Taux d'enlèvement de matière plus élevé dans le tournage CNC
Outils de tournage pour le multitâche
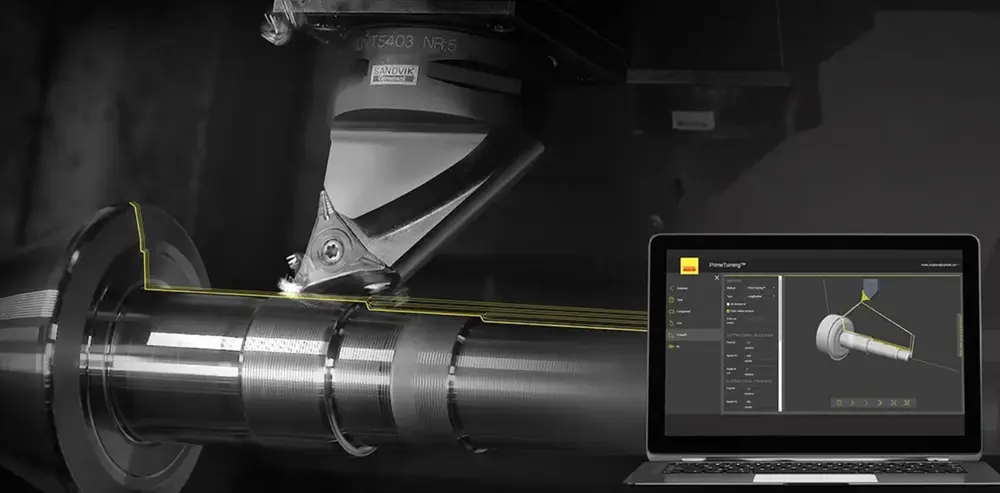
Le tournage CNC est désormais une technologie d'usinage bien établie dans l'industrie métallurgique, à tel point que les tourneurs CNC supposent une stabilité fiable du processus. En général, ils fixent donc les conditions de coupe "à l'aveugle" et continuent à utiliser leurs outils habituels. Une occasion manquée pourtant, car les fabricants d'outils innovent non seulement dans les outils de fraisage, mais aussi dans les outils de tournage.
Outils de tournage pour le multitâche
Le développement continu des outils de tournage s'appuie sur les machines multitâches, qui combinent le tournage et le fraisage en un seul serrage. Ces multi-machines exigent que les outils de tournage subissent des innovations autres qu'une nouvelle géométrie ou un nouveau revêtement.
Un développement observé chez plusieurs fabricants d'outils concerne les outils de tournage adaptés à de multiples usinages. Au lieu de devoir changer de plaquette à chaque fois – par exemple pour le pré-tournage ou le tournage de finition –, des solutions sont développées pour permettre d'effectuer des opérations d'usinage avec moins de changements d'outil.
Réduire le temps d'usinage
Un développement récent concerne, par exemple, les outils – avec la stratégie correspondante – qui permettent de tourner dans deux directions avec une seule plaquette amovible. Cela signifie moins de mouvements à vide. Selon la pièce à usiner, cela permet de réduire rapidement le temps d'usinage de 25 à 60% par rapport à la méthode habituelle jusqu'à présent.
Les outils de tournage bidirectionnels permettent de réduire le temps d'usinage jusqu'à 60%
Cela est rendu possible par la meilleure stabilité des nouveaux concepts d'outil. C'est la broche qui absorbe les chocs et non pas le porte-plaquette, et celle-ci est en mesure de bien mieux supporter ces forces.
Cependant, cette solution implique souvent l'investissement dans un système d'outils complet: plaquettes, supports et programmation avec d'autres paramètres.
Révolution dans le tournage CNC
Sandvik Coromant a jeté les bases de la "révolution" qui se produit actuellement dans le tournage CNC il y a plusieurs années avec PrimeTurning. Des outils spéciaux combinés avec des algorithmes de programmation développés à cet effet dans les logiciels de FAO permettent de tourner dans deux directions le long de l'axe Z. PrimeTurning peut également être utilisé comme un concept autonome, en combinaison avec un logiciel spécial de Sandvik.
Avec l'arrivée de ce type d'outil de tournage, le statu quo de longue date en matière de productivité du tournage CNC a été brisé. Comparé aux développements dans le domaine du fraisage avec des outils comportant beaucoup plus d'arêtes de coupe, le processus de tournage classique avec une seule arête de coupe dans le matériau semble s'être figé. Le gain de productivité dû à l'augmentation limitée du taux d'enlèvement de matière (MRR) était jusqu'à récemment beaucoup plus faible que celui dans les opérations de fraisage.
Avec la nouvelle technologie de virage bidirectionnel, on tourne avec un angle d'attaque plus petit, ce qui crée un copeau plus fin et plus large. Il en résulte une meilleure répartition de la charge mécanique et thermique sur une plus grande surface de l'arête de coupe, d'où une réduction des contraintes.
La profondeur de coupe exerce la plus grande influence sur les forces
Des recherches ont montré que la profondeur de coupe exerce la plus grande influence sur l'apparition de forces importantes. L'influence des vitesses de coupe plus élevées est nettement moindre, ce qui signifie que ces outils se prêtent au tournage à des vitesses de coupe élevées. Une partie du gain de productivité provient donc de cela. Une condition préalable est toutefois que la machine et la pièce à usiner soient suffisamment stables dans le serrage.
La vitesse de coupe a une influence minime sur la force de coupe, tandis que la profondeur de coupe exerce la plus grande influence
Au demeurant, cette évolution est en partie rendue possible par les progrès réalisés par les développeurs FAO. En effet, on tourne avec un angle d'attaque variable, différentes alimentations, vitesses de coupe et profondeurs de coupe. Ceci est donc très exigeant en termes de programmation. D'ailleurs, la plupart des programmes de FAO l'ont entre-temps intégrée.
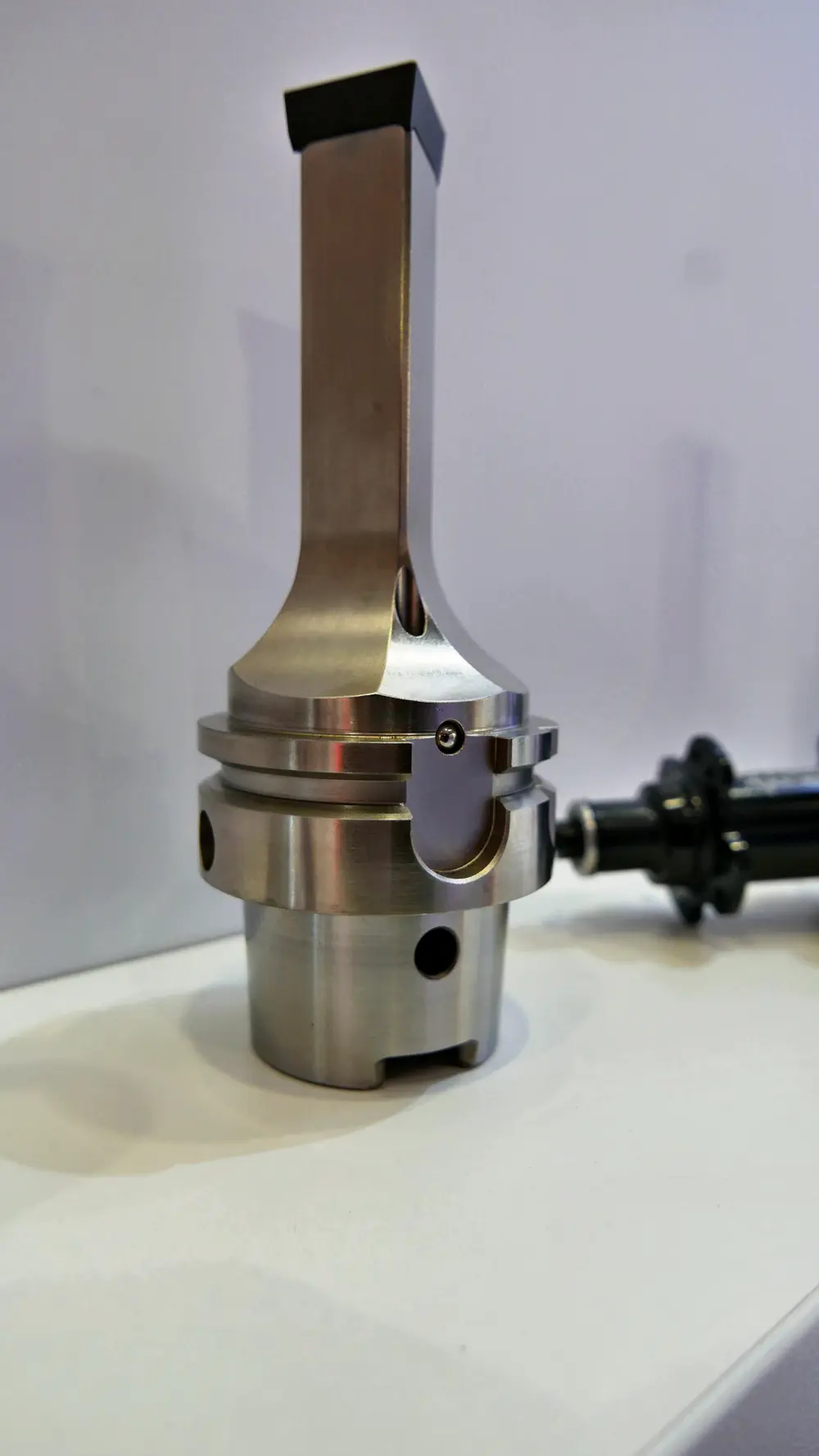
L'outil FreeTurn de Ceratizit est un exemple de la façon d'effectuer des opérations de tournage fréquemment planifiées avec un seul type de plaquette. Il permet le tournage de contour, le dressage sur tour et le chariotage avec un seul outil.
Le même fabricant d'outils a développé le procédé de tournage HDT (High Dynamic Turning) pour les machines multitâches, qui utilise FreeTurn. Grâce à la liberté de l'axe B, on peut positionner la plaquette sur la pièce sous n'importe quel angle de réglage correct. Outre la réduction des changements d'outil, l'avantage réside également dans une vitesse de coupe plus élevée.
Tours CNC avec axe Y comme alternative?
De plus en plus de fabricants fournissent des tours CNC incluant un axe Y. Certains y voient une alternative moins coûteuse aux machines multitâches qui disposent de nombreuses capacités de fraisage grâce à leur axe B. C'est en partie vrai. Une tourelle sur l'axe Y d'un tour qui accueille des outils entraînés offre une capacité de fraisage sur le tour. Cela autorise une finition plus complète des pièces qui nécessitent un fraisage limité en un seul serrage.
Les avantages de cette alternative sont des coûts d'investissement plus faibles et une programmation plus facile des pièces, éventuellement même sur la machine, ce qui, avec les machines multitâches, évolue rapidement vers un progiciel de FAO.
La limitation de cette alternative est la puissance limitée de l'outil entraîné, ainsi que la portée limitée de l'axe Y.
Les personnes qui doivent régulièrement effectuer des opérations de fraisage dans un plan X-Y sur une pièce rotative y trouveront leur compte. De plus, l'axe Y offre des avantages dans les opérations de tournage avec des outils statiques, du fait que les copeaux longs tombent automatiquement grâce à la gravité.
Outils pour le tronçonnage avec l'axe Y
Les fabricants d'outils répondent à la croissance du nombre de tours à axe Y. Les outils pour le tronçonnage sur l'axe Y en sont un exemple.
La lame peut plier, en particulier avec un diamètre de barre plus important et si l'outil de tronçonnage doit pénétrer plus profondément dans le matériau. Lors du tronçonnage, la rigidité du support est cruciale pour un usinage précis. Le tronçonnage avec l'axe Y permet d'éviter ce problème, et donc l'imprécision de la pièce.
Une meilleure utilisation des forces tangentielles améliore le comportement dynamique de l'outil, et c'est un avantage important du tronçonnage avec l'axe Y. Cela permet d'obtenir des résultats plus précis non seulement pour les petites largeurs de coupe, mais aussi pour le tronçonnage de grands diamètres exigeant une pénétration profonde de l'outil dans le matériau.
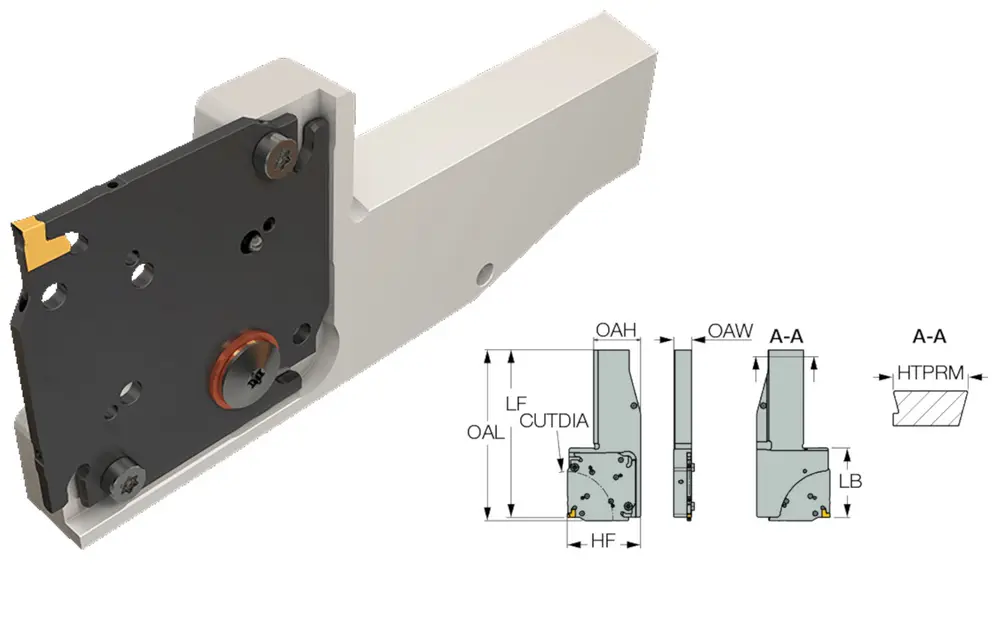
Avec le LOGIQ-F-GRIP, Iscar répond à la demande d'un outil de tronçonnage rigide et stable pour le tronçonnage suir l'axe Y. Le support est équipé de quatre plaquettes, ce qui garantit une longue durée de vie de l'outil. Le porte-plaquette est disponible avec ou sans refroidissement haute pression à travers l'outil. Grâce à la rigidité du système d'outils, il se prête bien au tronçonnage de grands diamètres, même lorsque celui-ci est effectué avec l'axe X.
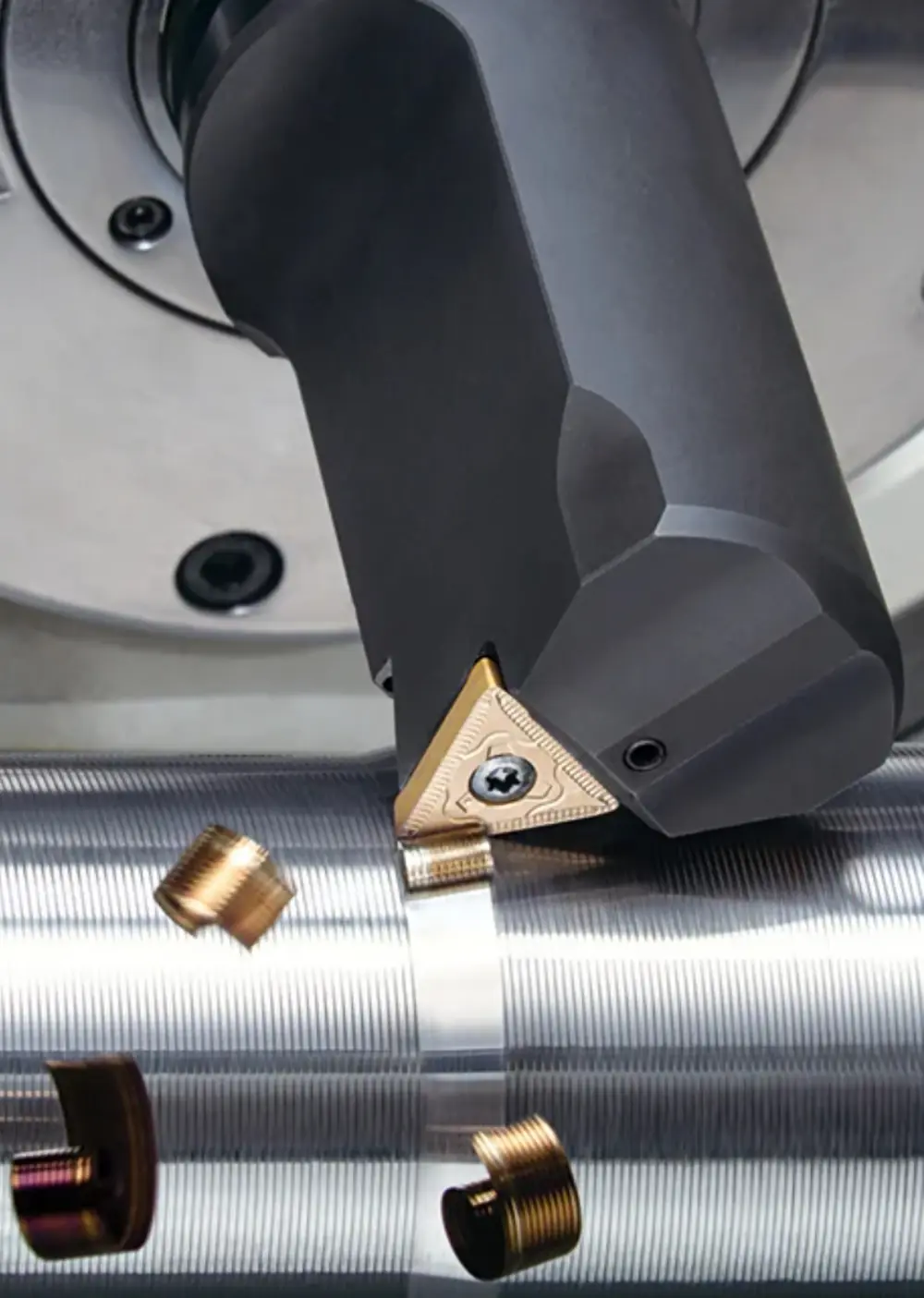
demande accrue de matériaux durs et de superalliages
La demande de composants en matériaux durs et en superalliages est en hausse. Le tournage CNC ne doit pas être un obstacle, pour autant qu'un certain nombre de conditions soient respectées.
L'une d'entre elles est la façon dont la plaquette entre et sort du matériau. Cela ne doit pas se faire trop brusquement. Pour les pièces qui seront ensuite durcies, les rayons doivent être tournés dans la phase tendre du matériau. De préférence, le tournage se fait à sec, sans utilisation d'un lubrifiant réfrigérant. Les économies ainsi réalisées compensent le coût plus élevé des plaquettes en CBN ou en céramique, qui sont de préférence utilisées pour l'usinage à sec.
En comparaison, lors du tournage avec des plaquettes standard, les coûts d'outillage tournent autour de 3% des coûts totaux, alors que ce pourcentage se situe entre 5 et 6% avec les outils CBN. Mais cela est compensé par l'élimination des coûts de lubrifiant de refroidissement – et éventuellement de nettoyage – et par les temps de cycle plus courts.
Les matériaux de coupe qui ont permis le tournage dur
Ces matériaux de coupe CBN et PCBN (nitrure de bore cubique polycristallin) sont plus résistants aux températures plus élevées, qui sont inévitables. Le PCBN est encore plus dur que le carbure lui-même. Ces deux matériaux de coupe ont rendu possible le tournage dur au cours des dernières décennies, jusqu'à une valeur HRC de 65.
Les vitesses de coupe élevées ne posent aucun problème
Étant donné que la part du lion (80%) de l'énergie thermique générée par l'opération de tournage se retrouve dans les copeaux, une bonne élimination des copeaux de la zone de l'arête de coupe est importante. Évitez les vitesses de coupe trop faibles, car cela augmente le risque de casser la plaquette. Les vitesses de coupe élevées, en revanche, ne posent pas de problème.
Des alimentations plus élevées entraînent une rugosité de surface légèrement inférieure à celle d'une opération de meulage. Pour le tournage sans intervention humaine, la stratégie consistant à travailler avec deux coupes est la meilleure, car un outil dédié au pré- et post-usinage offre la plus grande certitude en termes de tolérances et de précision de surface. En effet, lorsque le pré-usinage et le post-usinage sont effectués avec le même outil, la précision dimensionnelle peut être moindre.
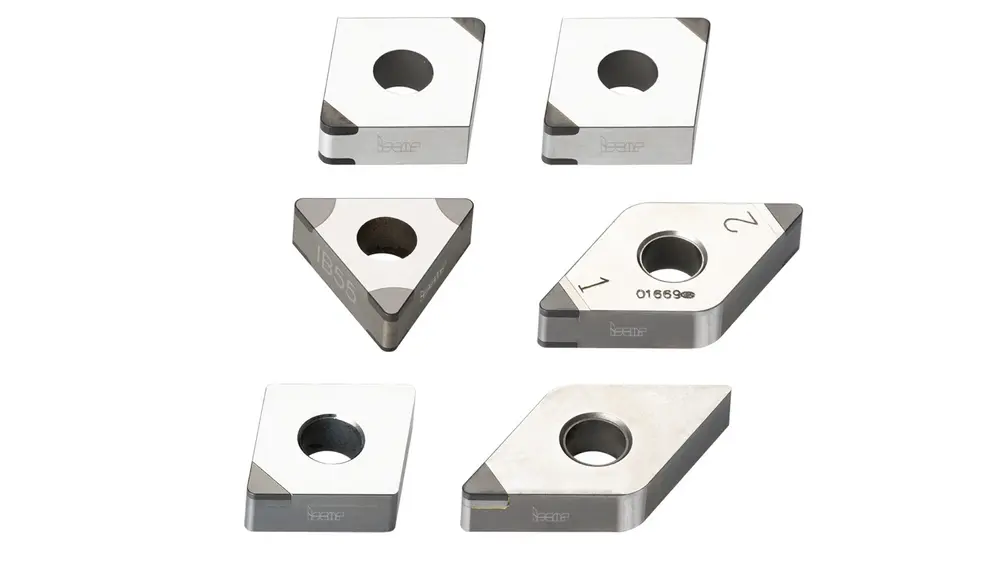
Avec la collaboration d'Iscar, Sandvik et Tungaloy