Un nouveau regard sur la surveillance de l'usure des outils de coupe
Le projet TETRA 'WearAI' a été lancé en 2020 en réponse à la demande croissante d'un flux de travail clair pour la surveillance des machines. Dans ce projet, la Haute Ecole VIVES, la KU Leuven et VLAIO travaillent ensemble pour introduire des techniques de pointe à un niveau prêt à l'emploi, c'est-à-dire prêt à être déployé directement dans le contexte industriel. Le projet se concentre sur l'exploitation du Machine Learning (ML) dans l'analyse de l'usure des outils. Il soulignait déjà la valeur ajoutée du ML prédictif mais en même temps, l'importance de caractéristiques d'usure correctes est devenue évidente. Sans mesures ou observations fiables, même les algorithmes les plus avancés peuvent être perturbés. C'est pourquoi, dans cet article, nous passons brièvement en revue les principes de base et fournissons de précieuses indications sur la dégradation des outils, acquises au cours d'études de cas pratiques du projet TEchnology TRAnsfer (TETRA).
Introduction
La recherche a montré que même de simples algorithmes d'apprentissage automatique peuvent prédire de manière fiable l'état d'usure des outils, mais uniquement dans des conditions optimales. Les flux de données mesurées doivent contenir des caractéristiques d'usure des outils fortement corrélées, qui servent d'input pour le ML. Les indicateurs directs, comme l'usure des flancs, sont difficiles (voire impossibles) à mesurer en dehors des conditions de laboratoire. Pourtant, il y a de grands avantages à le faire.
Pour concevoir ces algorithmes, il est essentiel de connaître les principaux concepts et de bien comprendre l'évolution de la dégradation des matériaux. L'usure suit principalement deux courbes différentes. L'une est presque linéaire sur toute la durée de vie, la seconde (voir Figure 1) est plus complexe mais plus d'application. Elle se caractérise par une usure initiale rapide, une augmentation linéaire de l'usure au milieu de la durée de vie de l'outil et enfin une augmentation rapide de l'usure avant la rupture complète de l'outil.
Vous trouverez de plus amples informations dans la norme ISO 3685:1996.
Comment fonctionne l'usure?
L'adhérence, l'abrasion et la diffusion sont les trois effets qui influencent le plus la déformation géométrique de l'outil de coupe. L'adhérence se produit lorsque le matériau à travailler adhère à l'outil à cause du frottement entre l'un et l'autre. Lorsque ces liens sont rompus, des petits morceaux de l'outil sont perdus. L'abrasion est une usure mécanique causée par l'action de coupe, où l'outil se déplace sur le matériau à travailler. L'usure par diffusion se produit dans une zone de réaction étroite entre l'outil et le matériau à travailler. Les atomes de l'outil se déplacent vers le matériau à travailler. Cela accélère généralement les deux autres processus d'usure (adhérence et abrasion), car le matériau de l'outil s'affaiblit au fur et à mesure du processus.
À quoi ressemble l'usure?
La Figure 2 montre l'usure du flanc (1), l'usure en cratère (2), l'usure en entaille/notch de la face de dégagement (3), l'usure du sommet (4) et l'usure en entaille/notch de la face d'attaque(5). L'usure du flanc est causée par l'abrasion mécanique après interaction de particules de matériau dur avec l'outil. L'usure en cratère est causée par l'abrasion mécanique lorsque des particules métalliques dures présentes dans le copeau (oxydes, carbures ...) frappent la surface d'attaque. Ce processus peut être accéléré par la diffusion entre le matériau et le ciseau. L'usure en entaille est également due à l'abrasion mécanique, tout comme l'usure des flancs. Si de longues bandes se forment entre les bandes petites/courtes, cela peut être dû à une déformation de la surface lors d'une étape précédente. L'entaille peut également se produire sur la surface d'attaque. Les fissures en peigne sont des petites fissures dans le sens longitudinal de l'arête de coupe, causées par des oscillations thermiques répétitives qui provoquent la dilatation et la contraction du matériau. Cela crée des fissures et du chipping. Le chipping est la perte de matière de l'outil au niveau de l'arête de coupe, souvent due à des contraintes thermiques. Enfin, une déformation plastique peut se produire au niveau de l'arête de coupe. Le matériau de l'outil de coupe s'affaiblit en raison de la surchauffe.
FIGURE 2: Illustration des types d'usure courants
La relation entre l'usure et la force de coupe est évidente. Des forces de coupe élevées sur de longues périodes de temps entraîneront une usure accélérée. En ajustant les paramètres de coupe, il est possible de réduire ces forces. Faites attention, par exemple, à: l'angle de coupe, la vitesse de coupe, le choix du matériau, les vibrations...
L'angle d'attaque garantit à son tour que le copeau glisse correctement sur la surface d'attaque. Si cet angle est plus petit, il y a moins de résistance car le copeau est plus facilement dévié. Une résistance plus faible se traduit par des forces d'usinage plus faibles, ce qui augmente la durée de vie de l'outil. L'angle de dégagement a des propriétés similaires. En le maintenant suffisamment grand, il y a moins de contact entre l'outil et le matériau de coupe, ce qui augmente encore la durée de vie. Enfin, l'angle de taillant est important. Plus cet angle est grand, plus l'outil sera solide. Un autre avantage d'un large angle de taillant est une meilleure dissipation de la chaleur à travers l'outil.
Paramètres de la machine
Les outils de coupe sont de formes et de tailles différentes, si bien qu'il est souvent difficile de s'y retrouver. En raison de cette diversité, il est préférable de laisser le fournisseur vous guider pour un processus nouveau (ou actuel). Grâce à son expertise et à son expérience, il peut vous donner un meilleur aperçu de la durée de vie estimée en fonction des paramètres de la machine et des conditions de travail.
Lors du réglage des paramètres de la machine, l'opérateur doit garder à l'esprit les règles suivantes:
- Une vitesse de coupe élevée a un effet positif sur la rugosité de surface, mais réduit la durée de vie de l'outil.
- Une alimentation plus élevée augmente la productivité en retirant plus de matière dans un court laps de temps.
- Une avance plus élevée a un effet négatif sur la qualité de la surface.
- Une avance plus élevée réduit la durée de vie de l'outil.
- Une profondeur de coupe plus élevée augmente la productivité, mais réduit la durée de vie de l'outil.
- Une profondeur de coupe trop faible génère de la chaleur, ce qui est désastreux pour la qualité de la surface et la durée de vie de l'outil.
Des informations précieuses sont perdues si les caractéristiques d'usure ne sont pas correctement reconnues en cas de défaillance – due ou non à une rupture d'outil.
Prolonger la durée de vie
Mesurer, c'est savoir. Des observations fiables sont la première étape pour prolonger la durée de vie de chaque outil. Nous avons déjà discuté des aspects du processus de coupe qui influencent la qualité de l'outil. En combinant les mesures directes et indirectes, on obtient un ensemble de données précieuses qui permettent une analyse plus approfondie. En combinant le principe de pareto et la méthode des surfaces de réponse (RSM), on peut déduire les conditions de coupe optimales.
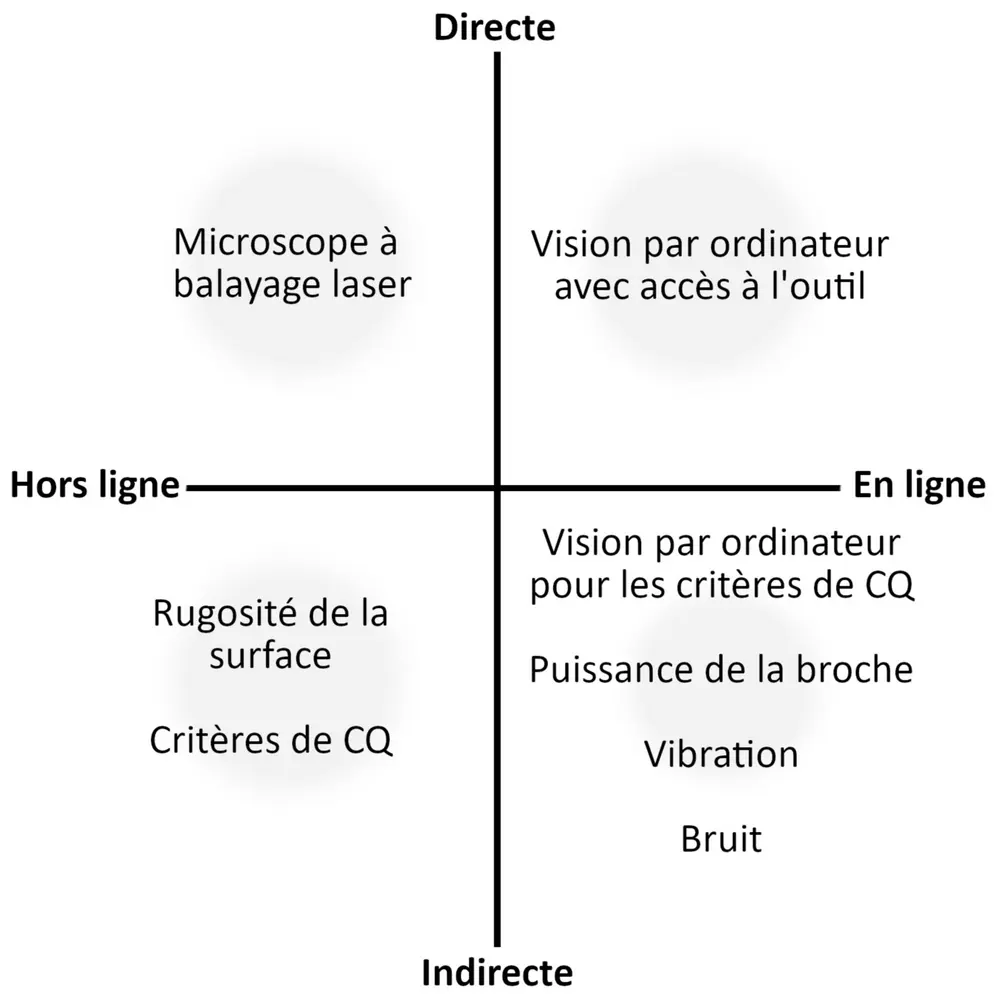
S'il est nécessaire de surveiller l'état de l'outil de manière très précise, des mesures plus radicales s'imposent. Les systèmes de vision par ordinateur dotés d'algorithmes de reconnaissance des caractéristiques spécifiques de l'usure offrent les meilleures performances et ont l'avantage de générer des indications directes et fiables.
conclusion
La surveillance de l'état de l'outil tout au long de sa vie est la première étape de la prédiction de l'usure. Non seulement cela évite des ruptures catastrophiques, avec les coûts que cela implique, mais en plus la production peut se poursuivre plus longtemps, ce qui équivaut à une réduction des temps d'arrêt. Plus de temps de production par outil, c'est plus d'efficacité et moins de coûts de matériaux. En raison de la fiabilité accrue, la capacité des pièces de rechange peut être réduite, ce qui entraîne une réduction des coûts de stockage.
En ayant davantage d'informations sur le schéma d'usure pendant les processus de coupe, on peut réduire les coûts dans plusieurs domaines. Avec un investissement initial très faible, un opérateur est en mesure de collecter des informations, d'analyser des données et de tirer des conclusions. Une fois que l'on a acquis plus d'expérience, on peut passer aux méthodes de mesure de l'usure online. Si la situation s'y prête, nous recommandons une technique de mesure directe pour atteindre le plus haut degré d'automatisation et de fiabilité possible.
Merci au dr. Tim Claeys et au prof. Jeroen Boydens pour leur soutien et leur implication dans ce projet. Les collaborateurs du projet, Hans Naert, Pieter Ideler, Peter Vanbiervliet et Robin Loicq, ont été indispensables pour la saisie des données et la communication avec les partenaires industriels.