Comment usiner des matériaux 'difficiles'?
le résultat dépend du substrat, du revêtement et du modèle de brise-copeaux
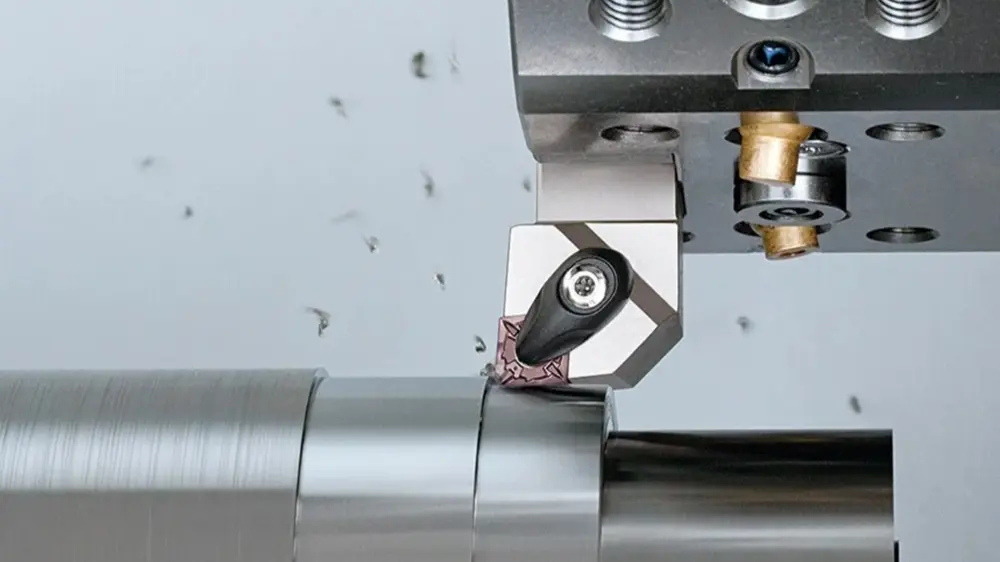
Dans de nombreuses applications qui impliquent l'énergie ou les entraînements, les développeurs cherchent à utiliser des matériaux capables de résister à des températures toujours plus élevées. En effet, dans les centrales électriques, par exemple, plus la température est élevée, plus le rendement est important. Cette tendance est soutenue, mais parfois ralentie, par l'évolution des technologies de fabrication. En effet, ces matériaux 'difficiles à usiner' doivent malgré tout rester usinables.
inconvénients des superalliages
L'évolution de l'usinabilité des matériaux est clairement visible lorsque l'on observe les entreprises qui les transforment. Le titane, par exemple, était encore considéré comme un matériau exotique au début du siècle, mais aujourd'hui, de plus en plus de PME de l'industrie métallurgique le transforment. Une évolution similaire peut être observée dans les aciers duplex. Ils sont plus faciles à traiter que les aciers inoxydables austénitiques en raison de leur structure différente et du fait que moins de nickel y est ajouté. Les superalliages, en revanche, restent un défi, bien qu'ils soient très demandés dans les secteurs de l'aviation, de la marine et de la médecine, entre autres. Ces alliages sont à base de fer, de nickel ou de cobalt et, dans cet ordre, l'usinabilité diminue.
Les superalliages sont développés pour résister à des températures élevées et sont donc difficiles à usiner
Les alliages à base de nickel sont particulièrement demandés de nos jours. Ces superalliages ayant été développés pour résister à des températures élevées, ils ne se ramollissent pas au niveau de l'arête de coupe sous l'effet de la température, comme c'est le cas pour les matériaux facilement usinés. La pression sur l'arête de coupe augmente donc, ce qui peut entraîner une rupture, une accumulation de matière sur l'arête de coupe ou une déformation. En outre, la résistance élevée augmente la charge statique sur l'arête de coupe et entraîne des copeaux segmentés. L'évasement est un autre problème qui peut survenir lors du tournage des superalliages à base de nickel. Cela peut être évité en choisissant une profondeur de coupe élevée et en optant pour des revêtements PVD.
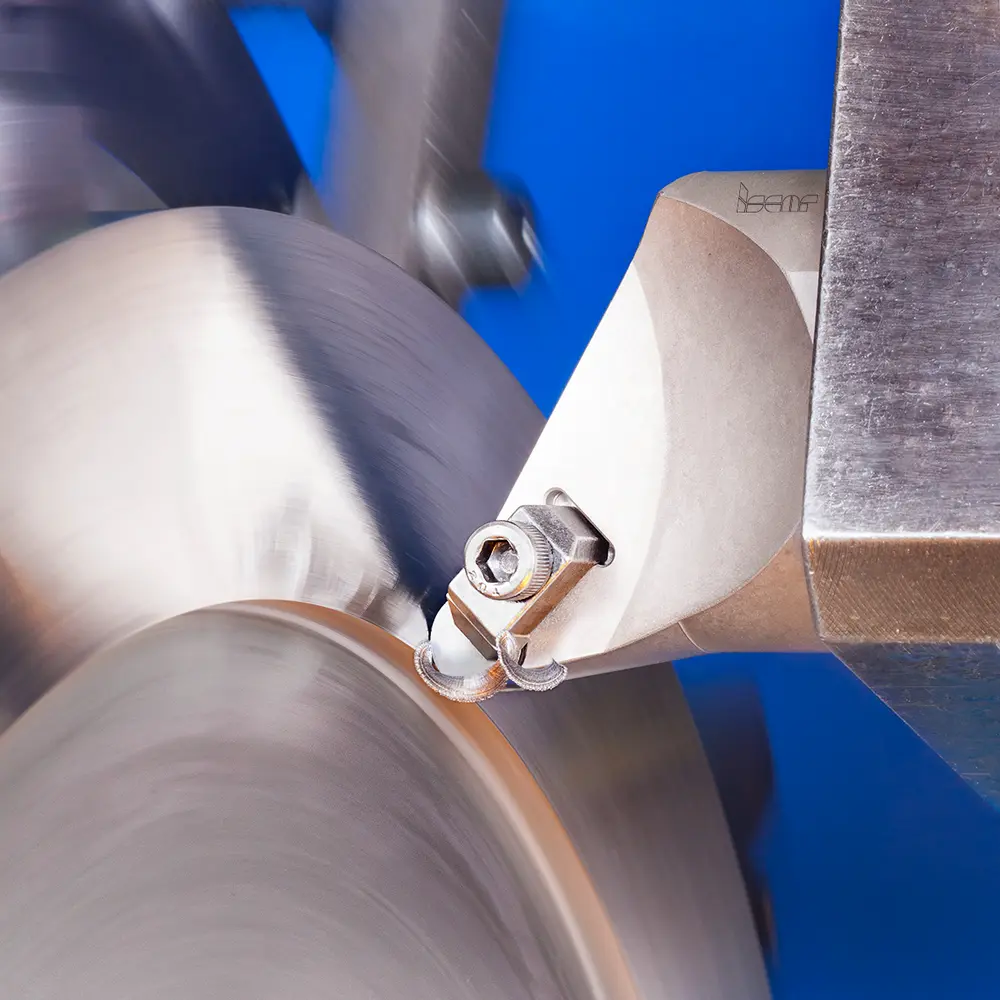
Une autre conséquence de l'augmentation de la température au niveau de l'arête de coupe est que le risque de réaction chimique avec le revêtement augmente. En raison de l'augmentation de la chaleur, le matériau du revêtement a tendance à réagir avec le matériau à usiner. Pour maintenir la température plus basse, le refroidissement à haute pression est un facteur qui a une influence positive sur le processus de tournage. En effet, l'apport du lubrifiant réfrigérant sous haute pression assure une meilleure dissipation de la chaleur. Un effet positif est déjà visible à une pression de 10 bar, mais à partir de 70 bar on parle de refroidissement haute pression. Cela permet de s'attaquer au problème à la base. Cependant, la machine doit être capable de résister à cela.
Les fabricants d'outils proposent également des porte-plaquettes spéciaux avec un refroidissement à travers le support, parfois même avec une buse en haut et en bas pour un refroidissement plus efficace. Cette solution n'est pas seulement intéressante pour les superalliages, mais peut également être utilisée pour le tournage CNC d'autres matériaux. Il augmente la stabilité du processus et garantit une plus longue durée de vie des outils. Le refroidissement cryogénique est une alternative encore peu utilisée.
Types de matériaux pour l'outil
Tous les matériaux difficiles à usiner se caractérisent par une mauvaise conductivité thermique et, sous l'effet de l'usinage, ils durcissent; l'augmentation de la pression les fait passer à une structure cristalline différente. Ce durcissement peut être causé par des éléments d'alliage qui s'implantent dans les espaces vides entre les atomes de métal. Lors du passage suivant, l'outil subit alors une usure par entaille.
L'adhésion du matériau au bord de coupe, due à son accumulation sur la surface de raclage, est un autre problème courant. Il en résulte une modification de la géométrie de l'outil et de la surface de contact entre la pièce et l'arête de coupe originale en carbure. En conséquence, la qualité de la surface diminue, la durée de vie des outils devient imprévisible, les forces exercées sur la machine augmentent et les outils peuvent se briser prématurément, ce qui perturbe le processus ou même endommage irrémédiablement la pièce.
Le bon équilibre entre carbure, revêtement et finition
Ces dernières années, l'industrie de l'outillage a beaucoup fait pour développer des processus d'usinage stables pour les différents groupes de matériaux, notamment pour les superalliages. Cela nécessite toujours un bon équilibre entre le métal dur, le revêtement et le processus de finition, comme l'application de brise-copeaux. Ces trois facteurs déterminent ensemble le résultat final, tant en termes économiques que qualitatifs.
Cependant, d'autres matériaux de coupe tels que la céramique, le nitrure de bore cubique (CBN) et le diamant peuvent également offrir des avantages pour le tournage stable d'alliages résistant à la chaleur. En examinant les différences de résistance aux hautes températures, il est facile de comprendre pourquoi certains choix sont faits. Les carbures, par exemple, peuvent supporter des températures allant jusqu'à 1.000 °C; les céramiques jusqu'à 1.200 °C et les CBN jusqu'à 2.000 °C, avec en plus une grande résistance à l'usure.
Les revêtements améliorent encore les propriétés des matériaux de coupe, ce qui a une incidence particulière sur la durée de vie des outils. Le CBN, le matériau le plus dur après le diamant, se prête très bien au tournage de matériaux tels que l'Inconel 718. Par rapport à une plaquette en carbure avec un revêtement TiAlN, la durée de vie de l'outil double à une vitesse de coupe de 50 m/min. Les plaquettes CBN sont particulièrement adaptées au tournage de l'acier trempé (55 HRC et plus). La meilleure résistance à la température du CBN assure une plus longue conservation des arêtes de coupe sans rupture ni déformation. Les plaquettes CBN à géométrie Wiper peuvent être utilisées pour améliorer la qualité de surface (tout en maintenant la productivité) ou pour tourner avec la même qualité de surface que les plaquettes conventionnelles, mais avec une vitesse d'avance plus élevée et donc un plus grand volume de copeaux. Le temps de cycle peut être réduit de moitié avec cette géométrie, et pas seulement lors du tournage de matériaux trempés à la CNC.
L'influence du brise-copeaux
Comme mentionné précédemment, un processus de tournage stable est une combinaison de substrat d'outil, de géométrie, de revêtement, de serrage de la machine et de stratégie. Un autre élément important, c'est le type de brise-copeaux. En effet, les copeaux plus courts dissipent mieux la chaleur lors du tournage d'alliages à base de nickel. Dans de nombreuses applications, le brise-copeaux comprime fortement le copeau pour créer une rupture forcée du copeau. La situation est quelque peu différente avec les matériaux robustes et résistants à la chaleur. Il s'agit ici de retirer le copeau avec précaution mais rapidement afin d'éviter l'accumulation sur l'arête de coupe et d'empêcher la chaleur de se transférer à la plaquette. Par conséquent, le fait de briser les copeaux est important, car cela permet de dissiper la chaleur. Le revêtement de l'outil joue également un rôle à cet égard. Ce qui compte le plus, c'est l'adhérence du revêtement au substrat. Plus la structure du substrat est homogène, plus le risque de projection est faible.
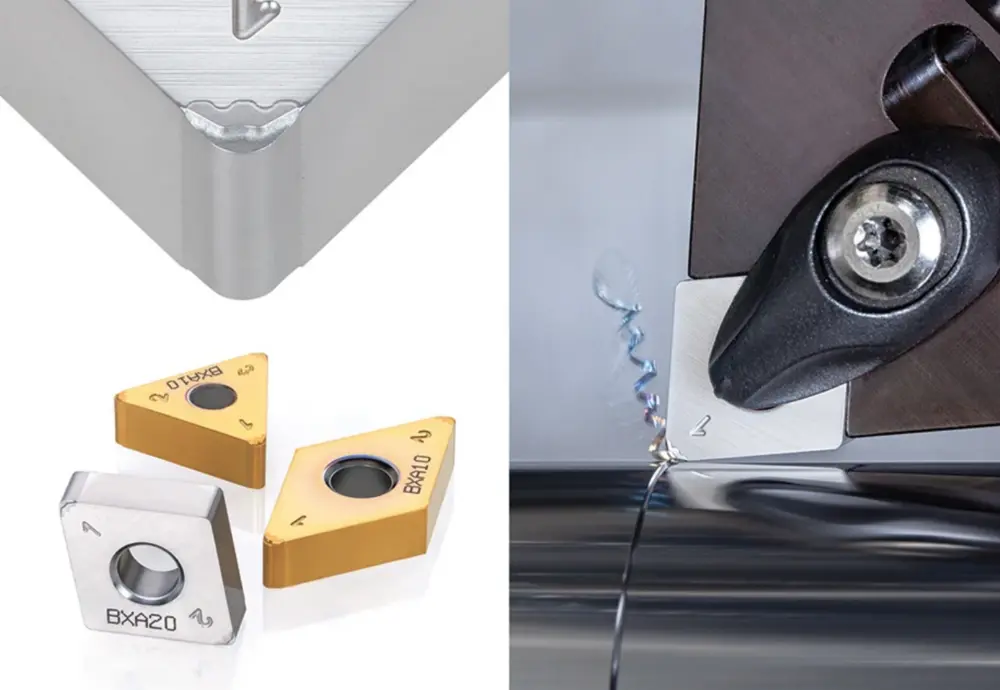
Les céramiques accélèrent le processus de tournage
Un exemple de matériau relativement nouveau est l'insert en céramique: les outils en céramique SiAlON (silicium - aluminium - oxygène - azote; une céramique dite non-oxyde). La particularité de ces outils est que les grains sont déformés à haute température en structures quasi longues, qui se superposent de manière totalement aléatoire. En termes de structure, cela ressemble à des fibres, mais positionnées dans toutes les directions. Ainsi, la chaleur n'a que peu d'effet sur le substrat.
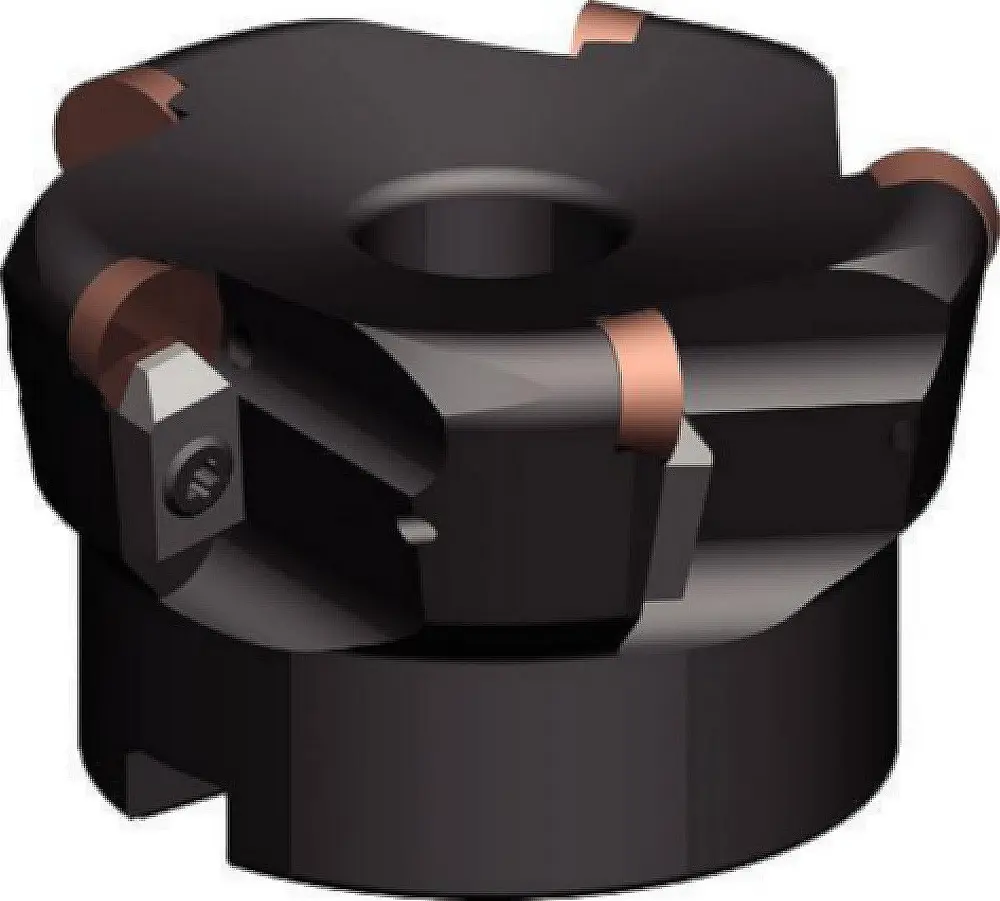
Le processus d'usinage est très différent de celui des outils en carbure, entre autres parce qu'au lieu de copeaux, on parle plutôt de pulvérulents; il ne s'agit donc pas de copeaux à proprement parler. Ce sont des particules emportées par l'air. Par rapport aux céramiques renforcées par des whiskers, le SiAlON est moins sensible aux changements de température. Avec ces plaquettes, il est possible d'obtenir des conditions de coupe beaucoup plus élevées qu'avec des outils ordinaires. Le taux d'enlèvement de matière (MRR) est 20 à 30 fois plus élevé que lors de l'usinage de superalliages avec des outils en carbure, principalement en raison du fait que vous tournez à des vitesses de coupe beaucoup plus élevées.
Tournage avec des vitesses d'avance élevées
La stratégie est un autre aspect qui affecte la productivité. Le tournage avec des vitesses d'avance élevées permet de gagner beaucoup de temps dans le processus d'ébauche. Cette approche a toutefois pour conséquence de créer des forces de coupe extrêmement élevées. Par exemple, lors du tournage avec une avance allant jusqu'à 3 mm par tour, les forces de coupe peuvent atteindre 16.000 N. C'est pourquoi cette stratégie impose des exigences élevées à la fois à la pièce et à l'outil: tous deux doivent être serrés de manière stable afin d'éviter toute vibration.
Avec cette stratégie, l'angle d'attaque est également réduit à 10 ou 20 degrés, ce qui permet d'obtenir une puce plus fine. Cela permet de mieux dissiper les forces dans le sens axial et radial, de réduire l'usure de l'encoche de la plaquette et de diminuer la pression sur l'arête de coupe lorsque le burin entre ou sort du matériau. L'inconvénient d'un petit angle d'attaque, cependant, est que le risque de vibration augmente. D'où les exigences élevées en matière de stabilité du serrage avec cette stratégie.