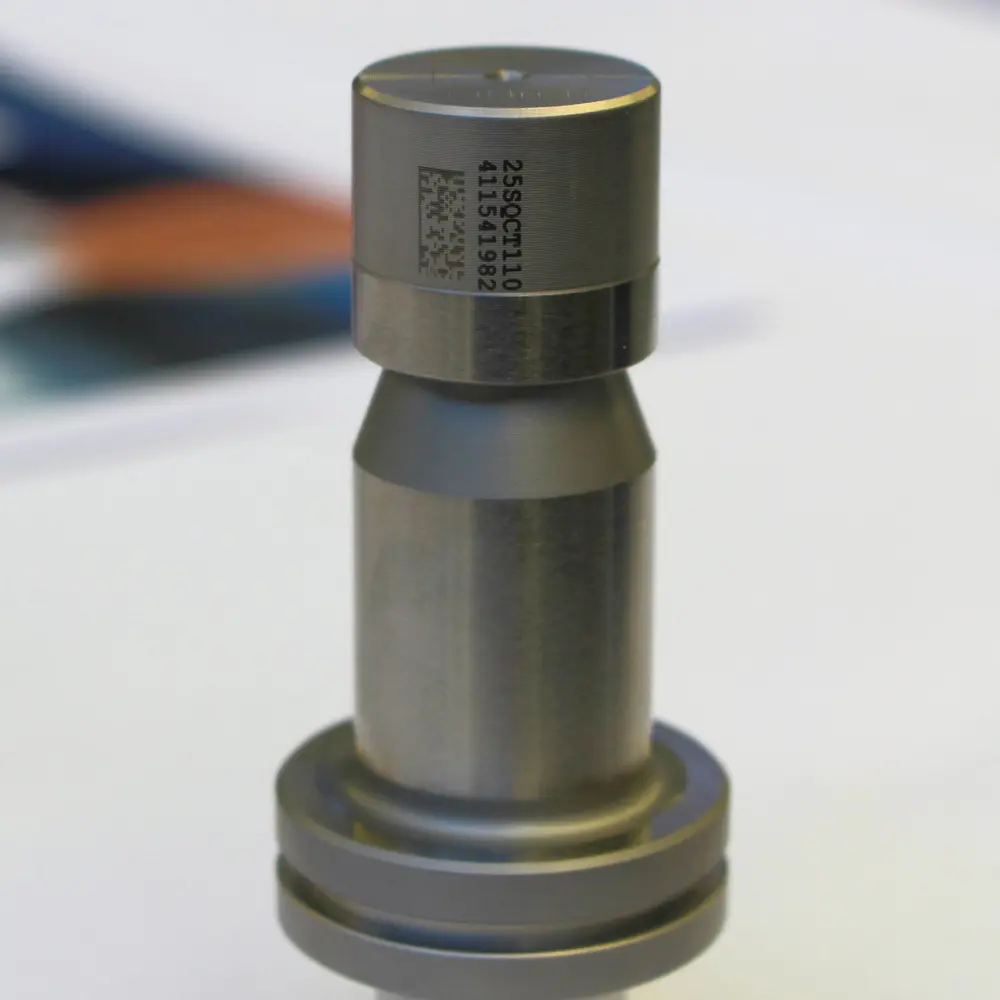
Le code Datamatrix, composé de points et de carrés, est la troisième solution. Ce code est appliqué une fois dans le porte-outil - généralement à l'aide d'un laser de gravure - et peut ensuite être lu à l'aide d'un scanner portable à différentes étapes du processus, tout comme le QR code.
Ce code Datamatrix ne contient aucune information en soi, mais seulement un lien vers la base de données où les informations sur l'outil sont constamment mises à jour. Lorsqu'une fraise est changée dans le porte-outil, les données de réglage de la nouvelle fraise sont introduites dans le fichier lié au code Datamatrix unique. En scannant le code, toutes les données sont disponibles. Cette opération peut être effectuée manuellement, mais aussi automatiquement.
Plan à étapes pour l'implémentation
Pour ceux qui en doutent encore, les avantages qui peuvent être obtenus à un stade plus avancé du processus de production sont plus importants que les économies immédiates de temps et d'argent. La numérisation du tool management se traduit par un processus fluide, dans lequel les données de réglage sont transmises à la machine via le réseau et les durées de vie des outils sont disponibles en ligne ailleurs dans l'entreprise.
L'Industrie 4.0 ouvre de nouvelles perspectives dans ce domaine, mais elle oblige les entreprises à adapter leurs méthodes de travail. C'est peut-être là que réside le plus grand défi si l'on veut franchir cette étape. Cela nécessite également un investissement, car le modèle 3D de tous les outils doit être disponible dans les différents systèmes logiciels avec lesquels on travaille.
Examiner le stock d'outils
Cela peut demander un investissement en temps considérable mais c'est aussi l'occasion d'examiner en profondeur l'arsenal d'outils. Tous ces outils sont-ils vraiment nécessaires? N'y a-t-il pas de chevauchements? L'utilisation des outils est-elle standardisée ou chaque opérateur ou programmeur FAO a-t-il ses propres préférences? La standardisation, qui consiste à utiliser le même outil à chaque fois pour une opération donnée, peut être bénéfique à bien des égards et rendre le processus plus clair.
Évaluer la gestion actuelle des outils et choisir le bon système d'émission
Pour commencer à implémenter un système de gestion des outils numérique, les PME doivent d'abord évaluer leurs processus actuels et identifier les points sensibles spécifiques. Cela implique d'évaluer les méthodes de travail existantes pour la gestion des outils et d'identifier les inefficacités. Il est essentiel de choisir une solution évolutive qui puisse s'adapter à la croissance de l'entreprise.
Prérégler les outils
L'étape suivante consiste à mettre les données à la disposition du logiciel de FAO et de la commande de la machine en effectuant un préréglage à l'aide d'un dispositif de préréglage. Vous préférez utiliser des modèles ou des données réelles à cet effet? Aujourd'hui, il existe de nombreuses bases de données contenant des modèles 3D d'outils. Elles conviennent parfaitement pour alimenter votre propre base de données FAO.
Mais pour la programmation proprement dite, un système de gestion d'outils avancé offre des avantages si le processus est correctement configuré. Il s'agit notamment de mesurer à nouveau les outils après leur utilisation. En ajoutant ces données au système de gestion des outils, les programmeurs FAO pourront programmer avec des données réelles la prochaine fois.
Cela permet également d'obtenir une image réelle de la durée de vie restante de l'outil. En fait, on construit un jumeau numérique de l'outil avec les données de production et ces informations peuvent être utilisées à plusieurs endroits dans l'entreprise.
La norme ISO 13399 s'applique à l'échange de ces données d'outils (à la fois celles de l'outil de coupe et celles du porte-outil). Cette norme décrit notamment un format de données neutre qui facilite l'échange de données entre différents systèmes. Non seulement avec les systèmes de gestion d'outils, mais aussi avec les systèmes PLM, PDM et ERP, les logiciels de CFAO, etc.
L'utilisation de données réelles et d'un système de gestion d'outils est indispensable si l'on veut automatiser davantage la production et usiner des petits lots ou même des pièces uniques (dans le cas de commandes répétées) avec une faible intervention humaine. Dès qu'un outil est sélectionné, le système vérifie s'il est déjà présent dans la machine, quelle est sa durée de vie et si elle est suffisante pour l'opération programmée. Cela permet d'éviter les arrêts de production imprévus ou les rejets pendant la nuit parce qu'un outil présente une usure trop importante.
L'utilisation de données réelles et d'un système de gestion d'outils est indispensable si l'on veut automatiser davantage la production et usiner des petits lots ou même des pièces uniques (dans le cas de commandes répétées) avec une faible intervention humaine
Préréglage automatisé
Le préréglage des outils est encore loin d'être généralisé dans l'usinage. Ce qui est encore unique, c'est le (pré)réglage automatisé des outils. Néanmoins, les premiers systèmes ont été présentés dans ce domaine également. Ici, un cobot prend en charge l'assemblage de l'outil à la place de l'opérateur CNC et, après l'assemblage, le cobot place l'outil dans un dispositif de préréglage pour la mesure ou dans un dispositif d'équilibrage ou de sertissage.
Le développement de ces cellules de réglage d'outils en est encore à ses débuts. Pour beaucoup d'entreprises, il reste pour l'instant une lointaine réalité, mais celles qui changent souvent d'outils pourront en tirer profit. En particulier lorsqu'une telle cellule est reliée à un AGV, la gestion des outils et leur distribution aux machines peuvent être encore plus automatisées.
Il n'est pas surprenant de constater une tendance à déplacer l'accès au magasin d'outils vers l'avant sur les machines. Pour l'opérateur qui place lui-même les outils dans la machine, il s'agit d'une solution ergonomique; pour ceux qui veulent automatiser davantage, c'est nécessaire car le magasin devient alors accessible à un AGV avec cobot.
Faut-il de nouveaux modèles de revenus?
La distribution d'outils pour l'usinage des métaux se caractérise par un grand nombre de petits acteurs qui fournissent des outils aux PME. Les experts du secteur s'attendent à ce que la numérisation finisse par affecter le modèle de revenus de ces fournisseurs et à ce qu'ils doivent se repositionner.
Il est certain que les outils standard deviennent de plus en plus des produits de base. Les petits acteurs devront donc trouver un créneau ou se faire connaître en tant que solutionneurs de problèmes. Grâce à leurs connaissances, ils peuvent aider leurs clients à optimiser leurs processus.
Les grands équipementiers de l'industrie de l'outillage cherchent également de nouveaux modèles de revenus pour leurs gros clients. Certains proposent à leurs plus gros clients des outils en tant que service et prennent en charge la gestion complète, depuis la commande et la gestion jusqu'au préréglage, ce qu'ils font avec leurs propres collaborateurs, qu'ils envoient chez le client final.